無偏差最小二乘法伺服控製係(xì)統參數辨識
2018-4-18 來源:合肥工業大學 作者:吳路路 韓江 田曉青 夏鏈
摘要:為準確辨識伺服控製係統參數,針對高(gāo)性(xìng)能運動控製算法的要求,在分析典型伺服控製係統結構模型基礎上,基於“庫侖摩擦+黏性摩擦”模型,設計了無偏差最小二乘方法,研究其在“工控機+運動控製卡”數控係統平台上的實現(xiàn)方法。實時采集電機角速(sù)度數據,利用設計的方法(fǎ)估(gū)算伺服係統(tǒng)轉動慣量、黏性(xìng)摩擦和庫侖(lún)轉矩,通過角速度重構,對比理論計算和實際測量角速度,驗證參數辨識的有效性和準確性。理論分析(xī)和實驗(yàn)結果表明,所設計的參數辨識方法能夠(gòu)準確辨識(shí)係統參數。
關(guān)鍵詞:伺(sì)服控製;無偏差最小二乘法;角速度重構(gòu);參(cān)數(shù)辨識
0、引言
設計高(gāo)性能(néng)的伺服驅動控製係統(tǒng),需要準確辨識(shí)執行機構的動力(lì)學(xué)參數。起初,控製係(xì)統都是(shì)基(jī)於偏差調節的反饋控製方式,為了降低運動軌跡(jì)的(de)輪廓誤差,要求各運動軸有匹配的閉環(huán)動態響應。隨後,在傳統反饋控製器的基礎上,人們(men)又提出前饋控(kòng)製算法,即在控製器中(zhōng)引入(rù)了(le)預估前饋數據。Tomizuka提出了(le)一種零相位誤差前饋控製器(qì)(ZPETC),通(tōng)過在前饋控製器中輸入零點來補償閉環係統的不穩定零點(diǎn),增加控製係統的帶寬,提高伺服係統的跟蹤精度。然而,對於ZPETC控製算法而言,如果想(xiǎng)要設計具有較強魯(lǔ)棒性的控製器,需要準確(què)獲取反(fǎn)饋係統的模型(xíng)參數。
Ramesh等指(zhǐ)出,如果控製係統(tǒng)參數與實際控製對象的參數不匹配,則使用前饋控製(zhì)器反而會降低係統的控製精度,即(jí)使采用最小方差(generalised minimum variance)和極點配置(zhì)方法設計係統控製器,如果(guǒ)想(xiǎng)獲得較好的控(kòng)製性能也需精確知曉(xiǎo)控製對象的參數。從工(gōng)業上(shàng)廣泛使用的 P、PI、PID 控製器,到(dào)較為複雜的 ZPETC 控製器,再到更複雜的集成控製器(qì),雖然各(gè)種控製算法都(dōu)有一定的抗幹擾(rǎo)能力,但對於突(tū)變的幹擾來說,這(zhè)些控製算法都(dōu)需要一定的時間來消除突變幹(gàn)擾的影響。在(zài)圓弧插補的過象限(xiàn)處和線性輪廓拐角處,運動軸方向改變,摩擦力方向會隨之發生突變(biàn),由於無法及時消除摩(mó)擦力的影響,該位置的精度(dù)會顯著降低。解決這一問題(tí)的方式就是利用已知的信息(如插補的參考位置、速度),提前預估即將產生的幹(gàn)擾情況,通過前饋補償的(de)方式來(lái)消除突變幹擾(rǎo)對係(xì)統運動精度的影響。然而,對於這種提前(qián)補償的方式,需要預(yù)先獲取突變幹擾的特征。就進給係統(tǒng)中因運動方向改變而發生突變的摩擦幹擾而言,需(xū)要(yào)提前掌握摩擦(cā)的特(tè)征才能進行(háng)補償。
