hyperMILL:把“神棍”拉下神壇——整體式KN95熔(róng)接齒模的編程(chéng)與優化
2020-6-15 來源(yuán):-- 作者:-
摘要:熔接齒(chǐ)模是(shì)各類全自動和半自動口罩機的核心零部件,一度被譽名為“神(shén)輥”。本文基於OPEN MIND公司hyperMILL軟件的加工功(gōng)能,針對整體(tǐ)式(shì)KN95口罩熔接齒因結構複雜而導致數(shù)控編程和加工難度大的特點,實(shí)現數控加工編程及加工工藝(yì)優化的(de)過程。本文(wén)通過軟件中五軸形狀(zhuàng)偏置和五軸輪廓加工指令,為解決熔接齒模在(zài)加工過程中加工空間狹窄,切削刀具(jù)小,刀具壽命短,其(qí)他軟件(jiàn)程(chéng)序抬刀、跳刀(dāo)、空刀過多導致加工效率低下的問(wèn)題(tí)提(tí)供(gòng)了一(yī)些解決方法與實用技術。結果表明hyperMILL軟件可以簡化編程的過程,提高編程和加工的效(xiào)率,充分發揮多軸數控加工的技術(shù)優勢,幫(bāng)助數控加工企業充分(fèn)利用現有設備,快速應對市場變化,並為(wéi)其它同類複雜零件的編程加工提供(gòng)了重要依據。
口罩熔接齒模是各類(lèi)全自動和半自動口罩機的核心零部件。該模具的加工質量對於口罩(zhào)在加工成型的生產過程中有著非常大(dà)的影響,稍有(yǒu)偏(piān)差口罩便麵臨著切不斷,邊緣有毛邊甚至出現刀口崩裂的狀況。該模具也因結構特(tè)殊,加(jiā)工精度要求高,數控編程複雜和加工難度大(dà)等特點一度(dù)也譽名為“神輥”。如何(hé)快速(sù)準(zhǔn)確的實現數控加工編程和加工工藝優化,提高加工精度(dù)及加工效率成(chéng)為該產品加(jiā)工的關鍵(jiàn)。
hyperMILL是德國OPEN MIND 公司的一款CAM軟件,其軟件中的五軸形狀偏置和五軸輪廓加工指令,為熔接齒模在加工過程中因加工(gōng)空間(jiān)狹窄,切削刀具小(xiǎo),刀(dāo)具壽命(mìng)短,其他軟件程序抬刀、跳刀、空刀過多導致加工(gōng)效率(lǜ)低下的問題提供了(le)一(yī)些解決方法與(yǔ)實用技術。
整體式KN95熔接齒模(mó)模型
熔接齒模是打片機上最為(wéi)主(zhǔ)要部件之一,用於熔(róng)切無(wú)紡布。熔(róng)接齒模最為主要的(de)位置由壓花齒、切刀口和送料齒三部分組成,其中壓花齒與切刀口保證口(kǒu)罩的壓印與切斷,兩側送料齒保證無紡布的(de)輸送。工(gōng)作時熔接齒模呈軸向旋轉運動,通過超(chāo)聲波超聲振動原理對多層(céng)無紡布(bù)進行熱(rè)熔與切削。本文所研究的熔接(jiē)齒模是整體式KN95口罩熔接齒模,如圖1所示。
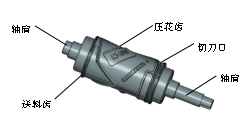
圖1 整體式KN95熔接齒模及其主要結構(gòu)
整體式KN95熔接齒模的外形尺寸如圖2所示。該模型為一出一熔切一體式熔接齒模,模具總長285mm,最大外徑(jìng)Φ79,切刀口角度為60°,壓花齒與送料齒數分(fèn)別為380、120個,間距為1mm。
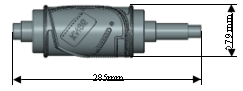
圖2 整體式KN95熔接齒模外形尺(chǐ)寸圖
整體式KN95口罩熔接齒模結構(gòu)複(fù)雜,加工難度大,其數控編程和加工的難點主要有以下幾點:
(1)壓花齒與送料齒間距(jù)小,加工效率低、易斷刀;
(2)切刀口處要求寬度(dù)均勻,一般控製在0.1mm~0.3mm, 並保證刃肩光順,因(yīn)與壓花齒距離較近,隻能選用(yòng)小刀進行粗、精加工,效率低下,加工效果不佳;
(3)壓花、送料齒(chǐ)與切刀口存在(zài)一定量(liàng)落差,落差若不同軸(zhóu)則造成口罩壓花印高低,將直接對模具使用產生影響。
