高精度數控機床主軸係統熱(rè)誤差的(de)控製方法
2021-1-27 來源:西安(ān)交通大學 陝西省智能機器人(rén) 等 作者:趙亮 雷默涵 朱星星 王帥 淩正 等
摘(zhāi)要:為了解決高(gāo)精度數控機床主軸係統熱誤差的難題,提出了一種(zhǒng)主動控製主軸熱(rè)誤差的新方法.根(gēn)據設(shè)計的螺旋盤管冷卻器(qì),分析了矽脂厚度對主軸與冷卻(què)器間的接觸熱阻的影響規律,建立了熱阻模型.在簡化主軸係統模型的基礎上,構建了主軸係統的(de)熱-流-固有限元模型,並對冷(lěng)卻參數進行(háng)了仿真.利用搭建的溫度控製係(xì)統,對(duì)有限元模型進行驗證(zhèng).結果表明,有限元模型能有效預測主軸係統熱特性的(de)變化規律,其冷卻器的換熱效率(lǜ)高,熱平衡時間(jiān)縮短(duǎn)了約68%,熱誤差減小(xiǎo)了約19%.本研究為精密機床主軸熱誤差控製提供了一種新思路。
關鍵詞:數控機床;主軸係統;溫度(dù)控製;熱(rè)誤差;熱-流-固模型
機床溫度變化和溫度場分布不均勻引起的熱誤(wù)差是導致精密機床加工精度降低的最主要因素在加(jiā)工中減小主軸熱誤差影響的常(cháng)用辦法有誤差(chà)補償法和(hé)溫(wēn)度控製法.Liu等研究了主軸徑向熱(rè)誤差在不同工況下的(de)變化規律,提(tí)高了(le)誤(wù)差模型(xíng)的預測精度並達(dá)到了良好的誤差補(bǔ)償效果.Liu提出了基於嶺回歸的主軸熱誤差建模方(fāng)法。
減少了熱敏感點之間共線性對熱誤差模型的長(zhǎng)期預測(cè)精度的影響.但是,補償法的補償範圍和(hé)有效性(xìng)具有一定限製,且魯棒性較差,對複雜工況的自適應性較弱.此外,熱誤差(chà)補償實(shí)施的過 程具有離散性、非均 勻(yún)性,存(cún)在溫度反饋信(xìn)號延時等問題,在通用性和穩定性方麵存在局限。溫(wēn)度控製法利用(yòng)冷卻液循環帶走主軸內部過度累積的熱量(liàng),使電主軸內部溫度分布(bù)更(gèng)均(jun1)勻,可有效降低主軸的熱(rè)誤(wù)差 .Xia等(děng)[7]基於分形理論,建立了(le)散熱器的三維熱流體動力學模(mó)型(xíng)。
分形樹形(xíng)通道淨散熱器具有壓降小、溫度場分布均勻(yún)、性能係數大等優(yōu)點.Liu等提出了差異化多回路冷卻係統和匹配功(gōng)率的散熱策略以及(jí)主動冷卻(què)液策略(luè),使主(zhǔ)軸溫(wēn)度分布(bù)更容易達到均。針(zhēn)對傳統的冷卻裝置,Grama等
提出了一種新的冷卻觸發模型(xíng),對(duì)冷壓縮機的開關頻率和開啟時間進行動態控製,可顯著減小熱變形.上述方法雖然可以有效減少主軸的(de)熱誤(wù)差,但均未考慮主軸(zhóu)達到熱平衡的速度和熱誤差的穩定性問題.為了達到最佳的溫度控(kòng)製效果,需要對在冷卻作用下的主軸的(de)熱(rè)特性進行精確仿真。
