軋輥磨床數控化改造與應(yīng)用
2023-11-27 來源: 江蘇省高淳中等專業學校 作者:張芬芬
摘要: 以某冷軋薄板廠軋輥磨(mó)床改造項目為例,對(duì)數控技(jì)術在(zài)軋輥磨床改造中的應用展開分(fèn)析。結果表(biǎo)明,對軋輥磨床數控係統改造後,輥(gǔn)形偏差縮小,磨削時間縮短,人機交互(hù)界(jiè)麵更(gèng)加友好,可以顯示圖形,磨床(chuáng)的整體性能得到提升。
關鍵詞: 數控技術; 軋輥磨床; 改造
數控技術在多個領域得到了廣泛的應用,其中軋輥磨床是(shì)製(zhì)造業不可或缺(quē)的重要設備,其磨削精(jīng)度(dù)與產品質量密(mì)切相(xiàng)關。為提高軋輥磨床的磨削(xuē)精度,需對(duì)數控係統進行改造升(shēng)級。某(mǒu)冷軋薄板廠興建於 20世紀 90 年代末,建廠時的(de)設計產量為 70 萬 t,共有 9條生產線,12 套機組,設備與技術基本上(shàng)都是從國外引進,能夠生產高檔的冷軋板、彩塗板等,其產品在汽車製造、石化油工、建築等行業中(zhōng)有著廣泛(fàn)應用。該廠磨輥車間采用的支撐輥磨床是從(cóng)美國引進的,主要負責酸洗冷軋聯合機組(zǔ)與平整機組的支(zhī)撐輥修磨任務。磨床在長時間服役中數控係統不斷老化,部(bù)分(fèn)功能喪失。而客戶對板麵的質量要求逐步提高,軋輥磨床的加工(gōng)精度對生產形成了一定的製約,亟需對軋輥磨床進行改造,以便更好地滿(mǎn)足生產需要。
1、改(gǎi)造(zào)原因及目標
1. 1 改造原因
近年來,軋鋼技術逐步完善,帶鋼質量逐步提升,為(wéi)生產出能夠(gòu)滿足不同客戶需求(qiú)的帶鋼產品,需(xū)提升軋輥修(xiū)磨技術,令軋(zhá)輥的輥型複雜程度更高,磨削精度更高,偏(piān)心度、錐度偏(piān)差更小,操作(zuò)更加方便,自動(dòng)化程度更高,磨削速度更快,以適應更多的軋輥材質,應用範圍更廣(guǎng)。該廠的支撐輥磨床數控係統由插件版計算機、德國西門子公司出(chū)品的 S5 係列 PLC 組成,計算機(jī)與(yǔ) PLC 之間以點對點方式傳輸信號[1]。受到計(jì)算機軟(ruǎn)、硬件方麵的限製,導致該磨床的自動化程度偏低(dī),使用過程(chéng)中(zhōng)經常出現(xiàn)問題(tí),具體表現在以下幾方麵:偏差大。磨削加(jiā)工後的軋輥輥形存在較大的偏差,影響了冷軋板質量。輥形偏差是(shì)指磨削加工的輥(gǔn)形與預先設定的輥形(xíng)之間(jiān)的差值。軋(zhá)輥作為軋(zhá)鋼生產中鋼板的變形工具,對精度要求較高,尤其是對平(píng)直度要求(qiú)較高,即 < 50μ。軋輥磨床存在的主要(yào)問題是磨(mó)削輥形偏差較大,約為 100μ,無(wú)法滿足冷軋(zhá)鋼板的板形精度要求,對冷軋板質量的提升產生了嚴重製約,無法滿足高精度、高質量產品的生產需要。
磨削效率低。磨床對軋輥中心校準的時間較長,數控程序中不具備補償功能,導致(zhì)磨削效率低,平均每根(gēn)軋輥的磨削用時約為 60 min 左右。由於效率過低(dī),導致磨削至規定精度所需的道次增多,軋(zhá)輥及砂輪的損耗隨之增大,致使輥耗降低。為供應質量合格、精度達標的軋輥(gǔn),需保(bǎo)證軋(zhá)輥的周轉量充足,這樣將導致生產成(chéng)本(běn)增加。若是能夠在現有條件(jiàn)基礎上(shàng)提高軋輥磨床的磨削效率(lǜ),則可使軋輥的周轉量隨之減少。
自(zì)動化程度(dù)偏低。從軋輥磨(mó)床的操作性能來看,係統采用的操作界麵較(jiào)差,無法(fǎ)顯示(shì)圖形,導(dǎo)致生產過程中無法隨時查看圓度、磨削偏差等情況[2]。磨削程序較落後,無法自由編程,不(bú)具備硬件(jiàn)擴展功能,無法實現(xiàn)聯網通信及集中控製,不利於磨輥間生產率的提升。
