航空發動機製造裝(zhuāng)備驗收現狀與關鍵(jiàn)技術
2020-5-11 來源: 中國機(jī)床工具工業協會(huì)cmtba 作者:原創 於建華 等
接上文“航空發動機零組件加工特點(diǎn)與裝備分析”及2020年5月7日“航空發(fā)動機製造裝備的性能需(xū)求"(可點開鏈接閱讀)。因原文較(jiào)長,為便於閱讀,經與作者商議,將其拆分成相對獨立的3篇文章陸續發布,但保留原文圖片及(jí)參考(kǎo)文獻的編號。若想一氣嗬成看全文(wén),請關(guān)注《世界製造技術與裝備市場(WMEM)》雜誌2020年第3期(qī)“航空發動機加工裝備的性能需求與驗收關鍵技(jì)術(shù)”一文。
——編者注
1 、驗收流程
設備選型:這個階段是(shì)設備廠商了(le)解用戶(hù)需求的重要階段,是保證設備滿(mǎn)足後期使用要(yào)求(qiú)的前(qián)提。機床企業(yè)的設(shè)計代表和(hé)航空用戶的工藝代表應進(jìn)行多輪(lún)次的技(jì)術交流,將設備的功(gōng)能、性能、配置、數控係統、精度、使用便捷性、可靠(kào)性等逐項落實(shí)。如果是重要設備,要專門設計樣件進行試切加工,對功能和性能可行性進行驗證,最終形成指導設備選型(xíng)的《技術規(guī)格書》。對於新研製設備,探索機床企業與航空用戶企業(yè)關鍵技(jì)術人員交(jiāo)叉任職、較長時期交流辦公等深度融合的工作機製(zhì),有利於(yú)推(tuī)動高端機床與航空發(fā)動機製造的匹配發展。
招標投標:由設備廠商的銷售代表(biǎo)和航空用戶的(de)商務代表依據《技術規格書》和招投標法規完成。
技術協議:對設備的用途、功能、結構形式、主要技術(shù)指標、安裝要求、關鍵部(bù)件配置、驗收執行標準、供貨(huò)範圍及其他特殊要求做出約定,形成《技術協議》。
合同簽訂:由(yóu)設備廠商的銷售代表和航空用戶的商務代表依據《技術協(xié)議》和合同法規完(wán)成(chéng)。
設備(bèi)預驗收:這是至關重要的環節(jiē),尤其對於有特殊要求的設備,應該將特殊(shū)的性能要求充分進行加(jiā)工驗(yàn)證,如有必要甚至可以創新性地設計新的驗收標準。預驗收主要檢查、驗證所購(gòu)置的機床能否滿足自身產品的(de)加工質量(liàng)及(jí)生產效率要求,提供(gòng)的資料(liào)、備附件等是否齊全,具體內容根據《技術協議》中的要求。需要注意(yì)的是:機床通過正常運行試加(jiā)工並經(jīng)整體檢(jiǎn)驗合格後,購置(zhì)方才能進行預驗收工作,預(yù)驗收通過後可(kě)以向用戶廠家發運機床。
設備終(zhōng)驗收:主要包括到貨後開箱驗收、安裝過程驗收、安裝後總(zǒng)體驗(yàn)收。對於分體運輸的大型設(shè)備,在(zài)用戶場地對經過長途運輸後的各(gè)部件安裝組合精度進行(háng)恢複(fù)調試更有利於機床的精度保證和運輸隱(yǐn)患排查。機床驗收時的所(suǒ)有驗收記錄都應有簽字確(què)認,並交由用戶設備主管部門保管存檔。
2 、驗收內容
航空發動機數控機床與裝備的驗(yàn)收是指利用高精度儀(yí)器對機(jī)床本身(shēn)的(de)機械、電路、液壓和氣動裝置等各係統進行綜(zōng)合(hé)使用性能、單項使用性能和靜態及動態精度檢測的過程,最後給出本(běn)機床性能的綜合(hé)評(píng)估。驗收的項目主要有以下五部分內容。
