350 km /h 標準動車組電機軸承(chéng)蓋鑽(zuàn)銑工裝
2021-7-9 來源: 中(zhōng)車永濟電機有限公司 作者:單國慶,許廣永,王(wáng)海龍,齊 影,李 輝等
摘要: 針(zhēn)對 350 km/h 標準動車組電機(jī)傳動端、非(fēi)傳動端軸承蓋鑽銑加工後,軸承蓋軸向安裝孔、徑向深槽孔的位置(zhì)尺寸超差(chà)原因進行分析,設計製作 350 km/h 標準動車組電機傳動端、非傳動端軸承蓋鑽(zuàn)銑加(jiā)工(gōng)專用工裝。通過實際應用(yòng),保證了 350 km/h 標準動車組電機傳動端、非傳動端軸承蓋軸向安裝孔、徑向深槽孔的位置尺寸,提高了生產效(xiào)率,降低了勞(láo)動強度(dù)。
關鍵詞: 350 km/h 標(biāo)準動車組; 電機軸承蓋; 鑽銑工裝
1、電機軸承蓋交檢現(xiàn)狀及原因分析
1. 1 現狀
350 km /h 標準動車組電機傳動端軸承蓋結構如圖 1 所示,傳(chuán)動端軸承蓋 4 × 9 mm 軸向安裝孔與(yǔ) 125M6 ( - 0.008 / - 0.033) 軸(zhóu)承室 A、軸承室(shì)端麵 B 的位置度 0.2 mm 及軸(zhóu)承蓋中心線的位置角度 45°超差,一次交檢合格率為 89. 5% 。
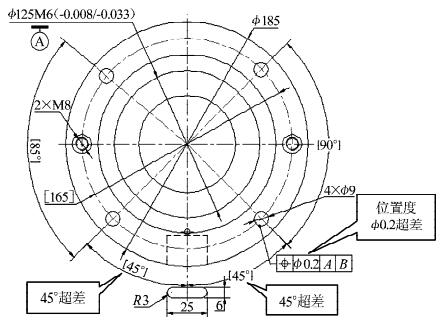
圖 1 350 km/h 標準動車組電機傳動端軸承蓋結構示(shì)意圖
非(fēi)傳動端軸(zhóu)承蓋 4 ×9 mm 軸向安(ān)裝孔與90M6 ( - 0. 006 / - 0. 028) 軸承室 A、軸承室端麵 B的位置度 0.2 mm 及軸承蓋(gài)中心線的位置(zhì)角度 45°超差(chà),一次交(jiāo)檢合格率為87.6% 。
1. 2 原因分析
350 km /h 標準動車組(zǔ)電機傳動端、非傳動端軸承(chéng)蓋加工借用 250 km /h 標(biāo)準動車組電機軸承(chéng)蓋加工工裝(zhuāng)。由於借用工裝定位台的長度偏短,與軸承蓋定位(wèi)孔的配合間隙過大,定位銷為圓柱形銷,軸承蓋徑向過定位,圓周方向(xiàng)配合間隙過大,軸承蓋定(dìng)位不可靠,定(dìng)位精度低,造成 350 km /h 標準動車(chē)組(zǔ)電機傳(chuán)動(dòng)端、非傳動端軸承蓋鑽銑加工後,軸向安裝孔、徑向深槽孔的位置尺寸超差。傳動端軸承蓋鑽銑胎體定位台長度 10 mm,長度偏(piān)短。定(dìng)位台與傳(chuán)動端軸(zhóu)承蓋軸承室的最小配(pèi)合間隙為: - 0. 033 -( - 0.135) = 0102 mm,配合間隙過大(dà)。非傳(chuán)動端(duān)軸承蓋鑽銑胎體定位台長度 6 mm,長度偏短。定位台與非傳(chuán)動端軸(zhóu)承蓋軸承室的(de)最小配合間隙為: -0.028 - ( - 0.116) = 0.088 mm,配合間隙過大。工裝定位銷圓周方向上偏差 - 0. 25 mm,與軸承蓋 9( + 0.2 /0) mm 孔的配合間隙過大。
2、改進措施
2. 1 設計製作軸(zhóu)承蓋鑽銑(xǐ)加工專用工(gōng)裝
