車床傳統加工工藝在數控車加工(gōng)中的實現及優(yōu)化(huà)分析
2019-7-5 來源(yuán): 杭州市臨平職業高級(jí)中學 作者:屈政偉
摘 要:當前,數控車加工逐漸呈現出科學(xué)性、集成性(xìng)以及多元性,對(duì)車床加工工(gōng)藝的(de)要求也更為嚴格(gé)。在這一背(bèi)景下,圍繞數控車加工與車床傳統加工工藝的結合問(wèn)題展開分析與(yǔ)研(yán)究,並(bìng)提出了優化車床加工工藝的相(xiàng)關建議。
關鍵詞:數控(kòng)車 車床(chuáng)加工 優化
數控即數字控製技(jì)術,是指在數字化(huà)信號(hào)輔助下對設備運行、加工過程進行全麵控製(zhì)的一種(zhǒng)自動(dòng)化技術。數控車床在數控技術輔助下,根據事先編製數控程序(xù),對工件進行自動且高效加工處理,具有高度自動化、精確(què)性的特點,在(zài)現(xiàn)代機械製造業中具有非常重要的應用價值與(yǔ)潛力。尤其在當前機械製造產業呈現出集(jí)成化、智(zhì)能化發展趨勢的背景下,如何在數控車床加工中融入傳統車(chē)床加工工藝,以改進加工流程與方法,已成為業內人士高度重視的一項課題。已有大量研究表明,數控(kòng)車床可以以數控(kòng)技術以及數控程序為引導,將已經編製好的數控程序引入加工過程中,提高機械(xiè)零部件加工中數控設備的運行(háng)效率,這成為整個機械製(zhì)造工藝發展的主流趨勢之一。本文即圍繞車床傳統加工工(gōng)藝在數(shù)控車加工中的(de)實現(xiàn)及其優化措施(shī)展開分析與探討。
1 、短軸零(líng)件連(lián)續(xù)加工
在機械加工領域操作實踐中,短軸類零件具有較大的尺(chǐ)寸,有良好的剛性,但自身軸向尺寸較大(dà)。在(zài)短軸(zhóu)類零件的製作(zuò)加工中(zhōng),進行批量生(shēng)產,但生產中所(suǒ)選用的毛坯料以長料為主(zhǔ),必須經過處(chù)理後方可作為毛坯使用。針對這一問題,在車床傳統加工工藝中所采(cǎi)取的方法是:將長毛坯料伸出卡盤 100 ~ 200mm,以實現一次性裝夾,連續加工多個(gè)零件,通過此種方式來促進短(duǎn)軸類零件加工生產效(xiào)率(lǜ)的提升。而(ér)從數控加工的角度來說(shuō),為實現對多(duō)個短軸類零件的連續性加工作業,可以借助子程序調用的方式實現。在數控編程中(zhōng),通過 G54 ~ G59 實現對短軸(zhóu)類工件(jiàn)坐標係的設置,在 X 軸上取值完全一致,在 Z 軸上取值有一定調整,以待加工(gōng)短軸類零件工(gōng)件長度、斷麵切削餘量以及切斷刀寬的綜合作為 Z 軸相(xiàng)差值。換言之,假定長毛坯料伸出卡盤的長度足夠,很容易實現對多個短軸類零件的連續加工作(zuò)業。
2、梯形螺(luó)紋工藝(yì)加工
在數控機(jī)械(xiè)操作實(shí)踐中,針對(duì)梯形(xíng)螺紋的加(jiā)工是較常涉及的問題之一。梯形螺紋加工深度較(jiào)深,在普通車床加工中為了完成加工作業,常常需要采取借刀的工藝方案。換言之(zhī),在螺紋加工深度相同的情況下,借助於小(xiǎo)拖板對前後位置(zhì)進行合理調節(jiē),以確保機床螺紋刀(dāo)以單(dān)麵方式進行切削,減少了切(qiē)削加工過程中所承受作用力,確保加工作業的順(shùn)利完成。而在(zài)數控車床輔助下,完全可以通過數控編程的方式(shì)提前完成對小拖(tuō)板位置(zhì)的調節工作,以達到提高整個梯形螺紋部件加工精度與自動化水平的目(mù)的。需要特(tè)別注意的是,在對(duì)梯形螺紋進行加工的過(guò)程中,加工螺紋借(jiè)刀程序會反(fǎn)複運行,直至達到最終螺紋加(jiā)工深度。在其後多個(gè)步驟的借刀過程中,借刀所需距離不斷降低,此種方式能夠避免在數控加工過程中梯形螺紋出現(xiàn)過切問題,進而影響整體加工效果。
3、連續(xù)走刀自動加工