(1)機床外觀功能檢測
主機及(jí)各零部件有無磕碰損傷、鏽蝕(shí)等現象;各係統(tǒng)的(de)動作試驗、空載(zǎi)/負荷運轉試(shì)驗。
(2)機床幾何精(jīng)度檢測
各運動軸相對工作台移動的直線度(dù)、平行度、垂直度(dù)、平麵度、跳動等,對於機床的幾何精度和(hé)定位精度(dù)檢測(cè)要打開後台補償,查閱機床精度補(bǔ)償量(liàng),對於補償較大的應要求進行硬件調整或更換。
(3)機床位置(zhì)精度檢測
機床各驅動軸在數控係統控製下的定位精度、重複定位(wèi)精度、反(fǎn)向差(chà)值、原點的(de)複位精度、位置偏差及定位(wèi)係統偏(piān)差等。一般推薦采用VDI/ DGQ 3441,GB/T17421.2,ISO 230 –2等標準。
(4)機床工作精度檢(jiǎn)測(cè)
對於車削機床、四軸以下機床的工作精度檢(jiǎn)測一(yī)般推薦NAS試件,如果切削難加工材料或者有其它(tā)特殊要求,可(kě)適當增加未來需加工的典(diǎn)型特征試件;對於五軸機床除了NAS試件外,應針對性(xìng)設計可(kě)檢測外圓與內孔同(tóng)軸(zhóu)度、圓度、傾斜角度、鑽/鏜孔(kǒng)精度及各尺寸精度等的試件;對於(yú)航空發動機難加工材料(liào)所用機床,主軸的扭矩、功率、轉速要符合加工工況的(de)扭矩/功率/轉速曲線圖,不能以單個指標去衡量切削性能;尤其對於工作剛度和動態性能會有針對性的驗收措施。
(5)機床綜合性能檢測
機床軟件程序導入導出(chū)及後處理匹配性(xìng);機床負載一定周期下的可靠(kào)性與精度保持性;裝夾找正、上下料(liào)、維護保養操作便捷性。
3 、存在問題與關鍵技術
新出廠的數控機床與裝備在檢驗時僅把機(jī)床(chuáng)本身(shēn)的(de)幾何與位置精度、加工精度(dù)作為考(kǎo)核測試的標(biāo)準是遠遠不夠的,必須對機床綜合精度和動態響應特性(xìng)、連續運轉時間、係統穩定性及機床溫升等各項(xiàng)指標做(zuò)出全麵的檢測。隻有這樣做才能夠保證高速切削數控機床今後加工性(xìng)能的穩定度(dù)[15]。美國航(háng)空航天局(jú)於1969年發布了NAS 979標準,這也是此(cǐ)前唯一被行業公認的試件標準。然而大量的實(shí)踐表明,NAS五坐標錐台檢測試件加工時始終處於開角加(jiā)工區域,不能準確反映機(jī)床的綜合精度。傳統精度檢測儀器如激光幹涉儀、雙球杆儀、激光跟蹤儀(yí)等對多軸(zhóu)聯動誤差和動態誤差檢驗的局限性逐步顯現。近年來S型(xíng)試件、RTCP檢驗方法逐漸得以推廣和應用,有效彌補了五軸機床加工航空難加工材料時工作性能檢測的短板。此外,航空發動機(jī)企業(yè)對於專用或者複雜的機床裝(zhuāng)備還要設計專門樣件(jiàn),進行樣件加工,它是對機床從設計(jì)到製造再(zài)到安(ān)裝調試的質量和性能的總體檢驗,直接關係到機床裝備的功能、加工(gōng)精度和綜合加工能力的可靠性。
(1)S型試件檢測
