利用車(chē)床(chuáng)鑽削小孔的(de)工藝研(yán)究
2021-11-16 來源: 中國空空導彈研(yán)究院 作者:翟(zhái)建偉
摘要:以實際加工案例為基礎,對車削加工中鑽削 準1.5 mm 小孔的加工(gōng)工藝進行分析,找出(chū)鑽削過程中影響(xiǎng)加工質量和加工效率的主要因(yīn)素,並根據案例中的加工經驗,提出(chū)了一種(zhǒng)對鑽頭改(gǎi)進的方法,為小孔加工提供了解(jiě)決方案,同時(shí)也為其他小孔加工提供參考。
關鍵(jiàn)詞(cí):機械加工;車削;小孔(kǒng)
0 前言
在航空產品中,結構重量是衡量產品性能的一個非常重要的指標。為了提高產品的指標,設計人員在設計產品時,在滿足其他性能指標的前提下,會盡可能的壓縮結構尺寸以追求更輕的產品。壓縮結構(gòu)尺寸可以有效地減輕結構重量,但帶來的問題就是產品零件(jiàn)變小,更小的零件意味著零件上各種特征的尺寸也會變得更小,對於傳統機(jī)械加工來說,尺寸過大或過小(xiǎo)的零件特(tè)征都是加工中的難點(diǎn)。
在零件的各種特征中,孔是較難加工的一種。由於孔本身的特殊結構(gòu),在加工中存在排(pái)屑不暢、冷卻潤滑不及時等各種問題,容易在加工中出現孔內壁糙度差(chà)、孔軸線直線度差、孔橫截麵圓度差、孔直徑尺寸精(jīng)度差,孔定位尺寸精(jīng)度(dù)差等各種問題,常常成為零件質量問(wèn)題的高發點,尤其是對於長徑比比較大的孔,加工難(nán)度較一般孔(kǒng)更大。
由(yóu)於產品的各種限製,實際設計出的零件往往是上(shàng)麵兩種加工難點的疊加,即長徑比大的小孔。當前,國內(nèi)外已經發展出了很多新的加工方法可(kě)以完成(chéng)此類(lèi)小孔的加工,如激光、電腐蝕、高能粒子束等加工方法,均可以比(bǐ)該孔直徑更小、長徑比更大的孔的(de)加工。但這些加工方(fāng)法均存在加工效率(lǜ)低和加工成本高的問題,傳統的機械加工雖然沒有新方法的(de)加(jiā)工能力強,無法完成許多有極端(duān)要求的特征的加工,但在加工成本和加(jiā)工效率方麵相(xiàng)比較於這些新方法卻占有很大的優勢。因此如果可以發掘傳統機械加工的潛力,拓(tuò)展傳統機械加工的適用範圍,就可以完(wán)成一些要求比較苛刻(kè)的零件的加工,為零件生產降低加工成本和提高加工效率提供了有效的解決方法。
車削加工是一種傳統的機械(xiè)加工方法,其最大的優點就是加工回轉體時圓度特別好,因此很適合加工孔(kǒng)或(huò)軸等回轉體特征。本文以實際加工案例為範例,討論了如何使用車削加工完成長(zhǎng)徑比為 12.3的 準1.5 mm 小孔的加工(gōng),並據此探討在加工大長徑比的小(xiǎo)孔(kǒng)時(shí)需注意的事項以及可采用的(de)一些方法。
1、加工難點分析
零(líng)件結構示意圖如圖 1 所示。
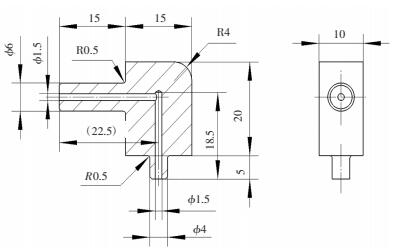
圖 1 零件結構示意圖
