電加工技術在航天零件加工中的應用
2015-3-10 來源(yuán):數控機床市場網 作者:北京控製工程(chéng)研究所 馮豪
在航天產品零件加工中有許多難加工材(cái)料,如鈦合金、高溫耐熱材料、不鏽鋼和硬質合金等,這些材料用傳統的金屬切削(xuē)機床加工(gōng),不僅效率低而且刀具費用昂貴,加工成本極高,有的材料甚至根本無法加工。還有許多零(líng)件形狀複雜,如窄縫、窄槽、空間位置複雜刀(dāo)具(jù)無法完成的加(jiā)工部位,以及微小(xiǎo)孔等采用傳統的機械加工(gōng)方法無能為(wéi)力。以上這(zhè)些成為航天零件加工(gōng)中的“瓶頸”。
電加工技術(shù)不僅實現了硬、脆、韌、粘等難加工材料的加(jiā)工,而且實(shí)現了高效低成本的加工。
目前, 我所(suǒ)的電加工技術(shù)主要應用在(zài)過濾器中液濾片、殼體、分流板,閥體中導向簧片、彈簧,微小孔以及異形孔(kǒng)零件(jiàn)的加工。電加工技術隨著現代製造業的發展(zhǎn),加工精度和效率不(bú)斷提高,航天產品中許多高精度、結構複(fù)雜(zá)的零件采用傳統的金屬(shǔ)切削加工效(xiào)率低、合格率低,很難適應航天任務的需求,但是,如果通(tōng)過改進(jìn)加工工藝流程,采用電加工技術很多問題就(jiù)迎刃而解(jiě)了。下麵就通過幾個典型案例(lì)來探討電加工技術在提(tí)高零件精度、表麵質量以及(jí)加工效率等方麵的優點。
1. 案例一:采(cǎi)用線切割技術解(jiě)決細長孔加工難題
如圖(tú)1所示的零(líng)件,材料為:
1Cr18Ni9Ti,外徑10.5 mm,內孔(kǒng)直徑newmaker.com,總長23.5 mm。根據設計要求,內(nèi)孔直徑newmaker.com尺寸公差必須滿足圖樣要(yào)求。因此內孔直徑newmaker.com成為該零件加工的難點。
難點一:材料為難加工(gōng)材料。
1Cr18Ni9Ti為奧氏體不鏽鋼,韌性大、熱強(qiáng)度高、導熱係數低、加工(gōng)過程中硬化(huà)嚴重(chóng)和散熱困難等諸多因素,導致(zhì)刀尖處切削(xuē)溫度高、極易產生積屑瘤,既加劇了刀具的磨(mó)損,又影響了(le)零件(jiàn)表麵粗糙度。
難點二:孔小、尺寸精度高。
內孔直徑newmaker.com直接采(cǎi)用(yòng)鑽削方(fāng)式根本(běn)無法達到圖樣尺寸精度(dù)要求,采用車削鏜孔方式,由於孔的深徑比大於5,鏜刀直徑必須小於4mm,強度(dù)低且刀尖磨損嚴重,同樣無法確保尺寸精度(dù)和表麵粗糙度。該孔一直采用(yòng)車削加工,先用φ 3.8 mm的鑽頭鑽孔,然(rán)後用鉸刀鉸孔,每次鉸孔前均需要用新(xīn)鉸(jiǎo)刀(dāo)試鉸,再手工磨製鉸刀摸索切削(xuē)參數(shù)。如此加工效率極低,每件加工耗時2 h左右,而且內孔加工容(róng)易(yì)出(chū)現錐度,合格率僅為30%左右(yòu),長期以(yǐ)來隻能通過多投產來保數量。
