基於精雕係統的七級葉輪加工技術實踐
2024-3-7 來源:北京精雕科技集團有限公司 作者:張歡龍
1. 序言
葉輪是渦輪增壓器最關鍵的零件之一,廣泛應用於航空、船舶、汽車和真空泵等行業的發動機中,其中七(qī)級葉片的複雜葉輪是渦輪分子泵內部的核心部件,而(ér)渦輪分子泵則(zé)廣泛應用於(yú)真(zhēn)空鍍膜(PVD)、半導體製造等行(háng)業(yè)中,這(zhè)些(xiē)行業需要在超高真空(kōng)環境(10-7Pa 以下(xià))中才能工作(zuò)。
考慮到葉片結構複雜、曲麵變化大以及精度高等特點,目前一般采用 Mastercam、PowerMill、UG及CATIA等國外軟件結合(hé)五軸聯動機床加工,這些五(wǔ)軸聯動機床(chuáng)一般采(cǎi)用海德(dé)漢、西門子等國外高檔數控係統。為打破國外軟件和數控係統在葉輪製造方麵的壟(lǒng)斷(duàn)地位,北京精雕科技(jì)集團有限公司(以下簡(jiǎn)稱北京精雕)開發了擁有自主(zhǔ)產權的 SurfMill 軟件以及北(běi)京精雕五軸聯動係統,並采用在線檢測、在線補償功能加工葉(yè)輪。
本文采用北京精雕(diāo)的 SurfMill 軟件造型(xíng)並采用 JDGR400 五(wǔ)軸聯動精雕機,對七級葉輪的五軸編程、工(gōng)藝規(guī)劃和實際加工進行探討與實踐。
2.七級葉輪結構及加工難點分析
七級葉輪(見圖 1)的基本(běn)特點 : 葉片分為7 級,共 249 個葉片,材料為 7075 鋁合金,尺寸f360mm×286mm。該零(líng)件上的葉片是由鋁(lǚ)合金整(zhěng)體加工而成(chéng),葉(yè)片加工完成後整體質(zhì)量 14kg。
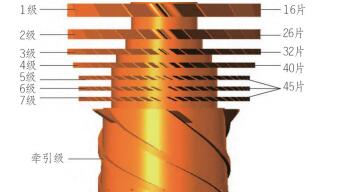
圖(tú) 1 七級葉輪
經分(fèn)析,七級葉輪五軸聯動加工(gōng)的難點如下。
1)該葉片屬於典型的(de)薄壁件,葉片高度與厚度比> 30:1,葉片剛性(xìng)差,加工時受力易變形,極易產(chǎn)生振動,彈刀過切風(fēng)險很大。
2)相鄰葉片間距小,導致加工所需刀具(jù)最大長徑(jìng)比(bǐ)為 14:1(見圖 2),加(jiā)工時刀具的切削剛性差。
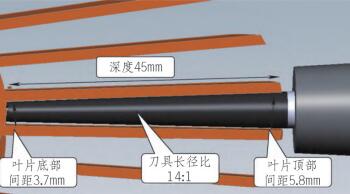
圖 2 刀具長徑比示意
3)葉片數量多達 249 個,葉片間距(jù)小,每一級之間距離小,刀具和葉片之間的安全距(jù)離最小隻有(yǒu) 2mm,加工時極易產(chǎn)生幹涉,如圖 3 所(suǒ)示。
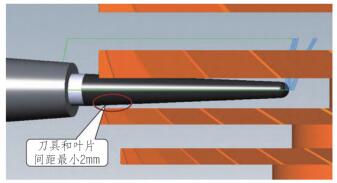
圖 3 刀具與葉片幹涉示意
3.七級葉輪五軸加工工藝規劃
3.1 設備(bèi)及軟件的選用
葉輪加工設備需要有強大的運算能力,且加工時主軸轉(zhuǎn)速高、擺動角度範(fàn)圍大、聯動精(jīng)度高,本次選(xuǎn)用北(běi)京精雕的 JDGR400_A15SH 機床,配置在(zài)機測量係統、激光對刀儀等設備,並采用北京精雕自有的軟件(jiàn) SurfMill 進行建模和編程。
3.2 刀(dāo)具的選用
針對薄壁件,刀(dāo)具(jù)的選擇需(xū)要(yào)從(cóng)減小切削力的角(jiǎo)度出發,因此選(xuǎn)擇角度較(jiào)大的前角和後角、較大的螺旋角(見圖 4)來減小切削力 ; 刀具結(jié)構采用短刃刀具(見圖 5),錐度避空,提升刀具剛性 ; 塗層選用 DLC 塗層,塗層厚 1μm,提高刀具鋒利度,減小切削力,提高刀具壽命及長時(shí)間加工時的穩定性。
