麵向能效的曲麵數控加(jiā)工刀具路徑優化方(fāng)法(下)
2018-10-8 來源:西南大(dà)學(xué)工程技術學(xué)院 作者: 李 麗 鄧興國 尚川博
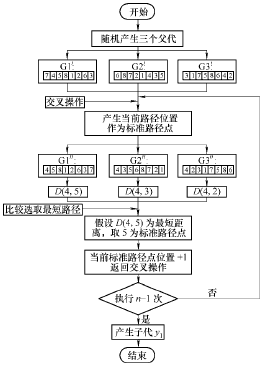
圖 4 子代(dài) y1產生過程圖
由貪心三父代算(suàn)法設計的交叉算子可得出,產生的兩個子代都較好地遺傳 3 個父代的(de)兩方向的基因,每(měi)次選擇的都是 3 個父代中最好的基因,使得後代完全繼承了父代全部優秀的基(jī)因,產生更加優秀的子代。通過(guò)對交叉算子的改進,使得尋(xún)優搜索效(xiào)率變高,同時提高了全局尋優能力,縮短了尋優時間(jiān)。
(3)自適(shì)應(yīng)模擬退火和精英混合選擇策略。 經過上述交叉變異後生成的兩個(gè)子代,但並(bìng)未直接用新生成的子代(dài)代替原有三個父代,而是在(zài)此五個中選擇最優的(de)三個(gè)作為下一輪的父代。通常遺傳算(suàn)法采用輪盤賭選擇方式,該方式(shì)在群體(tǐ)規模較小時能夠很好地選擇出優秀的個體(tǐ),群體規模一旦過大,該選擇方式無異於隨機選擇。本文利用自適應模擬退火算法與精(jīng)英混合的(de)選擇策略,過程如下所述。
(1) 計(jì)算交叉操(cāo)作的三個父代適應度分別為F(G1)、F(G2)、F(G3)。
(2) 再計算產生的兩(liǎng)個子代的適應度 F(y1)、F (y2):① 如(rú)果 F(y1)≤F(y2),則子代 y1被接(jiē)受進新種群,否則 y1以概(gài)率 exp[(−F(y1)−F(y2)/T]被接受(shòu)(T 為控製參(cān)數);② 在進化(huà)初期,T 值較大,適應度差的子代有更大的概(gài)率(lǜ)被接受,以保證前期種群的多樣(yàng)性,隨著迭代的進行(háng),T 逐漸(jiàn)減小,適(shì)應度差的個體的接受概率逐漸減低,避免破壞種群的適應(yīng)度。 (3) 為加快種群前期的收斂(liǎn)速度,算法中同時引(yǐn)入精英選擇方法,即直接將適應度最大(dà)、數量為(wéi)k 個的個體替換最小適應度和數量相同的(de)個體(tǐ)。
3.2.4 循環模式的改進
基本遺傳算法的循環(huán)模式比較單一,通過設定最大(dà)迭代次(cì)數來(lái)進行遺傳操作,當(dāng)迭(dié)代次數達到最大值即停止遺傳操作,使得收斂速度(dù)過快,容易(yì)陷入局部最優解。通過引入自適應模擬退火算(suàn)法的思想,將模擬退火算法中的溫度參數(shù)轉變為控製參數。當種(zhǒng)群收斂時,而(ér)未獲得最優解,則可(kě)進行參數調整後繼續計算,以尋求得到最優刀具路徑。過(guò)程如下(xià)所述(shù)。
參數設定:控製參數初始值 T0、控製參數初始值的(de)衰減函數 w、停止參數 Tf等。
while 1 {選擇、交叉、變異(yì)} 當前代數+1,當前控製參數 T0=T0*w 判(pàn)斷(duàn)當前種群(qún)中最好個體的適應值是否小(xiǎo)於父代種群中最好個體,如果連續(xù) 5 代小於父代種群中最好個體的適應值,則結(jié)束(shù)循環,或者(zhě)當前溫度T0<Tf也結束循環。否則,繼續交叉、變(biàn)異和選擇操作。end
4、實例(lì)及驗證
4.1 試驗條件
試驗設(shè)備:濟南第三機(jī)床公司的 JTVC650B 立式加工中心,日置 PW6001 功率分析儀來(lái)監(jiān)測機床切削過程的實時功率(lǜ)。
工件材料及加工要求(qiú):工件材料為 C6061 鋁合金棒(bàng),直徑 d=36 mm,半精加工深度 ap=0.5 mm,加工表(biǎo)麵(miàn)粗糙度 Ra不超過 6.4 μm。刀具:材(cái)料為硬質合金球頭銑刀,粗加工刀(dāo)具(jù)直徑 R=5 mm。
4.2 刀觸點優(yōu)化結果
圖 5a 為建立(lì)的曲麵模型,模型直徑 d=36 mm。圖 5b 為曲率分析(xī)圖,可(kě)得曲(qǔ)麵凹處最大法曲率 kmax = 0.36,待加工曲麵表(biǎo)麵粗糙度要求(qiú)為不(bú)超過
