高中壓開關櫃(guì)斷路器深孔觸臂冷擠壓工藝研究
2019-11-21 來源(yuán):福建省(shěng)三星電氣股份有限公司 作者:黃(huáng)順家 王培農(nóng) 王新(xīn)武 王漢欽
高、中壓開關櫃斷路器觸臂是斷路器的核心(xīn)零件(jiàn),經查閱現階段國內外該產品的生產工藝主要為采用 T2 紫銅棒料或管料通過數(shù)控車床加工而成,其缺點為原材料成本高(gāo)、產品(pǐn)的機械性能及物(wù)理性能受原材料本身狀態影響較大、毛料重量大、生產勞動強度(dù)高、消耗很大的自然及社會資源等。冷擠壓工藝是將金屬毛(máo)坯放(fàng)在冷擠壓模(mó)腔中,在室溫下,通過壓力機上固定的凸模向毛坯施加壓力,使金屬毛坯產生塑性變形(xíng)而製得零(líng)件的加(jiā)工方(fāng)法,是一種先進的近終成型工藝。冷擠壓工藝可提高材料利用(yòng)率(lǜ),減(jiǎn)少產品生(shēng)產(chǎn)周期,降低產品生產成本;可使金屬(shǔ)材料(liào)內部呈規則方向流動,提高(gāo)產(chǎn)品的硬度、抗(kàng)拉強度、電導率等機械及物理性能,從而大大提高產品的使用壽命及安全性(xìng)能。本文綜合(hé)多種學科(kē),應用先進的模塊化設計方法,對采(cǎi)用(yòng)冷擠壓工藝生產該類電力設備核心部件進行了研究。
1、零件(jiàn)工(gōng)藝分析
1.1 工藝(yì)分析
圖1所示為高(gāo)中壓開關櫃斷路(lù)器觸臂設計圖,材質為T2紫銅。
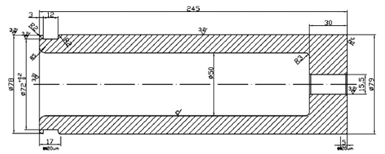
圖1 原高中壓開關櫃斷(duàn)路器觸臂設計圖(tú)
原有生產工藝是通過數控車床領用棒料 ϕ 80×250mm(11.18kg)進行加工,單件加工工時需要1.10h,特別是采用鑽鏜加(jiā)工內孔需要(yào)花費 0.6h 以(yǐ)上的工時,員工需要花費很大的體力進行鑽孔及搬(bān)運。日(rì)產能8~10件,生產投入成本和生產效率不理想。
采用冷擠壓工藝分析如下:
1)擠壓方案確認:該零件屬於套筒類產品,故采用反擠壓方案進行擠壓。
2)材料確定:冷(lěng)擠壓生產時如果材料硬度越高,那麽擠壓過程中需要的擠(jǐ)壓力也會更高。依據擠壓(yā)力選定(dìng)原(yuán)則:減少擠壓變形量,提高擠壓效率,降低衝頭的(de)擠壓衝擊力及原材料選擇優化,材(cái)料選擇用 T2 的 R 狀態,而產品外形尺(chǐ)寸為 ϕ 79mm,為(wéi)了 減 少 材 料 的 流 動 量 及 加 工(gōng) 量 ,原 材 料 采 用ϕ 80mm規格(gé)。
3)產品毛坯擠壓填充在凹凸模具之(zhī)間,內(nèi)腔與外圓會存在同心度(dù)偏差。由於機加工原(yuán)則為優先加工外部再加(jiā)工內部,采(cǎi)用冷擠壓時內孔的(de)粗糙(cāo)度可以達到Ra3.2以內(nèi),所以內孔可直接擠(jǐ)壓成形,外圓留加工餘量(liàng)。內腔(qiāng)直接擠壓成形,可減少鑽、鏜削內孔的工時 0.6h 和原材料重量 ϕ 50×215mm 約3.76kg。