為了確保零件加工滿足圖樣設(shè)計要求,經過多次試驗,將零件按照圖樣要求車外圓φ 10.5 mm和長度23.5 mm到尺寸,並確保尺寸一致性在0.02 mm內,內孔用φ2 mm鑽頭打通作為(wéi)線切割的穿絲孔。然後,用夾具夾外圓找正(zhèng),采用(yòng)慢走絲線切割加工內孔。試驗結果表明,采(cǎi)用慢走絲線切割的方法很好(hǎo)地保證了(le)零件的加工尺(chǐ)寸精度以及尺寸的一致性。經過(guò)計量內孔直徑為(wéi)4.009 mm,內孔表麵粗糙度值為0.825 mm,內孔直徑一(yī)致性(xìng)能控(kòng)製在0.002 mm內。線切割時間為每件30 min,加工周期能縮短50%,合格(gé)率卻能達到98%以上。因(yīn)此,采用慢走絲加工既能保證內孔直徑尺寸公差滿足圖樣要求,提高零件加工(gōng)合(hé)格率(lǜ),又能提高零件加工效率。
2. 案(àn)例二(èr):電火花成(chéng)形解決零件走線槽(cáo)毛刺問題
如圖(tú)2所示零件是由兩種不同材料焊接而成,其中中間兩(liǎng)段有1.5 mm×3 mm和1.5 mm×3.5 mm的走線槽,φ 1.5 mm通孔走線孔,走線孔和走線槽的加工隻能在分段單件粗加工之後進行,由於零件(jiàn)精車過程中毛刺翻到(dào)走線槽和孔內,長期以來走線槽和孔毛刺的去除都是由(yóu)鉗工手工用什錦(jǐn)銼刀倒角完成,由於(yú)中間兩段之間的(de)距離隻有5 mm(見圖(tú)2),施展銼刀空間狹(xiá)小,導(dǎo)致在修銼去毛刺過程中把(bǎ)零件(jiàn)劃傷(見圖(tú)3、圖(tú)4)。
以看出手(shǒu)工修銼走線槽和孔存在(zài)以下幾方麵的缺點:①修銼過程中零件表麵質量不易控製,很容易造成零(líng)件表麵劃傷。②手工修銼(cuò)去毛刺效率低下。③手工修銼走線槽倒角一致性不能保證。④手工去毛刺後容易引起二(èr)次毛刺。
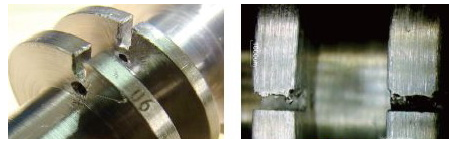
針對零件的結構特點以及加工特點,提出采用電火花成形的加工方(fāng)法去除零件1.5 mm×3 mm和1.5 mm×3.5 mm走線槽以及φ 1.5 mm走線孔邊沿的毛刺。根據(jù)圖5設計(jì)加工如圖6所示成形電極。
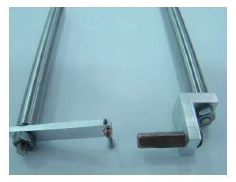
通過工藝試驗表明:針對零件1.5 mm×3 mm和1.5 mm×3.5 mm的(de)走線槽以及φ 1.5 mm走線孔邊沿的毛刺,采用電火(huǒ)花成形的加工方法進行加工去除具有如下幾方麵(miàn)的優點:①零件去毛刺過(guò)程可控,且不會造成零件表麵劃傷。②大大減輕了勞動(dòng)強度。③操作過程可控、省時高效,加工效率(lǜ)能(néng)提高50%以(yǐ)上。④能保證倒(dǎo)角加工的(de)一致性,適合零件的批量化生產。采用電(diàn)火花成形加工效(xiào)果良好,其加工後效果如圖7、圖8所示。
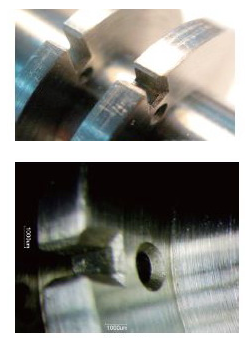
如圖9所示零件是太陽敏(mǐn)感器中(zhōng)承(chéng)載光(guāng)學頭部(bù)的(de)高精度重要零件, 2個梯形型通孔(kǒng)中間有一個50 mm×41 mm的(de)矩形窗口。通(tōng)過數銑其他所有形麵均能(néng)達到設計圖樣要求,唯(wéi)獨中間50 mm×41 mm的矩形窗口隻用T型刀能加工成(chéng)如圖10所示的形狀。

