深孔鏜床一體化刀具對缸筒加工效率的影響
2015-8-5 來源:數(shù)控(kòng)機床市場網 作者:無錫機電高等職業技術學(xué)校秦(qín)文偉
摘 要:高效的鏜床加工技術(shù)是研究者關注(zhù)的重點問題。 采用(yòng)刀具和滾珠(zhū)一體配合設計,同時利用(yòng)輔助液壓係統控製鏜刀伸縮設計的(de)一體化刀具,加工時負(fù)載低緩平(píng)穩,平穩時間區域較長,大大縮短了加工流程,減小了工(gōng)件受力時產生的振動,提高了精加工(gōng)的穩定性和可(kě)靠性,促(cù)進了產品質量。
關鍵(jiàn)詞:鏜床;一體化刀具;加工效率
0 引 言
鏜削加工是機械加工(gōng)過程中諸多加工方法的一種,它的加工過程就是把工件裝夾在(zài)鏜床的工作台上或者固定在附近裝置上不動(dòng),讓刀具主軸作(zuò)旋轉運動,並且使工作台移動做進給運動,從(cóng)而實現零件的(de)鏜削(xuē)加工。 對鏜床加工技術的研究,現在主要集中在電氣控製和機床性能改造兩個方麵,其(qí)中李金瑩、陳輝通過對連(lián)杆加工前狀況的分析和工序加工後要達到的各項精度進行分(fèn)析,在保證加工效率和精度的(de)同時,設計出(chū)臥式高速高精度雙軸連杆鏜(táng)床,重點介紹了機(jī)床的總體結構[1]。 華滿香、淩誌學利用三(sān)菱FX2N 係列 PLC 對 T68 鏜床的改造, 采用順序功(gōng)能流程圖的程序設計方法設計(jì)出梯形圖並進行現場調試,並使編程更趨(qū)於規範化、 標準(zhǔn)化(huà)[2]。 下企業實踐時,企業利用鏜削加工深孔缸筒類零件(jiàn)是精加工中的重要工序,影響深孔加工質(zhì)量的影響因素主要有機床精度、操作不當和(hé)刀輔具問題(tí)[3]。 針(zhēn)對刀輔具問題所引(yǐn)起的加工質量問題,企業采用鏜頭一體化刀具實現了深孔的高效加(jiā)工,大大提高了生產(chǎn)效率。
1 一體化鏜床刀(dāo)具(jù)企(qǐ)業引進的刮削滾光深孔(kǒng)鏜床,製造商為意(yì)大利塔基公司,設備型號為 FTSeries 450B500伊3000 CNC,主要技術參數:鏜床的中心高為 500 mm、床身回轉直徑(jìng)為 1 000 mm,最大鏜深3 000 mm,主軸的電機功率為(wéi) 75 kW,主軸移動速度範圍是 10 ~1 000 r/ min,刀具旋轉速度是 10 ~1 000 r/ min。 冷卻單元的最大流量為(wéi) 1 600 lt/ min,鏜頭的電機功率(lǜ)為(wéi) 100 kW。 刮削滾光深孔鏜床刀具的主(zhǔ)要特點為:一次裝夾 9 把刀具先刮(guā)後削實現一次性鏜削作業,鏜頭體與主軸的結合麵加長以提高整體剛性,鏜頭後端通過液壓控(kòng)製刀具的伸張(zhāng)以實現刀具準確讓刀,鏜孔直徑的微調是通過鏜頭(tóu)前(qián)端的調(diào)節螺栓來實現的,每把鏜刀前端的導向塊(kuài)實現進刀(dāo)過程(chéng)的導向。 並且大(dà)流量切屑液衝洗(xǐ)錐孔,避免鐵屑影響主軸的精度(dù)。
鏜床一體化(huà)刀具關鍵部件的主要功能為螺紋聯軸器實現鏜杆和鏜頭的螺(luó)紋鏈接,保證鏜杆和鏜頭液壓通孔準確對中;彈簧收縮套杆在(zài)鏜(táng)削結束使刀具收縮實現自動讓刀,當刀具退出時,為避免刀具在工件已加工麵上拉出刀痕,設置液壓裝置通過實現收縮刀具可以實現有效讓刀;刮削(xuē)刀具實現對切削螺(luó)紋的依次刮削;滾珠實現切削麵的強力滾壓;調節內六方(fāng)螺(luó)栓通(tōng)過內部錐麵實現(xiàn)切(qiē)削刀具的微量調節。 鏜床一體化刀具鏜削缸筒時的加工過程,如(rú)圖 1 所示。