本課題組研究了金屬粗糙表麵接觸(chù)時的熱傳導和熱阻現象,並基於接觸力學建立了模擬主軸內部結構接觸的熱阻模,提高了主軸熱誤差的仿真準確性(xìng)。本(běn)文提(tí)出了一種主軸主動熱誤(wù)差控製方法,以精密數(shù)控(kòng)坐標鏜(táng)床的機械主軸為研究(jiū)對象,設計了一種由螺旋盤管冷卻器、液體泵、油液溫控(kòng)箱等(děng)組成的外(wài)置主軸溫度控(kòng)製係統;綜合考慮了螺旋 盤管-矽脂(zhī)-主軸 接觸麵間的熱傳導速率,構建了接觸熱阻數值模(mó)型。
利(lì)用有限元方法(fǎ)建立了在(zài)冷卻作用下主軸的熱-流-固耦合仿真模型。該模型可準確反(fǎn)映恒溫溫控中不同的冷卻液溫度對主軸溫(wēn)度場和熱誤差的影響,實現冷卻液控製溫度的優化,縮短主軸熱平衡時間,減小(xiǎo)熱誤(wù)差。
1、 螺旋盤管冷卻器(qì)設計
銅質的螺旋盤管冷卻器具有較高的換熱效率,塗抹一定厚度(dù)的導熱矽脂可以提高(gāo)其與主軸外殼結合麵間(jiān)的換熱效率.在(zài)螺旋(xuán)盤管外包裹(guǒ)隔(gé)熱(rè)層,以阻斷由空氣對流換熱引起的熱量傳遞。螺旋盤管內流體的流(liú)動受管壁邊界層(céng)的作用和由離心力作用(yòng)產生的二次流(渦對)影響,如圖1所示.其中,螺旋盤管單圈(quān)直徑190mm,管間距12mm,管壁厚0.8mm,內徑4.4mm,橫截麵上的(de)平均流速為(wéi)3.53m/s.由於二(èr)次流的(de)影響,當流體旋轉著通過彎管時,流線呈螺旋形。
同時管內摩擦損失增大,螺旋管(guǎn)道中(zhōng)流體從層流向紊流轉變的 臨界雷諾 數(shù)為 6500.螺旋盤(pán)管內部流(liú)體在離心力(lì)誘發下會(huì)產生由一對縱向漩渦構成的二次流,導致管(guǎn)壁上產生不(bú)均勻的對流換熱,即產生不同的局部對流換熱係數。
但在層(céng)流情形下,螺(luó)旋(xuán)盤管中的二次流可強化其管內冷卻液的傳熱(rè)效率.本文選用4號主軸油作為冷(lěng)卻液,其運動黏度為
,瞬時流量為0.1L/s,雷諾數約為 7234。
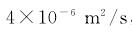
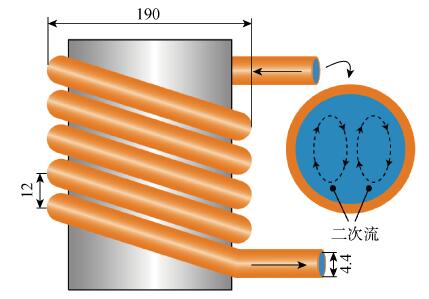
圖1 螺旋(xuán)盤管與二次流 (mm)
2、螺旋盤管-矽脂-主軸係(xì)統的(de)熱特性仿真
2.1 螺旋盤(pán)管-主軸結(jié)合麵熱阻模型
金屬固體間通過矽脂進行熱傳(chuán)遞(dì)時,熱阻主(zhǔ)要來自於矽脂,而矽(guī)脂的熱阻與其厚度(dù)呈正(zhèng)相(xiàng)關的線(xiàn)性關係.螺旋盤管(guǎn)橫截麵(miàn)近(jìn)似圓(yuán)形,如圖(tú)2所示。
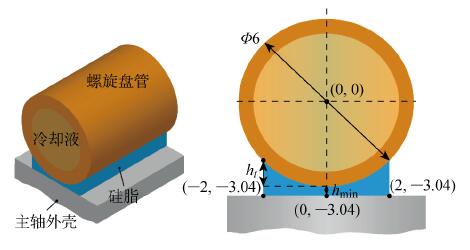
圖2 螺(luó)旋(xuán)盤管-矽脂-主軸外殼接觸處橫截麵 (mm)
在整(zhěng)個換熱麵積上塗抹的矽脂厚度約為2.5mm(經驗值),與螺旋盤管接觸的寬(kuān)度約為(wéi)4mm.其中,hmin為最小矽脂厚(hòu)度,ht為矽(guī)脂厚度.係統外殼表麵接觸區域較小,受到的法向(xiàng)力約為480N,在整(zhěng)個(gè)接觸區域內可產生平均的穩定壓力。