NAS試件主要對機床的幾(jǐ)何精度敏感,而對動態精度不敏感,按照此標準驗收的五軸機床在加工飛機(jī)結構零件複雜曲麵時,大量出現過切、欠切、表麵嚴重波紋等情況。為此(cǐ),由中國主(zhǔ)持(chí)修訂、由中航工業成都飛機工業(集團(tuán))有限責任公司基於航空製造經驗及多年自主深入研(yán)究成果提出的,ISO10791-7: 2020《加工中心檢驗條件第7部分:精加工(gōng)試件精度檢驗》國際標準,獲國際標準化組織(ISO)批準正式發布,成為國際(jì)標準 [16]。如圖(tú)20所示,試件由S形走向的扭曲曲(qǔ)麵形成(chéng)的等厚度緣(yuán)條和矩形底座組成。S型(xíng)緣條由上(shàng)下兩個(gè)平麵上的四條S形曲線相互交叉構成。由於緣條與底平麵(miàn)的夾角連續變化,在連續加工S型曲麵緣條兩側時,可檢查五軸數控機床連續變軸加工零件表麵時的粗糙度、厚度(dù)、輪(lún)廓誤差等,檢驗機床開、閉角轉換時的(de)性能,更好地反映多軸加工中各(gè)運動部(bù)件的綜合精度(dù)和動態響應特性,更能體現航空薄壁件的機床加工性能。在(zài)圖20中,直紋麵A由兩(liǎng)條準均勻三次B樣條曲線定義,這兩條B樣條曲線分別由兩組控製點即Mi(i=0-11)和Ni(i=0-11)定義。與直紋(wén)麵A相似,直紋(wén)麵B也由兩條準均勻三次B樣條曲線進行定義,兩條樣條線(xiàn)分別由兩(liǎng)組控製(zhì)點Pi(i=0-11)和Qi(i=0-11)定義[17]。
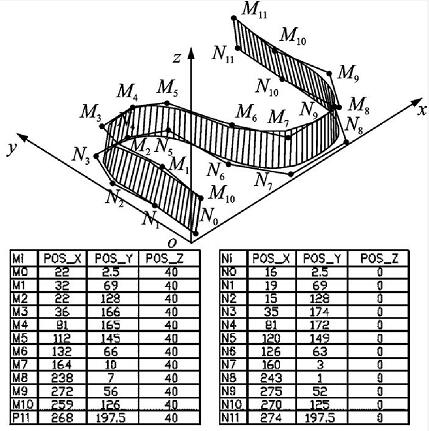
圖20 S型試件(jiàn)(直紋麵A和B)
(2)RTCP精度檢驗
隨著用(yòng)於檢測刀具中心點空間位置誤(wù)差的R-test測量儀的研究成熟(shú),可通過三個位移傳感器測量球(qiú)頭(tóu)空間(jiān)位(wèi)置配合機床刀尖跟隨功能(Rotation Tool Centre Point,RTCP),快速檢測多軸(zhóu)聯動時的刀具中心點空間運動誤差(chà)。R-test測量裝置的性(xìng)能主要取決於測量範圍和測量敏感度,應該選擇較大測量半徑和較高測(cè)量(liàng)敏感度的測量儀[18]。目前,ISO10971-6國際標準(zhǔn)中針對雙擺頭五軸機床的RTCP檢測用AK4軌跡,操作簡(jiǎn)單,無(wú)須編寫檢測數控(kòng)代碼,但無法反映出航空發動機零件曲麵突變加工時所需的機床動態性能,在RTCP 檢測軌跡的規劃過程中(zhōng),應采用更加複雜(zá)的函數或通過選取點(diǎn)位進行樣條擬(nǐ)合(hé)的方式生成檢測軌跡(如S型軌跡),以提升檢測性能[19]。
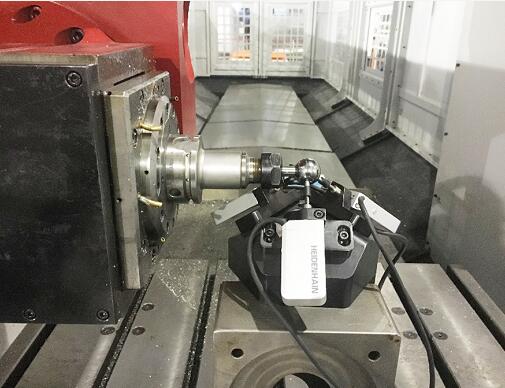
圖21 RTCP精度檢測
(3)樣(yàng)件設計與檢測
航空發動機零(líng)件對於機床的剛度、特殊工位行(háng)程可達性、難加工材料切削性(xìng)、使(shǐ)用便捷性等有苛刻要求。設計與真實零件特(tè)征相似的樣件,觀察樣(yàng)件加(jiā)工過程後置處理、刀具路徑規劃、路徑光順、誤差檢測與補(bǔ)償、原位測(cè)量與自適應補償的各功能的運行狀況[20],檢測加工樣件的精度可以有效(xiào)評價機床的(de)使用性能。
綜上,對(duì)於航空發動機零件加工的關鍵設備,用傳(chuán)統檢測儀器進行幾何精度和位(wèi)置精(jīng)度檢測;對於多軸機床要進行S形試件加工和RTCP精度檢查(chá);對於精加工或難加工材料切削機床要設計專門樣(yàng)件進行工作(zuò)精(jīng)度檢查(chá)。
4 、驗收(shōu)項目與流程