KN95熔接(jiē)齒模數控編程
hyperMILL是集成化NC編程的CAD/CAM軟件[1],其多軸(zhóu)模塊為熔(róng)接齒模(mó)提供了高效可靠的編程與加工方案。與其它加工軟件相比編程效率高,自帶的加工仿真模塊可檢(jiǎn)驗程序的(de)正確性。
2.1 刀具與加工參數選擇
選擇合(hé)適(shì)的刀具和刀具(jù)類型不僅可以保證加工效率,而且能夠(gòu)滿足(zú)零件的(de)加工質量。刀具的(de)選擇需要充分考慮工件的形狀、材料、加工效率和精度等各個方麵的因(yīn)素[2]。KN95熔接齒模加工刀(dāo)具的(de)選取可遵(zūn)循以下原則(zé):
(1)粗加(jiā)工時,在條(tiáo)件允許的情(qíng)況下應選擇直徑較大的平底銑刀,以提(tí)升加工效率;
(2)熔接齒間間距較小(xiǎo),但(dàn)加工(gōng)深度較淺,應選擇直徑較小(xiǎo)的立銑刀或角度刀;
(3)切(qiē)刀口是整個(gè)模型的(de)關鍵點之(zhī)一,且切刀口要求較高,可選擇較小的R角刀或者帶角度的(de)成型銑刀。
根據整體式KN95口罩熔接齒模的尺寸、材(cái)料等,選擇立銑(xǐ)刀、成型刀(dāo)分別完成各個加工工序。所選刀具的參數如表1所示。
表1 加工中選(xuǎn)用刀具(jù)的參數
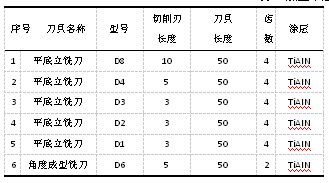
2.2整體式KN95熔接齒(chǐ)模加工工序及加工參數確(què)定
根據所用毛坯的形狀以(yǐ)及整體式KN95熔接齒(chǐ)模的(de)結構特(tè)點,將其加工(gōng)工序分為整體粗(cū)加工、清角加工、底麵精加工、送料齒精加工、壓花齒精加(jiā)工、切刀(dāo)口精加工。各加工工序所用刀具以及加工(gōng)參數如(rú)表(biǎo)2所示。
表2 各加(jiā)工工序使用(yòng)的刀具以及參數
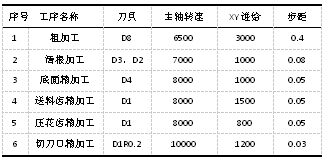
2.3數(shù)控編程
2.3.1 粗加工
粗(cū)銑加工完成了熔接齒模主要加工餘量的去除和後(hòu)續加工餘量的均勻(yún)化。因此,要求粗(cū)加工(gōng)具有較高的加工(gōng)效率,在保證不發生幹涉且盡可能多的前提下盡可能選擇直徑大的(de)銑刀,以保證加工效率[1]。在hyperMILL軟件(jiàn)上建立圓柱(zhù)驅動麵並法向與驅動麵進行加(jiā)工。最大橫向步距設置2mm,垂直步距0.4mm。底麵與側麵餘量均為0.15mm。生(shēng)成(chéng)刀具路徑如圖3所示。
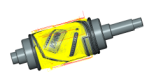
圖3 整體粗(cū)加工刀具路徑
2.3.2 清角與二次清角
整體式KN95熔接齒(chǐ)模輪廓島嶼眾多,較為複雜,粗加工後因刀(dāo)具直徑原因(yīn)無法保證側麵(miàn)餘(yú)量均勻化,因此需(xū)清角。直接選用D2平底立銑刀進行整體清角時(shí)效率低下,為此采用D4、D2平底立銑刀進行清角與二次清角,保證零件側麵(miàn)餘量均勻。最大橫向步距設置1.2mm,垂直步距0.08mm,底麵與側麵(miàn)餘量均為(wéi)0.15mm。
在hyperMILL軟(ruǎn)件中使用“五(wǔ)軸形狀(zhuàng)偏置精加工”設置“清角模式”參考刀具為7.5、3.8,加工選項為“側壁”進行零件整體清角。兩(liǎng)次整體清角的刀具路徑(jìng)如圖4所示。
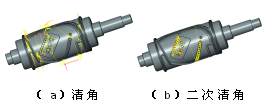
圖4整體清角加工刀具路徑
2.3.3 底麵精加工