從圖 1 中可以看出,該零件為接頭類零件,中間有貫穿孔用於工作時介質流(liú)動。由(yóu)於零件尺(chǐ)寸很小,因此零件上各特(tè)征的結(jié)構尺寸也(yě)很小。零件材料為17-4PH,材(cái)料出廠時進行過熱處理,材料硬度在HRC40 左右。由(yóu)於該零件從(cóng)結構上並不是回轉體(tǐ),適合在數控銑床上進行(háng)加工,因此主要特征均是(shì)在數控銑床上完成的加工。但由於兩個孔的(de)加工難度較大,數控銑床(chuáng)的無(wú)法滿足加工要求,因此孔的加工選擇在數控車床上完成。而(ér)零件的裝夾則是通過設計專用鑲嵌式夾具來完成(chéng)裝夾(關於夾(jiá)具的設計這裏就(jiù)不在詳細說明)。
所需加工孔孔直徑均為 準(zhǔn)1.5 mm,其中一個較淺的孔深度為 18.5 mm,長徑比為 12.3;另外一個孔要求和這個孔(kǒng)貫穿,因此深度至少要達到 22.5 mm,即長徑比至少為 15。
長徑比值大的孔在加工時可以(yǐ)選(xuǎn)擇從兩端向中間對(duì)向加工以變相的減小孔的(de)長(zhǎng)徑比值。但這個零(líng)件上的孔是盲孔,因此加工時必須從孔口加工,這就對加工(gōng)工藝提出了較高的要求,在麵對(duì)批量生產的情況時,使用普通的加工(gōng)工藝無法完成零件(jiàn)的穩定加(jiā)工,需要對加工工藝進行改進。
1.1 排屑問題
排屑是機械加工中的一個重要問題,及時排出切屑,可以(yǐ)方便刀具繼續(xù)對零件材料(liào)進行切削,提高加工效率。機械加工行業經過長期發展,絕大部分(fèn)加工過程,如車、銑、刨等,無論是刀具的排屑槽,還(hái)是機床斷屑器,加工(gōng)過程中(zhōng)都有了比較完善的排屑措(cuò)施,日常加工中(zhōng)基本可以不用單(dān)獨考慮排屑的問題。但(dàn)在此次孔的加工過(guò)程中(zhōng),排屑不暢的問題非常嚴重。主要原因是鑽孔加工與其他加工,如和車削外圓(yuán)相比最大的不同,就是孔的(de)直徑限製了刀(dāo)具的尺寸。對於該孔的(de)加工,使用鑽頭的直徑隻能選擇準1.5 mm。鑽頭直徑限製了鑽頭上(shàng)的排屑槽(cáo)深度很小,再加(jiā)上鑽頭鑽孔過(guò)程中鑽頭和(hé)孔內壁(bì)緊密貼合,鑽(zuàn)進(jìn)過程中產生的切屑必須完全(quán)依靠排屑槽排(pái)出,如果孔內的切屑不能及時排出,不僅影響鑽進效率,嚴重時還(hái)會發生孔內事故。主要是因為由於鑽頭直徑太小,導致鑽頭的強度小、剛性差,加工過程中產生的切屑如果不能及時排出,切屑(xiè)夾在鑽頭(tóu)和零件之間,會對鑽頭產生(shēng)擠壓,由於鑽(zuàn)頭剛性差的原因,稍微對鑽頭產生的擠壓就會造成鑽頭折斷,輕則造成鑽頭報廢,重則會使斷掉的鑽頭與零件“咬死”而造成零件報廢。
機械加工過程中,切削液的衝洗對排屑也起了非常(cháng)大的用處。但在該加工過程中,切削液也無法有效衝(chōng)洗(xǐ)到加工麵。該情況將在 1.2 切削熱問題部分進行詳述。
1.2 切削熱問題
機械(xiè)加工過(guò)程中,切削液的衝洗有兩個作用,一(yī)是對加工刀具和材料進行降溫,二是衝走加工後產生的切屑。一般條(tiáo)件下,機械加(jiā)工(gōng)過程中會使用盡可能大流量的切削液對加工部位進行直接衝洗(xǐ),但在該零件加工鑽孔過程中,切削液無法有效衝洗到加工部位。主要原因是因為孔的(de)直徑很小,鑽頭(tóu)直徑也很小,該尺寸的鑽頭沒有中央出水的類(lèi)型(xíng),而在加工(gōng)過程中鑽頭緊密貼合孔內壁,因此切削液要進入加工部位必須通(tōng)過排屑槽進入。但(dàn)由於鑽頭直徑太小,鑽(zuàn)頭上的排屑槽深度也很淺,導致冷(lěng)卻液很難進入小孔內部,無(wú)法實時(shí)對切削刃(rèn)進行冷卻,容易造成切削刃升溫過快造成鑽頭刀刃磨損甚至燒毀鑽頭。
