發動機動(dòng)、靜葉片激光電(diàn)火花複合製孔加工工藝技術研究
2017-2-9 來源:中航工業西安航空(kōng)發動機(集(jí)團)有限公(gōng)司 作者:陳(chén)陽,朱紅鋼,王增坤,王輝明,石銀喜(xǐ)
摘要:激光、電火(huǒ)花製孔這兩種加工(gōng)方法有一個共同的、主要(yào)的應用範圍,即可經濟而高效地對(duì)複雜的身體形狀作精細加工,且可應用於難加工(gōng)材料,已成為航空工業一種不可取代的加工工藝新方法。由於這兩種加工方法有非凡的加工能力和互補優勢,當今已穩定地用在現代航空製造業中。
關(guān)鍵詞:激光製孔;電(diàn)火花(huā)製孔;複合(hé)加工工藝;動靜葉片
在航空發動機中,各類型的動靜葉片在氣(qì)膜孔加工(gōng)中,由於葉片鑄造型麵(miàn)不一致、加工工(gōng)藝欠優化、可達性差等問題,存在氣膜孔位置、孔徑超差、連孔等諸多質量問題(tí),造成(chéng)激光、電火花都無法單(dān)工(gōng)藝實現(xiàn)本工序加工。且(qiě)各自工藝的短板,成(chéng)為影響發動機(jī)片(piàn)動靜葉片質量的瓶頸及交付。通過優化工藝及加工參數, 同時采用激光、電火花複合加工的方(fāng)式, 對加工工序進行合理調配,對零件型麵進行探測研究,減少零件型麵(miàn)誤差對加工的影響。
1.激光、電火花打孔(kǒng)的優缺點
1.1 激光(guāng)打孔(kǒng)
激(jī)光打孔的缺點:被加工(gōng)孔的(de)精(jīng)度和表麵粗糙度尚不夠(gòu)理想。激光打孔的優點有:
(1)激光不僅能對置於空氣中的工件打孔,而且也能對置(zhì)於真(zhēn)空中或其他前提下的(de)工件進(jìn)行打孔。
(2)因為加工過程(chéng)與工件不接觸,故加工出(chū)的工件清潔。因為加工時間短,故對被加工的材料氧化、變形、熱影響區域均較小,不(bú)需特殊保護(hù)。
(3)可加工各種材料的(de)微(wēi)孔。一般機械鑽頭隻能鑽(zuàn)出直徑大於250 μm 的孔, 而激光則能加工出10 μm 以下的孔。就加工種(zhǒng)類來看,不僅可對(duì)金屬而且可對非金屬甚至橡膠等進行鑽(zuàn)孔。從深徑比來看,用激光打出的孔,其深度與孔徑之比,可高達50以上,這是(shì)用其他加工(gōng)方(fāng)法難以達到的。如用一般方法在極(jí)硬的氧化鋁陶瓷上加(jiā)工小(xiǎo)孔所得到的深徑比為2,超聲波法隻有4,而激光可達25。
1.2 電火花打孔的優缺點
電火花打孔的優點有:
(1)加工孔徑範圍一般在0.3~3 mm 之間(jiān),深(shēn)徑比能達(dá)200∶1 以上。這(zhè)是其相比於其他工藝非常重(chóng)要的一個優點,即對小徑深孔(kǒng)的加工。由於高速(sù)電火花小孔加工技術使(shǐ)用水基工作液作為加工介質,因其電導率大,在極間(jiān)電壓作用下會產生(shēng)介電係數與水不同的氫氣,從而導致放電間(jiān)隙增大,增加擊穿延時,提高效率。另外,由於在加工過程中,脈衝間隔很(hěn)小,使脈衝頻(pín)率大大增加,脈衝電(diàn)源(yuán)的有(yǒu)效利用率大大增加,進一步提高了效率,獲得了高效的生產率。
(2)加工速度(dù)一般能達(dá)20~60 mm/min,且(qiě)加工深度對其影響相對不大,是電火花加工第一次在速度上能與機(jī)械加工相比擬。與常規電火花小孔加工技術相比, 由於水(shuǐ)基工作液(yè)高速地流過工作間(jiān)隙,將(jiāng)放電間隙中的蝕除物迅速排出間隙,並有良好的(de)冷(lěng)卻性(xìng)能,因而(ér)整個過程速度快,消(xiāo)電離(lí)過程快,精度(dù)高。