本文通過最小二(èr)乘法辨識進給驅動係統的動力學(xué)模型參數和摩擦(cā)幹(gàn)擾的特征參(cān)數,進給(gěi)係統模型采用典型模 型,摩擦幹 擾 模型采用 “庫侖摩擦(cā)+黏性摩擦”模型。模型辨識實驗在基於“工控機+運動控製(zhì)卡+伺服電(diàn)機”的運(yùn)動控製平台上實現,通過重構(gòu)電機運行速度,驗證模型辨識的有(yǒu)效性。
1、伺服控製係統建模
伺服控製係統模型(xíng)采用在實際應用中廣泛使用的慣量阻尼模型,摩擦模型則(zé)采用(yòng)“庫侖摩擦+黏性摩擦”的結構。摩擦是影響進給係統控(kòng)製精度的(de)主要幹擾因素,因此本文主(zhǔ)要考慮摩擦因素,忽略測量噪聲、量化誤差等次要因素對模型參數的影響。
1.1 伺服係統模型(xíng)
圖1所示(shì)的進給驅動係統模型在伺服(fú)控製係統中廣泛使用,係統(tǒng)中等效轉(zhuǎn)動(dòng)慣量為(wéi)、黏性摩擦因(yīn)數(shù)為B。u是輸入的電壓控製信號,由於伺服驅動係統的電(diàn)流環帶寬在幾千赫茲以(yǐ)上,遠高於係統的采樣頻率(lǜ),因此電流環可簡化(huà)成一個比例放大環節,比例係數為 Ka。經過驅動器的放大作用,在電機(jī)電樞中產生電(diàn)流i,電機轉動形成驅動轉矩 Tm,電機的轉(zhuǎn)矩常數為 Kt。 除了電機產生(shēng)的驅動轉矩 Tm外,導軌、絲杠、軸承上的摩擦力會(huì)在(zài)電機軸上(shàng)產生幹擾轉 矩 Tf,驅(qū) 動 轉 矩Tm 和幹擾轉矩(jǔ)Tf共同作用驅(qū)動電機軸轉動。轉動角速度為ω,電機軸連接導程為rg的滾珠絲(sī)杠副,經由絲杠將角速(sù)度轉化為伺服係統的直線運動速度,直(zhí)線運動(dòng)速度(dù)為x·,經過一個積分環節得到伺服軸的(de)位置x。
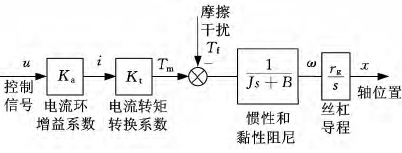
圖1 伺服控製係統模型
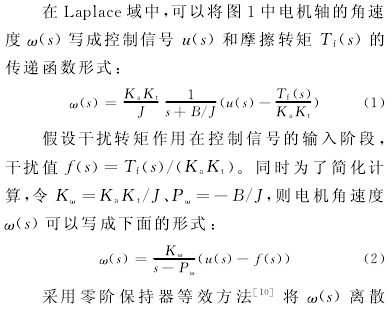
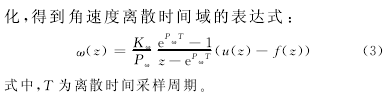
1.2 摩(mó)擦(cā)模型
文(wén)獻中對各(gè)種摩擦(cā)模型做了詳細的闡述,“庫侖摩擦 + 黏性摩擦”模型(xíng)能(néng)夠較準(zhǔn)確地反(fǎn)映摩擦特性,相比其他摩擦模(mó)型而言結構簡單,用較少的參數(shù)體現摩擦的特征,在工程中得到較(jiào)廣泛的使用。