為解決(jué) 350 km /h 標準動(dòng)車組電機傳動端、非傳動端軸(zhóu)承蓋鑽銑加工的工(gōng)藝、質量問題(tí),設計製作350 km /h 標動電機傳動端、非傳動端軸承蓋(gài)鑽銑(xǐ)加工專用工裝,如圖 2-3 所示。
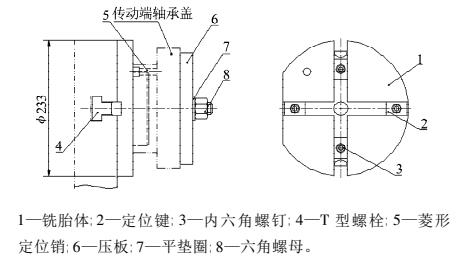
圖2 傳動(dòng)端軸承蓋鑽銑工裝
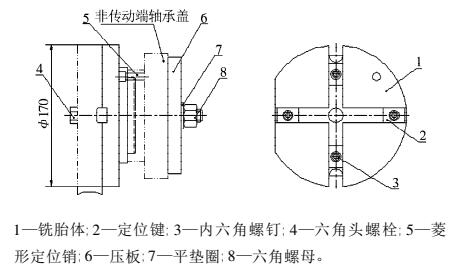
圖 3 非傳動端軸承蓋鑽(zuàn)銑工裝
350 km /h 標準(zhǔn)動車組電(diàn)機傳動端、非傳(chuán)動端軸承蓋分別通過軸承室由工裝定位(wèi)台定位,通(tōng)過壓板、螺杆壓緊。工裝通過定位鍵與臥式加工中心(xīn)直角板上的 T 型槽定位,可自動(dòng)找正(zhèng)工裝(zhuāng)的中心位置。工裝由六角螺栓、螺母固定在臥式加工中心直(zhí)角板上(shàng)。
2.2 軸承蓋鑽銑胎體定位台長度、配(pèi)合間隙改進
傳動端、非傳(chuán)動端軸承(chéng)蓋分別通過內孔由(yóu)工裝軸承蓋裝夾困難(nán)。由於配合(hé)間隙過大,軸承蓋定位精度低,傳動端、非傳動端軸承蓋軸向安(ān)裝孔、徑向深槽孔的(de)位置尺寸無法保證(zhèng)。同時軸承蓋裝夾剛(gāng)性差,加工切削用量小,生(shēng)產效率低。
傳動端、非(fēi)傳動端軸承蓋鑽銑胎體見圖 4-5。
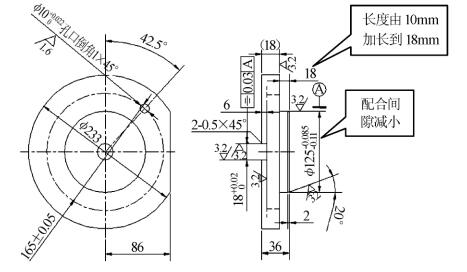
圖 4 傳動端軸承蓋鑽銑胎體
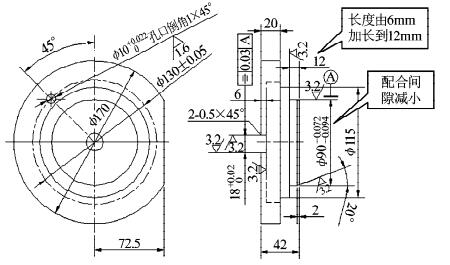
圖 5 非傳動端軸承蓋鑽銑胎體
傳動端軸承蓋鑽銑胎體(tǐ)定位台長度尺寸由原來(lái)的 10 mm 加長到 18 mm,最小配合間隙由 0 102 mm減小到: - 0.033 - ( - 0.085) = 0.052 mm 。非傳動端軸承蓋鑽銑胎體定位台長度尺寸由原來的 6 mm 加長到 12 mm,最小配合(hé)間隙 0.088 mm減(jiǎn)小到: - 0.028 - ( - 0.072) = 0.044 mm 。
2.3 軸承(chéng)蓋鑽銑工(gōng)裝定位銷改進
傳動端、非傳動端軸承蓋鑽銑工裝定位銷為圓柱形銷,軸承(chéng)蓋徑向過定位,圓(yuán)周方向(xiàng)配(pèi)合間隙過大,軸承蓋定位不可(kě)靠,定位精度低,造成(chéng) 350 km /h標準動車組電機傳動端、非傳動端軸承(chéng)蓋鑽(zuàn)銑加工後,軸向安(ān)裝孔、徑(jìng)向深槽孔的位置尺寸超差。
傳(chuán)動端、非傳(chuán)動(dòng)端軸承(chéng)蓋菱形定位銷如圖 6-7所示。
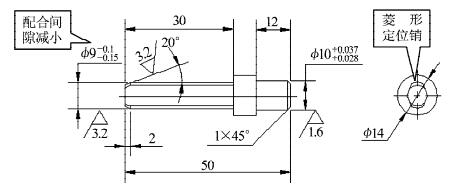
圖(tú)6 傳動端軸承蓋菱形定位銷
傳動端(duān)軸承蓋鑽銑工裝定位銷由圓柱形改為菱形,避免了傳動端(duān)軸承蓋(gài)徑向過定位(wèi),圓周方向定(dìng)位銷上偏差由 - 0.25 mm 改為 - 0.1 mm,減小了與軸承蓋 9( + 0.2 /0) mm 孔的配合(hé)間隙。
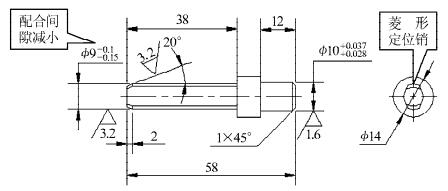
圖7 非(fēi)傳動(dòng)端軸承蓋菱形定位銷