由圖 1 可看(kàn)出,使用一體化刀具進行(háng)鏜削時,鏜削的過程為“先削次刮後滾冶。 當鏜杆實現進給運動(dòng)時,鏜頭隨著鏜杆在(zài)進給電機的帶動下沿導(dǎo)軌做直線(xiàn)水(shuǐ)平運動,三角切(qiē)削刀具首先進行比較厚的吃刀量,實現首次切削,扁平圓弧刮削刀具先後實現對鋸齒形的牙頂進行中度和(hé)微度兩次刮削,滾珠在鏜(táng)杆公轉和(hé)自身旋轉的受壓情況下實現缸壁內的表麵滾光,成型速度比較完好。
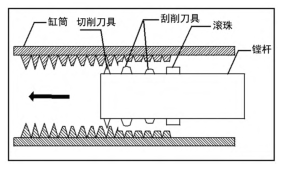
圖 1 一體化(huà)刀具的(de)鏜削過(guò)程
2 鏜削加工效率對比
以前(qián)在加工(gōng)深(shēn)孔缸筒時,采(cǎi)用 TKA2140400 伊3000 mm 進行鏜削,由於刀具采用(yòng)分(fèn)離(lí)式(shì)刀具,粗鏜與精(jīng)鏜分離,精鏜時滾珠不會自動退縮,依靠半環手動調整前後位置實現讓刀,鏜床的(de)動(dòng)作循環為間歇作業且僅有一把刀具,效率較低。 普通鏜床和刮削滾光深孔鏜(táng)床加(jiā)工深孔缸筒類零件(jiàn)的完整工序如圖 2 和圖3 所示。
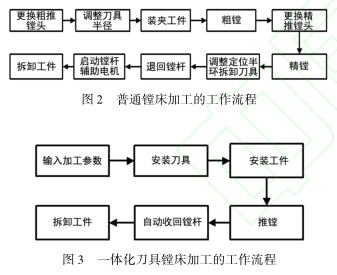
由圖 2 和圖 3 可知,相比較於普通鏜床,利用一(yī)體化刀具(jù)鏜孔時工序較少,依靠整體式(shì)刀具(jù),鏜削深孔時僅使用一道工序,通(tōng)過液壓自動控製刀具伸(shēn)張,縮短了更換刀具和半環的操作(zuò)時間,自動(dòng)化程(chéng)度很高,大大(dà)提高了工作效率。
經過統計和(hé)計算,在鏜削 漬400伊2 000 mm 的(de)缸筒時,普通推鏜運行時(shí),一般情況(kuàng)下(xià)轉速(S)為100 r/min,進給速度(F) 為 55 mm/ min,一(yī)體化刀具鏜削時,主軸轉速(S)為 100 r/ min,鏜軸轉速(S)為 80 r/min,進給速度(F)175 mm/ min。 普通鏜床和一體化刀具鏜削過程總時間對比結(jié)果(guǒ),如表 1 所列。
從表 1 可以看出(chū),從鏜削加工計算總耗時可知,一體化刀具鏜削加工(gōng)效率是普通鏜床加工效率的 3倍左右。 實際(jì)加工情況是,更換鏜頭時間和安(ān)裝刀具時間往往出現在批量生產加工(gōng)之前,單件(jiàn)加工時不會(huì)重複操作,批量生產時間愈長,更換鏜頭時間和安裝刀具時間對加工效率的影響越小,實際的加工時間為技術加工時間和測量調整時間之和,此時,一體化刀具鏜削實(shí)際加工加工效率是普通鏜床加工效(xiào)率(lǜ)的 6倍左右。
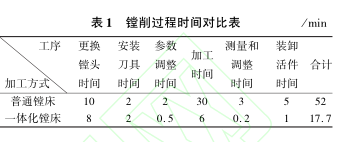
3 鏜削加工負載對比
采用一體化刀具的(de)刮削滾光深孔鏜(táng)床,它的(de)滾光刮削機(jī)鏜刀、滾珠進入和退出缸筒的時間(jiān)為連(lián)續作業,而普通鏜床則采用分離式刀具(jù),鏜刀(dāo)、滾珠進入(rù)和退出(chū)缸筒的時間為間歇式操作,造成鏜削加工過程中兩種負載的差別(bié)較(jiào)大。 刮削鏜床加(jiā)工和普通(tōng)鏜床加工負載是隨時間的變化而變化的,變化曲線如圖 4。
