航空複雜(zá)殼體零件深孔加工技術研究
2019-1-24 來(lái)源:- 作者:張曉東 韓策
摘要:深孔加工在航空製造業中具有廣泛需求,是加工難度(dù)最大的(de)工序之一。複雜(zá)殼體零件是航空發動機的關鍵部件,其深孔加(jiā)工質量(liàng)直接影響航空發動機(jī)的服役性能和使用壽命。以航空複雜殼體零件為對象,針對航空複雜殼體零件(jiàn)深孔加工的工藝(yì)特點及難點,就目前現(xiàn)有深孔加(jiā)工(gōng)方法、深孔鑽削力學、深孔鑽削切屑形態與排屑方法、深(shēn)孔加工在線監控及深孔加工設(shè)備等方麵關鍵技術進行綜述,並探討了深孔加工未來的發展趨勢。
關鍵詞:深孔加工;鑽削;加工係統;複雜殼體
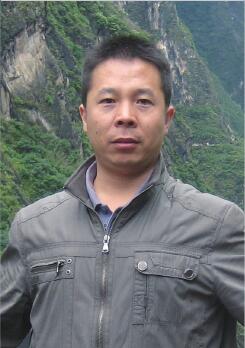
張曉東 博士研究生、高級(jí)工(gōng)程師,主要(yào)從事數字化製造、數控加工技術以及智(zhì)能加工技術研究
複雜殼體類(lèi)零(líng)件是航(háng)空發動機係統中典型的結構件和關鍵件,是實現航空發動機燃油係統高、中(zhōng)、低壓油路導引的核(hé)心部件。航空複雜殼體零件的顯著特點是結構複雜、孔係眾多,其內部有多達幾百個縱橫交錯的各種深孔,孔徑(jìng)小、深徑比(bǐ)大、直徑從 1mm 到幾十毫米不等、孔深與(yǔ)直徑之比高達 50 以上(shàng),而且帶有(yǒu)各種台(tái)階孔、環形槽等結構。這些孔結構複雜、精度要求高、孔的圓度和直線度要求高、加工難度大,使深孔(kǒng)加工(gōng)成為複雜殼體零件加工中(zhōng)難(nán)度最大的加工過程之(zhī)一。複(fù)雜殼體零(líng)件的深孔孔係是燃油係統油路導引的通道,其加工尺寸誤差直接影響發動機燃(rán)油係統工作性能,其表麵質量直接決定發動機燃油係統的服役壽命,對航空發動機的質(zhì)量和服役性能有著舉足(zú)輕重的作(zuò)用。隨著新一代飛機和航空發動機的發(fā)展,複雜殼體類零件孔係結構的設計更趨複雜、精度要求越來越高,對深孔加(jiā)工技術提出了更高的要求。
然而,我國深孔加工(gōng)領域(yù)的基(jī)礎較薄弱,目前航空企業中尚缺乏(fá)高性價比的深孔加工專(zhuān)用裝備,加之深孔加工(gōng)技(jì)術的研(yán)究尚不成熟,導(dǎo)致(zhì)目前我(wǒ)國航(háng)空企業中複雜殼體深(shēn)孔(kǒng)加工普遍存在合格率低、生產效率低以及加工質量不穩定等問題。深孔加工技術(shù)成為航空發動機燃油控製係統(tǒng)研製生產的(de)技(jì)術瓶(píng)頸,嚴重製約著我國航空製造業的發展,因此迫切需要對深(shēn)孔加工技術展開深入研究。本文以航空複雜殼體(tǐ)零(líng)件為象,對(duì)深孔(kǒng)加工技術的工藝特點及難點、發(fā)展現狀、關鍵技術等(děng)進行闡述,並展(zhǎn)望了未來深(shēn)孔加工的發展趨勢。深孔加工工藝特點(diǎn)及難點在航(háng)空複(fù)雜殼體零件的深孔加工過程中,孔(kǒng)的超大(dà)深徑比(bǐ)帶來的鑽杆低剛(gāng)度問題、排(pái)屑和散熱困難問題以(yǐ)及加工時的封閉或半封閉狀態等都使(shǐ)得(dé)深孔加工非常困難。航空複雜殼體零件深孔加工的難點主要(yào)體現在:
(1)工藝係統剛性差。殼體零件中孔的小直(zhí)徑和超大深徑比直接決定了鑽(zuàn)削所用鑽杆細且長,使得(dé)鑽杆剛度不足,從而造成鑽削過程中鑽杆易產生偏斜、振動、扭曲,甚至折斷。為避免這一問題,生產中往往采用小進給量鑽削以避免大切削力帶來的鑽杆剛度問題,這嚴重(chóng)製約了深(shēn)孔的加工(gōng)效率。然而即(jí)便如此,孔的加工質量仍很難保(bǎo)證。
(2)排屑困難。孔的(de)小直徑和大深度決定了鑽削過程中(zhōng)切屑在孔內的排(pái)屑空間小且(qiě)排屑路徑長,極易發生切屑堵塞,從而產生過大的(de)扭(niǔ)矩,鑽頭隨之發生崩(bēng)刃、折斷(duàn),造成
零件(jiàn)報廢。航空殼體零件多采用鋁合金材料,加工過程中易發生粘刀現(xiàn)象,使排屑(xiè)問題更為嚴峻。此(cǐ)外(wài),采用外排屑方式時切屑會刮傷孔(kǒng)的已加工(gōng)表麵,造成孔壁出現螺旋(xuán)溝(gōu),嚴重(chóng)影響孔表麵質量。
