數控機床驅動裝置可靠性技(jì)術研究
2019-6-28 來源: 大連(lián)機床(chuáng)集團 工藝裝備 大連(lián)金潤液(yè)壓 作者:饒彥平 尹闊 呂靜
摘(zhāi)要:數控機床驅動(dòng)裝置的穩定性決定了機床整機的可靠性。通(tōng)過分析驅動裝置關鍵零部件的結構(gòu)特點、加工及裝配過程的關鍵精度要求,提(tí)出了相關的精度保證方法以及評定過程,采用技術手(shǒu)段控製關(guān)鍵零件的加工方法,提高了零(líng)件(jiàn)的精度及穩定(dìng)性,並根據結構特點采用合適的裝配方法,從而提高了驅(qū)動裝置的可(kě)靠性(xìng)。該(gāi)方法(fǎ)可操作性強,有一定(dìng)的推廣價值。
關鍵詞:數控機床;驅動裝置;可靠性
目前,數控(kòng)機床在製(zhì)造業中所占(zhàn)的比重越來越大,數控機床在使用過程中的可靠性也越(yuè)來越受到重(chóng)視。在數(shù)控機床的可靠性中,定位精度及(jí)重複定位精度更是人們關注的焦點。機床(chuáng)的定(dìng)位精度與(yǔ)重複(fù)定位精度決定了(le)加工(gōng)零件的精(jīng)度,如數控車及數控磨加工外(wài)圓(yuán)的精度、加工中心加工零件的孔間位置誤差與加工模具時零件表麵質量等均與定位精度(dù)及重(chóng)複(fù)定位精度有關(guān)。定位精度與(yǔ)重複定位精度(dù)與驅動裝置有關。
1 驅動裝置分析(xī)
1.1 驅動(dòng)裝置結(jié)構
數控機床(chuáng)驅動裝置(見圖1)包括驅動電動機、電動機座、聯軸節、前軸承、絲杠螺母、螺母座、滾柱/滾珠絲杠、軸承座、後軸(zhóu)承和鎖緊螺(luó)母等。
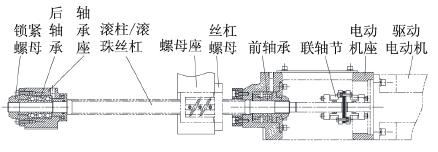
圖(tú)1 數控機床驅動裝置示例
1.2 安裝時關鍵精度
數控機床驅動裝置安裝(zhuāng)時應保證(zhèng)如下(xià)精(jīng)度要求:1)絲杠及螺母副本身的加工及(jí)裝配精度;2)安裝(zhuāng)前後(hòu)軸承外孔(電動機座及軸承座軸承孔)的加(jiā)工及裝配(pèi)時的同軸度誤(wù)差;3)螺(luó)母座與絲杠螺母接合麵的(de)平行度精度;4)電動機座中電動機安(ān)裝孔與軸承孔的同軸度精度;5)前軸承鎖緊螺母的鎖(suǒ)緊扭矩(jǔ)控製要求;6)後軸承鎖緊螺母預拉變形量控(kòng)製要求。
1.3 技術要求
驅動裝(zhuāng)置主要精度為電動機座、螺母座、軸承座(以下簡(jiǎn)稱三座)的製造精度,以及與(yǔ)之相配零件的裝配精度有關,其技術要求如下。
1)三座中的(de)基準孔一般是裝軸承或電動機止口安裝孔,其(qí)精度要(yào)求為(wéi)IT6~IT7,表麵粗糙度要求為Ra1.6μm。
2)零件上用於連接的裝配基麵將直接影響三座與其相連接零件安裝時的相對位置及加工中的定(dìng)位精度,因而要有較高的平(píng)麵度和表(biǎo)麵粗糙度。其平麵度要(yào)求為0.01~0.005 mm,表麵粗糙度要求為Ra0.8~Ra1.6μm。
3)與裝(zhuāng)配基麵平行或垂直的(de)基準孔中心線,其平行或 垂 直 在 全 長 範 圍 內 要 求 為 0.005~0.01mm。
4)當安裝基(jī)準(zhǔn)麵與基體連接有刮研要(yào)求(qiú)時,配合需精密吻合(hé)。
2 、加(jiā)工過程分析
由於三座中,電動機(jī)座的製造(zào) 精 度 起 作 用,因此,本文(wén)對電(diàn)動機座的加工過程進行分析。
2.1 電動機座加工(gōng)工(gōng)藝(yì)