(3)直(zhí)接從斜麵、曲(qǔ)麵(miàn)穿入,加工盲孔、深孔、斜孔及異形孔(kǒng)等。
(4)不受材料的硬度及韌性限製,除了能(néng)加工一(yī)般的(de)導電材料以外,還能順利加工不鏽(xiù)鋼、淬火鋼、硬質合金、欽合金、淬鋼等難加工材料。而普通加工方法手材料還有刀具的硬度和韌(rèn)性限製較大。
(5)加工孔的尺寸一(yī)致性,一般能在0.03~0.05mm 之間,圓度在0.02~0.03 mm 之間,表(biǎo)麵粗糙度Ra3.5 μm 左右,能滿足一定的垂直度要求。電火花打孔的(de)缺點有:
(1)放(fàng)電間隙狹窄。電火花放(fàng)電加工中工具電極與工件間(jiān)的絕緣工作介質(zhì)有一定的介電常數,放電加工時有一定的擊穿間隙(xì)(放電間隙),因此放電加(jiā)工後工(gōng)件的尺(chǐ)寸與工具電極的尺寸並不完全一致。且放電間隙是隨(suí)電參數、電極(jí)材料、工(gōng)作液等因素的變化而變化的,從而影響(xiǎng)了加工精(jīng)度。間隙越大,則複製(zhì)精度越(yuè)差,特別是對複雜形狀的加工表麵。如電極為尖角時,而由於放電間隙(xì)的等距離,工件則(zé)為圓角。因此,為了減少加工尺寸誤差,應采用較(jiào)弱小(xiǎo)的加(jiā)工規準(zhǔn),縮小放電間隙(xì),另(lìng)外還必須盡可能使加(jiā)工(gōng)過程穩定。
(2)易出現加工錐度和圓角。由於工具電極(jí)下麵部分加工時間長、損耗大,因此電極變小,而入口處由於電(diàn)蝕(shí)產物的存在,易發生因電蝕產物的介入而再次進行的非正(zhèng)常放電(diàn)(即“二次放電”),因而產生加(jiā)工斜度。這就要求高壓水質工作液必須有一定的速度,且持續工作。
(3)工具電極損耗嚴重。電火花加工是(shì)靠(kào)高溫熔化氣化金屬實(shí)現對工件的加工,工具電極必須是(shì)導電金屬用來傳導電能,所以(yǐ)在高溫和帶電粒(lì)子的(de)撞擊(jī)作用下工具電極也存在損耗,特別是在電參數選擇不當的情況下,電極的損耗更加明(míng)顯。
2.實驗過(guò)程及加工工(gōng)藝方法
2.1 激光加工實例
某機的高壓(yā)渦(wō)輪導向葉片加工組合件需加工排氣邊1 排(8-φ0.7+0.1 0),進氣邊(biān)3 排(25- φ0.4+0.1 0)共4 排33 個氣膜孔(圖1)。
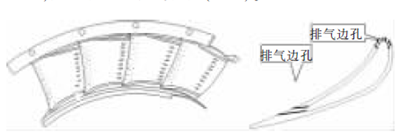
圖(tú)1 高壓渦輪導向(xiàng)葉片加工組合件氣膜孔分布示意圖
以前工藝方(fāng)案為電火花加工,效(xiào)率(lǜ)低。零件為鑄件,鑄件型(xíng)麵公(gōng)差(chà)大,葉片型麵一致性差,孔位置度難以保證。按照要(yào)求(qiú)的葉片型麵(miàn)線輪廓度為0.2mm,由於逐漸的(de)加工難度較大(dà),隻能保證葉片型麵在0.4 mm 左右,嚴重影(yǐng)響了氣膜孔加工的位置(zhì)度。通過對現有工藝分析,進氣邊3 排孔中,兩排氣膜孔壁薄,孔出口(kǒu)距型(xíng)腔(qiāng)內壁較遠,可塞保護材料進行有(yǒu)效保護,故改為激光加工,因激光加工無法有(yǒu)效控製(zhì)加工深度, 另一排距(jù)型腔內壁很近,無法(fǎ)添加保護材料(liào),存在擊傷內(nèi)壁(bì)的隱患(huàn),所以(yǐ)這排仍采用電火花加工。排氣邊孔為型腔內角度(dù)斜孔,加工(gōng)深度大(dà),加工空間(jiān)狹小,無法采用激光加工,故仍(réng)采用電(diàn)火花加(jiā)工。通過加工工藝的改進(圖(tú)2),由以(yǐ)前的電火花加工優化為激(jī)光-電火花複合加工,從而使加工效率得到(dào)很大提(tí)高。