4)該零件內孔深度與內孔直徑的尺寸比例為215/50=4.3,已趨(qū)於深(shēn)孔。擠壓過程中材料的流動量大。衝頭承受的力高,易(yì)產生偏移彎曲折斷,故需要針對衝頭進行(háng)詳細的設計。
生產工藝分析如下(高中(zhōng)壓開關櫃斷路器觸臂冷擠壓毛坯如(rú)圖2所示):
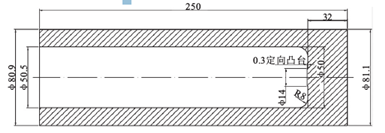
圖2 高中壓開關櫃斷路器(qì)觸臂冷擠(jǐ)壓毛坯圖
1)毛坯成形後的首道機加工基準(zhǔn)為內孔 ϕ 50mm及底麵,加工端麵(miàn)至30mm厚度,並鑽 ϕ 15.5mm孔,兩端倒角(jiǎo)1×45°。尾座頂 ϕ 15.5孔(kǒng)mm,車削外圓至ϕ 79mm,調(diào)頭,軟爪夾緊 ϕ 79mm校(xiào)正,以 ϕ 15.5mm底 部 端 麵 為 基 準 ,車 削 端 麵 定 總 長 及 切 槽 和倒(dǎo)角。
2)表麵處理電鍍。
綜上分析,該零件加工工序流程:軟態拉製 T2紫銅棒料—圓盤鋸床下料—潤滑—冷擠壓—車削ϕ 15.5mm 孔底部及外圓 ϕ 79mm—調頭車削定總長及車槽倒角—表麵處理電鍍。
1.2 工藝計算
1.2.1 毛坯重量計算
根據圖2計算出毛坯質量為7.689kg。
1.2.2 毛坯尺寸計算
選定外徑為 80mm 的 T2 紫銅棒料為毛坯料外圓,根據毛坯質量推算出毛料長度L=172mm。確定擠(jǐ)壓坯料尺寸(cùn)為 ϕ 80×172mm。
1.2.3 斷麵收縮率計算
斷麵收縮率 εF=(F0-F1)÷F0×100% (1)
F0—變形前毛坯的橫斷麵積(jī),mm2;
F1—變形後(hòu)毛(máo)坯的橫斷麵積,mm2。
由上可得F0=40×40×3.14=5024mm2
F1=40.5 × 40.5 × 3.14- 25 × 25 × 3.14=5150.39-1962.5=3187.89 mm2
所以斷麵收縮率(lǜ) εF=(5024-3187.89)÷5024×100%=36.55%
1.2.4 擠壓次數確認
當斷麵收縮率 εF≤ εF許時,隻用一次擠壓就(jiù)可以成形;當斷(duàn)麵(miàn)收縮率 εF≥ εF許,需要進行多次擠壓。
表1 常用(yòng)材料的許(xǔ)用變形量εεF許對照表
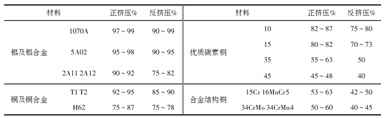
查表 1 可得在正擠壓情況下(xià)銅及銅合金的許用(yòng)變(biàn)形量 εF許為 92%~95%,確定該零(líng)件隻需一次就可以擠壓成形。
1.2.5 擠壓力(lì)計算及(jí)設備選擇(zé)
P=cp F (2)
P—擠壓力,KN;
p—平均單位擠壓力,Mpa,可在圖3中(zhōng)查出;
F—凸模與毛坯直接(jiē)接觸表麵在水平(píng)麵上的投影麵積,mm2;
c—安全係數,因材質的軟硬波(bō)動、潤滑處理的質量(liàng)、表麵粗糙度等意外因素、需要額外增加,一般取c≥ 1.3。
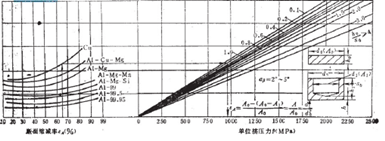
圖3 有色(sè)金屬(shǔ)反擠壓時單位(wèi)擠壓力圖算表
由式(2)可得,P=1.3×25×25×3.14×620MPa=1581.8k N
根據上文計算出(chū)的 P 值,選擇擠壓力 1600k N以上的四柱液壓機設備。
