新能源汽車電驅動總成及製造技(jì)術
2023-7-5 來源: 上海市汽車行業協會(huì) 作者:張書橋
1. 序言
發展新能源汽車是我國從汽車大國邁(mài)向汽車強國(guó)的(de)必由之路,新能源汽車概念最早(zǎo)於 “863”計劃中提(tí)出。在新能(néng)源汽車發展規劃中提出了“三縱三橫” 的(de)技術研發(fā)布局,即以純電動車、插電式混合動力(含增程式)汽車、燃料電池汽車為“三縱”,布(bù)局整車技術創新鏈,強化(huà)整車集成控製創新。以(yǐ)動力電池和(hé)管理係統、驅動電動機與電力電子、網聯化與智能化(huà)技術為 “三橫”,構建關鍵零部件技(jì)術供給體係,提升產(chǎn)業基礎能力(lì)。2022 年中國新能源汽車持續爆發式增長,全年(nián)銷量 680 萬輛,市場滲透率 25.6%。2023 年(nián)預計為 900 萬輛,同(tóng)比(bǐ)增長 35%。我國新能(néng)源汽車市場培育了全球最大的電(diàn)動車市場(chǎng),電池供應鏈體係遠遠領先美國和歐洲,但是品牌競爭力弱,尚未被全球市場廣泛(fàn)接受(shòu)。
2. 電驅動總成
電驅動總成是新能(néng)源電動(dòng)車的心髒,等同於傳統燃油車的動力(lì)總成(chéng)——發動機 + 變速器,作用是把化學能轉化成(chéng)電動車(chē)的動能,是直接決定車輛動力、能(néng)耗等性能的(de)核(hé)心部件。
電驅動總成是以電動機(jī)作為動力(lì)能源的驅動係統,包(bāo)括電動機控製(zhì)器、電動機及傳動機(jī)構。電驅動總成是電動車中至(zhì)關重要(yào)的(de)機構,直接影響到汽車壽命(mìng)以(yǐ)及駕駛員的安全。
純電動車(chē)的電驅動總成有四種形式,分別為傳統布置、電動機 & 驅動橋(qiáo)組合式、電動機 &驅動橋整體式、輪邊 / 輪轂電動機。四種電驅動總成的特點見表 1。
表 1 四種電驅動總成的特點
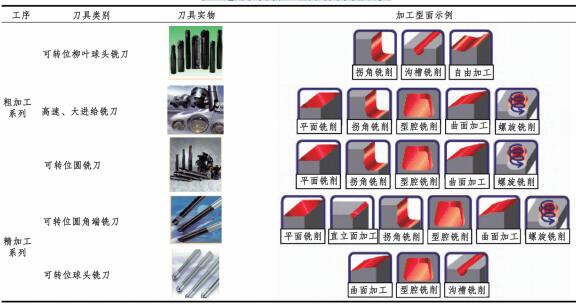
電動車驅動係統是電動車(chē)中最關鍵的係統,電(diàn)動車運行性能主要決定(dìng)於電動機驅(qū)動係統的類型(xíng)和性能。電動車驅(qū)動係統一般由牽引電動機、控製係(xì)統(包括電動(dòng)機驅動器、控製器及(jí)各種傳感器)、機(jī)械減速和傳動裝置(zhì)、車輪(lún)等構成。它有四種組合形式,分別為機械驅動係統、機電集成化驅動係統、機電一體化驅動係統及輪轂電動機驅動(dòng)係統。四種驅動係統的特點見表 2,幾種典型的驅動係統如圖 1 所示。
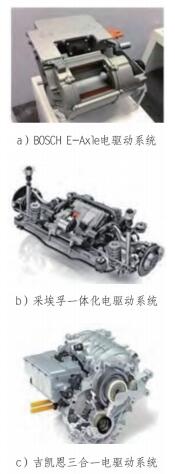
圖 1 典型的電驅(qū)動係統
表 2 四種驅動係統(tǒng)的特點
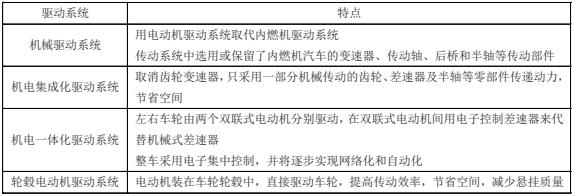