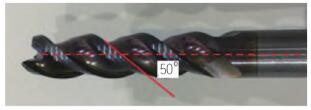
圖 4 大螺旋角

圖 5 錐度(dù)平底(dǐ)短刃刀具
3.3 加工工藝方案
針(zhēn)對(duì)長(zhǎng)徑比(bǐ)大的難題,為了(le)增加刀具的剛性,在(zài)深度上采(cǎi)用多把刀具分段加工的(de)方式,以保證切削剛性,提高(gāo)加工效率。刀具型號及加(jiā)工(gōng)參數見表 1。
表 1 刀具型號及加(jiā)工參(cān)數
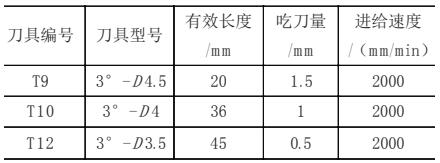
3.4 編程加工方案
七級葉輪葉片數量多、間距小,刀具極易產生幹涉和過切。為避免在實際加工中出現問題,采用北京精雕的 DT 編程技術,在軟件中實現過(guò)切檢查、幹(gàn)涉檢查和機床模(mó)擬,在計算(suàn)機端確保(bǎo)加工程序的安全,從而避免機床實際加工中的過切、幹涉和碰撞等問題,如圖 6 所示。
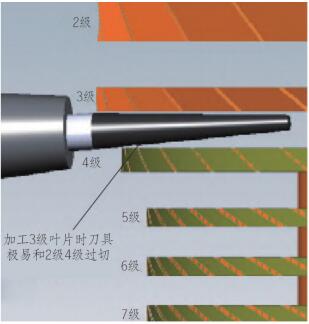
a)刀具與(yǔ)工件幹涉(shè)示意

b)DT 仿真加工(gōng)
圖 6 葉(yè)輪加工模擬
DT 編程技術最大的特點就是改變原有的調試模式(shì),將原來需要在機床上進行的操作(包括試切加工、人為觀察過切和碰撞,以及機床行程檢測等),全部加載到計算機中進行,減少人員機床上的操作,減輕調試人員(yuán)的心理壓力(lì),降低調試(shì)出(chū)錯的成本,縮短產品(pǐn)調試周期。
4. 加工試驗及方案改進
按照規劃的方案進(jìn)行加工試驗,試製(zhì)結果見表 2。通過(guò)表 2 數據可看出,試製結果不滿足工藝要求,需要優化改進。
表(biǎo) 2 試製結果
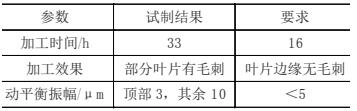
4.1 方案優化改(gǎi)進(jìn)
經分析,需要從 4 個方(fāng)麵進行優化改進 : ①優化加工效率。②改善表麵質量。③改進夾持治具。④管控(kòng)毛坯精度。
1)利用 CAM 軟件優化葉片間連刀高度。第一階段為保證絕對的安全,將葉片之間(jiān)路徑安全位置設置在 Z 軸原點位置 ; 優化階段依(yī)靠 DT 編程技術,將刀具連刀高度抬至葉片最高高度之上30mm,加工時間縮短了 6.5h。
2)優化 T9、T10 刀具有效長度,增加刀具剛性。試製用的 T9、T10 刀(dāo)具有效長度過長(zhǎng),刀具剛性差,切削參數無法提升,嚴重影響加工效率。依靠(kào) D T 編程技術,精確計算 T9、T10 刀具所需的最短有效長度,從而提升刀具剛性,增加刀具切削用量,將(jiāng)葉輪加工時間縮短(duǎn)了 55min。
3)優化表麵質量,縮(suō)短人工處理時間。葉輪加工完成後,其(qí)葉片銳角(jiǎo)邊留下了大量的毛刺,需要手工清理,工作量較大,並且毛刺會影響工件整體動平衡性能,因此在加工時(shí)加入去毛刺程序,節省去毛刺的時間。另外(wài),在機測量刀具錐度,減輕不同刀具間的接刀痕,使用激光對刀儀準確測量刀具錐度和直(zhí)徑,將刀具偏差補償在加工路徑中,確保各刀具間的接刀痕< 0.008mm。
4.2 解決動平衡問題
對於產品的批量生產,動平衡振幅能否控製(zhì)在 5μm 以內是生產(chǎn)的關鍵。目前機床精度、溫度管控都是合格的,針對動平衡偏大問(wèn)題,經過分析判(pàn)斷,是治具錐麵和毛坯錐麵配合誤差較大,使得毛坯安裝後毛坯軸線傾斜引起的。毛坯(pī)軸向圓跳動> 0.04mm,直接(jiē)影響葉輪加工(gōng)後的動平衡(héng)。治具夾持如圖 7 所示。