(3)切削散熱困(kùn)難。一般孔的鑽削過程(chéng)中,80%的切削熱(rè)被切(qiē)屑帶(dài)走。而在深孔加工中鑽頭在相對(duì)封閉的狀態(tài)下工作,切削熱(rè)很(hěn)難擴散,由於(yú)殼體零件中很(hěn)多孔直徑很小,因此加工過程中的冷卻、潤滑也都很困難,這使得鑽頭和工件成為主要(yào)散熱體,熱量積聚效(xiào)應非(fēi)常明顯,使鑽頭溫度升(shēng)高、磨損加劇,極大影響(xiǎng)了鑽(zuàn)頭使用壽命。同時,當溫度過高時,加工孔也會受到熱效(xiào)應影響而發生變形,影(yǐng)響孔的尺寸精度。
(4)難以觀(guān)察加工(gōng)過程。由(yóu)於殼體零件(jiàn)的孔隙結構複雜、深孔空間狹小(xiǎo),加工過程處(chù)於封閉或半(bàn)封閉的狀態(tài),無法直接觀察鑽頭的(de)狀態(tài)和孔的加工情況(kuàng)。以上(shàng)工(gōng)藝特點及難點決定了深孔加工過程中的隨機故障很多。大量的試驗和研(yán)究(jiū)表明,刀具磨損、破損和切屑堵塞是導致在深孔加工過程中較頻繁出(chū)現故障的主要(yào)原因(yīn)。
在航空複雜殼體零件的加(jiā)工中,孔加工通常(cháng)是中(zhōng)間工序或最後(hòu)工序,一旦在孔加工過程中(zhōng)發生鑽(zuàn)杆折斷或(huò)孔(kǒng)道刮傷、偏斜等故障,將直接導致零件報(bào)廢,造成巨大經濟損失。
深孔加工技術(shù)發展現狀
1 、深孔加工發展曆程
孔加工起源於(yú)美國人發明的扁鑽(zuàn),以及後來(lái)改(gǎi)進(jìn)形成的(de)麻花鑽。這兩種鑽頭的結構相對簡單,切削液導入方(fāng)便,便於(yú)製造出不同直(zhí)徑和長度的鑽(zuàn)頭以適用於(yú)加工不同尺寸(cùn)的孔(kǒng)。然而,當加工深孔時,扁(biǎn)鑽和麻花鑽的排屑和冷卻十分困難,同時由於鑽杆剛度隨之降低,也限製了加工效率。20 世紀初(chū),為解決(jué)槍管加工問題,美、英(yīng)等(děng)國軍事工業部門發明了槍鑽。槍鑽係統將高壓(yā)切削液通過(guò)鑽(zuàn)杆內部通道送到切削部(bù)分,進行冷卻和排屑,屬於外排屑的鑽削方式。此外,槍鑽鑽頭上安裝(zhuāng)有導向塊,具有自導向功能。但由於采用外排屑方式,切屑與加工表麵會(huì)發生刮擦,影(yǐng)響孔表麵質量。同時,由於自身結構缺陷,導致槍鑽的成本較高而加工效率和精(jīng)度較低。第二次世界大戰期間,為滿足槍炮高效生產的需求,德國的(de) Beisner 於 1942 年發明了一種內排屑深孔鑽,後經(jīng)國際孔加工協(xié)會(Boring and Trepanning Association, BTA)的改進,形成了 BTA 鑽削方法(fǎ)。BTA 係統(tǒng)采用的鑽杆結(jié)構剛(gāng)度較高,采用內排屑方式,孔表麵質量較好。但是 BTA 係統具有切削液壓力高、密封困難的缺點。1963 年,瑞典Sandvik 公司(sī)利用液體的噴吸效應原理,發(fā)明了噴吸鑽法,利用切(qiē)削液的(de)噴、吸聯合作用,改善了排屑方法,降低了係統的壓力。20 世紀 70 年代,日本冶金股份公司發(fā)明了雙進油單管噴吸鑽係統(Double Feeder,DF),它將雙(shuāng)管係統改為(wéi)單管,增加了一 個專門起吸效(xiào)應的油壓頭,增大了鑽(zuàn) 杆 的 剛 度。20 世 紀 80 年 代,國內中北(běi)大(dà)學的王峻等發明了單管內排屑噴吸鑽(Single-Tube Inner Chip Removal Ejector Drill, SIED),SIED 技術完(wán)善了 DF 鑽的抽屑容器設計,使抽屑能力大大增強,同時對鑽頭結構(gòu)進行了優化設計,構成了(le)以單邊刃、單管內排屑噴吸鑽、自導向為特征的鑽削係統,這項技術成為當前先進的深孔加工技術。
2 、現有深孔加工係統及方法