6.4 μm,由前麵的描述得半精(jīng)加工時球頭銑刀的半徑取(qǔ)R=2.5 mm,則由式(21)得 l=0.73 mm。按照等參數線采樣法(fǎ)對曲麵進行(háng)離散,離散結果如圖 5c 所示。最後得到合理的控製點共 2 075 個,即刀觸點數和(hé)初(chū)始種群數為 2 075 個,如圖 5d 所(suǒ)示。
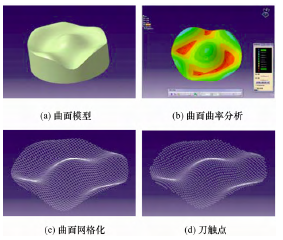
圖 5 刀觸點優化(huà)過程
4.3 刀具(jù)路徑優化結果
采用(yòng) Matlab 進行傳統遺傳算法和自適應模擬退火(huǒ)遺傳算(suàn)法的刀具路徑(jìng)尋優計算。參數設置為:基(jī)本遺傳算法(fǎ):種群大(dà)小 S=3 000,迭代次數(shù) c=450,交叉概率 Pc=0.9、Pm=0.1。改進遺傳(chuán)算法:種群規模 S=3 000,迭代次數 c=450,交叉概率 Pc1=0.95、Pc2=0.7,變異概率 Pm1=0.5、Pm2=0.2,選擇複製個數 w=50;控製參數初始值 T0=5 000,衰(shuāi)減函數k=0.95,停止參數(shù) Tf。基本(běn)遺傳(chuán)算法在計(jì)算中出現了早熟收斂的情(qíng)況,而改進遺傳迭代次數為260 次(cì),得到刀具路徑最優長度 L=1 548.52 mm。圖(tú)6 分別為改進遺傳算法的刀具路徑圖、投影圖及與計算過程收斂情況(kuàng)圖,其中圖 6a 表示經自適應模擬退火遺傳算法計算後產生的最優化刀具路徑圖,圖 6b為刀(dāo)具路徑圖在 XY 平麵上的投影圖,圖 6c 為自適應模擬退火遺傳算法計算最優(yōu)刀具路徑(jìng)的收(shōu)斂過程(chéng)圖。


圖 6 刀具路徑、投影圖以及計算過程收斂情況
4.4 仿真結果分析
曲麵模(mó)型加工的(de)切削仿真路徑在 Master CAM數控編程軟件中進行,根據(jù)本文建立的曲麵特點,選擇平行銑削、45°平行銑(xǐ)削和流線型銑削生成半精加工刀具路徑作為仿真對比,粗加工則采用相同的等高輪廓(kuò)銑削(xuē)方式,以(yǐ)最快速度去除材料,刀(dāo)具半徑為 5 mm,加工(gōng)餘量均留為 0.5 mm;本文研究的重(chóng)點在半精加工階段,半(bàn)精加工參數設置為:刀具半徑為 2.5 mm;切削用量:每齒進給量 fz=0.03 mm/z ,主軸轉速 n=3 500 r/min ,進給量 f=400 mm/min。
根據本文提出的刀具路徑(jìng)生成方法,並通過Matlab 求解得到了最優刀具路徑,並在 Master CAM數(shù)控編程軟件中通過設置相應加工參數,仿真模擬得到了如圖 7 所示(shì)生成的不同刀具路徑。表 1 為對應刀具路徑下仿真模擬得(dé)到的刀具(jù)路徑長(zhǎng)度以及切削時間。
從圖 7 可(kě)看出,在保證加工質(zhì)量的前(qián)提下,本文提出的算法生成的曲麵加(jiā)工刀具路徑規劃完全可(kě)行且連續性非常好,相對目前常用(yòng)的路(lù)徑生成方法而言,超(chāo)出工件加工麵(miàn)的空切行程(chéng)路徑較少。
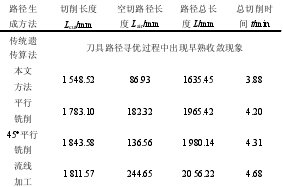
表 1 各方法(fǎ)生成的刀具路徑比較
由表 1 得出,本文方法生成的刀具路徑無(wú)論是切削長度還是空切路徑長度都有明顯的優勢。切削長度最大優化距離(lí)為 295.06 mm,相對減少 16.00%,最(zuì)短(duǎn)優化距離為 234.58 mm,相對減少 13.16%;路(lù)徑總長度方麵,可看出本(běn)文方法計算出的刀具(jù)路徑優勢更加明顯,刀具路徑總長度最大優化長度達到(dào)420.77 mm,相對減少 20.46%,最短優化長度為329.97 mm,相對減少 16.79%;
從表 1 數據可知,當其他參數一定時,刀具路徑的長度直接決定了機床的加工效率,刀(dāo)具路徑(jìng)的優化影響著總切削時間,刀具路徑長度減少,使得總切削(xuē)時間變短,進(jìn)而提高加工效率,驗證了麵向刀具路(lù)徑優化的加工效率函(hán)數的正確性。
4.5 試(shì)驗驗證