2 模具設計
2.1 模具結(jié)構(gòu)及設計特點
模具結構如圖 4 所示。由於觸臂類零(líng)件(jiàn)都是類似(sì),長短不一,故采用通用模架,隻需更換凸模(mó) 8和凹模3就可以(yǐ)重複使用。隨(suí)時更換,既降低了(le)成本,又擴大了使用範圍。增加卸料板及根據零件特點針對凸模進行細節設計。
4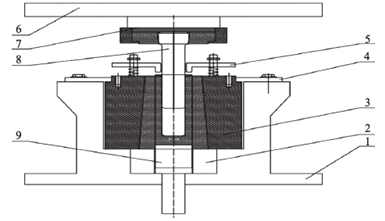
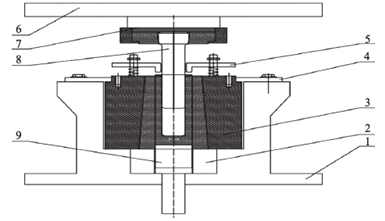
圖4 深孔觸臂冷擠壓模具圖
1.通用模架;2.墊塊(kuài);3.凹模;4.凹模壓(yā)板;5.卸(xiè)料板;6.上模板;7.衝(chōng)頭夾套;8.衝頭
2.2 凸凹模具受力分析
凸模單位最(zuì)大受力p凸=P÷F凸(3)
P—總擠壓力,N;
F凸—衝頭(tóu)水平投影受力麵積,Mpa/mm。由式(3)可(kě)得,凸模單位最大受力:p凸=1581775÷1962.5=807Mpa
凹模單位最大受力p凹=P÷F凹(4)
P—總擠壓力(lì),N;F凹—凹模水平投影受力麵積,Mpa/mm。
由式(4)可得,凹模單位最大受力:p凹=1581775÷5024=315Mpa
2.3 凸(tū)模設計分析
從上可得凸模在擠壓過程中承(chéng)受的(de)力比凹模大,凸模長度與工(gōng)作(zuò)直徑比值為 215÷50=4.3,凸模(mó)細長,在擠壓過程中易產生縱(zòng)向彎曲(qǔ)和偏移,為了防止及減少失穩的(de)情況,減少衝頭的受力。對(duì)衝頭(tóu)進行設計如下:
2.3.1 衝(chōng)頭表麵粗糙度拋光(guāng)至 Rz1.6,減少擠壓摩擦力。
2.3.2 原圖紙設計內孔底部為90度R3mm角,不利於擠壓過程(chéng)中(zhōng)原材料的(de)流動,造成擠壓壓力增加,所以必須變更底部(bù)根角的設計 R 角。觸(chù)臂是采用M14 的螺栓連接鎖緊,其 M14 墊片最大外(wài)徑為27mm,底部根角最大可以達到 R10mm。本設計為(wéi)R8mm。
2.3.3 衝頭底麵設計為圓錐麵角度為0.3°,增加擠壓過程中材(cái)料的流動性,減少受力。
2.3.4 因零件正(zhèng)中心後續加工需要鑽 ϕ 15.5mm的通孔,為了(le)保證衝(chōng)頭的穩定性,不會產生縱向偏移導(dǎo)致彎曲折斷,在衝頭正中心增加深度為(wéi) 0.3mm,直徑為 ϕ 14mm 的定位凹槽,使衝頭在擠壓過程中不會(huì)偏移導致彎曲折斷;
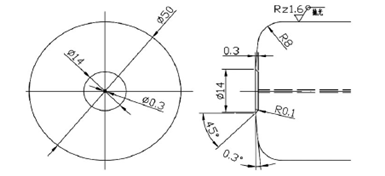
圖5 凸模設計細節圖
2.3.5 在擠壓完成後,衝(chōng)頭與零件脫模過程中,中間空腔會產(chǎn)生(shēng)真空,需要在衝頭鑽 ϕ 0.3mm 的小孔,使衝頭在脫模過程中不會因真空吸力導致零件吸附在衝頭(tóu)上而無法脫模。
凸模設計(jì)細節如圖5所示。
2.4 凹模設計分析
2.4.1 凹模采用組合式有如下優點(diǎn)
1)減少切向拉應力,有效的(de)防止內層凹模的縱向開裂,提高凹模的強度,延長模具壽命。
2)減少凹模材料的使用量,降低(dī)材料成本及熱處理成本。