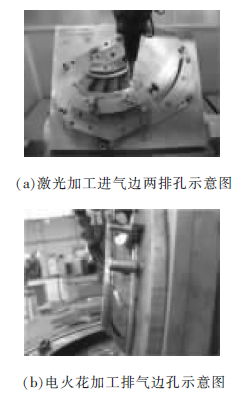
圖2 激光(guāng)-電火花(huā)複合加工示意圖
存在問題:
(1)零件型麵對加工的影響。零件為鑄件,型麵公(gōng)差大且一致性差,加工中需根據零件型(xíng)麵調整孔位,加工效率低。型麵公(gōng)差大還影響到加工深度,4排孔的出口(kǒu)都(dōu)在狹小的型腔內,空(kōng)間小(圖(tú)3),加工中存在擊傷內腔的隱患。加(jiā)工時無法(fǎ)設定一個(gè)固定的加工(gōng)深度, 隻能根據(jù)加工情況手動(dòng)調整加工深(shēn)度,以保證孔徑,避免擊傷零件。
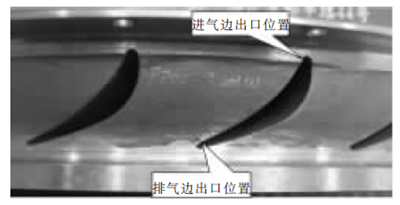
圖3 零件型腔示意圖
為降低零件型(xíng)麵對(duì)孔位置度的影響(xiǎng),加(jiā)工時需根據零件(jiàn)型麵情況對孔(kǒng)位進(jìn)行調整。孔位調整步(bù)驟為:標準樣件確定加工孔位→編製加工程序→加(jiā)工(gōng)試件→測算試件和(hé)標準件型麵差異對孔位的影響量→調整孔位→修改加工程序→加工正式零件。
(2)排氣邊孔(kǒng)加(jiā)工效率低。排氣邊孔(kǒng)為型腔內的斜孔,加工中選用細長杆導向器,避免與夾具發生幹涉。所用(yòng)電極為400 mm 長的銅管電(diàn)極,因選用細長杆導(dǎo)向器,使電極的有效使用(yòng)部分變小(xiǎo),加工效率低。孔的入(rù)口位於型腔斜麵上,加(jiā)工可靠性差,加工時電極沿(yán)型(xíng)麵滑動,孔位確定困難(nán)。加工時選用合理的加工參數,改(gǎi)善加工時的衝液狀況,以提(tí)高加工穩定性和加工效率。
2.2 電火花加工實例
使用ZT-017 型電火花(huā)小孔機床加工, 電極材料為黃銅(tóng),直徑(jìng)分別為0.25、0.35 mm,長300 mm,加工前找正夾具外圓跳動在0.01 mm 以內。用去離子水作為工(gōng)作介質,電導率為0.1×103 μs/cm。
2.2.1 加工過程與步驟
(1)裝夾電極,校正電極基準麵與工作台的(de)位置精(jīng)度,保證裝夾(jiá)可靠。
(2)以榫齒和側平(píng)麵為定位基準麵裝夾工(gōng)件,加工時將工件以(yǐ)定(dìng)位麵為基準,裝夾後校正與電極的相對位置。機床可建立及變更坐標係統原點(diǎn),利(lì)用高靈(líng)敏度和快速響應速度的置零功能,能實現電極對工件的定位、找正。校正電(diàn)極與工件的相對位置後(hòu)將工件固定,移動主軸頭,使電極下端麵與(yǔ)工件上平麵保持合適的距離。
(3)打開工作(zuò)液泵,將壓力調到8 MPa,工作液由循環係統進(jìn)入密封夾頭,再通過電極(jí)中部毛細(xì)管孔進入加工區,啟動脈衝電源與控製係(xì)統,調出編製好的加工程序,準備進行加工。
(4)加工時根據(jù)加(jiā)工穩定狀態調節(jiē)進給速度、衝液壓力等。通過參數(shù)顯示屏隨時觀察孔(kǒng)的加(jiā)工深度、電極損(sǔn)耗及(jí)加工時間等。加工過程中應抽查孔的尺寸和加工表(biǎo)麵情況,以保(bǎo)證(zhèng)零件的加(jiā)工品質。
2.2.2 試驗結果
試驗加工參數見表1,試驗現場見圖(tú)4。利用電火花工(gōng)藝進行高壓渦輪葉片(piàn)氣膜孔加工,產品品質明顯改善(shàn),效率與葉片加工合格率大幅提高,零件合格(gé)率提(tí)高到80.7 %,加工成本顯著降低。加工品質與效率(lǜ)的提高使發動機的按時交付得到了保證(zhèng)。
表1 氣(qì)膜孔電加(jiā)工參數
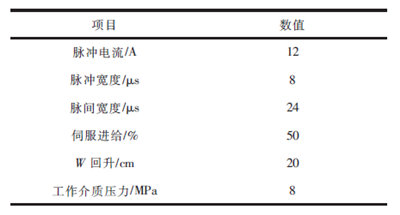