螺旋盤管與主軸(zhóu)外殼間的矽脂厚度 H =ht+hmin.當x=0時,ht=0,H=hmin.結合麵間的(de)矽脂厚度隨接觸(chù)麵間壓力的增大而(ér)減小,受壓狀態下,hmin值(zhí)通常在 0.01mm 數量級[15-16],遠 小於螺 旋盤管-主軸外殼結合麵間多 矽脂區域內的ht值,因此(cǐ)hmin對結(jié)合麵間的接觸熱阻影響不大,估計hmin值為0.04mm.矽脂熱導率kb=0.58 W/(m·℃),圓心距離主軸表麵3.04mm,則

式中:x 為螺旋盤管-矽(guī)脂-主軸外殼接觸處橫截麵中(zhōng)橫坐標的值.在不考慮脂-固(gù)接(jiē)觸熱阻的情況下,螺旋盤管與主軸外殼結合麵間的熱導為

式中:a=-2mm;b=2mm;L 為(wéi)螺旋盤管管長,取5.97m. 螺旋盤管與主軸外(wài)殼(ké)表麵接觸時單位麵積內的矽脂熱阻

由於螺旋盤管表麵粗糙度較小,矽脂與螺旋盤管、主軸外殼結合麵的接觸(chù)熱(rè)阻(Rc)比Rb小,對總熱阻(zǔ)的貢獻有限.參考文獻中的結果,矽脂與螺旋盤(pán)管、主軸殼體間的接(jiē)觸熱阻總和的估計值(zhí)為
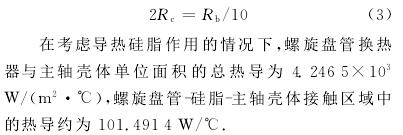
2.2 熱-流-固耦合(hé)模型建立和仿真計算
基於螺旋(xuán)盤管冷卻器和主軸(zhóu)的部件型號、結構設計、結構尺寸(cùn)以及運行(háng)工況,對內部(bù)生熱率、換熱邊界條件等進行計算.其中,軸承生熱率、主軸外表(biǎo)麵與空氣之間的對流換(huàn)熱係數、主軸內(nèi)部金屬部件結合部(bù)(如(rú)軸承與軸心以(yǐ)及(jí)主軸套之間)的接觸熱導(dǎo)等邊界條(tiáo)件的計算(suàn)采用課題組已(yǐ)有方法.利用有限元方法,對安裝螺旋盤管冷卻器的主軸進行瞬態的熱-流-固耦(ǒu)合仿 真.模 型 建(jiàn)立過程主要包括:在三維建模軟件 Creo中建立主軸三維實體模型(不包括螺栓、螺孔、凹槽、圓角和倒(dǎo)角等對主軸係(xì)統熱特性影響(xiǎng)較小的微細結構);將模(mó)型導入 ANSYS中進行網格劃分;選擇熱-流-固耦合分析單(dān)元;加(jiā)載邊界條件;求解;進行結果後處理.瞬態的熱-流-固耦合仿真結果包括各瞬態時間點(t)的盤管內冷卻液溫度分布、主軸溫度(T)場和變(biàn)形(ε)場(chǎng)。
仿真工況包(bāo)括:主軸轉速選擇(zé)精密鏜床實際加工中的典型轉速(1 000r/min),環境溫度設定為恒(héng)溫實驗室實際溫度(19℃),仿真結果如圖3所示.結果表明,冷卻(què)液溫度 為 16 ℃ 時冷卻(què)效果明顯。
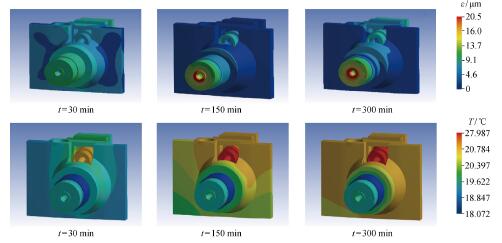
圖3 冷卻液溫度為16℃時的熱特性(xìng)仿真
3 、實驗驗證
3.1 冷卻係統設計和實驗裝置
主軸冷卻控製係統總體架構如圖4所示.係統的(de)冷(lěng)卻工質選(xuǎn)用4號主軸油,冷卻循環從(cóng)油(yóu)溫控製箱(xiāng)開始,工質經循環泵增壓(yā),經渦輪流量計和控製閥控製流量後輸出至螺旋盤管換熱器,用於主軸冷卻,最後(hòu)回流至溫(wēn)控箱(xiāng),實現循環冷卻。為了監控係統的工(gōng)作狀態,在螺旋(xuán)盤管進出口的位置設置溫度傳感器和壓力傳感器,在主軸被冷卻的位置設置溫度傳感器。
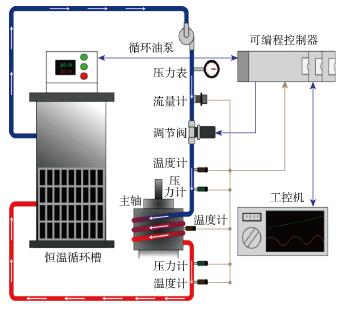