除傳統鑽削外(wài),目前常(cháng)用的深孔加工係統有槍鑽係(xì)統、BTA 係(xì)統、噴吸鑽係統、DF 係(xì)統(tǒng)和 SIED 係統。現有深孔加工方法按排屑方式可分為外排屑和內排屑兩種,外排屑是指切削(xuē)液由(yóu)鑽(zuàn)杆內部進入,經鑽(zuàn)頭小孔噴射到切削區域,然後攜帶切屑從鑽杆外部與孔壁的間隙排出的方法,主(zhǔ)要包括扁(biǎn)鑽、麻花鑽和槍鑽等;內排屑是指(zhǐ)切(qiē)削液從鑽(zuàn)杆與孔壁的(de)間隙進(jìn)入,靠切削液的壓力將切屑推入鑽頭(tóu)小孔,經(jīng)鑽杆的內部通道排出的方法,主要包括 BTA 鑽、噴(pēn)吸鑽、DF 鑽和 SIED 鑽等。外排屑的缺點是切屑會與孔(kǒng)壁接觸產生劃痕而破壞孔表麵質量,此外鑽杆(gǎn)剛度不足導致加工效率較低,加工精(jīng)度難以保證;內排屑克服了這些缺點,但由於需要(yào)足夠的容屑空間,導致鑽杆的最小直(zhí)徑受到(dào)限製。生產實踐中需要根據加工孔的(de)尺寸和質量要求等實際情況合(hé)理選(xuǎn)擇加工方法。
2.1 傳統鑽削(xuē)
傳統深孔加工一般以使用麻花(huā)鑽(zuàn)為代表。在航空複雜殼體(tǐ)零件深孔加工(gōng)中典型(xíng)的工(gōng)藝方法是采用長、短(duǎn)麻花鑽配合使用、鑽削過程多次退刀排屑、逐級延伸鑽孔的方法。傳統鑽削方法材料去除率大,便於在數控加工中心上與其他加工方法集成,加工效率高,而且具有加工操作簡單、不需要專用設備、成本低等(děng)優勢。因其鑽(zuàn)頭結構相對簡(jiǎn)單,鑽杆可以製造得很細,目前對(duì)於直徑小於 6mm 的深孔,傳統鑽削仍是主要的加工方法。基於上(shàng)述原因,傳統鑽削方法目前仍是我國航空企業(yè)複雜殼體零(líng)件深(shēn)孔(kǒng)加工的最常用(yòng)方法。但是,傳統深孔加工的主要問題在於鑽頭易折斷、排屑和冷卻問題難以解決,因此將造成返工返修,甚至整套殼體零件的報廢(fèi),導致生產周期延長(zhǎng)、質量穩定(dìng)性差等(děng)問(wèn)題。目前(qián),隨著航(háng)空複雜殼體批量(liàng)生產質量和加工效率(lǜ)要求(qiú)的逐(zhú)步提高,傳統(tǒng)鑽削方法麵臨越來越多的(de)問題和挑戰。
2.2 槍鑽
槍鑽因最(zuì)早用於槍管製造而(ér)得名。它采用單切(qiē)削刃並具有自導向功能的 V 型中空鑽杆(gǎn),屬(shǔ)於外排屑方式。其(qí)工作原理如圖 1 所示,切削液從入口經加壓泵進入鑽杆內(nèi)部通道,流向鑽(zuàn)頭的切削部分進行冷卻潤滑,並(bìng)將攜帶切屑通過鑽杆和孔壁間的 V 型槽,最後從出口排出。槍鑽相(xiàng)比於采用麻花鑽(zuàn)的傳統鑽削方式,改(gǎi)善了排屑(xiè)和冷卻的方法,鑽(zuàn)頭具有自導向功能,能夠加工更深、更小的孔(kǒng)。但由(yóu)於它(tā)仍屬於外排屑方式,切屑容(róng)易擦傷已加工孔壁(bì),而且孔較深時切屑必須保持小(xiǎo)而薄的形狀,才能保證被冷卻液衝出,加之槍鑽係統的排屑方法對油壓要(yào)求很高,要求使用(yòng)專用(yòng)機床,導致費用昂貴。此外(wài),槍鑽具有難以彌補的結構性缺陷:一是其鑽杆是 V 形非對稱空心軸,剛性差,鑽孔過程中容易發生質心偏移,因此隻能傳遞有限(xiàn)的扭矩,進給量受到限製,隻適用於加工(gōng)小直徑孔,加工效率低;二是其鑽頭(tóu)與鑽杆不可分離,通用性差。目前,槍鑽係統主要用於加工直徑 φ<20mm 的(de)深孔。
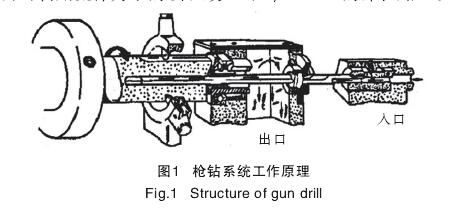
2.3 BTA係(xì)統
針對槍鑽係統存在的缺(quē)點,國際(jì)孔加工協會發明了一種(zhǒng)內排屑深孔(kǒng)鑽,BTA 係統中鑽頭與(yǔ)鑽杆為中空圓柱體,提高了刀具剛性和快速拆裝問題。其工作原理如圖 2 所示,切削液經加壓從入口進入授油器後通過鑽杆與孔壁形成的密封環狀空(kōng)間,流向切削部分進行冷卻潤滑,並將切屑壓入鑽頭上的出屑口,經鑽杆內腔(qiāng)從出口排出。相比於槍鑽,BTA 係統采用內(nèi)排(pái)屑方式,切屑不與工件孔(kǒng)壁摩擦,加工質量較(jiào)好,而且其鑽杆為圓管(guǎn)狀,剛(gāng)性(xìng)較好,加工效率較高(gāo)。但 BTA 係統對切削液壓力要求高、密封困難,受鑽杆內排屑限製,排屑空間小,經常發生堵屑。為解決這一(yī)問題,通常需(xū)要在鑽(zuàn)頭上加工斷(duàn)屑台或采(cǎi)用錯(cuò)齒結構,而結構的(de)複雜化造成鑽頭(tóu)製造難度大且價格高,使 BTA刀具(jù)實際上成為價格昂貴而並不耐(nài)用的壟斷性工具產品,這是 BTA 鑽在我國航空企業難以普及推廣的重(chóng)要原因。目前,BTA 係統主要適用於直徑 φ>12mm 的深孔加工。