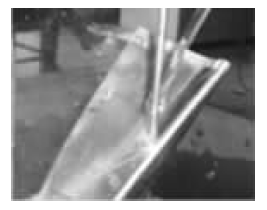
圖4 工作葉片加工現場
2.2.3 加工工藝難點分析與對策
在試驗過程中發現,采用小孔機加工氣膜孔的難點主要表現在加工深度控製、加(jiā)工設備穩定(dìng)性與精度的提高、加工中硬件故障的判斷與排除等。在分析原因的基礎上, 結合實際情況來製定解決措施,取得了(le)良好效(xiào)果。
2.2.4 加(jiā)工深度的控製
由於目前使用的電火花加(jiā)工設備使用半(bàn)閉環係統,加工深度信(xìn)號沒有反饋,所以無法準確控製加工深度。高壓渦輪葉片, 內腔距離(lí)僅為0.198~0.215 mm。如何保證既把(bǎ)孔打通又不打傷或打(dǎ)穿葉片內腔對麵基體的難(nán)度(dù)非常大。現采取以下措施來解決問題。
(1)軟阻斷。計算出所有孔(kǒng)各(gè)截麵穿頭深度,根據電極長度(dù)消耗值,按尺寸公差偏上(shàng)差計算加工深度,並將深度值固化在程序中,控製電極加工深度。
(2)硬(yìng)阻斷。將一個長80 mm、寬1.85 mm、厚0.8 mm 的銅條插入葉片腔體, 用來阻(zǔ)擋電極損耗,防止打傷或打穿葉片(piàn)。
(3)補加工工藝方案(àn)。當遇到葉(yè)片壁(bì)厚不均勻、電極品質不好、機床(chuáng)故障等特殊情況,造成孔沒有打通時,分(fèn)別(bié)編製(zhì)了直徑0.3、0.5 mm 孔的補加工程序,對通(tōng)孔位進行補加工。
2.4.5 加工設備穩定性與精度的提(tí)高
試驗發現,電火花設備的B 軸、旋轉頭、泵、電器等設備易出現故障。B 軸剛性差, 易出現位置偏移,造(zào)成第6~9 排孔的(de)位(wèi)置度極易不合格;旋轉頭不轉、碳刷接觸不好及導向器同(tóng)心度不好等;高壓泵正常使(shǐ)用壓力為6 MPa 以下,而加工需8 MPa 的高壓,這就使高壓泵(bèng)超常運行,再加上設備全天不間斷運行,使高壓泵的(de)許多部件疲勞運行,其故障必然頻繁發生,主(zhǔ)要損傷的部件有過濾器、節流墊、節流(liú)閥、滾珠、電動機等。另外,由於疲(pí)勞運行,工(gōng)作液裏含有電蝕物及(jí)部(bù)分金屬(shǔ)微粒(lì),再加上某些泵的品質問題,使低壓泵也常有故障發生,嚴重影響電火花機床的(de)效率。實踐(jiàn)證明,通過下述措施可有效解決故障問(wèn)題。
(1)重新編製一個新程(chéng)序,對6~9 排孔單獨加工,以保證其空間位置不受機床缺(quē)陷的影響。
(2)新旋轉頭(tóu)采用陶瓷軸承,防止了鏽(xiù)蝕(shí)和電蝕,一般壽命(mìng)提高(gāo)3~6 倍。
(3)通向電極的電(diàn)流直接連接碳刷,減少電(diàn)流流經的中間環節,降低了故障率,也提高了係統(tǒng)加工的穩定性。
(4)優選高、低壓(yā)泵,通過(guò)多品牌(pái)、多(duō)型號(hào)泵的運轉試驗,選擇壽命(mìng)長、參數(shù)和性能穩定的泵進行加(jiā)工。
(5)對主要損傷部件增加了庫(kù)存量,使設備可進行長時間、不(bú)停機加工,提高緊迫生產任務的應變能力(lì)。
(6)定期對高、低壓泵進行檢查,如發現異常情況立即更換, 並對更換下來的高壓(yā)泵進行檢查、維護、修理。
(7)對計(jì)算機係統軟件進(jìn)行修改和升級,對原時間當量由原來的30 s 改為10 s,有(yǒu)效降低了超差品的概率和機床故障率。
3.成效及結論
