汽車內外飾驗證台架設計與開發
2021-6-21 來源:東風汽車公司(sī)技術中心 作者:楊 興
摘要(yào) : 隨著中國汽車市場競爭(zhēng)加劇,顧客對於汽車品質提出更高的要求,無論從外觀、內(nèi)飾,智能網聯化、綜(zōng)合能耗、聲噪指標(biāo)都有新的(de)訴求(qiú)。作為汽車研發部(bù)門,東風汽車技術中心已初步具備仿真、色彩、驗證模(mó)型設(shè)計及(jí)主模型(xíng)加(jiā)工能力。汽車(chē)內外飾驗證(zhèng)台架設計及開發主要解決整車開(kāi)發前期設計方(fāng)案是否合理和裝配(pèi)驗證是否幹涉的作用。本文(wén)通過東風自主轎車內外飾驗證台架 X53 項目設計(jì)與(yǔ)開發過程,對(duì)今(jīn)後該類工程模型自製(zhì)工作做了有益的探(tàn)索。
一、汽車內外飾驗證台架的概念和(hé)用途
內外飾驗證(zhèng)台架是(shì)為了在 ET0 前(qián)驗證車身內外飾件結構數據,驗證汽車零件(jiàn)結構,驗證(zhèng)裝配可行性,驗證 DTS 製作的工程驗證模(mó)型。通過內外飾驗(yàn)證台架,不僅能夠進行零件裝配驗證,同時能夠進行感知質(zhì)量評價,在 ET0 階段作為車身內外飾件檢具(jù),驗證(zhèng)設計結構作為標準白(bái)車(chē)身,安(ān)裝 RP 件或 ET0 件進行人機驗證。
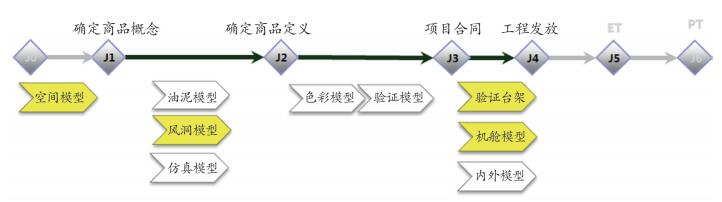
圖 1 汽(qì)車相關模型開發流程圖
二、汽車內外(wài)飾驗證台架主要的技術要求
1.內外飾驗證台架模型材料要求
采用鋼管骨架,5166 代木為型麵材料,表(biǎo)層加工厚度 30mm 以上。采用鋼板底座,底板厚度要求 15mm 以上(shàng),檢具本體采用可加工樹脂板材(cái)為型麵材料。型麵輪廓材料為 5166 代木,其性能(néng)要求 : 密度≥ 1.2g/cm3, 硬度邵氏 D ≥ 75,線性熱膨脹(zhàng)係(xì)數 (10-6m/℃ ): ≤ 35。定位(wèi)麵及支撐麵(miàn)材料采用 SK5 或相當材(cái)料(liào),其結構必須采用可拆卸式結構,不允許采(cǎi)用膠水粘結。
2.內外飾驗證台架骨架(jià)製(zhì)作要求
①骨架材料為 A3 鋼,120×60mm 方鋼管厚度為 5mm,50×50mm 方鋼管厚度為 3mm。
②骨架製作根據設(shè)計定義的整車姿態,可(kě)以調整姿態 ; 骨架要求具備用於二次加(jiā)工的複位基準和對刀(dāo)塊 ; 有可連接風洞五(wǔ)帶係統的固定結構 ;有可拆卸(xiè)的副(fù)骨架,用於支撐模型,以確(què)保模型在長途運(yùn)輸途中安全。
③骨(gǔ)架滿焊,焊縫無虛焊、氣孔、裂紋(wén),骨架外(wài)表麵焊痕磨平,焊接完進行不低於(yú) 48 小時人工(gōng)時效處(chù)理,骨架製作完成後(hòu),本體需(xū)塗防鏽漆,基(jī)準塊塗防鏽油。