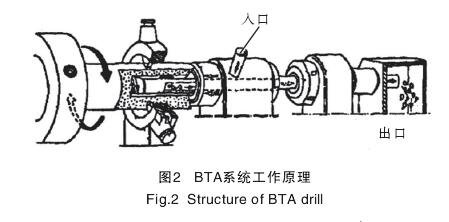
2.4 噴吸(xī)鑽係(xì)統
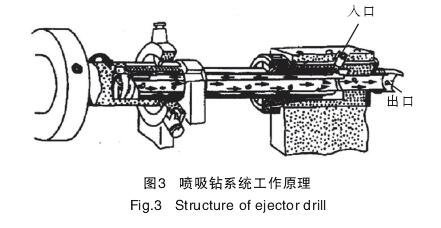
噴 吸 鑽 係(xì) 統(見 圖 3)是 瑞 典Sandvik 公司利用流體力學的(de)噴吸效應原理發明的雙管內排屑深孔鑽削方法。進(jìn)一步(bù)改善了排屑過程,降(jiàng)低了冷卻係統的壓力。其(qí)噴吸鑽係統(tǒng)采(cǎi)用雙層管(guǎn)刀杆,切削液經加壓後從入口進入,其中(zhōng) 2/3 的切(qiē)削液進入(rù)內、外鑽杆間的環形空間,流向切削部分進行冷卻和潤滑,並將切屑推(tuī)入(rù)鑽杆內腔;其餘 1/3 的切削液,從內鑽(zuàn)杆上月牙狀噴嘴高速噴入內鑽杆,在內鑽杆(gǎn)內腔形成一個低壓區,對攜帶切屑的切削液產(chǎn)生抽吸(xī)作用,在噴、吸雙重作用下(xià),促使(shǐ)切屑快速從出口(kǒu)排出。噴吸鑽係統的切(qiē)削液壓力低(dī)且穩定,排(pái)屑順暢,降低了密封性要求。此外(wài)由於其采用雙層管刀杆,剛度較高,可以采用大進給量加工。然而噴吸鑽係統(tǒng)的鑽具結構複雜,製造難度大(dà),成本高。對(duì)於孔深較大的孔負壓抽屑效果受限,加之其采用雙層管刀杆結構(gòu),容屑空間小,限製了排屑能力。目前(qián),噴吸鑽(zuàn)係統(tǒng)主要適用於(yú)直徑 φ>18mm 的深孔加工。
2.5 DF係統
DF 係(xì)統(見圖(tú) 4)是日本冶金股份有限公司研製出的雙進油(yóu)單管內排屑係統(tǒng),其(qí)切削液(yè)分(fèn)為前後兩支(zhī),分別從兩個入口進入。前一支 2/3的切削液經過鑽杆與己加(jiā)工孔壁形成的環狀區域流向切削部分,並將切屑推入鑽頭上(shàng)的出屑口進入鑽杆,流向抽屑器;後一支 1/3 的切削液(yè)直接進入抽屑器,經前、後噴嘴之間喇叭口狀的窄狹錐形間隙後獲得加(jiā)速,產生負壓抽吸作用,達到加速排屑的目的。DF 係統前半部分起(qǐ)“推”作用的結構類似於 BTA 係統(tǒng),後半部分起“吸”作用的結(jié)構類似於噴吸鑽係統,而由於 DF 係統采用了雙進油裝(zhuāng)置,僅用一根鑽杆即完成推壓和抽吸的切屑方法,鑽杆直徑可以做得更小(xiǎo),相比於噴吸鑽(zuàn)能(néng)夠加工更小的孔(kǒng),抽屑效果也優於噴吸鑽。但其抽屑器設計仍不夠完善,生產(chǎn)實踐中DF 係統僅可在(zài)有限範圍內能替代BTA 和雙管噴吸鑽。目前,DF 係統(tǒng)的最小加工直徑 φ 可達 6mm。
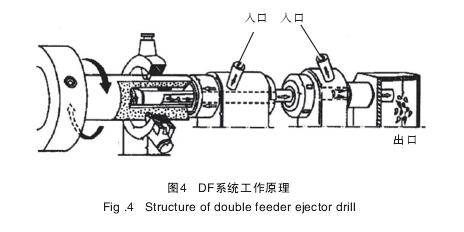
2.6 SIED係(xì)統
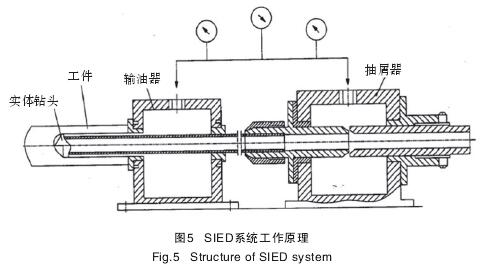
SIED 係統(tǒng)是一種(zhǒng)由中北大學王峻 發明的單管內排屑噴吸鑽係統。該技術以 BTA、噴吸(xī)鑽、DF 係(xì)統 3 種內排屑鑽削技術為基礎,增加了分調式功率增補型抽屑裝置(zhì),可實現冷卻和排屑液流的獨立控製。其基本原理(lǐ)如圖(tú) 5 所示(shì),切削液由液(yè)壓泵輸出後,分為兩個分支:前一支切削液流入(rù)輸油器(qì),經鑽杆與孔壁(bì)之間的環狀空間流向切削部(bù)分,將切屑推(tuī)入鑽頭上的出屑口;後一支切削(xuē)液流入抽屑器,經錐形噴嘴副之間的間隙進(jìn)入後噴嘴內(nèi)腔,產生高速射流和負(fù)壓。SIED 係(xì)統對兩支液流各設獨立的調壓閥,可以分別調整至最佳(jiā)冷卻、抽屑狀(zhuàng)態。當鑽孔長徑比過大時,可適當(dāng)加大後油路的壓力,以保證不因油壓降過大而降低抽屑功效。SIED 係統的分調式功率增補型噴吸鑽抽屑裝(zhuāng)置提高了係統對於(yú)不同尺(chǐ)寸(cùn)深孔排屑的適(shì)用性。Sl ED 機(jī)床具有全麵(miàn)的兼容性(xìng),適用於包括內排屑深孔鑽、深孔擴鑽、套(tào)料(liào)鑽、深孔鉸刀、深孔鏜頭、電鍍金剛石深孔刀具在內的各種內排屑深孔刀具。Sl ED 係統是(shì)一種正在逐漸推廣的(de)係統,也是目前較先進的係統。目前,Sl ED 係(xì)統可將最小鑽孔直徑(jìng)縮小(xiǎo) φ5mm 以下。深孔加工關鍵技術近(jìn)年,針(zhēn)對深(shēn)孔加工中存在的問題,國內外專家學者進行(háng)了大量的(de)研(yán)究,主要涉(shè)及深孔加(jiā)工的鑽削力學(xué)、切屑形態及排屑方法、在線監控、加工係統及設備(bèi)等(děng)方麵。