1.3 鑽頭強度問題
鑽(zuàn)頭的結構為細長型,長徑比很大,所以鑽頭的強(qiáng)度一般都不高,並且(qiě)在實際使用過程中強度會(huì)隨著刀具伸出長度的增加而(ér)進一步下降,鑽削加工又屬於切削力較大的加工方式,所以在加工前選(xuǎn)擇鑽(zuàn)頭時要特別注意鑽頭(tóu)強(qiáng)度是否(fǒu)能夠滿足加工要求。
鑽頭的強度和鑽頭的(de)直徑正相關,小鑽(zuàn)頭直徑小,並(bìng)且(qiě)鑽頭(tóu)上還有排屑槽,會使鑽頭的強度進一(yī)步降低,使鑽頭在加工過程(chéng)中無法承受較大的切削力或其他衝(chōng)擊(jī)力,如果使用不當,比如鑽孔過程中(zhōng)進給速度過快,很容易在加工過程中發生鑽頭折斷的情況。
1.4 精度問題
在(zài)車(chē)床上鑽(zuàn)削小(xiǎo)孔的過程中,零件軸線和(hé)鑽頭軸線的同軸度對加工的影響(xiǎng)很大,如果(guǒ)因為精度的原因,造成零件軸(zhóu)線和鑽頭軸線不在同(tóng)一條線(xiàn)上,加工過程中鑽頭會承受很大的徑向力,尤其是鑽頭剛(gāng)鑽入時,此時不同軸會造成鑽頭接觸零件不均勻,會(huì)給(gěi)鑽頭施加很大的徑(jìng)向力,而此時鑽頭懸空長度是最長的(de),也就意味著此時鑽頭的結構強度(dù)是最弱的,這(zhè)也(yě)成為鑽孔時鑽頭折斷的高發點。
2、 改進方法與措施(shī)
2.1 多退刀,勤排屑
切屑(xiè)對加工過程影響很大,由(yóu)於(yú)鑽頭直徑(jìng)小(xiǎo),鑽頭上的排屑槽也很淺,排(pái)屑能力弱,如果光靠排屑槽進行排屑無法滿(mǎn)足穩定加工(gōng)的要求,加工過程中必(bì)須通過退刀的方式(shì),使鑽頭完全退出孔以徹底排出切屑。數控車床(chuáng)可(kě)以(yǐ)通過編製數控加工程序對加工過程進行精確控製,以(yǐ)哈挺(tǐng)數控車床為例(數控係統(tǒng)為 FANUC),控製係統中內置了一種點鑽的加工方式用以解決此問題。該程序語(yǔ)句為:G1101 W()F()Q()P()B()L(),在鑽孔程序中使用該語句進(jìn)行加工,機床就可(kě)以每次步進一定深度(dù)後自動退出刀具進行排屑[1]。
需要注意的是,由於刀具排屑槽排屑能力弱,切屑(xiè)很難在產生的同時被同步排出(chū)孔外,實(shí)際過程是切削產生(shēng)的切屑被儲存在鑽頭前段的排屑槽內,等鑽頭退出孔時再完全排出孔外。由於排(pái)屑槽儲存切(qiē)屑能力有限,所以每次步進的深度不能過深,否則產(chǎn)生的切屑過多,排屑槽無法儲存,多餘(yú)的切屑就會堆積(jī)在孔底或孔壁處(chù),對(duì)加工過程造(zào)成影響,退刀排屑的意義就失去(qù)了(le)。但步進深度也不宜過小,否(fǒu)則進退刀次數過多,會嚴重降低加工效率,從加(jiā)工經驗得到的參考值每次(cì)步進深度均保持在 0.5 mm 左右為宜,鑽孔時進給速度也不易過快(kuài),但可提高退刀的進給速(sù)度以保證整體加工效率。
2.2 改造鑽頭,增強強(qiáng)度