文獻從工程實用角度采用圖2所示的模型(xíng),很好地補償了摩擦的影響,摩擦轉矩Tf與軸轉速ω在一定程度上成線性(xìng)關係。
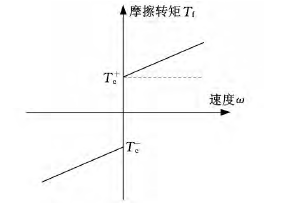
圖2 摩擦模(mó)型
當驅動轉矩小於庫侖摩擦轉矩Tc時,伺服係統運動(dòng)軸處於停止狀態,當軸運動(dòng)後(hòu),隨著角速度值增加,摩擦轉矩成現(xiàn)線性比例增(zēng)長,直線的斜率為進給驅動係統的黏性摩擦因數 B,當運動方向發生改變時摩擦轉矩發生突變。摩擦轉矩與角速度的關係如(rú)下公式所示:
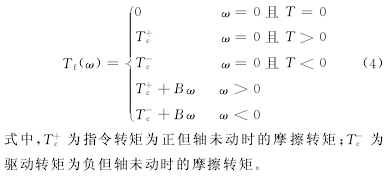
2、係統參數辨識
利用圖1所示的伺服係統模型和圖2所示(shì)的摩擦模型,在一個簡化的伺服係統上(shàng)進行參數辨識(shí)實驗。係統辨識采用兩種方(fāng)式:簡單最小(xiǎo)二乘法和(hé)無(wú)偏差最小二乘法。簡單最小二乘法忽略庫侖摩擦的影響,默認 Tc=0,實際辨識(shí)過程中隻需估(gū)算轉動慣量和黏性摩擦因數值;無偏差最小二乘(chéng)法考慮摩擦幹擾的影響,需要(yào)估算慣量、黏性摩擦因數和庫侖摩擦值。
2.1 簡單最小二乘法係統參數辨(biàn)識(shí)
采用簡單最小二乘法忽(hū)略運動方向改變時的摩擦突變的影響,認為 Tc=0。
根(gēn)據式(3),如果
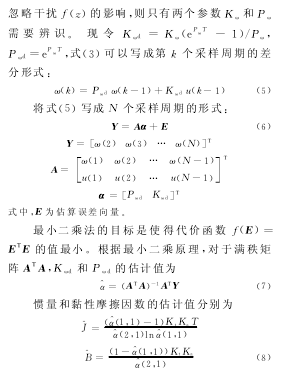
2.2 無偏差最小二(èr)乘法係統參(cān)數辨識
在實際工作過程中,由於幹擾的存在可能會(huì)使得(dé)估算值出現較大偏差(chà),故需要考慮幹擾對估算值的影響,此(cǐ)時式(3)寫成如下形式:
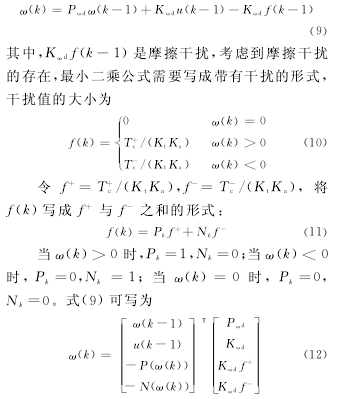
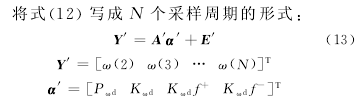
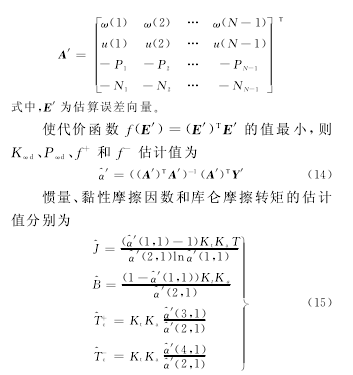
3、參數辨識實驗
通過兩種方(fāng)法(fǎ)辨(biàn)識伺服控製係統的轉動慣量和黏(nián)性阻尼係數,與(yǔ)平(píng)台的實際轉動慣量對比,驗證無(wú)偏(piān)差(chà)方法的準確(què)性;然後將兩(liǎng)種方法辨(biàn)識的結果分別代入到伺服係統模型中,根據輸入指令計算係統的理論輸出速度,並分別與實際(jì)采集的速度作對比,分析兩種方法的速度偏差,驗證無偏差方法的有效性。
3.1 實驗平台
伺服係統參(cān)數辨識實驗是在基於“工控機+運動控製卡+伺服電機”的平台(tái)上(shàng)進(jìn)行的,如圖3所示。工控機通過以太網(wǎng)總線向運動控製(zhì)卡發送控製指令,運(yùn)動控製卡根據指令值控製電機運轉,實時采集電機編碼器(qì)反饋的脈衝值,根據反饋(kuì)值計算電機(jī)實際轉動的(de)角速度;將電機的實際角速度實時反饋給工控機,工控(kòng)機將對應(yīng)時刻的角速度值寫入相關文檔,用於相關參數辨識。