激光打孔不論材料的種(zhǒng)類和硬(yìng)度(dù)都可進行,故(gù)應用範圍較廣,但因精度較差,重複精度也較低,所以(yǐ)用(yòng)量(liàng)、規模都不是很大(dà)。但對一些特殊(shū)零件(jiàn),采用激(jī)光打孔卻取得了很大的效益。渦輪葉片氣膜孔(kǒng)的加工(gōng)采用激光旋切,盡管在孔壁局部範圍尚(shàng)存在重熔層(céng),最大厚度<0.05 mm,個別孔存在微裂紋,但(dàn)不進入基體。另外,激光打孔對高硬度、非導體材料的微小孔、孔(kǒng)數量很大的零件進行(háng)加工(gōng)也很有優勢。電火花打孔最突出的特點是其重熔層厚度僅為激光打孔重熔(róng)層厚度(dù)的一半, 可控製在0.02 mm以內,能滿足所有(yǒu)發動機動、靜葉片的冶金質量(liàng)要求。對於某些位(wèi)於葉身型麵的氣膜冷(lěng)卻孔,可使用高速電火花(huā)打孔機(jī)床, 重熔層厚度(dù)一般在0.04 mm以(yǐ)內。
激光打孔工藝不(bú)需工作(zuò)電極(jí),在數控工作台上安(ān)裝零件不需製作複雜的工(gōng)裝,氣(qì)膜冷(lěng)卻孔的尺寸可任意調節,最適宜作為(wéi)新機(jī)研製時打孔的工(gōng)藝方法。電火花打孔成本低,加工(gōng)質量比激(jī)光加工重熔層薄。在加工氣膜孔的過程中,將電火花及激光工藝共同融入其中,合理地調整加工工序,會大大地提高零件的加工質量及效率,同時也會降低其加工成本。通過采用(yòng)電火花加工、激光加工兩種工藝方法,對(duì)零件工序進行合理調配,並對工藝方法和加工參數進行優化。
隨著先(xiān)進製造技術的發展,新的氣膜孔加工工藝(yì)不斷被開發出來,對(duì)帶有陶瓷塗(tú)層(céng)葉片的氣膜孔加工,公司內(nèi)部現正在使用的加工工藝是先加工(gōng)冷卻氣膜(mó)孔,再塗覆(fù)陶瓷,最後用微型鑽頭在相應(yīng)的(de)孔位處去除陶(táo)瓷(cí)塗層,其工序複雜、效率低、質量不(bú)易控製。現在使用激光電火花複(fù)合加工技術(shù),可在相應的打孔位置上精確地用(yòng)激光去除(chú)陶瓷塗層,再使用(yòng)高速電火花精(jīng)確(què)打孔, 縮短了零(líng)件的加工(gōng)周期,確保了加工(gōng)質量。同時,為公司各(gè)類型動(dòng)、靜葉片零件的加工(gōng)摸索出可行的工藝方案, 此方法也可在其他(tā)機種的零件中應用, 拓寬了該方法的用途。因此,激光(guāng)、電火(huǒ)花複合加工工藝的研發,對航空發動機的製造有著深(shēn)遠意義。
投稿箱:
如果您(nín)有機(jī)床行業、企業相關新聞(wén)稿(gǎo)件發表,或(huò)進行資訊合作,歡(huān)迎聯係本網編輯部, 郵(yóu)箱:skjcsc@vip.sina.com
如果您(nín)有機(jī)床行業、企業相關新聞(wén)稿(gǎo)件發表,或(huò)進行資訊合作,歡(huān)迎聯係本網編輯部, 郵(yóu)箱:skjcsc@vip.sina.com
更(gèng)多相(xiàng)關信息
業界視點
| 更多
行業數(shù)據
| 更多
- 2024年11月 金屬切削機床(chuáng)產量數據
- 2024年11月 分(fèn)地區金(jīn)屬切削機床產量數據
- 2024年11月 軸承出口情況
- 2024年11月(yuè) 基(jī)本型(xíng)乘用車(轎車)產量數據
- 2024年11月 新能(néng)源汽車產量數(shù)據
- 2024年11月 新能源汽車銷量情況
- 2024年10月 新能源汽車產量數據
- 2024年10月 軸(zhóu)承出口情況
- 2024年10月 分地區金屬切削機床產量數據
- 2024年10月 金屬切削機床產(chǎn)量數據
- 2024年9月 新(xīn)能源汽車銷量情況
- 2024年(nián)8月(yuè) 新能源汽車產量數據
- 2028年8月 基本型乘用車(轎車(chē))產量數據
博文選萃
| 更多