在批量加工零(líng)件的過程中,單純采(cǎi)取退刀的措施並不能完全解決鑽頭折斷(duàn)的問題,為保證鑽頭的強(qiáng)度(dù),此次加工(gōng)過程(chéng)中在普通鑽頭(tóu)結構的基礎上進行了修(xiū)改,製作了專用鑽頭用於孔的(de)加工。改進後的鑽頭結構示意圖如圖 2 所示。
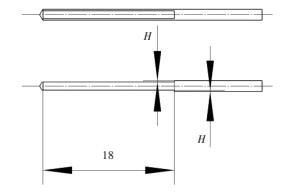
圖 2 鑽(zuàn)頭結構示意圖
鑽頭製(zhì)造(zào)原(yuán)料的選擇上可以選用與孔直徑(jìng)一樣的高速鋼或硬(yìng)質合金棒,在(zài)需(xū)要鑽孔的深度範圍內將鑽(zuàn)頭磨扁,一般 H 值(zhí)可選擇在 0.1 ~ 0.2 mm 之間(jiān),這樣的結構(gòu)取消了排屑槽,極大地增強了鑽頭的(de)強度,同時磨扁的部分也可以兼顧排屑的功能,前端切削刃的刃磨與普通鑽頭保(bǎo)持相同結構(gòu)即可。經實際加工測試(shì),按此方法改進(jìn)製(zhì)作的鑽頭比普通商(shāng)用(yòng)鑽頭強度更(gèng)高(gāo),在相同的切削參數、排屑(xiè)情況和冷卻(què)條件下(xià),不但加工出的零(líng)件質量更好,而且能避免折斷鑽頭,保證(zhèng)了整批零件(jiàn)加工的順利進行,提高了整批零件的加工效率。
從(cóng)改製鑽頭的結構示(shì)意圖上看,鑽頭應該隻滿足深度 18.5 mm 孔(kǒng)的加工需求,加工另一個(gè)孔則麵臨長度(dù)不足的問題。需要強調的是,零件中貫穿(chuān)的兩個孔,在(zài)加工順序上必(bì)須嚴格分先(xiān)後,深度為18.5mm 的孔先加(jiā)工,然後再加(jiā)工另一個孔。這是(shì)由於(yú)兩孔相互貫穿,在加工第二個孔時,很難保證孔的軸線(xiàn)和第一個孔軸線相交,因此鑽頭在鑽破第一個孔時有可能存在鑽頭受力(lì)不均(jun1)衡(héng)問題而導致鑽頭折斷。為避免該(gāi)問題,在加工時鑽頭僅鑽入 19 mm 就不再繼續鑽進,最後的 3 mm 改用 1.5 mm 銑刀進行加工,即將 1.5 mm 銑刀裝夾在刀盤上,利用銑刀完(wán)成最後兩孔鑽透的加工過程,由於銑刀強度較高且銑刀側齒可用於切削,因此可有效避免折斷情況的發生。
2.3 檢查中心軸線是否重合
該零件加工時,零件是通(tōng)過夾具裝夾在機床卡盤上,而刀具裝夾(jiá)在機床(chuáng)刀盤上,機床(chuáng)本(běn)身、夾具(jù)、裝夾過程(chéng)都會存在誤差,這些誤差累計起來會造成零件與(yǔ)刀具的裝夾誤差,這(zhè)誤差會對零件加工造(zào)成影響,因此加工(gōng)前(qián)必(bì)須檢查校正。
檢查(chá)裝夾(jiá)精度時,必須檢查在(zài)零件和鑽頭裝(zhuāng)夾好的情況下,鑽頭(tóu)軸(zhóu)線(xiàn)和零件軸線是否重合,本次加(jiā)工過程中使用的是一種比較簡單的檢查方法[2]:第一步用磁吸式固定器將千分表(biǎo)固定在機床刀盤上,千分表表頭接觸零件外圓表麵,然後沿機床 X 軸方向前後移動刀盤,觀察千分表(biǎo)數(shù)值變化,要(yào)求要將零件調整到千分(fèn)表數值變化不超過 0.02 mm,這樣的檢測要在零件圓周上選擇(zé)均布的(de)三條(tiáo)線進行測量,三條線的測(cè)試都合格才算合格。第二(èr)步,使千分表表頭接觸(chù)零件外圓,用手搬動機(jī)床主軸(zhóu),使零件按機床 A 軸(zhóu)