整(zhěng)體式KN95熔(róng)接齒模(mó)齒底麵(miàn)加(jiā)工要求並不高,在整個模具的運行中屬於避空麵。但壓花、送料齒頂麵要求較高,在使用過程中(zhōng)與無(wú)紡(fǎng)布存在直接接觸,其與切(qiē)刀口頂麵存在落差,一(yī)般控製與0.15mm~0.2mm之間,若落差不均勻(yún),則直接影響這個模具的使用,為保證齒麵與切刀口的落差,在該工序運(yùn)行前需再次驗證模具在(zài)機床上(shàng)是否位於同軸。為保證加工質量(liàng),加工底麵時對零件側麵留有0.15餘量(liàng),行距不宜過大,可選擇D4的銑刀進行齒底、齒頂表麵精加工。齒底、齒頂表(biǎo)麵精加工刀具路徑如圖5所示
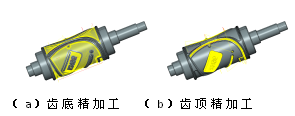
圖5齒頂與齒底加工刀具路(lù)徑
2.3.4 壓花齒、送料齒精加工
壓花齒呈環(huán)繞形纏繞於整體式KN95熔接齒模表麵,起(qǐ)到壓印的作用,數量較多。送料齒在整體式(shì)KN95熔接齒模上可壓花齒平齊或稍(shāo)高於壓花齒麵,為更好(hǎo)的保證送料齒(chǐ)的輸送作用(yòng),可與切刀口均采用外圓磨床磨削。
壓花齒、送料齒齒間(jiān)距較窄,數量較多,對側壁的表麵(miàn)要求不高,可選擇D1平底立銑刀采(cǎi)用“五軸形(xíng)狀偏置(zhì)粗加工”進行加工,該位置刀路拐角較多,采用刀具路徑倒圓角進行光順過渡。最大橫向步距設置0.4mm,垂直步距0.05mm,底麵與側麵餘量無。壓花、送(sòng)料齒(chǐ)精加工刀(dāo)具路徑如圖6所示。
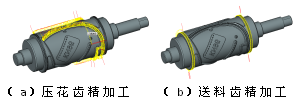
圖6送料齒精加工刀具路徑
2.3.5 切刀口精加工
切刀口是熔接齒模加工要求最高的部位(wèi),起到切斷(duàn)無紡布的(de)功能,加工(gōng)要求高,若無法保證切刀(dāo)口寬度,在使用時易發生毛邊、局部未切斷等情(qíng)況。可選擇D1R0.2 R角刀采用hyperMILL軟件中“五軸形狀(zhuàng)偏置精加工(gōng)”進行螺(luó)旋環繞(rào)式加工。因在熔接齒模的使用中(zhōng)對(duì)切刀口側壁表麵質量要求較(jiào)高,因此軸向進給(gěi)設置為0.03,以保證表麵(miàn)粗糙度。切刀口加工路徑如圖7所示
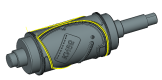
圖7切(qiē)刀口加工刀具路徑
2.3.6 加工仿(fǎng)真與後處理
利(lì)用hyperMILL的內部機床或模擬功能進行仿真模擬[3],整個過程未發現幹涉、漏切,仿真結果如圖(tú)8所示。使(shǐ)用加工中心的操作係統為牧野V33i立式四軸(zhóu)加工中心,刀具路(lù)徑經過後處理器處理生成.nc格式的NC文件。
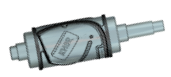
圖8 加工仿真效果
程序優化
3.1 壓花齒程序(xù)優(yōu)化
壓花齒數量眾多,一般在400個齒左右,使用“五軸形狀偏置精加工”效(xiào)率低(dī)下、刀具壽命(mìng)低(dī)下,且跳刀較多。優化(huà)後利用hyperCAD-S軟件進行軌跡輪廓線構建,再采(cǎi)用“五軸輪廓加(jiā)工”,以走輪廓線上的方式進(jìn)行程序編寫,生(shēng)成刀路軌跡有以下優(yōu)點:
(1)跳刀(dāo)少,基本無(wú)空刀;
(2)刀具壽命(mìng)長;
(3)加工效率提升三倍以上。
壓花齒優化前後刀具路徑(jìng)如圖9所示。

圖9壓花齒(chǐ)優化前後刀具路(lù)徑
3.2 送料齒程序優化
送料齒一(yī)般呈環繞形均(jun1)勻附著於熔接齒模(mó)表麵,起到輸送(sòng)布料的作用,其數量多、間距小,使用“五軸形(xíng)狀偏置粗加工”加工效率低,且刀具壽命短。優化後(hòu)采用“五軸輪廓加工”編寫一齒,使用轉換功能進行圓(yuán)形陣列並(bìng)連結工單。該加工(gōng)方案刀路整潔清晰,最大程度的簡化(huà)了刀具路徑。送料齒優化(huà)前後刀(dāo)具路徑如(rú)圖(tú)10所示。