④ 骨架基準麵垂直及平行度≤ 0.05mm ,安裝基準孔距公差≤ 0.02mm,整體(tǐ)安裝後的骨(gǔ)架總體尺寸誤差小於 2mm。
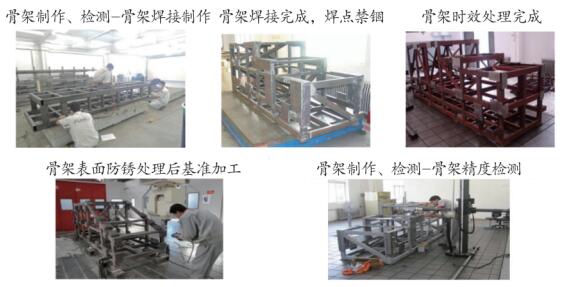
圖 2 內外飾驗(yàn)證(zhèng)台(tái)架骨(gǔ)架製作流程圖
3.內外飾驗證台架試製精度要求
①精確製造(zào)檢具所有的部件包括檢具基座、定位(wèi)基準和檢驗零件(jiàn),以保證產品檢驗(yàn)所(suǒ)需精確度。
②硬質模型工(gōng)作型(xíng)麵的精度誤差應小於0.20mm。
③所有用(yòng)於被測零件的定位(wèi)基(jī)準在(zài)檢具上的位置公差都必須(xū)限製在 ±0.10mm 以內(nèi)。
④ 硬質模型的所有用(yòng)於檢(jiǎn)測被測零件的零件包括檢驗銷和(hé)導(dǎo)套,在檢具上的位置公差都(dōu)必須限製(zhì)在 ±0.15mm 以內。
⑤用於內部線條 / 塞片檢驗的表麵(miàn)輪廓特(tè)性在檢具上的位置公差都應該限製在 ±0.15mm 以內。
⑥用於邊緣線條 / 塞片檢驗(yàn)的表(biǎo)麵輪廓特性在檢具上的位置(zhì)公差應限製在 ±0.20mm 以內。
⑦ 模板( 活裝塊(kuài))在檢具上(shàng)的公差應限製在 ±0.20mm 以內。
⑧作為目測基準的公差應在 ±0.30mm 以內。
⑨零件製造公差分列如下。
坐標線 :0.05mm; 無搭接裝配要求的全部形狀 :±0.30mm; 有搭接裝配要求的形狀 :±0.15mm; 支承及定位(wèi)公差 :±0.1mm; 對稱(chēng)形狀的不對稱度 :0.20mm; 左 / 右檢(jiǎn)具的(de)不對稱度 :0.30mm; 最大加工刀痕深度 :0.05mm;非功能孔目測刻度(dù) :±0.30mm; 用銷(xiāo)規檢查的一般功能孔位置度 :±0.15mm; 用銷規(guī)檢查的重要功能孔位置度 :±0.10mm; 一般輪廓對(duì)齊處(chù) :±0.30mm; 重(chóng)要輪廓對齊處(chù) :±0.15mm; 某一產品的特性偏離上述規範時(shí),檢(jiǎn)具的(de)公差可采用 1/4 準則,在產品圖紙上針對某一特別產品特(tè)性標注公差的 1/4 可用作檢(jiǎn)具製造公差。
4.內外飾驗證台架試製骨架強度要求(qiú)
①內外飾驗證(zhèng)台架骨架必(bì)須進行退火處理,保證整個骨架的強度和剛度。
②在搬運、包裝及試驗時要求保證模型的完好性,保證整(zhěng)車、零部件及零部件之間的連接不發生斷裂、脫落等損壞事件,油泥表麵不發生開裂現象。
三、內外飾驗證台架零件構成與關(guān)鍵
總(zǒng)成(chéng)零件設(shè)計要點(diǎn)
1.設計使用的CAD軟件
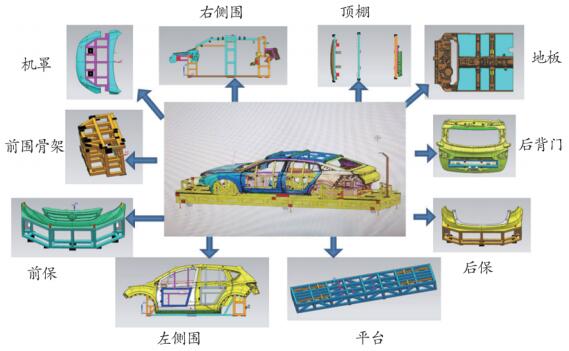
圖 3 汽車內外飾驗證台架(jià)零件構成