非傳(chuán)動端軸承(chéng)蓋鑽銑工裝(zhuāng)定位銷由圓柱形改為菱形,避免了非傳動端軸承蓋(gài)徑向過(guò)定位,圓周方向定位銷(xiāo)上偏差由 - 0.25 mm 改為 - 0.1 mm,減小與軸承蓋 9( + 0.2 /0) mm 孔的配合間隙。由於鑽銑胎體定位台長度尺(chǐ)寸加長,定位台與軸承蓋軸承室配合間隙減小,避免了裝夾過程(chéng)中軸承蓋的脫落。定位(wèi)銷由圓柱形改為(wéi)菱形,使(shǐ)軸承蓋定位精度(dù)提高,定位更可靠,保證(zhèng)了軸向安裝(zhuāng)孔、徑向深槽孔加工的位置尺寸(cùn),提高了傳動端、非傳(chuán)動端軸承蓋在(zài)電機運行中的可靠性。同時軸承蓋裝夾剛定位台定位,由於原定位台長度偏短,與軸承蓋內(nèi)孔配合間隙過大,裝夾過程中,軸承蓋時常脫落,造成性提高,加(jiā)工中切(qiē)削用量增大,提(tí)高了生產效率,降低了生產製造成本。
3、技術特點
該鑽銑(xǐ)工裝通過臥式加工中心工(gōng)作台(tái)的旋轉,可獲得兩個加工位置。鑽銑工裝通過定位鍵與臥式加工中心直角板上的 T 型槽定位,可自動找正鑽銑工裝的中心位置,使軸承蓋在一次裝夾後,可分別完成軸向安裝孔和徑向深(shēn)槽孔的鑽(zuàn)銑加工(gōng),提高了生(shēng)產效率,保證(zhèng)了軸(zhóu)承(chéng)蓋軸向安裝孔、徑向深(shēn)槽孔之間的位置尺寸。同時,鑽銑(xǐ)工裝定位精度高,避免了(le)借用工裝定位精度(dù)低的問題,由此保證了(le)傳動端、非傳動端軸(zhóu)承蓋軸向安裝孔、徑向深槽孔的鑽銑加工質量。
4、結束語
通(tōng)過使用上述(shù)鑽銑工裝,對所(suǒ)加工的 350 km /h標準動車組電機傳動端、非(fēi)傳動端軸承蓋進行三坐標檢測,軸承蓋(gài)軸向安裝(zhuāng)孔(kǒng)、徑向深槽孔的位(wèi)置尺寸及兩者之間的位(wèi)置角度,全部符(fú)合產品圖紙設計(jì)要求,一次(cì)交檢合(hé)格率提高到 100% 。
投稿箱:
如果(guǒ)您有機床行業、企業相關新聞稿件發表(biǎo),或進行資訊合作,歡迎聯係本網編(biān)輯部, 郵箱(xiāng):skjcsc@vip.sina.com
如果(guǒ)您有機床行業、企業相關新聞稿件發表(biǎo),或進行資訊合作,歡迎聯係本網編(biān)輯部, 郵箱(xiāng):skjcsc@vip.sina.com
更多相關信息
業界視點
| 更多
行業數(shù)據
| 更多
博文選萃(cuì)
| 更多
- 機械加工過程圖示
- 判斷一台加工中心精(jīng)度的(de)幾種辦法
- 中走絲線切(qiē)割機床的發展趨勢
- 國產數控係統和數控機床何去何從?
- 中國的技術工(gōng)人都(dōu)去(qù)哪裏了?
- 機械(xiè)老板做了十多年,為何還是小作坊?
- 機械行業最新自殺性營銷,害人(rén)害己!不倒閉(bì)才
- 製(zhì)造業大逃亡
- 智能時代,少談點智造,多談點製造
- 現(xiàn)實麵前,國人沉(chén)默。製造業的騰飛,要從機床
- 一文搞(gǎo)懂數控車床加工(gōng)刀具(jù)補償功能
- 車床鑽孔攻螺紋加工方法及(jí)工裝設計
- 傳(chuán)統鑽(zuàn)削(xuē)與螺旋銑孔加工工藝的區(qū)別