1 、 鑽(zuàn)削力學研究
鑽(zuàn)削靜力學是研究(jiū)鑽削過程力學特性的基礎,過去幾十(shí)年(nián)間得到了專家學者的廣(guǎng)泛關注。Altintas以標準麻花(huā)鑽為研究對(duì)象,推導(dǎo)了鑽頭切削刃微元的幾何角度關係並利(lì)用直角切削到斜(xié)角切削的變換建(jiàn)立了麻花鑽的鑽削力和扭矩模型(xíng)。白萬民等以鑽槍為(wéi)研究對象(xiàng),對(duì)深孔鑽削過程進行了(le)受力分析,建立了槍鑽的鑽削力模(mó)型,並(bìng)提出了試(shì)驗和模型相結合的求解方法。李(lǐ)琦等以內排屑深孔鑽為研究對(duì)象,通過試驗方法建(jiàn)立了鑽削力的經驗公式,試驗表明各段切削(xuē)刃對切屑變形的影響趨勢基本相同。除鑽(zuàn)削靜力學(xué)的
研究外,鑽削動力學也是近年來深孔加(jiā)工領域的研究熱點之一。朱林等通過鑽削試驗,根據鑽削過(guò)程模型和試驗數據分析了影(yǐng)響鑽削穩定性的因素,在此基礎上(shàng)改進了深孔鑽的結構設計,提高了鑽削的穩定(dìng)性。常豆(dòu)豆以 BTA 係統為研究對象,分析了鑽(zuàn)削過程中由於速度和位移反饋引起(qǐ)的切削顫振現象(xiàng),建立了 BTA 鑽橫向、軸向、扭轉方向的動力學模型及動態鑽削力模型(xíng)。Perng等(děng)根據 Hamilton 原理,考慮切削液和軸向壓力的影響,分別(bié)推導了基於 Timoshenko 和(hé) Eule-Bemoulli 梁模型的深孔鑽杆運(yùn)動方程,用旋轉鑽杆和非旋轉(zhuǎn)鑽杆兩種不同方式添加隨機激勵,研究了鑽杆的動態(tài)特性。
Ahmadi 等研(yán)究了鑽杆不同方向的穩定性,建(jiàn)立了通用的鑽(zuàn)削過(guò)程(chéng)穩定性模型,並采用(yòng)磨(mó)損刀具的鑽削試驗驗證了模型的(de)準確性。許多研究表明,深孔鑽削過程中,鑽杆(gǎn)係統存在明顯的非(fēi)線性特(tè)征,針對這(zhè)一問題,Kovacic建立了深孔鑽削鑽杆係統的(de)非(fēi)線性動力學模型,並采用不同的刀具前角、剪切角以及進給量對鑽削顫振機理進行了較全麵的理論分析。因鑽頭的幾何特點、鑽削(xuē)加工的封閉性以及鑽削過程切屑和熱效應影響,鑽削相對於銑削、車削等切削過程更為複雜。目前針對鑽削力學的研究中,大多以試(shì)驗和數(shù)值模擬(nǐ)作為(wéi)研(yán)究手段,得到的模型(xíng)和結論主要依靠經驗,缺乏對鑽削機理的透徹理解,相關理論尚(shàng)不完(wán)善。但這些研究對於了解鑽削過程,改進鑽削係統、鑽(zuàn)削刀具、鑽削工藝,以及優化鑽削(xuē)參數具有(yǒu)指導意義。
2 、切屑形態及排屑方(fāng)法研究
排屑過程是深孔加(jiā)工與一般孔加工相比最顯著的不同之處。在深孔加工中(zhōng),由於排屑空間(jiān)狹小,排(pái)屑過(guò)程變得困難且重要,直接影響加工的順利進(jìn)行,決定了(le)孔加工的質量。因(yīn)此,切屑形態以及排屑方法一直是深孔加工領域的難點與研究熱點(diǎn)。趙如意等(děng)通過試驗(yàn)研究(jiū)了 3 種不(bú)同刀片在(zài) BTA 鑽過程中,在不同切(qiē)削參數下的切屑形態和切屑容屑係數(shù)對排屑的影響。試驗表明,切屑容屑(xiè)係數越小(xiǎo)排屑越好,而且 C 形切屑(xiè)的切屑容(róng)屑係數最小,對排屑最有(yǒu)利。汪誌明對負壓抽屑裝置進行(háng)了研究,改善了深孔加工係(xì)統的排屑條件。馬龍等通過 SIED 深孔鑽削試驗研究(jiū)了不同主(zhǔ)軸轉速和進(jìn)給下切屑的形(xíng)態和容屑係(xì)數對排屑效果的影響。針對深孔加工中斷屑和排屑的問題,隈(wēi)部淳一郎(láng)在 20 世紀50 年代提出了振動(dòng)鑽削理論,即在鑽削過程中在某一個或幾(jǐ)個特定方(fāng)向(xiàng)對鑽杆或(huò)工件施加某種有規律的振動激(jī)勵,鑽頭在振(zhèn)動中切(qiē)削,使切削用量按某種規律變化,以控製(zhì)切(qiē)屑的大小和形狀,達到避免發生切屑堵塞的(de)目標(biāo)。