UG(Unigraphics NX) 是 Siemens PLMSoftware 公司出品的一個產(chǎn)品工程解決方(fāng)案,它為用戶的產品設計及加(jiā)工過程提(tí)供了數字化造型和驗證手段。Unigraphics NX 針對用戶的虛擬產品設計和工藝設(shè)計的需求,提供了(le)經過實踐驗證的解(jiě)決方(fāng)案。本次設計使(shǐ)用的設計和編程軟件為 UGNX12 版本。
2.關鍵總成零件設(shè)計要點
(1)前保總成(chéng)設計方案
長 =(車頭最前位(wèi)置(zhì) - 前輪眉邊界)-30mm(柔性板厚度),考慮不(bú)同車型在柔性骨架上的通用 ; 寬 = 右側前保安裝(zhuāng)麵 - 左(zuǒ)側前(qián)保安裝麵 ;高 = 前格柵下邊界 100mm 處-前保下邊界100mm 處 -30mm(柔性板厚度)選取最低高度為柔性骨架,針對高(gāo)度高的車型(xíng)可在(zài)柔性板和模型間增(zēng)加墊(diàn)塊。
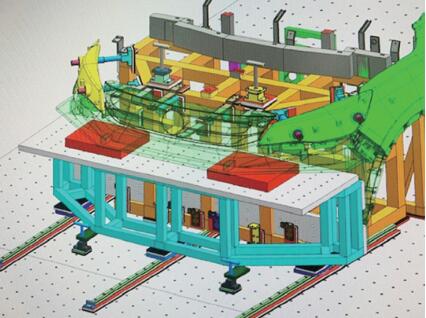
圖 4 前保總成裝配圖
(2)後保總成設(shè)計方案(àn)
後保設計方案使用柔性安裝板。柔性(xìng)安裝板為 30mm 厚度鋁合金板,均布直徑 10mm 銷孔,孔間距為 50×50mm,安裝板(bǎn)尺寸參考骨架本體尺寸 ; 連接方式 : 骨架與柔性板之間使用(yòng)螺栓緊(jǐn)固連接 ; 柔性板與模型之間通(tōng)過(guò)柔性板上銷孔使用螺栓和銷等方式連接。
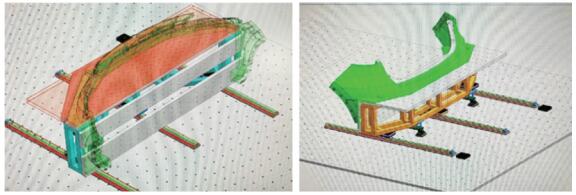
圖 5 後保總成裝(zhuāng)配圖
(3)前門總成設計方(fāng)案
內外飾驗證台架驗證門總成使用(yòng)單邊一側進行(háng)驗證,設(shè)計為左側前門,B 麵保留完整鈑(bǎn)金麵。玻璃導軌、B 麵和 A 麵一體式加工,玻(bō)璃導軌外表麵加厚 10mm。模型上保留大小 20×20mm的加工基準,門前後各一處。參考車身門鈑金保留車身內飾件和後視鏡(jìng)等安裝點,安裝點處布置金屬鑲塊,內嵌於模型內。玻璃單獨(dú)加工,水切處設置螺(luó)栓孔用於固定。前(qián)門分別設置三(sān)處擰緊在側(cè)圍上(shàng)的銷孔,上端兩處下端一處,鎖(suǒ)緊方(fāng)向為正 Y 向 ; 並預留相應的銷控墊板結構。為便於門的拆遷,將鉸鏈處 A 麵門板作為附件,單(dān)獨安裝在門板主體(tǐ)上。
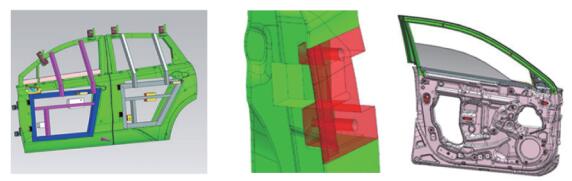
圖 6 前門總成裝配和內部結構圖
(4)後門總(zǒng)成設(shè)計方案
後門主體骨(gǔ)架是 “口” 形,加(jiā)上橫豎兩條加強筋,另焊接兩(liǎng)根連接骨(gǔ)架與車門模型上端連接,連接骨架位置(zhì)和間距按車門尺寸均布。骨架前段焊接與鉸鏈連接的安裝鐵塊,後方無鎖扣結構。骨架與代木(mù)主體之間(jiān)采用糊狀代木連接,無螺栓等連接結構。主體框架距離鈑金邊界距(jù)離≥ 110mm。模型避讓門板主體骨架外邊界距(jù)離≥ 5mm。材料 45 鋼,厚度 5mm ,20×40mm管(guǎn)材焊接而成(chéng) 。車門開(kāi)啟角度以設計輸入為準。