電(diàn)動機座(見圖2)為數控機床Z 向驅動裝置中與伺(sì)服電動機相(xiàng)連的關鍵零件,其總體尺寸不大,從其功能上(shàng)看,一方麵(miàn)滿足與電動機的連接及與床體的(de)連接;另一方麵(miàn)通(tōng)過軸承支(zhī)承絲杠和聯軸節等零件,故要求有(yǒu)較高的支(zhī)承(chéng)剛度,因此一般將其做成不規則(zé)的腔型結構(見(jiàn)圖(tú)2)。
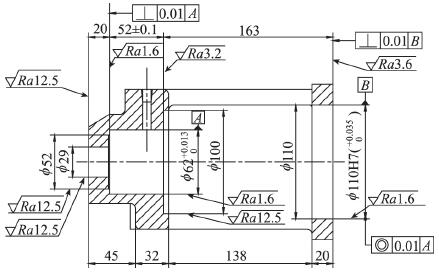
圖2 電動機座尺寸圖
為(wéi)了(le)提高電動機座的強度和(hé)剛度,一般采用力學性能較好(hǎo)的珠(zhū)光體灰口鐵HT250或 HT300鑄造而成。
2.2 電動機(jī)座技術要求
電動機座的技(jì)術要求見表1。
表1 電動機座的技術要求
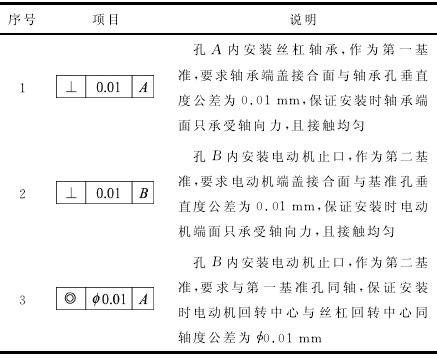
2.3 機械加工(gōng)工藝過程
電動機座(zuò)按成批生產時的加(jiā)工工藝過程如下。
1)10序:以安裝麵定位加工工藝粗基準麵。
2)20序:粗半精(jīng)加工安裝麵及(jí)工藝孔。
3)30序:以20序安裝麵及工藝孔定位粗半精加工各麵(miàn)、孔。
4)40序:精(jīng)加工安裝麵。
5)50序:以精加工後安裝麵及工(gōng)藝孔定位精加工(gōng)各麵、孔。
2.4 工藝分(fèn)析
2.4.1 精度要求
要求孔係與安裝接合麵平行度為0.01mm(比較嚴格),距離公差為(wéi)±0.05mm,電動機安裝麵與孔(kǒng)係垂直度為0.01mm,電動(dòng)機安裝孔與軸承安(ān)裝(zhuāng)孔同軸度為0.01mm。從各項幾何公差(chà)來看,此工件(jiàn)為高精度工(gōng)件。
2.4.2 材料(liào)特性(xìng)、加工(gōng)方案及工藝措施
工件材料為灰口鑄鐵 HT250或 HT300,材質比較軟,裝夾力量過大則容易變形,為保證工件各(gè)項精度,對於單件生產需要對安裝接合麵進行(háng)刮研,保證平麵度0.01 mm,在 坐 標 鏜 床 上(shàng) 對(duì) 孔 係 進 行 精鏜,保證孔係與安裝接合麵的(de)平行度及電動機安裝孔與軸承安裝孔的同軸度。但是(shì)對於目前機床的批(pī)量生產,電動機座需要大批量加工製造,每天(tiān)的產量在60件以(yǐ)上,仍然使用傳統工藝對工件進行加工製造,需要增加坐標鏜床的數量,生產成本過大。
為了完成(chéng)每天60件的生產任務,在保證工件加工精度的(de)前提下,筆(bǐ)者對工件的加工工藝進行(háng)了調整,使用立式加工中心(VDL1000)對安裝接合麵進行粗銑留(liú)量,同時加工兩沉孔(按 H7加工成品)以一麵兩銷的定位形式對孔(kǒng)係及工(gōng)件其他部分進行粗加工,使用立式加工中心(MDV55 帶 光 柵 尺(chǐ))對安裝接合麵進行精加工,同時(shí)加工兩定位銷孔(按 H7加工)孔距±0.01mm,再以(yǐ)一麵兩銷的定位形式對(duì)孔係進行精加工(gōng)。如此方法,隻需在原有設備基礎上新增2、台立式加工中心(MDV55)設計製作4套液(yè)壓夾具,實行一人多機,即可降低每年數十萬元的生產成本。
2.5 質量評(píng)定
試製(zhì)的樣件經過三坐標檢測,安裝接合(hé)麵平(píng)麵度為0.01mm,電動機安裝麵與孔係垂直度(dù)在 200mm 長度上為0.01mm,距離公差為±0.02mm,電(diàn)動機安裝孔與軸承安裝孔同軸度為0.008mm。實踐證(zhèng)明,新的工藝方法能夠滿足圖樣設計要求。
3 、裝配過程分析
3.1 主要裝配零件