在機械零(líng)部件(jiàn)生產製造(zào)加工技術水平不(bú)斷提升的背景下,自動化(huà)加工形式開始投入生產實(shí)踐(jiàn)中。在這一背景下,實現“借刀”的最終目的在於連續性走刀加(jiā)工。在數控程序的輔助下,幫助車床實現連續性走刀,同時實現 2 軸(zhóu)聯動運(yùn)行的效果,並以(yǐ)此種方式完(wán)成軸類機械零件(jiàn)中圓弧以及錐度等特殊形狀的加工作(zuò)業。這一(yī)特點在任何一軸類零件數控(kòng)車床加工中均有著非常廣泛的應用價值。通過數(shù)控車床連續性走刀的方式,完成對軸類零件倒角、端麵、外徑的連續性走刀切削(xuē)作業,從而達到提高數控機械零部件加工效率,改善表麵加工質量水平的目的。某零件如圖 1所示,在普通車床傳(chuán)統加工過程中,其遵循的工藝流程(chéng)為:一是先左端加工:車端麵→粗(cū)車外圓至標準尺寸→精車外圓至標準尺寸(重複上述操作直至圓料尺寸達到設計標準)→倒角→去除毛刺;二是掉頭裝夾直徑 38mm 的外圓,加工右端:粗(cū)車外圓(yuán)至標準尺寸→精車外圓至標準尺(chǐ)寸→切槽→倒角→去除毛刺→螺紋加工。
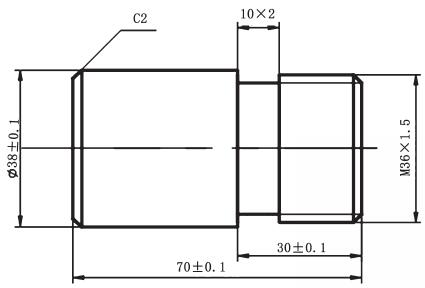
圖 1 某毛坯圓件加工尺(chǐ)寸(cùn)示意圖
結合圖 1 來看,在普通車床加工工藝技術處理下,被(bèi)加工零部件表麵(miàn)可能產(chǎn)生一定毛刺,其主要原因是:倒角放在車外圓後(hòu),該工序中工件(jiàn)持(chí)續受到(dào)刀具(jù)作用力(lì)擠(jǐ)壓,導致(zhì)精車(chē)後被加工部(bù)件右端產生一定毛刺,因此必須在退刀後增加去(qù)除毛刺這一處理工序。
而在(zài)數控車床加工技術的輔(fǔ)助下,可以(yǐ)通過連續走刀(dāo)的方式來避免該問題,這樣既可提高加(jiā)工質(zhì)量,還能夠減少毛刺產生的風險,省(shěng)略毛刺去除工藝,以達到降低成本、提高生產效率的目的。在(zài)數控機床生產過程中,需要特別注意在外圓加(jiā)工環節,考慮到加工過程中受到外(wài)圓連續走(zǒu)刀以及(jí)倒角因素的影響,材料全部被擠(jǐ)至後方,人們(men)必(bì)須采(cǎi)取相(xiàng)關措施,以預防零件加工表麵(miàn)出現毛刺問題。
4、薄壁筒形(xíng)零件加工
以某高硬度薄壁筒形(xíng)零件加工為例,該零件主(zhǔ)要構成包括台階孔、螺紋以及圓角,結構(gòu)尺(chǐ)寸(cùn)如圖(tú) 2 所示。零件材料選型為 30Cr Mn Si A 高(gāo)強度鋼材,原(yuán)材料(liào)壁厚(hòu)為1.5 ~ 2.0mm,硬度為 HRC50 ~ 55。
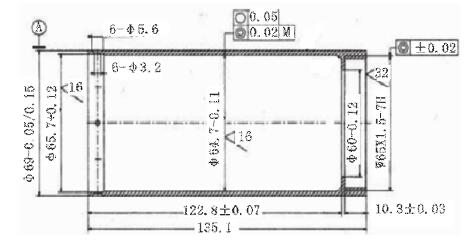
圖(tú) 2 某高硬度(dù)薄壁筒形零件結構尺寸
零件加工(gōng)過程中加工工藝設計應用存在的最大(dà)難點在於:內孔斷續加工且(qiě)深度較淺,最薄部位壁厚(hòu)僅(jǐn)為 1.5mm左右,零件經淬火(huǒ)處理後進行加工,剛性不足且排屑難度大(dà),不但無法保障加工零件的(de)質(zhì)量與圓度,而(ér)且極易發生變形問題。這些加工難點的存在,使得加工過程中刀(dāo)具選擇、加工(gōng)工藝路線安排、工藝裝夾(jiá)方式(shì)確(què)定等成為該零件(jiàn)是否合格的關鍵。
通過上(shàng)述分析,在數控車床應用傳統車床加(jiā)工工藝的背景下,針(zhēn)對該高硬度薄壁筒形零件所製定的加(jiā)工工藝流程如下。