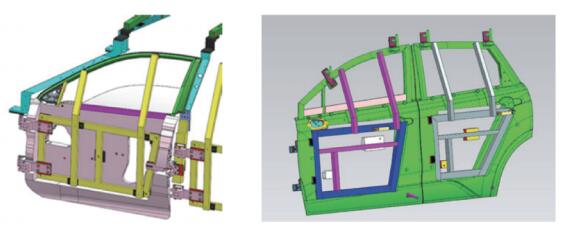
圖 7 後門總成裝配和內部結構圖
(5)後尾門總成設計(jì)方案
尾門結構設計包含 : 模型設計及骨架設計。模型設計 : 參考(kǎo)尾門內外鈑金數據、預留與骨架鉸鏈安裝點、預留尾門飾板安裝點,與側圍配合安裝點,基準塊布置 ; 骨(gǔ)架設計 : 與頂蓋處鉸鏈骨架連接,預埋加強鋼管骨架,尾門支撐杆處骨架 ; 尾門本體模型設計結合內外鈑金數據設計(jì)成一體。
台架主(zhǔ)體骨(gǔ)架通過鉸鏈(liàn)與(yǔ)尾門骨架連接 (; 參考數據撐杆安裝點高度,開啟角度 77° - 開啟角度 90°)尾門模型內預埋鋼管與(yǔ)尾門(mén)鉸鏈及(jí)支撐(chēng)杆骨架連接(jiē) ; 保留飾板以及尾燈安裝點,安裝點(diǎn)布置銷套 ; 尾門模型主體通(tōng)過左右兩側邊定位銷限位 ; 尾門模型鈑金翻邊單獨加(jiā)工並與主體粘(zhān)貼 ;設計四個基準塊 30×30mm,位置左右對稱均布。
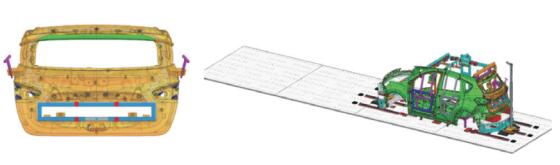
圖 8 尾門總(zǒng)成裝配和內部結(jié)構圖
(6)地板總(zǒng)成設計方案
型麵 : 以鈑金麵為基礎,人的腳部踩踏區域設計為平麵。數(shù)控加工 : 將前排座椅間隙和人的(de)腳部踩踏區域與整體切分開,其 他區域一體式(shì)加工或者拆(chāi)分為 2 個大(dà)塊加工。定位 : 在(zài)中部區域開槽與骨架(jià)匹配 + 螺栓定位。材料使(shǐ)用 : 主體采用密度 1.2g/cm3 的代木 ; 所有安裝孔位製作金屬鑲套 ; 前排(pái)座椅間隙和(hé)人的腳部踩踏區域采(cǎi)用密(mì)度 0.2g/cm3 的 PU,厚度約 30mm。
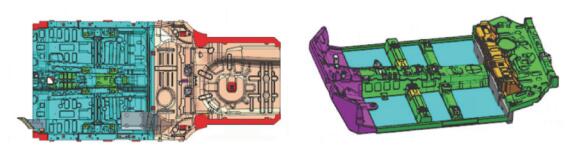
圖 9 地(dì)板總成裝配和內(nèi)部結構(gòu)圖
(7)發(fā)動機罩總成設計(jì)方案
支撐(chēng)點(diǎn)位:後端(duān)兩點為(wéi)鉸鏈,中前段3點支撐。
中間為鋼骨架,周邊(biān)采用代(dài)木製(zhì)作(zuò)。由於機艙不安裝零部件,B 麵隻(zhī)保留(liú)邊界 50mm 的鈑金結構,其餘地方做成平麵或光滑曲麵(簡化處理)。
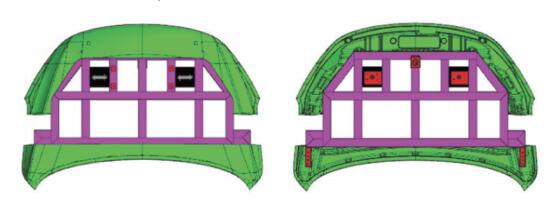
圖 10 發動機罩總成(chéng)裝配和內部結構(gòu)圖
(8)側圍總成設計方(fāng)案