隨著中國新能源汽車銷量的逐步增加,電動化將催生(shēng)電驅動總成成為繼電池係統之後的第二個賽道,預計2025—2030年中國新能源汽車(chē)電驅動市場規模將達到 866 億 ~1572 億元(yuán)。縱觀全球新(xīn)能源汽車研發方向,由於受到車輛空(kōng)間限製和使用(yòng)環境的約束,電動汽車對電驅動總成提出了更高的要求 : ①更高的性能,低速大扭矩,寬恒功率等。②耐環(huán)境溫度更高,壽(shòu)命更長(zhǎng),噪聲更低。③耐高強度振動,結構(gòu)堅固,質量輕,體積小。④成本低。⑤參與整車(chē)熱管(guǎn)理。
3. 電動機
美國汽車行業(yè)指定了電動機(jī)發展路線圖,到2025 年效率> 97%,功率密度 5.7kW/kg,成本3.3$/kW。按照這樣的發展方向,今後電動機的(de)改(gǎi)進有以下幾方麵。
3.1 發卡電動機——Hair-pin扁線(xiàn)電動(dòng)機技術
相對圓(yuán)線電動機,采用 Hair-pin 扁線電動機(見圖 2)可以明顯減小電動機體積、減輕電動機質量、增加電動機功(gōng)率密度及(jí)轉矩密度。通常可將(jiāng)槽滿率(lǜ)提高至 70% 以上(shàng),超過普通繞組 20%~30%,有效降低繞組電阻,從而降低銅耗,產生更強的磁場強度,提升電動機功率密度。扁線之間接觸麵積大,可提高散熱效率。繞組(zǔ)端部更(gèng)短,可以降低電動(dòng)機端部空間用銅量15%~20%。
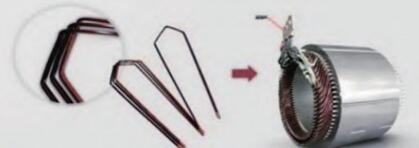
圖 2 Hair-pin 扁線電動機
3.2 永磁同步電動(dòng)機
永磁同步(bù)電(diàn)動機(見圖 3)的優勢是體積小、質量小、功率密度高、運(yùn)行(háng)效率高(gāo)、結(jié)構簡單緊湊(còu)、扭矩大且平順、調速性能好。劣勢是(shì)弱磁控製(zhì)問題、反電動勢及高(gāo)溫(wēn)振動環境下的退磁問題。
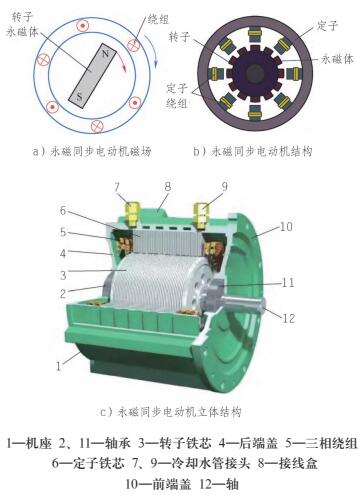
圖 3 永磁同步電(diàn)動機
轉子轉速與定子磁場的轉速保持(chí)同步。降(jiàng)低定子、轉子的鐵耗也非(fēi)常重要,定子、轉子矽片內部會因(yīn)為電流磁場等(děng)變化而產生渦流,為了減少這部分的渦流(liú)損耗,矽鋼(gāng)片的(de)厚度越來(lái)越薄,從 0.35mm 降到 0.3mm 以(yǐ)下。為了優化電動機內部的磁場分布,提高電(diàn)動機效率,針對轉(zhuǎn)子鐵芯的磁道(dào)設計也(yě)得到越來越多的關注。
3.3 混合磁鐵技術
混合磁鐵技術就是用燒結永磁鐵 + 永磁體粉末與黏合劑混合。美國 Lucid Air 公司電動機每英裏(lǐ)的能耗為 218W · h,特斯拉(lā) Model S 每(měi)英裏能耗為 250W · h,續航(háng)裏程美(měi)國 Lucid Air公司超過特斯拉 Model S100 餘英裏(1 英裏=1609.344m)。