該驅動裝置是由滾珠絲(sī)杠副、前端電動機座組件、後端軸承座組件、聯軸器及伺服電動機組成(chéng)的,這種結構有著很(hěn)高的傳動精度、定位精度和重複定位精度。由於經過精密的加工、裝配,加(jiā)上絲(sī)杠的傳動效率(lǜ)高,所以它有(yǒu)較好的高速特(tè)性。滾珠絲杠副由絲杠與螺母兩大部分組成,工作時(shí)借助鋼球在絲杠(gàng)與(yǔ)螺(luó)母之間做點接觸的滾動,從而實現絲杠或螺母的(de)位移。
近年來,滾珠絲杠副作為數控機床直線驅動執行單(dān)元,在機床行業(yè)得到了廣泛的應(yīng)用。滾珠絲杠副具有極高的傳動效率,可達90%以上,為傳統滑動絲杠的 3 倍,並可實現可逆性傳動,使運動部件的(de)發熱量大幅降低。滾珠絲杠副經過精密(mì)磨削、精密裝配和嚴格檢(jiǎn)驗,因此,有很(hěn)高的傳動精度。由於絲(sī)杠(gàng)、螺母和鋼球之間均為點接觸,且本身經過硬化處理及多次定性(xìng)處理,所(suǒ)以(yǐ)其磨損、變形極小,因而大(dà)大提高了其使用壽命。
電動機座組件是絲(sī)杠的主要支承單元,絲杠的前端支承在一對角接觸軸(zhóu)承上,兩軸承背靠背安裝,能承受徑向(xiàng)負荷和2個方向的(de)軸(zhóu)向負荷,在有力矩作用(yòng)時剛(gāng)度很高(gāo),但同時這種結構對軸承孔的幾何公差要(yào)求較高;預緊力是(shì)決定角接觸軸承性能的重要因(yīn)素,預緊力越(yuè)大,徑 向剛 度和軸向剛度都會提高,但同時(shí)溫升也會加大,因此在安裝過程中應采用合適的力矩控製軸承的預(yù)緊力,防止預緊力過大或(huò)過(guò)小(xiǎo)。
聯軸器(qì)能在一定程度上補償連接件的軸向、角向和徑向偏差(chà),同時不會造成磨損和(hé)提前失(shī)效,最大程度地避免(miǎn)了伺服電動機振動、發熱等因(yīn)素對(duì)絲(sī)杠的影響。在安裝過程中,連接軸的(de)對中性越好,它的使用壽命和傳遞效果就越好,因此,應最大程度地保證聯軸器的安裝精度。為確保數控機床進給係統的傳動精度(dù)、靈敏度(dù)和工作穩定性,在裝配過程中應使用合理的工具、工裝和(hé)檢具,才能保證裝配精(jīng)度,獲得合格的產品。
3.2 裝配要求
驅動裝置裝配要求如下。
1)絲杠組件(jiàn)自身的精(jīng)度。滾珠絲杠副作為關鍵的滾動原件,對(duì)機構的性能舉足輕重,其精度的高低直接影響(xiǎng)了(le)整個(gè)機構的工作效果,因而應根據實際的工作要求(定位精度、傳動速(sù)度和扭矩等情況(kuàng))選擇合適的絲杠組件。
2)絲(sī)杠中心線(xiàn)與導軌平行度。由於絲杠(gàng)是精(jīng)密部件,電動機座、軸承座的同心度以及軸線對床身導軌(guǐ)的平行(háng)度直接決定了絲杠安裝後的綜合精度,在整機試車(chē)過程中的定位精度、重複定位精度和反向偏(piān)差等都與絲杠安裝質量的好(hǎo)壞有著直接(jiē)的關係;因此,在安裝(zhuāng)絲杠前(qián),應先(xiān)檢測電(diàn)動機座、軸承(chéng)座的單項精度、兩座軸線對導軌的等距度及接合麵的接觸精度,並將各支座打上錐銷孔定位;之後再進行滾(gǔn)珠絲杠副和其餘件的安裝。
3)絲杠裝配後的軸向竄(cuàn)動與徑(jìng)向跳(tiào)動。這兩項精(jīng)度對所傳動部件的運動(dòng)精度(dù)有很大影響,國家標準對於絲杠(gàng)的軸向竄動和徑向跳動有著嚴 格的規定,主要通過軸承的預緊進(jìn)行控(kòng)製。
4)聯軸器的安裝精度。要(yào)求安(ān)裝時絲杠(gàng)軸線與伺服電動機軸線(xiàn)同軸(zhóu)度為0.01mm。3.3 精度要求安裝過程中應重點保證如下精度。