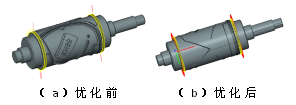
圖10送料齒優(yōu)化前後刀(dāo)具路徑
3.3 切刀口程序優化
在加工切刀口時,一般使用“五軸形狀偏置精加工”呈(chéng)環繞形加工, R角刀(dāo)分層切削效率低下,且表麵效果不佳。優化後采用“五(wǔ)軸輪廓加工(gōng)”使用(yòng)成型刀分(fèn)層加工,大大的提升(shēng)了加工效率與表麵質量。切刀口優化前後刀具(jù)路徑如圖11所示。
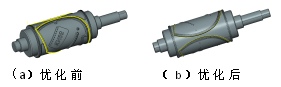
圖11切刀口優化前後刀具路徑
結論
整體式KN95熔接齒模對製造要(yào)求的水平較高,且(qiě)加工時間(jiān)加長,製造質量對熔接齒模的性能、使用壽命(mìng)及應用效果有著重(chóng)要的影響,因此要製造出一款優異的(de)產(chǎn)品,不僅要有良好的製造方法,還要有良好的工藝作保證。
參考文獻(References):
[1] 合(hé)肥工業(yè)大學 張文祥、韓江.基於hyperMILL的整體葉輪(lún)五軸數控加工[J].製造技術與機床,2012(6):125—128
[2] 山東大學 李曉君、劉戰強、沈琦、王(wáng)兵.基於加工特征的整體葉盤數控編(biān)程與加工參數優化.組合(hé)機床與自動化加(jiā)工技術,2019(3):153-156.
[3] 山(shān)東大學 趙文明,莊鵬,鞠崗崗(gǎng)等. 基於hyperMILL 的半開式整體葉輪五(wǔ)軸數控編程與加工技術(shù)[J]. 組合機床與自動化加工技術,2017( 1) : 70-73.
[4] 上海建橋學院 張雲玲. 基於hyperMILL 葉輪模具母輪(lún)加(jiā)工(gōng)方法的研究[J]. 組(zǔ)合機(jī)床與自動化加工(gōng)技術,2013( 5) : 34-35.
[5] 李亞寧.將hyperMILL用於(yú)人工關節的加工CAD/CAM與製造業(yè)信息化(huà),2009年(9):32-33
(來源:杭州蕭(xiāo)山技師學院;作者:沈梁、崔凱(kǎi)冬、尹耀、張慶明)
投稿箱:
如果您有機床(chuáng)行業、企業相(xiàng)關新聞(wén)稿(gǎo)件發表,或進行資訊合(hé)作,歡(huān)迎聯係本網編輯部, 郵箱:skjcsc@vip.sina.com
如果您有機床(chuáng)行業、企業相(xiàng)關新聞(wén)稿(gǎo)件發表,或進行資訊合(hé)作,歡(huān)迎聯係本網編輯部, 郵箱:skjcsc@vip.sina.com
更多相(xiàng)關(guān)信息
業界視點
| 更多
行業數據(jù)
| 更多
- 2024年11月(yuè) 金屬切削機床產量(liàng)數據
- 2024年11月(yuè) 分地區金屬切削機床產量數據
- 2024年(nián)11月 軸承(chéng)出口情況
- 2024年11月(yuè) 基本型乘用(yòng)車(轎車)產量數(shù)據
- 2024年(nián)11月 新能源汽車產量(liàng)數據
- 2024年11月 新能源汽車銷量情況
- 2024年10月(yuè) 新能源汽車產量數據
- 2024年10月 軸承出口(kǒu)情況
- 2024年10月(yuè) 分地區(qū)金(jīn)屬切削機床產(chǎn)量數據
- 2024年10月 金(jīn)屬切(qiē)削機床產量數據
- 2024年9月(yuè) 新能源汽車銷量情況(kuàng)
- 2024年8月 新能源汽車產量數據
- 2028年8月 基本型(xíng)乘用車(轎車)產量數據