故障率偏高。由於磨床的控製及傳動係統結(jié)構較為複雜,致使設(shè)備故障率(lǜ)增加(jiā)。該軋輥磨床的傳動係統為直流係統,穩定性與可維護性較差,不但會對作業效率的提升產生影(yǐng)響,還會增加維護成本。直流電動(dòng)機的缺點是需要經常保養碳刷,如果維護不及時將可能引發故障。係統插件版采用分立元件,與 PLC 之間的通信方(fāng)式為點對點,PLC 與現場元件的通信方式也是點對點,需要敷設的電(diàn)纜(lǎn)數量較多(duō),故障率隨之增高,發生故障後查找及處理難度較大[3],因此(cǐ)對軋輥磨床的數控係(xì)統進行升級改造勢在必行。
1. 2 改造目標
結合軋鋼生產(chǎn)及磨輥需求,對軋輥磨床數控係(xì)統進行升級改造(zào),主要目標(biāo)如下:
係統改造後,使磨削加工的輥形偏差小於 10 μ,提高板形質量,為高品質(zhì)、高精度產品的批(pī)量生產提供保障。在(zài)數控係統軟(ruǎn)件程序中增加補償功能(néng),縮短磨削時(shí)間,提高磨削效率,使(shǐ)每根軋輥的磨削時間從原來(lái)的 60 min 縮減至 40 min 以內,以降低軋輥的周轉量[4]。引入友好型的人機操作界麵,增加圖形(xíng)顯示功能,采用模塊化思路設計磨(mó)削程序,為自由編程提供支撐(chēng)。進一步簡化控製與傳動係統的結構,避免發(fā)生故障,提高磨床運行穩定性。用(yòng)工業 PC 機替代 CNC 係統,數控係統(tǒng)與 PLC 的通信及 PLC 與現(xiàn)場元(yuán)件的通信全部改為程序總(zǒng)線網絡( Profibus) ,減少電纜敷設量。
2、改造內容
本次改造屬(shǔ)於整體(tǐ)項目範疇,數控係統的選擇是改造(zào)的重點內容,要求所選的數控(kòng)係(xì)統具(jù)備良好的控製性及(jí)通用性,在提升軋輥磨(mó)削精度及質量(liàng)的基礎上降低工作強度。
2. 1 改造方案
可用於軋輥磨床數控(kòng)係統改造的方案有以下幾種:
方案一: 工業 PC 機(jī) + CNC + PLC。該(gāi)方案的係統架構(gòu)如圖 1 所示。
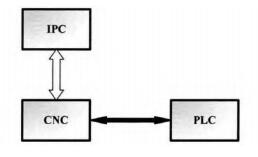
圖 1 工業 PC 機 + CNC + PLC 架構示意圖
該方案(àn) 中,數控係統的所有單元均獨立,通 過840D 將獨立 PC 機、CNC、PLC 等單(dān)元集中於一塊插件版上,各自獨立運行程序(xù)。其最突出的(de)特點是(shì) 840D的應用,係統具有較強的通用性,故障率(lǜ)相對較低,便於維修(xiū)[5]。
方案二: CNC + PLC,以(yǐ)工業 PC 機替代 CNC。該方案的係統架構如圖 2 所示。
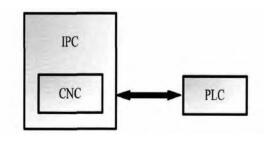
圖 2 CNC + PLC( 以工業 PC 機替代(dài) CNC) 架構示意圖
該方案中,CNC 被工業 PC 機取代(dài),PLC 得以保留,將 PC 機(jī)劃(huá)分為兩部分(fèn),即操作和控(kòng)製(zhì),前者主要(yào)負責(zé)對控製部分發出的指令信息進行接收與執行,後者可(kě)實現控製及圖形處理等功能。CNC 被工業 PC 機所取代,係(xì)統的硬件結構變得更加簡單,因 PC 機為工(gōng)業專用,故而(ér)該係統的通用性較差,但專業性(xìng)非常強,維修難度增大(dà)。
方案三: 工業 PC 機代替 CNC 與 PLC。該方案的架構如圖 3 所(suǒ)示
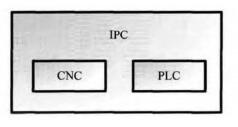
圖 3 工業 PC 機代替 CNC 與 PLC 的架構示意圖(tú)
該方案中,CNC、PLC 的(de)功能均在 PC 機上,以軟件控製方式實現,PC 機具有超強的邏輯運算能力,利用擴展的總線接口(kǒu),可與外部的驅動單(dān)元相連接。軟件型控製係統為實時操作係統,能夠對 CPU 資(zī)源(yuán)自主使用,借助 Windows 操(cāo)作係統,可完成畫麵顯(xiǎn)示、數據通信、邏(luó)輯(jí)掃描、控製任務等。該係統突出的特點是運算功能強大,現場總線技術的運用,豐富了控製(zhì)係統對外圍(wéi)輸入及輸出信號的監控。