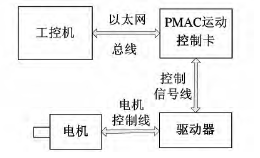
圖3 實驗平(píng)台結構(gòu)
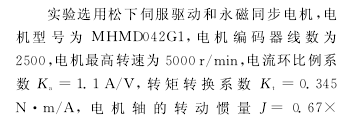

3.2 參數辨識
實驗(yàn)輸入的指令是一係列階躍電(diàn)壓信號,指(zhǐ)令電壓先增大再減小,共進行3組(zǔ)實驗,如圖4所示(shì)。3組實驗中,指令電壓值從0增加到每組實驗的最大(dà)值,再減小到0,相應階躍點的控製電壓值如表1所示,3組(zǔ)實驗的最大值分別為75mV、100mV 和(hé)150mV,最小值為0。
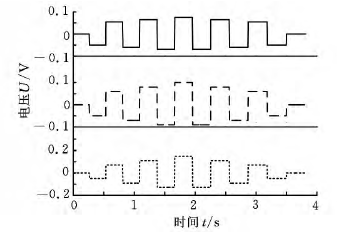
圖4 3組實驗指令電壓信號
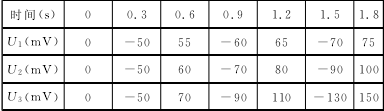
表1 指令電壓值
利用 PMAC 運動控(kòng)製卡實時(shí)采(cǎi)集電機的速度值,利用(yòng)式(shì)(7)和式(shì)(14)分別對係(xì)統的參數進行估算,得到轉動慣量、黏性摩擦和庫侖摩擦轉矩的估計值。表2是通(tōng)過簡單二乘法獲得(dé)的轉(zhuǎn)動慣量(liàng)和黏性(xìng)摩擦值。表3是通過無偏差最小二乘法得到(dào)的轉動慣量、黏性摩擦值和庫侖摩擦轉矩值。圖5是3組實(shí)驗的估算值對(duì)比圖(tú)。
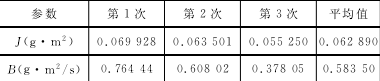
表(biǎo)2 簡單(dān)最小二乘(chéng)法估算值
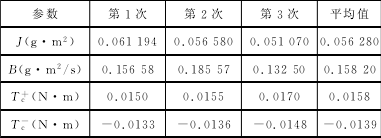
表3 無偏差最小二乘法估算值
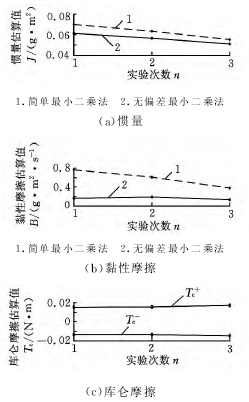
圖5 實驗數據對比
對比3組實驗的估算值,簡單最小二乘法得到的轉動慣(guàn)量(liàng)和(hé)黏性摩擦(cā)值相(xiàng)對較大(dà),且3組實驗結果存(cún)在較大差異,無偏差最小二乘(chéng)法3組實驗得到的估(gū)算值(zhí)波動較小,三次實驗的結(jié)果基本一致。由表(biǎo)2可得簡單最(zuì)小二乘法3組實驗(yàn)的平均估算值為
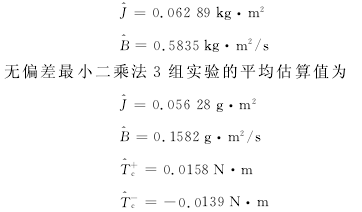
對比實際和辨識所得的(de)伺服控製平(píng)台的轉動慣量值,從以上(shàng)的估算結果可以看出(chū),兩(liǎng)種(zhǒng)方式估算得到的轉動慣量值都很接近實際(jì)值,兩種方式都能(néng)很好地辨識(shí)係統的(de)轉(zhuǎn)動慣量。然而,簡(jiǎn)單最小二乘方式辨識得到的轉動慣量和黏性摩擦的值相對無偏差方式較大,而且3次(cì)辨識的結果差別較大。簡單(dān)最小二乘法未考(kǎo)慮庫侖摩擦(cā)的影(yǐng)響,將庫(kù)侖摩擦的影(yǐng)響轉化成黏性摩擦的影響,致使黏性摩擦和轉動慣量 值增大並使得結果波動較大。