將構建的曲麵模型與生成的刀具路徑在其他外部(bù)環境以(yǐ)及切削參數設置相同(tóng)條件下進行實際加工,且每種不同的加工方式分(fèn)別進行(háng)了 5 次試驗,並記錄每次加工過程(chéng)中的功率消耗值,取平均值(zhí)作為最後的能耗(hào)值,模型曲麵加工試驗結果如圖(tú) 8 所(suǒ)示,每(měi)種(zhǒng)加工方法的實測 Pcut和 Pair功率值分別(bié)如表 2 和表 3 所(suǒ)示。
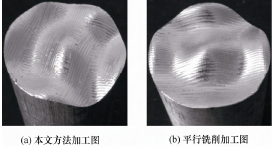
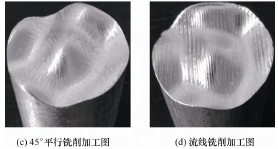
圖 8 實際加工結果
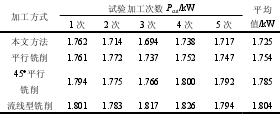
表 2 各路(lù)徑實際加工實測切削功率 Pcut
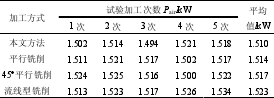
表 3 各路徑實際加(jiā)工(gōng)實測空切功率 Pair
由(yóu)表 2、3 可看出,在進行實際加工時,本文提(tí)出的(de)路徑優(yōu)化算法生(shēng)成的刀具路徑,機床消耗的功率較少。又因刀(dāo)具(jù)路徑長度的減少,使得加工時間變短,從而整個加工能耗最小,表 4 為各路徑加工方式下的(de)能耗值大小,從表中得出運用該刀具路徑優化(huà)方法進行零件加工時,機床所消(xiāo)耗的能耗相(xiàng)對於(yú)其他加工(gōng)方法最低減少了 8.94%,最高減少(shǎo)了20.57%。進而驗證了麵向刀具路徑優化的機床(chuáng)能耗函數的正確性。
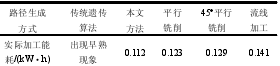
表 4 各路徑加工機床能耗對比
5、結論
(1) 分析了刀具路徑對(duì)加工效率(lǜ)和刀(dāo)具路徑對機床能耗間的映射關係,建立了以(yǐ)機床能耗和加工效率為目標,以機床主軸(zhóu)轉速、進(jìn)給量(liàng)、最大切削功率、最大切削力、加工行距等為約束的刀(dāo)具路(lù)徑優化數學模型。
(2) 提出了一種刀觸點(diǎn)優化方法,該方法根據(jù)進刀方向法曲率半徑、刀具半徑以及曲麵加工後殘留高度,把待加工的曲(qǔ)麵進行(háng)自適應離散,從而得到曲麵控製點,以各個(gè)控製點作(zuò)為刀具加工路(lù)徑的刀觸點(diǎn)。
(3) 提出了一種自(zì)適應模擬退火(huǒ)遺傳算法進行刀具路徑刀觸點連接順(shùn)序(xù)及方式優化方法,該方法引入模擬退火算法、貪心算法對(duì)遺傳算子進行了改進,提高了算法在進行大量曲麵控(kòng)製點計算尋求(qiú)最優路徑時種群進化速度,避(bì)免陷入局部最優解,加(jiā)快了(le)運算速度。 但是由於數控加工方式種類多,本文主要針對曲麵模型半精加工單工序為高效低耗刀具路徑優化研究,而(ér)實際曲麵零件加工是一個(gè)多工(gōng)序、多(duō)加工方式的過程,且同一個曲麵(miàn)零件加工可以由多條工藝路線完成(chéng),因此,從曲麵零件(jiàn)多工序(xù)、多工藝路線上進行刀(dāo)具(jù)路徑優化,進而降低機床能耗將(jiāng)是以後研究的重點。
投稿箱:
如果您有機床行業、企業相關新聞稿件發表,或進行資訊合作,歡迎聯(lián)係本(běn)網編輯部, 郵箱:skjcsc@vip.sina.com
如果您有機床行業、企業相關新聞稿件發表,或進行資訊合作,歡迎聯(lián)係本(běn)網編輯部, 郵箱:skjcsc@vip.sina.com
更多相關信息
業界視(shì)點(diǎn)
| 更(gèng)多
行業數據
| 更多
- 2024年11月 金(jīn)屬切削機床(chuáng)產量數據
- 2024年11月 分地區(qū)金屬切削機床產量數據(jù)
- 2024年11月 軸承出口情況
- 2024年11月 基本型乘用車(轎車)產量(liàng)數據
- 2024年11月 新能源汽車產量數據(jù)
- 2024年11月 新能源汽車銷量情況
- 2024年10月 新能(néng)源汽車(chē)產量數據
- 2024年10月 軸承出口情況
- 2024年10月 分地區金屬切削機床產量(liàng)數據
- 2024年10月 金屬切削機床(chuáng)產量數據
- 2024年9月 新能源汽(qì)車銷量情況
- 2024年(nián)8月 新能源汽車產量(liàng)數據
- 2028年8月 基本型乘用(yòng)車(轎車)產量(liàng)數據(jù)
博文選萃
| 更多