混合磁鐵技術把一切空間利用到(dào)極致,磁鐵填滿所有的空隙(xì)。釹(nǚ)鐵硼燒結永磁體是難加工成異型的,就是在燒結永磁鐵的基礎上,將永磁體粉末與黏合劑混合,直接填滿整個空(kōng)間,既解決磁鐵(tiě)固定的問題,又增加了磁通量,如圖(tú) 4 所示。
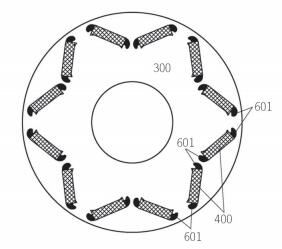
圖 4 混合磁鐵技(jì)術
3.4 碳纖維套筒
高轉速(sù)隔磁橋的設計一直是難點,轉子高速旋轉,轉速大,離心率大,轉子邊緣的(de)部位容(róng)易受壓破裂。如果加(jiā)厚隔磁橋,會產(chǎn)生閉合磁場,在轉子內部,沒有(yǒu)與定子磁場產生相互作用,磁場就會浪費,效率被限製,產生鐵耗、增加發熱,高熱加劇轉子的膨脹和解體的風險。
特斯拉在電動機轉子上增加了(le)碳纖維保護(hù)套,其核心作用是加強電動機和轉子的結構強度(dù),防止高速工況下永(yǒng)磁鐵的脫落。特斯拉碳纖維轉子如(rú)圖 5 所示。
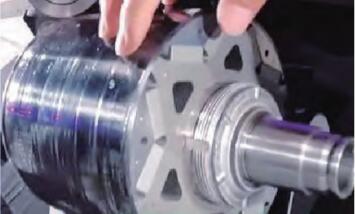
圖 5 特斯拉(lā)碳纖維轉子
3.5 油冷卻
隨著電動(dòng)機(jī)功率密度和轉速的不斷提升,以(yǐ)及集成化使單體部件體積逐漸縮小,傳統電動機的風冷或者外殼水冷方(fāng)式已經(jīng)無法滿足散熱需求,油冷電動機(jī)技術路(lù)線逐漸興起。冷卻油可直接與電(diàn)動機發熱部件接(jiē)觸,散熱效率高於傳統的水冷和風冷(lěng),且油介質具有絕緣性好、介質常數高、凝固點低和沸點高等優勢,可提升電動機的效率密度。對原有的熱管理係統(tǒng)進行重新設計,將電動機腔體和減速(sù)器打通,然(rán)後通過電子油泵或機械設計,使(shǐ)減振器內部原有的冷卻潤(rùn)滑油能夠進入到電動機內腔,實現定子(zǐ)、轉子的物理降溫。另(lìng)外對油品的性能和清潔度有更高的(de)要求。扁線(xiàn)油冷電動機轉子如圖 6 所示。
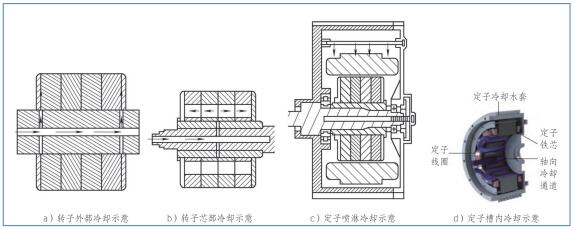
圖 6 扁線油冷電動機(jī)轉子
4. 二(èr)級變速器
電動車電動機的工作範圍廣,轉速一般在0~20000r/min,甚至可以達到30000r/min。相對(duì)來說,中低轉速的情況下,電動機的扭(niǔ)矩非常足,工作效率相對較(jiào)高 ; 在高速的情況下(xià),電動機的效率和扭矩則會急速下降。而二級變速器(qì)的作用就是(shì)使(shǐ)電動機盡量工作在高效率的轉速區間,從
而降低損(sǔn)耗,提高續航裏程,可節省的電量高達13%。二級(jí)變速器的電(diàn)動機效率如圖 7 所示。
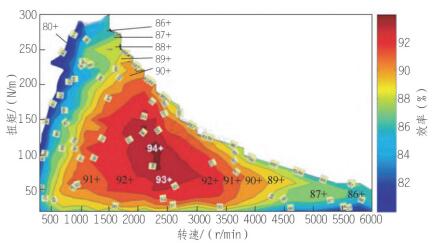
圖 7 二(èr)級變速器的電動機效率
5. 高壓化