駕駛員側完整結構,副駕(jià)駛側隻有骨架支撐結構 , 結構必須采用可拆卸式結構,不允許(xǔ)采用膠水粘(zhān)結(jié)。中間為鋼骨架,周邊采用高密度代木(密度 >1.2g/cm3)製作。安(ān)裝的孔位和定位采用實(shí)車(chē)狀態,安(ān)裝孔位必須(xū)鑲(xiāng)嵌金屬機構保證拆卸換裝(zhuāng)及(jí)強度。外觀不是重點項,連接結構可以從 A 麵打孔進行連接。
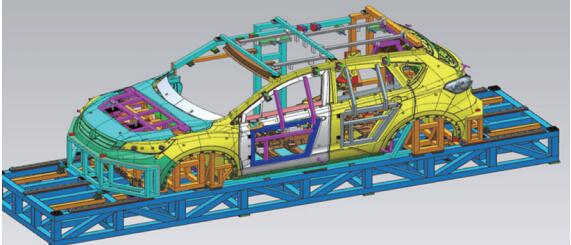
圖 11 側圍(wéi)總(zǒng)成總成裝配結構(gòu)圖
四、內外飾驗證台架工藝製造
內外飾驗證台架試製分為以下幾個階段 : 第(dì)一階段為骨架製作,包含骨架設計、下料切割、拚(pīn)料焊接、熱處理、安裝孔和基準麵(miàn)機加、骨架檢測(cè)和防鏽處理(lǐ)等 ; 第二階段為內外飾驗證台(tái)架分總成主體結構設計(jì) ; 第三階段為零部件(jiàn)製作及裝配,根據設(shè)計(jì)圖紙要(yào)求製作分總成的毛坯,主要零件采用數控加(jiā)工進行,做好每個分總成相應的裝配基準,製作完成後對應(yīng)主骨架的基準進行相應位置的裝(zhuāng)配工(gōng)作 ; 第四階段為檢(jiǎn)測,檢測零(líng)件表麵、整車姿態、定位安裝孔位、間隙麵(miàn)差(chà)。主要工藝(yì)製作流程(chéng)按照以下順序(xù)進行(háng) : 骨架設計→骨架確認→骨架焊接→骨(gǔ)架加工→骨架檢(jiǎn)測→數據處理→毛坯製作→粗(cū)加工→ NC 加(jiā)工→分總成與骨架裝配→五軸加工→車身附件 NC 加工→樣件修配→組配→評審→噴漆→組配。
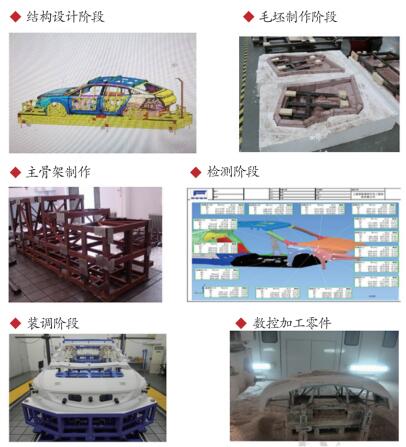
圖 12 內(nèi)外飾驗證(zhèng)台架製作流(liú)程圖(tú)
1.數控編程加工工藝方案
數控編(biān)程的精度按照規(guī)範要求,其中(zhōng) A 麵精度≤ 0.3mm,切削的最大殘留高度≤ 0.02mm,DTS 檢(jiǎn)測值公差≤ 0.2mm,相應編程(chéng)參數應與此對應。數控編程使用公差參照 GB/T 1804一般公差未注公差的線性和角度尺寸的公差和(hé)GB/T 1184 形狀和位(wèi)置公差未注公差值進行設定。粗加工,切削步(bù)距(jù)設定為所使用刀具(jù)直徑的1/4,例如(rú) φ20mm 球(qiú)刀切削間距設定為 5mm。精加工(gōng)切削間距(jù)設定為所使用刀具直徑(jìng)的 1/40。例(lì)如 φ20mm 的球刀取切削(xuē)間距設定為 0.5mm。模型編程坐標係(xì)建立包括坐標原點選擇和坐標軸確定,數控機床坐標係(xì)標準為右手笛卡坐(zuò)標係,確定(dìng)模型在機(jī)床上的裝夾方向和相(xiàng)對位置。模(mó)型整體數控加工的編(biān)程按照 EQCY-5044 汽車驗(yàn)證模(mó)型設計規範定義的設計(jì)基準編(biān)製。使用編程軟件(jiàn) NX12.0, 數控加工設(shè)備JOBS 五軸加工中心和馬迪克斯五軸加工中心。