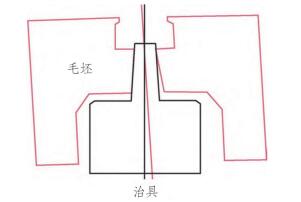
圖(tú) 7 治具夾持(chí)示意
重新精磨治具,其錐(zhuī)度達到 5° 43′ 9″,毛坯安裝後跳動得到大幅改善,結果見表 3。
表 3 精磨治具後(hòu)跳動改善結果
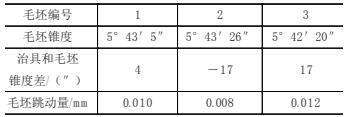
4.3 曲麵加(jiā)工方案
葉(yè)片曲麵根據曲率可分為自由曲麵和直(zhí)紋(wén)曲麵(miàn),自由曲麵采用五軸點銑方式加工,直紋曲(qǔ)麵采用(yòng)五(wǔ)軸側銑方式加(jiā)工,如圖 8 所示。
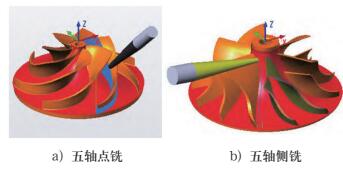
圖 8 曲麵加工方式示意
在 SurfMill 中建模和編(biān)程。分層粗加工如圖9 所示,流道精加工如(rú)圖 10 所示。

圖 9 分層粗加工
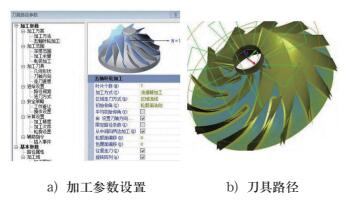
圖 10 流道精加工
4.4 改進後的實際加工驗證
利用(yòng) DT 技術和軟件編程,優化了(le)刀(dāo)路和加(jiā)工程序,避(bì)免了幹涉,消除(chú)了動平衡(héng),提高了加工效率,同(tóng)時零件的加工質量得到提升。加工後的零件如(rú)圖 11 所示,經檢測,達到了葉輪尺寸精度和表麵粗糙度的要求。
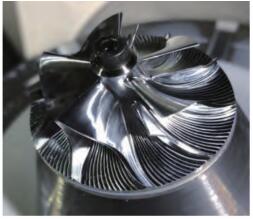
圖 11 加工後的七級葉輪
5. 結束語
本文在分析七級葉輪結構特點和加(jiā)工難點的基礎上,對機床選用、刀具選擇、工藝修正以及治具(jù)改進(jìn)等(děng)做了深入分析。為提高效率,避免幹涉,采用(yòng)北京(jīng)精雕(diāo)特有的 DT 技術(shù)進行模擬校正,並通過(guò)試件的研製,優化一係列(liè)工藝參數,最(zuì)後在北京精雕五軸聯動機床上完成七級葉輪的加工,加工精度、表麵(miàn)粗糙度以及動平衡等都符合要求,給(gěi)類似的葉輪及(jí)複雜零件的加工提供了參考。
投稿箱:
如果您有(yǒu)機床行業、企業相(xiàng)關新聞稿(gǎo)件發表,或進行(háng)資訊合作,歡(huān)迎聯係本網編輯部, 郵箱:skjcsc@vip.sina.com
如果您有(yǒu)機床行業、企業相(xiàng)關新聞稿(gǎo)件發表,或進行(háng)資訊合作,歡(huān)迎聯係本網編輯部, 郵箱:skjcsc@vip.sina.com
更多(duō)相關信息
業界視點
| 更多
行業數據
| 更多
- 2024年(nián)11月 金屬切削機床產量數據
- 2024年11月 分地區金屬切削(xuē)機床產量數據
- 2024年11月 軸承出口情況
- 2024年11月 基本型乘用車(轎車)產量數據(jù)
- 2024年11月 新(xīn)能源汽車產量數據
- 2024年11月 新能源汽車銷量情況
- 2024年10月 新能源(yuán)汽車產(chǎn)量數據
- 2024年10月 軸承出口情況
- 2024年10月 分地區金屬切削機床產量數據
- 2024年10月 金屬切削機床產量數據
- 2024年9月 新能源汽車銷量情況
- 2024年8月 新能(néng)源汽車(chē)產量數據
- 2028年8月 基本型乘(chéng)用車(轎(jiào)車)產量數據