在國內,薛萬夫等在1982 年開發出振(zhèn)動鑽削設備,並對(duì)深孔振動鑽削中切削刃(rèn)的相鄰運動(dòng)軌跡進行了理論分析,得出了保證斷屑的(de)加工條件。西安石油大學朱(zhū)林,西安交通大學高本河等以及成都工具(jù)所的樊(fán)鐵镔也在深孔加(jiā)工的低頻振動鑽削開展(zhǎn)了大量研究。目前,振動(dòng)鑽削已(yǐ)成為深孔加工的一個(gè)重要分支。排(pái)屑問題是(shì)深孔加工中最關鍵的(de)問題之一,針對這一問題,近年來(lái)專家學者們從鑽削刀具結構、抽屑裝置、鑽削參數以及鑽削方法等方麵進行了研究,發明了(le)大量的新刀具、新裝置和新工藝,排屑(xiè)問題得到一定改善。未(wèi)來,切屑(xiè)形態(tài)和排屑過程的定(dìng)量(liàng)化以及各種排屑結構、裝置和方法(fǎ)的融(róng)合有待進(jìn)一步研究(jiū)。
3 、在線監控研(yán)究

由於(yú)大深徑比以(yǐ)及加工時的封閉或(huò)半封閉狀態,無法直接觀察到深孔加工過程中刀具的狀態變化。因此,通過(guò)各種手段對深孔加工過程進行在線監測與控製成為深孔加工的另一個重要(yào)研究方向。在線監控的研究主要以切削力、機床功率、聲發射、振動加速度等信號作為測量參(cān)量,在線監控鑽頭磨損(sǔn)及失效、振動、切屑堵塞、軸線偏移(yí)等(děng)現(xiàn)象(xiàng),研究問題(tí)包括深孔加工在線監測的信號(hào)處理、信號特(tè)征提取和(hé)加工狀態識別與反(fǎn)饋控製。常見的深孔加工在線監測方案如圖 6 所示。Kavaratzis 等將深孔鑽削過(guò)程分為 4 個階(jiē)段,以鑽削力和扭矩為監測信(xìn)號(hào),采用多層級的控製方法,針對鑽削過程的不同階段采用不同(tóng)的控製策略。在國內,哈爾濱工業大學、北京理工大學、西安理工大學、上海交通大學等院(yuàn)校和一些科研機構都對此進行了深入研究。其中,哈爾濱工業大學的王清明等提(tí)出利用多個特征參數綜合監測(cè)鑽削(xuē)過程,通(tōng)過大量試驗,觀察(chá)刀具在(zài)破損、折(shé)斷等異常情況下,各(gè)個特征參(cān)數的變化規律,並設(shè)定閾值,對鑽削加工過程進(jìn)行監測。北京理工大(dà)學的王忠民等(děng)利用模糊模式識(shí)別技術處理經過離散二(èr)階小波變換分解的切削過程聲發射信號樣本,實現(xiàn)對刀具磨損(sǔn)狀態的在線(xiàn)識(shí)別。西安理工大學的李鵬(péng)陽等以鑽削軸向力和扭矩為監測信號,通過(guò)對信號進行幅域和頻域(yù)分析,提取了特征信號(hào)隨鑽(zuàn)頭磨損量的變化規律。上海(hǎi)交通大學的孫(sūn)程成等分析了槍鑽擴散磨損和粘結磨損的形成機理,並以(yǐ)鑽削力、扭矩和聲(shēng)發射(shè)為監(jiān)測信號對鑽頭狀態進行監測,采用聲發射信號對刀具磨損(sǔn)狀態(tài)進行了表(biǎo)征。現有文獻及相(xiàng)關報道中,在在線監測方麵針對信號處(chù)理、特征提取和狀態識別3 個(gè)領域均有大量研(yán)究(jiū),以上研究為在線監控係統及(jí)設備的研發提供了理論依據,但多數為針對各領域相關算法及策(cè)略的獨立研究,缺乏對完整在線監控閉環係統(tǒng)的整體研究。此外,針對深孔(kǒng)加工(gōng)中易出現的故障,文獻中對刀具狀態的研究較多,而針對(duì)鑽削過程的其他現象諸如切屑堵塞、鑽杆振動以及孔擴大、偏斜(xié)等與孔加工質量相關的問題仍需要進一步研究。
4 、深孔(kǒng)鑽削(xuē)設備的研發(fā)