圖4 溫控係(xì)統整體設計
在精(jīng)密坐標鏜床實(shí)驗(yàn)平台上進行主軸(zhóu)的恒溫主動冷卻控製實驗,驗證溫度控製的效果.實驗在恒溫車間進行,環境溫度為 19 ℃,主 軸 恒 定 轉 速 設 為1000r/min.電渦流位移傳感器測量(liàng)主(zhǔ)軸的伸長量:溫度(dù)傳感器吸附在主軸外表麵,分別(bié)布置在主軸前端法蘭(T1),主軸殼體前端上(shàng)方(T2)和下方(T4),主(zhǔ)軸殼體前端側方(T3和(hé) T5),主(zhǔ)軸殼體後端上方(T6)和下方(T8),主軸殼體後端側方(T7和 T9),如圖5所示。

圖5 主軸特征溫度和熱誤差(chà)測量
3.2 主軸熱-流-固模型(xíng)的實驗驗證
實施溫度控(kòng)製之前需要建立準確的有限元仿真模型,並作為冷卻(què)參數選擇的依據.在(zài)冷卻液(yè)溫度分(fèn)別為20℃和16℃時,對(duì)比(bǐ)主軸的熱誤差和經模糊聚類(lèi)辨(biàn)識的熱敏感點(T2、T3、T6)溫度的瞬(shùn)態熱-流-固仿真結果與實驗測量值(zhí),如圖6所示(shì).對於20℃ 恒溫冷卻的螺旋盤管(guǎn)-主軸(zhóu)係統,實驗中 T6的溫(wēn)度在約 130min後上升趨勢 顯著減緩,在 200min後趨於平(píng)穩;T2、T3的溫度在130min左右逐漸趨(qū)於平穩.仿真中 T6的溫度在100min之(zhī)前上升趨勢明顯,在100min之(zhī)後上升(shēng)趨勢減緩並逐(zhú)漸趨於平穩.對於16℃恒溫冷卻的係統,實驗中 T2、T3的溫度在0~25min範(fàn)圍內持續下降,25min後(hòu)上升,並在(zài)150min後逐漸平穩;T6的溫度與 T2、T3的溫度同時下降,隨後上升至200min左右在逐漸平穩.主軸熱平衡時的溫(wēn)度隨冷卻液溫度的降低而(ér)有所降低。
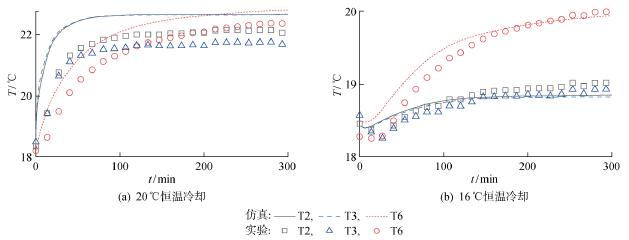
圖6 主軸溫度的仿真-實驗對照
恒溫20℃和16℃冷卻(què)時主軸熱誤差測量和仿真結果如圖(tú) 7所示(shì).熱誤差在 50min 之前快速增加,在50min之後增加速度漸緩,並在150min之後達到平穩(wěn)狀態.仿真(zhēn)得到的熱誤差大小和變(biàn)化趨勢與實驗結果吻(wěn)合。
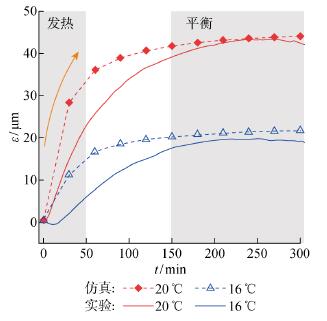
圖(tú)7 主軸熱誤差的仿(fǎng)真-實驗對照
3.3 溫控(kòng)效(xiào)果的實驗驗證
在無(wú)外加冷卻的條件下,主軸係(xì)統從靜置狀態開機,恒(héng)定轉速為 1000r/min,測試得到的溫度-熱誤差曲線如圖8所(suǒ)示.其中,變速箱由機床自帶的獨立油冷(lěng)機冷卻,控製周(zhōu)期較長,溫度波動比(bǐ)其他位置稍大.主軸最高溫度 (24.1 ℃)出現在主(zhǔ)軸中段上(shàng)方,主軸最大伸長(zhǎng)量為 53.4μm,熱平衡(héng)時間約為492min.恒溫控製的實驗結(jié)果如圖9所示。
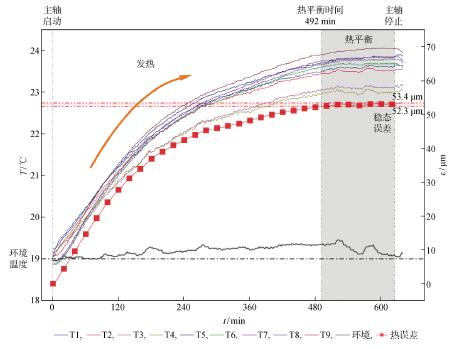
圖8 溫度(dù)-熱誤差曲線(xiàn)
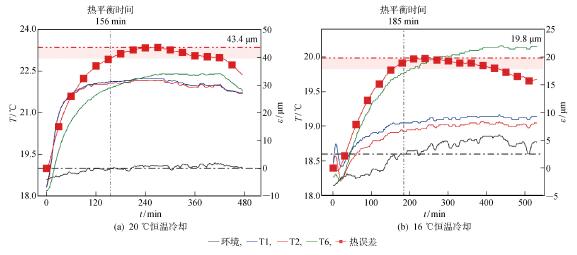