從硬件結構、操作界麵、編程方式、磨削功能等方麵對上述 3 種改造方案進行比較,確定將方案一作為本次軋輥磨床數控係統改(gǎi)造的主(zhǔ)要方案,選用某機床廠提供的支撐輥磨床 MK84125,因為 840D 係統的通用性強,能(néng)夠使(shǐ)現場設備保持(chí)正常運轉,加(jiā)之係統價格較低,故將其作為首(shǒu)選。840D 數控(kòng)係統由德國西門子公司(sī)研發,功(gōng)能強大,包括(kuò)人機界麵、可編程控製器、數控內核、驅動控製等。係統(tǒng)各部分功能如圖 4 所示。
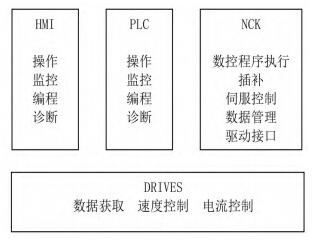
圖 4 係統各部分功能示意圖
2. 2 操作界麵(miàn)的開發
選好數控係統後,依托相關的(de)開發軟件,對(duì)操作界麵進行定義,通過操作界麵的開發,實現(xiàn)全麵自動化(huà)操作,以提升磨床的磨削效力及加工質量,輔助用戶以(yǐ)分層方(fāng)式管理機床。對軋輥磨床的加工工藝進行融合設計,包括工件中心自動校正、砂輪(lún)自動修整、磨削自(zì)動循(xún)環(huán)、輥形偏差自動測量與修整及補償,按照實(shí)際需求(qiú),對加工工序進行靈活組合(hé),實現不同軋輥及表麵質量的整合。操作界麵由(yóu) 6 個窗口組成,具體開發過程如下:手(shǒu)動調整。軋輥磨床在非磨削(xuē)加工狀態時,可運用手(shǒu)動調整窗口,以(yǐ)實現對磨床(chuáng)伺服軸、頭架主軸電機、砂輪主(zhǔ)軸電機、測量(liàng)臂等的手(shǒu)動(dòng)調整。
參數設(shè)置。該窗口的主要(yào)功(gōng)能(néng)是設置軋輥(gǔn)磨床的基本參數,由於參數對磨床的控製過程具有直接影響,故應正確、合理進行設置。大部分參數是在軋輥(gǔn)磨床調試期間完成(chéng)設置,少部分參數需在特定情況(kuàng)下按磨床(chuáng)運行特點修改設置[6]。在修改設置參數時,用戶應具備相應的權限,參(cān)數(shù)修(xiū)改完畢後予以(yǐ)保存,以替代之前的參數。
加工程序編輯。該窗(chuāng)口(kǒu)能夠編製軋輥磨床的加工程(chéng)序,將係統提供的加工工序整(zhěng)合後,輸入最佳(jiā)的磨削參數,使軋輥加(jiā)工實(shí)現最(zuì)優目標。
曲(qǔ)線參數。該窗口能夠(gòu)完成軋輥輥(gǔn)形曲線參數的錄入、修改、保存等操作。可編程的曲線類型包括平輻(fú)輥形、正弦輥輥形、錐度輥輥(gǔn)形、曲線輥形等。在(zài)默認的情況下,係統保存數十條輥形參數,用戶可對曲線進行修改,並新增所需的曲線(xiàn)。
磨削。該窗口能夠對軋輥磨床自動磨削加工過程進(jìn)行控製,係統裝載(zǎi)大量的程序,可提供多種控製方案,實現由簡到繁的自動磨削控製。
3、結(jié)束語
在軋輥磨床數控係統改造過程中,需合理應用先進的數控技術,根據生產需要選擇最為適宜的係統,達到改造目的,提高軋輥磨(mó)床的磨削精度,提升產品質量。未來一段時(shí)期,要加(jiā)大數控技術研究力度,逐步改進完善,研發新技術,使其更好(hǎo)地為工業生產服務。
投稿箱(xiāng):
如果您有機床行業、企業相關新聞稿件發(fā)表(biǎo),或(huò)進行(háng)資訊合作,歡迎聯係本網編輯部, 郵箱:skjcsc@vip.sina.com
如果您有機床行業、企業相關新聞稿件發(fā)表(biǎo),或(huò)進行(háng)資訊合作,歡迎聯係本網編輯部, 郵箱:skjcsc@vip.sina.com
更多相關信息
業界視點
| 更多
行業數據
| 更多
- 2024年11月 金屬切削機床產量(liàng)數據
- 2024年11月 分地區金屬(shǔ)切削機床產量數據
- 2024年11月 軸承出口情況
- 2024年(nián)11月 基本(běn)型乘用(yòng)車(轎車)產量數據
- 2024年11月 新能源汽車(chē)產量數據
- 2024年11月 新能源汽車銷量情況
- 2024年10月 新能源汽車產量(liàng)數據
- 2024年10月 軸承出口情況
- 2024年10月 分地區金屬切削機床產量數據
- 2024年10月 金屬(shǔ)切削機床產量數據
- 2024年9月 新能源汽(qì)車銷量情況
- 2024年8月 新能源(yuán)汽車產(chǎn)量數(shù)據
- 2028年8月 基本型乘用車(轎車)產量數據