美國汽車行(háng)業三電控製器發展路線(xiàn)圖中提出,到 2025 年(nián)電控效率> 98%,密度 100kW/L,成本 2.7$/kW。對(duì)於電動車來說,高壓(yā)化可大大減少同等功率需求條(tiáo)件下電驅動總(zǒng)成內組的損耗,提高係統效率,繼(jì)而可進一步減少達成同樣續航裏程條件下的電池電量。減少電池成本的同時降低整車質量。另(lìng)外,高壓化還能(néng)提(tí)高充電效(xiào)率(lǜ)。因此,提(tí)高電動車整車(chē)電壓至800V,甚至(zhì)1000V是行業的發展方向。
例如保時捷 Taycan 是首款 800V 高壓平台的量產車型,同等功率下,當電壓從(cóng) 400V 提升到 800V 時,工作電流將降低一半,進而線束(shù)體積、功率損耗均有下降。與奧(ào)迪 e-tron 400V 電壓(yā)平台對比,係統能耗損失降(jiàng)低 5%,續航裏程增加10%,質量減少 20%,係統尺寸優化 30%,其中電動機尺寸可優化 35%。
6. 電驅動總成製造技術(shù)
電驅動總(zǒng)成不斷發展,其新的製造技術主要圍繞輕量化、高速(sù)化、低噪(zào)聲及一體化。
6.1 一體化壓鑄
三電(diàn)係統通(tōng)常占新能源汽車質量的30%~40%,因此(cǐ)三(sān)電係統是新能源汽車(chē)輕量化(huà)的主要方(fāng)向(xiàng)。與傳統汽(qì)車相比,新能(néng)源汽(qì)車三電(diàn)係(xì)統將導致整(zhěng)車質量增加,三電(diàn)係統會額(é)外增加200~300kg 的(de)質(zhì)量。新能源汽車動力總成(chéng)係統比傳統燃油車重 1.5~4.0 倍。目前三電係統的電子殼(ké)體、電(diàn)動機殼體、電控殼體、電池構件及電(diàn)池箱都在使用鋁壓(yā)鑄產品,雙電動機桶和電控殼(ké)體如圖 8、圖 9 所示。
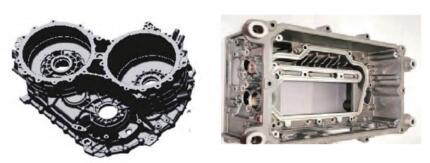
圖 8 雙電動機桶 圖(tú) 9 電控殼體
6.2 強力珩齒
由於電動(dòng)車中電動機要求更高的轉速——15000~30000r/min,更嚴苛的噪聲限製NVH(噪聲、振動與聲振粗糙度),更高精度(dù)的動力齒輪要求——4~5 級,更高的波紋度和表麵(miàn)粗糙度,更高的幾何公差(chà)來降低不穩定(dìng)性,所以要采用強(qiáng)力珩(héng)齒(chǐ)工藝。強(qiáng)力珩齒工(gōng)藝的特點是機床對於磨齒具有更小的退刀間隙,齒麵加工為魚刺紋,區別於傳統磨齒的直線型紋路,此外具有(yǒu)更好的NVH 特性,降低(dī)噪聲,適合高速旋轉的電動機軸。
6.3 行星(xīng)齒輪
錐齒輪(lún)結(jié)構跟傳(chuán)統的(de)差(chà)速器(qì)差別很大,采用(yòng)行星齒輪可實現小型化,多個外部齒輪繞著中間齒輪旋轉,行星齒輪承載能力大、體積小,多(duō)個行星齒(chǐ)輪相互配合作用,每個齒輪傳動之間的效率損失隻有(yǒu) 3%,幾乎無反衝。行星齒輪如圖 10 所示(shì)。行星齒輪加工工藝流程為 : 鍛造(zào)→車削→強力刮削→熱處理→磨孔珩孔→平麵磨→珩(héng)齒→清洗。