圖9 恒溫控製實驗
其中(zhōng),油箱的溫度分別設置為20℃和16℃.從圖中可知,恒溫20℃冷卻時測點的最高溫度為22.4℃,主軸的最大伸(shēn)長(zhǎng)43.4μm,熱平衡時間約為156min.與無外加冷卻的工況相比,主軸的最(zuì)大伸長量減少了(le)10μm,即熱誤差減小了約 19%;熱 平 衡 時 間(jiān) 縮 短(duǎn) 了 336min,縮短了約68%.結果表明:基於螺旋盤管的主軸(zhóu)冷卻控製方法可以縮短機床的預熱時間並有效(xiào)減小熱誤差(chà),且(qiě)控(kòng)製溫度越低,熱誤差的最大值越小.但是,降低控製溫度會(huì)延長係統達到熱平衡的時間(jiān),從而不利於精度的提高,並且(qiě)還會導致平衡時溫度(dù)穩定性下降,製冷功(gōng)率和能耗增加.在實際加工過程(chéng)中,熱誤差的穩定性比其最大值更(gèng)加重要.並且,較為穩定的熱誤差可以通過補償等方法消(xiāo)除.因此,與16℃相比,20℃是更加理想的恒(héng)溫(wēn)冷卻控製溫度。
4 、結語
本文針對精密數控機床主軸(zhóu)係統熱誤差的問題,提出了一種基(jī)於螺旋盤管(guǎn)的外置主軸熱(rè)誤差抑製方法。分析了螺旋盤管與主軸外殼接觸麵(miàn)間(jiān)的矽脂厚度對熱傳導的影響,計算得到了結合麵間的熱傳導率。通過綜合考慮(lǜ)主軸部件生熱、換熱等邊界條件,建立了螺旋盤管(guǎn)-主軸係統的瞬態熱-流-固耦合模型。
該模(mó)型能(néng)夠準確預測螺旋盤管冷卻(què)器作用下的主軸熱(rè)特性,並且(qiě)可以作(zuò)為選擇冷卻液溫度(dù)的(de)依據。理想的恒溫冷卻控製溫度為20℃,當螺旋盤管冷(lěng)卻器內冷卻液的流動狀態為層流時,冷卻器的換熱效(xiào)率(lǜ)高:與無外加冷卻工況相比,達到熱平衡的時間縮短了約68%,熱誤差減小了(le)約19%.該方(fāng)法(fǎ)成本低,效率高,無需建立(lì)熱誤差模型,具有普適性。
投(tóu)稿箱:
如果您有機床行(háng)業、企業相關新聞稿件發表,或進(jìn)行資訊合作,歡迎聯係本網編輯部, 郵箱:skjcsc@vip.sina.com
如果您有機床行(háng)業、企業相關新聞稿件發表,或進(jìn)行資訊合作,歡迎聯係本網編輯部, 郵箱:skjcsc@vip.sina.com
更多相關信息
業界視點
| 更(gèng)多
行業數據
| 更多
- 2024年(nián)11月 金屬切削機(jī)床產(chǎn)量數據
- 2024年11月 分地區金屬切削機床產(chǎn)量數據
- 2024年11月 軸承出口情況
- 2024年11月 基本型乘用車(轎車)產量數據
- 2024年11月 新能源汽車產量數據(jù)
- 2024年11月 新能源汽車銷量情況
- 2024年10月 新能源汽(qì)車產量數據
- 2024年10月(yuè) 軸承出口情況(kuàng)
- 2024年10月 分(fèn)地區金屬切(qiē)削機床產量數據
- 2024年(nián)10月 金屬切削機床(chuáng)產量數據
- 2024年9月 新能源汽車銷量情況
- 2024年8月 新能源汽車產量數據
- 2028年8月 基本型乘用(yòng)車(轎車)產量數據
博(bó)文選萃
| 更多