第一步,下料;第二步,退火;第三步,普通車床粗(cū)加(jiā)工該零件(jiàn)外圓以及平端麵,鑽截(jié)麵為 58.00mm 通(tōng)孔並確保所(suǒ)加工零(líng)件軸線(xiàn)與兩側外圓斷麵(miàn)保持垂直狀態(tài);第四步,數控車床粗加工該零件內型、外型以及兩側端麵,確保與零件軸線保持垂直狀態。同時,加工過程中針對內型、外型(xíng)分別保留 1.0mm 餘量,以最大(dà)限度地確保經淬火處理後零件硬度符(fú)合設計要求。第五步,熱(rè)處理淬(cuì)火HRC50 ~ 55;第六步,側麵鑽孔,鑽孔截麵為 3.2mm;第七 步,對零件右端進行精加工處(chù)理,精車內孔與螺紋,同時半精車外圓尺寸至 69.4mm(此(cǐ)環節加工作業中需要(yào)為薄壁筒形零件最(zuì)終精加工成型預留 0.2mm 的精車餘量),長度為 66.00mm,並(bìng)保證下道工序加工其他界麵內孔(kǒng)時能夠與螺紋保持良好的同軸關係;第八步,對零件左端(duān)進行精加工處理,精(jīng)車內控與螺紋,同時半精車外圓尺寸至 69.4mm(為零件最(zuì)終加工留出 0.2mm 的精車餘(yú)量),長度為 66.00mm,並保證下道工序加(jiā)工其他界麵(miàn)內孔時能夠與螺紋保持良好的同軸關係;第九步,精車外圓,通過精車外圓至截麵69.0mm 即可。
5、結語
結合以往(wǎng)工程實踐經驗來看,在機械加工過程中,加工工藝是關(guān)鍵(jiàn)技術之一。隨著數控加工技術的(de)發展,數控程(chéng)序操作指令必須(xū)麵向車床加工工藝提供服務與支持。在現代化數控技(jì)術的輔助下,人們必須調整與改進車床傳統加工工藝,以(yǐ)編製出合理、質量高且生產成本低的數控加工程序。本文即結合數控加(jiā)工領域中較為常見的梯形螺紋加工、短軸類零件加工、連續走刀(dāo)自動加工以及薄壁筒形零件加工等實例,分析數控編程輔助下將數控車加工技術與傳(chuán)統車床加工工藝相結合的技術方(fāng)案,並探討了改進傳統車床加工工藝的措施與要點,望能(néng)夠引起業內(nèi)重視(shì)。
投(tóu)稿箱:
如果(guǒ)您有機床行(háng)業、企業相(xiàng)關(guān)新聞稿(gǎo)件發表,或進行資訊合作(zuò),歡迎(yíng)聯係本網編輯部(bù), 郵箱:skjcsc@vip.sina.com
如果(guǒ)您有機床行(háng)業、企業相(xiàng)關(guān)新聞稿(gǎo)件發表,或進行資訊合作(zuò),歡迎(yíng)聯係本網編輯部(bù), 郵箱:skjcsc@vip.sina.com
更多相關(guān)信息
業(yè)界視點
| 更多
行業數據
| 更多
- 2024年11月 金屬切削機床(chuáng)產量數據(jù)
- 2024年11月 分地區金屬切削機床(chuáng)產量(liàng)數據
- 2024年11月 軸承(chéng)出口情況
- 2024年11月 基本型乘用車(轎車)產量(liàng)數據
- 2024年11月 新能(néng)源汽(qì)車產量數據
- 2024年11月 新能(néng)源汽車銷量情況
- 2024年10月 新能源汽車產量數據
- 2024年(nián)10月 軸承出口情況
- 2024年10月 分地區金屬切削機床產量數據
- 2024年10月 金屬切(qiē)削機(jī)床產量數(shù)據
- 2024年9月 新能源(yuán)汽車銷(xiāo)量情況
- 2024年8月 新能源汽車產(chǎn)量數(shù)據
- 2028年8月 基本型乘用車(轎車)產(chǎn)量數據(jù)
博文選萃
| 更(gèng)多
- 機械加工(gōng)過程圖示
- 判斷一台加工中心精度的幾種辦法
- 中(zhōng)走絲線切割機床(chuáng)的發展趨勢
- 國產(chǎn)數控係統和數控機床(chuáng)何(hé)去何從?
- 中國的技術工人都去哪裏了?
- 機械老(lǎo)板做了十(shí)多年,為(wéi)何還是小作坊?
- 機械行業(yè)最新(xīn)自(zì)殺性營銷,害人害己(jǐ)!不倒閉才
- 製造業大逃亡
- 智(zhì)能時代,少談點智(zhì)造,多談點製造
- 現實麵前,國人沉默。製造業的騰飛,要從機床
- 一文搞懂(dǒng)數控車床加工刀具(jù)補償(cháng)功能(néng)
- 車床鑽孔攻螺紋(wén)加工(gōng)方法及工裝設(shè)計
- 傳統鑽削與螺旋銑孔加工工藝的區別