3.3 精度要求
安裝過程中應重點保證如下精度。
1)軸承座、電動機座與床體接觸麵的接觸精度,螺母座端麵(miàn)與接合麵(miàn)的接觸精度:8個/25mm×25mm。
2)軸承座與(yǔ)電動機座軸承孔軸線(xiàn)與床身導(dǎo)軌(guǐ)的平行(háng)度0.01mm/200mm。
3)軸承座與(yǔ)電動機座(zuò)軸承孔軸線與床身導軌的等距度0.02mm。
4)伺服電(diàn)動機軸線與絲杠軸線的同軸度0.01mm。
3.4 保證精(jīng)度的措施
保證精度的(de)措(cuò)施如下。
1)首先,將電動機座(zuò)、軸承座各接觸(chù)麵(miàn)、棱邊、內孔各處清理幹(gàn)淨,保證各安裝麵無飛邊後,將其固定到床體麵上;然後,將軸承座、電動機座孔內分別裝(zhuāng)上檢驗棒,采用專用找表(biǎo)胎,以床身導軌為(wéi)基準,用千分表分別檢測兩(liǎng)檢驗棒的上母線、側母線,按具體情況調整(zhěng)各件;最後根據實測誤差配磨軸承座下的(de)調整墊,以達到精度要求。精度合格後,將電動(dòng)機座、軸(zhóu)承座分別打上錐(zhuī)銷孔,複查各(gè)檢棒精度合格後將(jiāng)檢棒拆下。
2)滾珠絲杠副安裝到軸承座過程中(zhōng),應保證軸承端蓋壓靠到軸承外環(huán)上,前後鎖(suǒ)緊螺母應采用力矩扳手安(ān)裝(zhuāng)並鎖緊。定(dìng)絲杠螺母座時,應(yīng)檢測螺(luó)母座端麵與接合麵的接觸(chù),保證(zhèng)螺(luó)母座與螺母接合麵的(de)平行度。為補償由於(yú)加工過程中絲杠溫度引(yǐn)起的伸縮變形,在裝配時還應通過鎖緊螺母對絲杠進行(háng)預拉伸。
3)該(gāi)聯(lián)軸器的安裝精(jīng)度主要通過加工保證,即(jí)電動機座上的110H7孔與A 孔的(de)同軸度保證了安裝(zhuāng)後徑向偏差的大小,伺服電(diàn)動機和電動機座接合麵與110H7孔的垂直度要求保(bǎo)證了安裝後角向偏差的大小,在加工過程中應重點保(bǎo)證其精度。
4 結語(yǔ)
經過近幾年對大連(lián)機床集團數控機床驅動裝置生產過程中加工及裝配工藝的研究,產品質量和出廠精度穩定性有了明顯(xiǎn)的提高,機(jī)床使用(yòng)的可靠性也有了明(míng)顯(xiǎn)的提高。
投稿箱:
如果您有機床行業、企(qǐ)業相關新聞稿件發表,或進行資訊(xùn)合作,歡迎聯係(xì)本網編輯部, 郵箱:skjcsc@vip.sina.com
如果您有機床行業、企(qǐ)業相關新聞稿件發表,或進行資訊(xùn)合作,歡迎聯係(xì)本網編輯部, 郵箱:skjcsc@vip.sina.com
更多相關信息
業界(jiè)視點(diǎn)
| 更多
行業數據
| 更多
- 2024年11月 金屬切削(xuē)機床產量數據
- 2024年11月 分地區金屬切削機床產量數據
- 2024年11月 軸承出口情況
- 2024年11月 基本型乘用車(轎(jiào)車)產量數據
- 2024年11月 新能源汽車產量數據(jù)
- 2024年11月 新能源汽車銷量情況
- 2024年10月 新能源汽車產量(liàng)數據
- 2024年10月 軸承出口情況
- 2024年10月 分地區金屬切削機床產量數(shù)據
- 2024年10月 金(jīn)屬(shǔ)切削(xuē)機床產量數據
- 2024年9月 新(xīn)能源汽車(chē)銷(xiāo)量情(qíng)況
- 2024年8月 新能源汽車產量數據
- 2028年8月 基(jī)本型乘用車(轎車)產量數據
博文選萃
| 更多(duō)