按照工(gōng)藝流(liú)程要求單獨有一道工序在普(pǔ)通銑床上用特製(zhì)的T型刀加工矩形(xíng)窗口上下“殘留”的尖角。如果采(cǎi)用普銑的加工方法(fǎ),直接用T型刀仍無(wú)法加工,必須將特製的T型刀的刀柄先從梯形腔內穿過底部的接插件窗口(見圖11),再將(jiāng)刀柄裝到機床的(de)主軸上。在加工的時候還必須確保T型(xíng)刀(dāo)的側刃不能碰到側麵,加工(gōng)1件就需要換裝刀具至少2次。因此,加工效率不僅低,而且還很難保證圖樣尺寸要求。
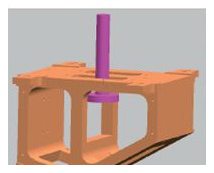
為了滿足設計圖樣要求,決定采用電(diàn)火花成形技術加工(gōng)矩(jǔ)形(xíng)窗口, 設計如圖1 2 所示尺寸為:材料為紫銅的電火花成形電(diàn)極。
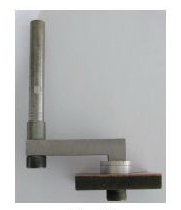
通過試驗表(biǎo)明,改用電火花成(chéng)形加工方法完全可行且具有如下幾方麵優點:①找正方便、加工(gōng)效(xiào)率(lǜ)高。隻(zhī)需找正首件,基本不用重(chóng)複找正,適(shì)於小批量生產。②加工成本低。采用的紫銅電極(jí)成本比合金(jīn)刀具成本相比廉價,電極(jí)損耗小可重複使(shǐ)用。③尺寸一致性有保證(zhèng),能提高零件合格率。減少零件加工對操作者技能水平(píng)的依賴,找正工件,隻要參數設置合(hé)理,正確操(cāo)作就能確保零件合(hé)格。
4. 結語
通過上述典型(xíng)案例分析表明,隨著電加工技術的快速發展,許多采用傳統金(jīn)屬切削加工(gōng)很難解決的問題,采用現代電(diàn)加工技術能“迎刃而解”。實踐說明電加工不但能(néng)提(tí)高零件的加工合格率、表麵質量,而且還能提高加工效率,降低成本。因此,要(yào)不(bú)斷創新、開拓思路,利用電加工技術優勢(shì)結合先進的金屬切削技術來製定高效、優質(zhì)的加工方案,提高零件的加工精度和合格率,才能確保航天產品的高可靠性。
投稿箱:
如果您有(yǒu)機(jī)床行業、企業相關(guān)新聞(wén)稿件發表,或進行資訊(xùn)合作,歡迎聯係本網編輯部, 郵箱:skjcsc@vip.sina.com
如果您有(yǒu)機(jī)床行業、企業相關(guān)新聞(wén)稿件發表,或進行資訊(xùn)合作,歡迎聯係本網編輯部, 郵箱:skjcsc@vip.sina.com
更多相關信息
業界視點
| 更多
行業數(shù)據
| 更多
- 2024年11月 金屬切削機床產量數據
- 2024年11月 分(fèn)地區金屬切(qiē)削機床產(chǎn)量數據
- 2024年(nián)11月 軸承(chéng)出口情況
- 2024年11月 基本型(xíng)乘用車(轎車)產量數據
- 2024年11月 新能源汽車產量數據
- 2024年(nián)11月 新能源汽車銷量情況
- 2024年10月 新能源汽車產量數(shù)據
- 2024年10月 軸承出口情況
- 2024年(nián)10月 分地區金屬切削機床產量數據
- 2024年10月(yuè) 金屬切(qiē)削機床產量數據
- 2024年9月 新能源汽車銷量情況
- 2024年8月 新能源汽車產(chǎn)量數據
- 2028年8月 基本型乘用車(轎車)產量數據
博(bó)文選萃
| 更多