為了驗證辨識參數(shù)的有(yǒu)效(xiào)性和(hé)準確性,將辨識獲得的參數代入到理論模型中,根據輸入的電壓指令計算並重構理論角速度,將理論角速度與實測角速度相比較,結果如圖6所示。
采用簡單最小二乘(chéng)方式重構的角速度最大誤差值為15rad/s,無偏差方式重構的角(jiǎo)速度誤差值為7rad/s,不到前一種方式 的一 半,采 用 無 偏 差(chà) 方式辨識獲得(dé)的參數重新構建的角速度與實際的角速度相(xiàng)符度更高,更能準確地描述實際(jì)伺服係(xì)統。
采用無偏差方式估算的參數(shù)計算(suàn)得到的理論角速度曲線更接(jiē)近實測角速度曲線,而且角速度誤差波動更小。
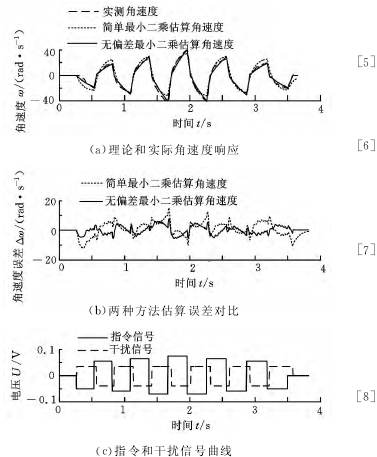
圖6 角速度重構與分析圖
4、結語
本文(wén)分(fèn)析了伺服控製係統結構模型,采用無偏(piān)差(chà)最小二乘方法,基(jī)於“庫侖摩擦+黏性摩擦”模型,辨識伺(sì)服控製係統參數(shù)。研究了最(zuì)小二乘法(fǎ)參(cān)數辨識在(zài)“工控機+運動控製卡”數控平台上的(de)實現(xiàn)方(fāng)法,從理(lǐ)論和實驗的(de)角度分析了辨(biàn)識方法的準確(què)性。通過辨識實驗獲得係統的參數,並將估算得到的係統參數代入係統(tǒng)模型,重構電機(jī)角速度。實驗(yàn)結果表明,所采用無偏差最小二乘方法可以更準確地辨識係(xì)統的參數。
投(tóu)稿箱:
如果您有機床行業、企業相關新聞稿(gǎo)件發表,或進行資訊合作,歡迎聯係本網編輯(jí)部, 郵箱:skjcsc@vip.sina.com
如果您有機床行業、企業相關新聞稿(gǎo)件發表,或進行資訊合作,歡迎聯係本網編輯(jí)部, 郵箱:skjcsc@vip.sina.com
更多相關信息
業(yè)界視點
| 更多
行業數據(jù)
| 更多
- 2024年11月 金屬切削機床產量數(shù)據
- 2024年(nián)11月 分地區金屬切削機(jī)床產量數據
- 2024年11月 軸承出口情況
- 2024年11月 基本型乘用車(轎車)產量數據
- 2024年11月 新能源(yuán)汽車產量數據
- 2024年11月 新能源汽車銷量情況
- 2024年10月 新能源汽車產(chǎn)量數據
- 2024年10月 軸承(chéng)出口情況
- 2024年10月 分地區金屬切(qiē)削機床產量數據
- 2024年(nián)10月 金屬切(qiē)削機床產(chǎn)量(liàng)數(shù)據
- 2024年9月 新能源汽車(chē)銷(xiāo)量情況
- 2024年8月 新能源汽車產量數據
- 2028年8月 基本(běn)型乘用車(轎車)產量數據