在深孔加(jiā)工中,由切屑堵塞和(hé)鑽頭磨損失效造成的鑽杆折斷是最常見的故障(zhàng)。近年來隨著傳感技術的發展,越來越(yuè)多的在線監測設備已經應用於(yú)深孔加工領域。目前,在深孔鑽削力測量技術方麵(miàn)處(chù)於國際領先地位的德國 Dortmund 大學(xué)的科研工作者 Raabe 等發明了帶有測力元件的測量鑽頭,可以直接測量切削分量。日本町田鐵工生產的全自動鑽床(chuáng) Micro-hole 配備了扭矩傳感器和鑽頭磨損監控係統,鑽削過程中當鑽頭所受扭矩超過預設(shè)值時,係統控製鑽頭(tóu)退刀並重新開始鑽削(xuē),實現了鑽削過程(chéng)多次退刀排屑方法的自(zì)動化。近幾年國內越來越多的專家學者已開始投入研發深孔加工的新設備、新裝置。中北大學的關(guān)世璽等結合力傳感器、加速度傳(chuán)感器以及電(diàn)磁離合器自主(zhǔ)研發了電磁式過載保護裝置,可以實時(shí)監控加工的全過程,對深孔加工刀具係統(tǒng)和(hé)被加工零件起到保護作用。蘇州大學的張勇等利(lì)用 PLC 和交流變(biàn)頻調速技術把普通車床改造成具有電氣控製係統的深孔加工機床(chuáng),降低(dī)了(le)加工成本,提高了深孔加工的效率和精度。德州德隆(lóng)機床公司(sī)自主研發(fā)了可在塑料模具上進行多孔係加工的ZK2103 型三(sān)坐標數控深孔鑽床,其鑽孔直(zhí)徑範圍為
φ4~φ30mm,最大加工深度 1200mm,在國內處於領先水平。目前,國產深孔加工設備相對德(dé)國、美國等製造(zào)業發達的國家仍較落後。在(zài)我國航空企業中,大多數仍采用傳統鑽削方法,對專(zhuān)用深孔加工設備(bèi)的使用較少,少數企業(yè)通過對普通機床的改造以滿足深孔加工的需求。目前,高(gāo)性價比的(de)專用深孔加工設備的研發仍是我國航空企業亟待解決的問題。
深孔加工技術(shù)發展趨勢
1 、智能加工
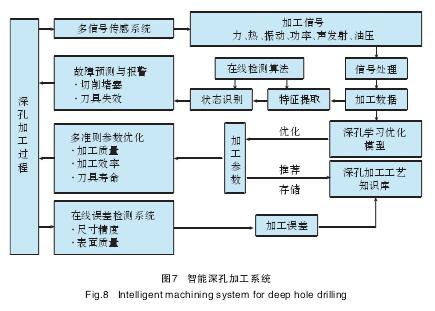
目(mù)前,我國航空企業在複雜殼體零件深(shēn)孔加工中,對於鑽削參數的設(shè)定往往(wǎng)是憑經驗。為避免加工中出現鑽頭折(shé)斷和切屑堵塞等問題,設定(dìng)的鑽削參數通常很保守(shǒu),這樣就造(zào)成了加工效率低下,加工質量難以(yǐ)保證。近年來,隨(suí)著(zhe)計算機輔(fǔ)助製造技術、傳感技術以及機器學習等領域的發展,加工設備及加工係統具(jù)有對加工狀態的自主感知,對加工(gōng)工藝知識的學習、進化、積累,以及對加工過程的實時反饋、決策等智能化功能已成為可能。智能加(jiā)工已成為(wéi)未來(lái)深孔加工發展的(de)必然趨(qū)勢,發展具有(yǒu)自主感知、學習(xí)、進化、決策功能的智能深孔加工係統將成為深(shēn)孔加工的重要研究(jiū)方向(xiàng)。智能深孔加工係統的結構如圖 7 所示(shì)。智能深孔加工(gōng)係統包括多信號傳感係統、在線(xiàn)誤差檢測係統等感知模塊,通過(guò)時監測得到深孔(kǒng)加工(gōng)過程力、熱、振動、功率、聲發射、油壓等信號,利用在線監測算法將處理後的加工數據做特征提取及加工狀態識別,用於切(qiē)屑堵塞、刀(dāo)具(jù)失效等故障預測與報警;同時,利用智能學習優化模型(xíng)並結合工藝知識庫,以加工(gōng)數據和在線誤差檢測係統獲取的孔尺寸精度和表麵質量信息作為輸入,實(shí)現加(jiā)工質量、加工效率和刀具壽命等多準(zhǔn)則加工參數優化(huà),實時反饋到深孔加工過程,完成深孔加工學習進化的閉環係統。目前在機械加工領域中,智能刀柄、智能刀具的等智能元器件,以及智能加工係(xì)統的研發已成為研究的熱點(diǎn)與趨勢。已有一些公司開發了商(shāng)業化的(de)加工過程智能監(jiān)控係統(tǒng),比如ARTIS 在線監控係統,該係統利用傳感及在線監測技術,不僅可監測(cè)加工過程機床狀態、刀(dāo)具狀(zhuàng)態、異常及故障,而且可通過其內部算法對加工周期(qī)進行優(yōu)化,根(gēn)據在每一個加工(gōng)周期中工藝知識的學習(xí)與積累,優化下一個(gè)加工周期的加工參數,使加(jiā)工係統(tǒng)具有自主學(xué)習、進化的能力。未來,隨著相關學科與技術的不斷發展,智能深孔加工係統將亦趨成(chéng)熟。
2 、特種加工