2.4.2 零件臂厚14.5mm,零件在(zài)擠壓過(guò)程(chéng)中(zhōng)需要衝頭脫模動作。為了增加脫模效果,需要內凹(āo)模內(nèi)腔製作成為內倒錐設計,倒(dǎo)錐錐長控製在0.3mm以內。
3、實驗與(yǔ)分析
3.1 通(tōng)過以上工藝及模(mó)具優化(huà)後實現(xiàn)了觸(chù)臂批(pī)量(liàng)生產。如圖 6 所示(shì)為冷擠壓生產的深孔觸臂毛坯實物圖(tú)。
3.2 金屬流線更加密實,流線擠壓過程不會被切斷,增加(jiā)了零件的機械(xiè)強度。金屬流線圖對照詳見圖7。
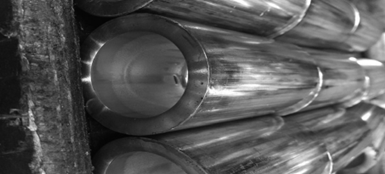
圖6 冷擠壓生產的深孔觸臂(bì)毛坯
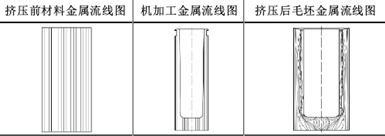
圖7 金屬流線圖對(duì)照
3.3 提高了產品的硬度,並使零件的材料基體(tǐ)更(gèng)加密實,晶粒組織更為均(jun1)勻、細化。棒料與冷擠(jǐ)壓(yā)性能對照詳見(jiàn)表2,經濟性能指標詳見表3。
表2 棒料與冷擠壓性(xìng)能(néng)對照(zhào)表

表3 經濟性能指標

4、結論
4.1 采用冷擠壓工藝生產(chǎn)該零件(jiàn)具有(yǒu)提高生產(chǎn)效率、提高原材料(liào)利用(yòng)率、降低原材料使(shǐ)用成本、零件的(de)硬度(dù)得到(dào)顯著提高和金屬流線更加(jiā)合理從而提高(gāo)產品使用壽命等優點。
4.2 詳實的工藝模具分析、計算充分考慮(lǜ)冷擠壓過程中產生的問題並列出相應解決方(fāng)案,最終有效的生產出合格的毛坯。
4.3 突破性的提出平麵斜錐、端(duān)角增加圓角、增加真空導(dǎo)氣孔等(děng)工藝和設(shè)計,有效(xiào)地減少了擠壓過程中材料流(liú)動性原因產生的擠壓力和脫模時產生的真空吸附力,提高了衝頭的生(shēng)產壽命。
投稿箱:
如果您有機床行業、企業相關新聞稿件(jiàn)發表,或進行資訊合作,歡迎聯係本網編輯部, 郵(yóu)箱:skjcsc@vip.sina.com
如果您有機床行業、企業相關新聞稿件(jiàn)發表,或進行資訊合作,歡迎聯係本網編輯部, 郵(yóu)箱:skjcsc@vip.sina.com
更多相關信息
業界視點
| 更多
行業數據
| 更多
- 2024年(nián)11月 金屬切削機床產量(liàng)數據
- 2024年11月 分地區金屬切削機(jī)床產(chǎn)量數據
- 2024年11月 軸承出口情況(kuàng)
- 2024年11月(yuè) 基本型乘用車(轎車)產(chǎn)量數(shù)據
- 2024年11月 新能源汽車產量數據
- 2024年11月 新(xīn)能源汽車銷量情(qíng)況
- 2024年10月 新能源汽車產量數據(jù)
- 2024年10月 軸承出口情況
- 2024年10月 分地區金(jīn)屬切削機床產量數據
- 2024年10月 金屬切削機床(chuáng)產量數據
- 2024年9月 新能源汽車銷量情況
- 2024年8月 新能(néng)源汽車產量數據
- 2028年8月 基(jī)本型乘用車(轎車)產量數據