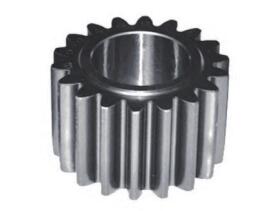
圖 10 行星齒輪
6.4 切削技術
電動機是新能源汽(qì)車的核心部件,其(qí)製造要求高精(jīng)度、高效率和高可靠性,特別(bié)是切削精度直(zhí)接影響汽車的質量。很多刀具企業針對驅動電動機殼可(kě)提供整體解決方案(àn),例如森泰英格的鏜刀(dāo)(見圖 11)采(cǎi)用合金鋼整體輕量化(huà)設計,刀體質量控(kòng)製在 18kg 以內,多台階 PCD 導條式(shì)可(kě)調鏜鉸刀(dāo),多切削刃,內冷設計。相較於單刃鏜刀,可提高效率 6 倍以上。另(lìng)外森泰(tài)英格自主研發的可轉位強力車(chē)齒(chǐ)刀(見圖 12),采用高剛性精密(mì)定位接口技術和複合基多熵納米塗層技術,刀片耐磨性更好,壽命更長。
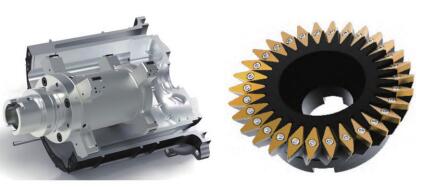
圖 11 鏜刀 圖 12 車齒刀
電(diàn)動機(jī)軸花鍵的加工方法有很多,以往主要采用車削、銑削、滾切和磨削等(děng)加工方法。滾軋刀通過數控(kòng)機床進(jìn)給的優點是刀具可以在任意位置切入工件,而不像傳統的搓齒工藝(yì)工件成形圈數受齒條長度(dù)限製。如(rú)圖 13 所(suǒ)示為恒鋒工具(jù)股份有限公司開發的滾軋刀。
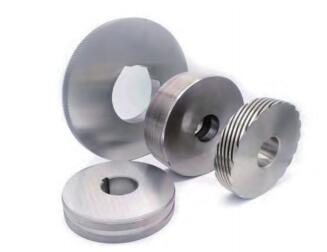
圖 13 滾軋刀
隨著電驅動(dòng)的一體化,電動(dòng)機軸(zhóu)最受青睞的加工方式還是冷擠壓成形工藝,冷擠壓的工件(jiàn)尺寸(cùn)準確、強度(dù)高。從生產廠家角度(dù)講,冷擠壓工藝節約材料,生產(chǎn)效率(lǜ)高,適用麵廣。
投稿箱:
如果(guǒ)您有機床行業、企業相關新聞稿件發表,或進行(háng)資訊(xùn)合作(zuò),歡迎聯係本網編輯部, 郵箱:skjcsc@vip.sina.com
如果(guǒ)您有機床行業、企業相關新聞稿件發表,或進行(háng)資訊(xùn)合作(zuò),歡迎聯係本網編輯部, 郵箱:skjcsc@vip.sina.com
更多相關信息
業界視點
| 更多
行業數據
| 更多
- 2024年11月(yuè) 金屬切削機(jī)床產量數據
- 2024年11月 分地(dì)區金屬切削機床產量數據(jù)
- 2024年11月 軸承出口情況
- 2024年11月 基本型乘用車(轎車)產量數據
- 2024年11月 新(xīn)能源汽車產量數(shù)據
- 2024年11月 新能源汽車銷量情況
- 2024年10月 新能源汽車產(chǎn)量數據
- 2024年10月 軸承出口情況
- 2024年10月 分(fèn)地區金屬切削機床產量數據
- 2024年10月 金屬切削機床產量數據
- 2024年9月 新能源汽(qì)車銷量情況
- 2024年8月(yuè) 新能源汽車產量數據
- 2028年8月 基本型乘用車(轎車)產量數據