旋轉(zhuǎn),觀察旋轉過程中千分表數值變化,同第一步一樣(yàng),變化範圍不超(chāo)過 0.02 mm 才算合格。如果發現誤差過大,則(zé)需要進行調整校正,調整的循(xún)序按照難易程度安排,先零件、再夾具、最後機床;如果對零件和夾具(jù)的調整(zhěng)都無法(fǎ)修正誤差,而在對機床進行調整後依然無法達到加(jiā)工要求,則說(shuō)明機床精度以無法滿足加工要求,必須更(gèng)換(huàn)機床進(jìn)行加(jiā)工,否則將(jiāng)無法保證加工效果。
3、加工結果驗證
通過數據(jù)對比來驗證了(le)改進方法(fǎ)和措施的有效性,改進前後兩種工藝(yì)方案的(de)加工結果如表 1 所示。
表(biǎo) 1 加工結果對照表
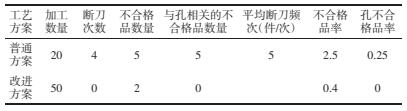
從表 1 的(de)數據可以得到質量(liàng)對比的折線圖(tú)如圖3 所示。
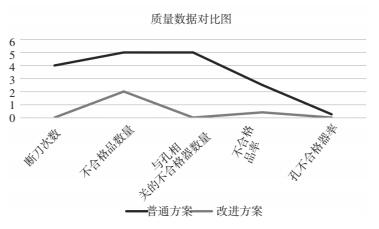
圖 3 質量數(shù)據對比(bǐ)圖
從圖(tú) 3 中可(kě)以很清晰地看出,雖(suī)然沒有定量的計算,但改進後的工藝方案的有效性還是非(fēi)常(cháng)明顯的,零件質量有(yǒu)非常大的改善,證明了改進方法和措施解決了孔加工過程中存在的問題。
4、 結束語
本文(wén)提出了一種對鑽頭改進(jìn)利用車床鑽削小孔方法,為小孔加工(gōng)提供了解決方案。對類似的小孔加(jiā)工本文中的工藝方案可以借鑒,但需要根據具體的情況不同采取的對應措施,不能照搬,但在製定工藝方案時,一些共同點必須要考慮:
(1)要加強退刀排屑,不能簡單依靠鑽頭的排屑槽排屑;
(2)商用鑽頭不一定滿足所有加工工(gōng)藝方案的要求,要根據具體情況(kuàng)考慮自製鑽頭;
(3)要對零件裝夾後(hòu)的位置精度進行測量並調整,否則會(huì)影響零件的加工(gōng)。
投稿箱:
如果您有機床行業、企業相關新(xīn)聞稿件(jiàn)發表,或進行資訊合作,歡迎聯係本網編輯部, 郵箱:skjcsc@vip.sina.com
如果您有機床行業、企業相關新(xīn)聞稿件(jiàn)發表,或進行資訊合作,歡迎聯係本網編輯部, 郵箱:skjcsc@vip.sina.com
更多相關信息
業界視點
| 更多
行業數(shù)據
| 更多
- 2024年11月 金屬(shǔ)切削機床產量數據
- 2024年11月 分地區金屬(shǔ)切削機(jī)床產量數據
- 2024年11月 軸承出口情況(kuàng)
- 2024年11月 基本型乘用車(轎車)產量數(shù)據
- 2024年(nián)11月 新能源汽車產量數據(jù)
- 2024年11月(yuè) 新能源汽車銷量情況
- 2024年10月 新能源汽(qì)車產量數據
- 2024年10月 軸(zhóu)承出(chū)口情況
- 2024年10月 分地區金屬切削機床產量數據
- 2024年10月 金屬切削機床產量數據
- 2024年9月 新能源汽車銷量情況
- 2024年8月 新能源汽車產量數據(jù)
- 2028年8月 基本(běn)型乘用車(轎車)產量(liàng)數據