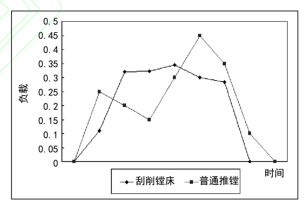
圖 4 負載變化(huà)曲線圖
由圖 4 可知,由於刮削鏜床主軸轉速和進給量比(bǐ)較大(dà),和普通鏜削相(xiàng)比,加工工件的時間較短,同(tóng)時,采用一體化刀具使(shǐ)車(chē)床係統的負載較低(dī),平穩時段主要集中在中(zhōng)間,約占(zhàn)整個加工時間(jiān)的 80%。
4 鏜床主要結構的數值模擬分析
目前利(lì)用計(jì)算機對(duì)刀具進行動態模擬(nǐ)的(de)研究很少,數值模擬理論分析主要集中於(yú)鏜杆、軸承、中(zhōng)心(xīn)架和底(dǐ)座的流場與(yǔ)動態特性研究。 其中邵俊(jun4)鵬通過計算流體力學有限體積的方法對重型臥式鏜床(chuáng)靜壓中心架流場進行數值仿真(zhēn),得(dé)到了靜壓支承的油腔壓力在整個油(yóu)腔麵積上是均勻分布的(de),並且油腔的麵積占到總有效麵積的2/3 以上[4]。 所以,支承件和被支承件的局部壓力都不會承受的較大,這有助於提高支承的耐用性。 王洪玉對(duì)精鏜床結構模型的動態特(tè)性進行分析,通過模態分析得到模型的基頻呈現出非線性增(zēng)大的變化趨(qū)勢,而且是隨著鏜杆軸套外圓直徑的增大(dà)出現的;鏜杆受力時,它的(de)模態分布是呈一定規律的[5]。 因此借鑒鏜床主要結構的數值分析結果,得到了鏜床(chuáng)主要構件的各種模態(tài)參數,為鏜削加工時鏜床的結構穩定性以及一體化鏜削刀具(jù)優良的加工效率(lǜ)提(tí)供了理論依據(jù)。
5 結 語
鏜床采用一體(tǐ)式刀具進行鏜削,刀(dāo)具功能較多,結構複雜,結合操作係統參數化智能操作(zuò),減少了退刀、換刀、測量時間,大大(dà)縮短了加工流程,同時鏜削時(shí)負載低緩平穩,減小了(le)工件受力時產(chǎn)生的振動,當(dāng)主軸轉速(sù)達到了 175 ~ 250 r/ min 時,所加工孔的光潔度達到了 Ra0. 8,圓度達到了 0. 02 滋m,提高(gāo)了精加工(gōng)的穩定性和可靠性,促進了(le)產品質量。
投稿箱(xiāng):
如果您有機床(chuáng)行業、企業相關新聞稿件發表,或進行資訊合作,歡迎聯係本網(wǎng)編輯部, 郵(yóu)箱:skjcsc@vip.sina.com
如果您有機床(chuáng)行業、企業相關新聞稿件發表,或進行資訊合作,歡迎聯係本網(wǎng)編輯部, 郵(yóu)箱:skjcsc@vip.sina.com
更多(duō)相(xiàng)關信息
業界視點
| 更多
行業數據
| 更多
- 2024年11月 金(jīn)屬切削機床(chuáng)產量數據
- 2024年11月 分地(dì)區金屬(shǔ)切(qiē)削機床產量數據
- 2024年(nián)11月 軸承(chéng)出口情況(kuàng)
- 2024年11月 基本型乘(chéng)用車(轎車)產量數據
- 2024年11月 新能源汽車產量數據
- 2024年11月 新能源(yuán)汽車銷量情況
- 2024年10月 新能源汽車產量數據
- 2024年10月 軸承出口情況
- 2024年10月 分地(dì)區金屬切削機床產量數據
- 2024年10月 金屬切削(xuē)機床(chuáng)產(chǎn)量數據
- 2024年(nián)9月 新(xīn)能源汽車銷量情況(kuàng)
- 2024年(nián)8月 新能源汽車產量數據
- 2028年8月 基本型乘用車(轎車(chē))產量數據