重要的機床與設備采購要經過以下九大環節才能完成驗收(見圖22),機床設計人員(yuán)應該在設備選型伊始就充分參與進來,並與機床使用的工藝人員充分交流,摸透用戶需求;在機床(chuáng)使用工藝人員要選擇合適的(de)驗(yàn)收標準,對機床(chuáng)所(suǒ)需的性能進(jìn)行充分檢驗。
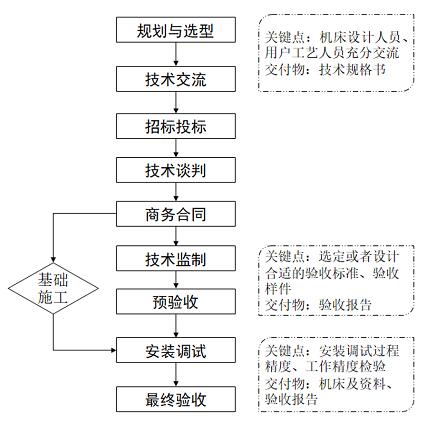
圖22 驗(yàn)收流程邏輯圖
結論
綜上所述,本文根據(jù)航空發動機零件結構的複雜特點和加工中的特(tè)殊(shū)要求,對(duì)所需的關鍵短板裝備性能特點(diǎn)進行分析(xī)。通過總結航空發動機的設備選型、性能提升改造(zào)、驗(yàn)收與使用經驗,得到以下結論:
(1)對於航空發動機(jī)所需的關鍵與瓶頸裝備,應充分發揮“用、產、學、研”機(jī)製,由用戶牽頭,設(shè)備企業(yè)、高校和研究(jiū)機構參與,研製之初(chū)就吃透工藝需求,共同攻關,新開發(fā)的機床(chuáng)應經過大量機床測(cè)試,通過幾輪迭代創造出符合先進航空發動機工藝需求的新(xīn)裝備。
(2)航空發動機研製生產準(zhǔn)備周期長,需(xū)要的工藝裝備品種多,要求高。而且發動(dòng)機還需要不斷更新(xīn)換代,具有(yǒu)典型的多品種小(xiǎo)批量特征,尤其是特種加工設(shè)備,批(pī)量(liàng)不大。對於這些(xiē)難度高、投資大、批量小的工藝裝備需(xū)要(yào)國家項目大力支持。
(3)機床設計應重(chóng)點(diǎn)關注結構(gòu)功能一體化、多種(zhǒng)工藝(yì)複合機床(chuáng)的(de)研製,關注本文提出的(de)共性技術性能(néng)提升。同時,機床設計者和機床使(shǐ)用者應該大膽創新,敢於提出新標準,與行業協會和各級標準化組織共同推動建立高端機床中國標準。
(4)對於粉末冶金難加工材料高效切削、複合材料切削加工、複(fù)雜(zá)型麵(如渦輪盤榫槽等(děng))電加工(gōng)和磨削加工(gōng)、激光打孔(單晶葉片氣膜孔)、增材製造(zào)等設備和驗(yàn)收標準,還有待進一步開發和研究。
投稿箱:
如果您有機床行業、企業相關新聞稿件(jiàn)發表,或進(jìn)行資訊合作,歡迎聯係本網編輯部, 郵箱:skjcsc@vip.sina.com
如果您有機床行業、企業相關新聞稿件(jiàn)發表,或進(jìn)行資訊合作,歡迎聯係本網編輯部, 郵箱:skjcsc@vip.sina.com
更多相關信息
業界視點
| 更多
行業數據
| 更多
- 2024年11月 金屬切削機(jī)床(chuáng)產量數據
- 2024年11月 分地區金屬切削機床產量數據
- 2024年11月 軸(zhóu)承出口情況
- 2024年11月 基本型乘(chéng)用(yòng)車(chē)(轎車)產量數據
- 2024年11月 新能源汽車產量數據
- 2024年11月 新能源汽車銷量情況
- 2024年10月 新能源(yuán)汽車產量數據
- 2024年10月 軸承出口情況
- 2024年10月 分地區金屬切削機(jī)床產量數據
- 2024年10月(yuè) 金屬切削機床(chuáng)產量數據
- 2024年9月 新能源汽車銷量情(qíng)況
- 2024年(nián)8月 新能源汽車產量數據
- 2028年8月 基本型(xíng)乘用(yòng)車(轎車)產量(liàng)數據