深孔機械加工(gōng)由於需要刀具,屬於接觸加工,這就導致無法(fǎ)避免一些固有問題(tí):例如刀具材料的(de)硬度必須大於工件(jiàn)材料、切削力導致的變形(xíng)和振動、工件殘餘應(yīng)力等。當(dāng)麵臨未來航空複雜殼體零件的複雜孔係結構、微小孔(kǒng)以及新材料(liào)時(shí),傳(chuán)統(tǒng)機械加工難以達到要(yào)求。特種(zhǒng)加工技術是借助電能、熱能、化學(xué)能、聲能、光能等多(duō)種能(néng)量或將幾種能量進行複合以實現材(cái)料切除的加(jiā)工(gōng)方法。自943 年前蘇聯科學家拉(lā)紮(zhā)林柯發明電火花加(jiā)工方法後,利用機械方(fāng)法以外的非傳統加工方式得到了大量的研究,形成了特種加工這一新的發展領域,可以實現超硬、超軟、超精、超光和超微等加工。目前,對於(yú)微小孔的加工,特種加工是主要的加工方法。一(yī)些學者已經開展了針對深孔的特(tè)種加工方法的(de)研(yán)究,主要有:電火花(huā)加工、電化學加(jiā)工、超聲加(jiā)工、激光加(jiā)工、電子束加工、離(lí)子束加工、液體噴射加工等。未來,隨著深孔(kǒng)加工的要求越來越高,機械加工方法將難以滿足,深孔的特種加工方(fāng)法(fǎ)將成為學術界的關注(zhù)點(diǎn)之一。
3、綠色加工
近年來,隨著環境保(bǎo)護的(de)迫切度越來越高,對製造業綠色化提出了(le)更高的要求。傳統深孔加工由於(yú)需要冷卻和排屑,會產生大量的切削(xuē)液(yè),造成環境汙染和資源(yuán)浪費。為節(jiē)省資源和減(jiǎn)少汙染物排放,綠色加工成為未來深(shēn)孔加工發展的必然趨勢(shì)。目(mù)前新型綠色加工技術主要有:綠(lǜ)色(sè)切削液、微量潤滑、壓縮空氣冷卻和幹式加工。幹式加工即在加工過程中不(bú)使(shǐ)用切削液,這從根本上避免了切削液的處理以及排放造成的汙染,同時也降低了加工成本。但(dàn)目前的深孔加(jiā)工技術水平尚難(nán)以處理幹式(shì)加工中產生的大量(liàng)切削熱,因此暫時無法推廣應用(yòng)。相對來講,使用微量切削液可較大程度減少汙染(rǎn),同(tóng)時技(jì)術難度大大小於幹式切削,目前在學術界受到更多的關注。此(cǐ)外,已有學者研究具有生(shēng)態性能的冷卻劑,這既降低了散熱的技術難度(dù),又(yòu)可實現綠色加(jiā)工,並且其(qí)對人體健康無影響,也是一種有潛力的發展方向。未來,深孔加工的綠色化將成為工業界不可忽視的研(yán)究內(nèi)容。
結論(lùn)
深孔加工技術是一項多學科交叉的綜合應用技術,目前在理論(lùn)和應用方(fāng)麵都(dōu)還不夠成熟。由於深(shēn)孔加工的困難,迫切需要對其理論和技術進行(háng)更加深入的研究。本文結合航空複雜殼體零件的深孔加工,介紹了深孔加工(gōng)的概念,分析深孔加工的工藝特點及難點(diǎn),闡述深孔加工發展的曆程和目前的發(fā)展現狀。通過(guò)對文獻資料的(de)調研,給出深孔加工的關鍵(jiàn)技術,並結合目前機械工業(yè)的發展現(xiàn)狀(zhuàng)展望了深孔加(jiā)工未來的發展趨勢(shì)。隨(suí)著數字化技術、傳感技術、信息技術等的快速發展(zhǎn)和不斷融合,深孔加工技術將會朝著智能化、多樣化、環境友好的方向不斷發展(zhǎn),在我國航空製造業中發揮更大的作用。
來源:西北工業大學(xué)現(xiàn)代設計與集成製造技術教育部重點實驗室 西(xī)安航空動力控製科技有限公司
投稿箱:
如果您(nín)有機床行業、企業相關新聞稿件發表,或進行(háng)資訊合作,歡(huān)迎聯係本網編輯部, 郵箱:skjcsc@vip.sina.com
如果您(nín)有機床行業、企業相關新聞稿件發表,或進行(háng)資訊合作,歡(huān)迎聯係本網編輯部, 郵箱:skjcsc@vip.sina.com
更多相關信息(xī)
業界視點
| 更多
行業數據
| 更多
- 2024年11月 金屬切削機床產量數(shù)據
- 2024年11月 分地(dì)區金屬切削機床產量數據
- 2024年11月 軸承出口情況
- 2024年11月 基(jī)本型乘用車(轎車)產量數(shù)據
- 2024年11月 新能源汽車產量數據
- 2024年11月(yuè) 新能源汽車銷量情況
- 2024年10月 新能源汽車產(chǎn)量數據
- 2024年10月 軸承出口情況
- 2024年10月 分地區金屬切削機床產量數據
- 2024年10月(yuè) 金屬切(qiē)削機床(chuáng)產量數據(jù)
- 2024年9月 新能(néng)源(yuán)汽車銷量情況
- 2024年8月 新能源汽車(chē)產量數據
- 2028年8月 基本型乘用車(轎車)產量數(shù)據