2.內外飾驗證台架質量控製方案
為保證整個驗證台架製(zhì)作順利、有序、按時完成,在骨架製作(zuò)完成、零件裝配完成(chéng)及交付(fù)之前三個階段進行驗收安排。第一次驗收為骨架驗(yàn)收,需檢測骨架的定位孔及定位麵的尺寸精度及後處理狀態,提供熱處理報告及實際(jì)尺寸與數據尺寸對(duì)照表,檢(jiǎn)測全過程必須有技術人員一直在場(chǎng) ; 第(dì)二次驗收是零件裝配完成之後,確認型麵質量、樣件質(zhì)量等滿足設計功能要(yào)求 ; 第三次驗收是在整車驗(yàn)證台架檢測後進行,確認內外飾驗證台架外觀、尺寸是否滿足要求並整改到位達到設計零件互換要求(qiú),采用三坐標打點(diǎn)檢測,檢測總點數不得少於 500 點,測點排布原則 : 功能敏感區加密點數,在過渡區減少點數。
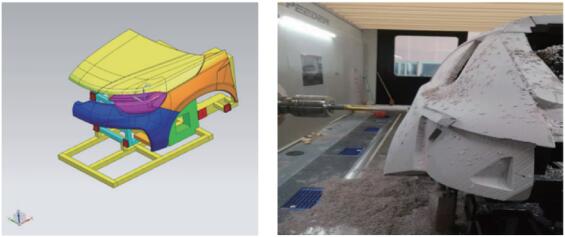
圖 13 數控編(biān)程和數控加工圖
五、總結
經過此次項(xiàng)目製作,增強了技術中心製(zhì)作工程類模型的能力。主要體現在 : 提高了內外飾驗證台架的設計能力 ; 通過自製縮短數控加工製作時間 ; 有效驗證了汽車前期研(yán)發出現的各類問題,加(jiā)快了整(zhěng)車(chē)研發的試(shì)製周期,在國內汽車模型製造(zào)領域具有實(shí)用和推廣價值。
與國際先(xiān)進(jìn)模型製造企業相比,國內模型製作的能力已經(jīng)接近國外先進水平,但是由(yóu)於起步較晚,專業性積累較少,在現(xiàn)場調試數據的反(fǎn)饋、搜集、整理並重新融入設(shè)計再應用環節尚有一定的(de)差距,各個模塊數據庫的建立還處在比較初級的階(jiē)段,隨著今後經驗的積累,將逐步縮小(xiǎo)與(yǔ)國外先進技術差距,高端工程類模型製造能力會不斷加強。
投稿箱(xiāng):
如果您有機床行業、企業相關新聞稿件發表,或進行資訊合作,歡迎聯係本網編輯部, 郵箱:skjcsc@vip.sina.com
如果您有機床行業、企業相關新聞稿件發表,或進行資訊合作,歡迎聯係本網編輯部, 郵箱:skjcsc@vip.sina.com
更多相關信(xìn)息
業界視點
| 更多
行業數據
| 更多
博文(wén)選萃
- 機械加工過程圖示
- 判(pàn)斷(duàn)一台加工中心精度的(de)幾種辦法
- 中走絲線切割機(jī)床的(de)發展趨勢
- 國產數控係統(tǒng)和數控機床何去何從?
- 中國(guó)的技術工人都去哪裏了?
- 機(jī)械老板做了十多年,為何還是小作(zuò)坊?
- 機械行業(yè)最新自(zì)殺(shā)性營銷(xiāo),害人害(hài)己!不倒閉才
- 製造(zào)業(yè)大逃亡
- 智能時(shí)代,少(shǎo)談點智造,多談點製造
- 現實麵前,國人沉默。製(zhì)造業的(de)騰飛,要從機床
- 一文搞懂數控車床加工(gōng)刀(dāo)具補償功能
- 車床鑽孔攻螺紋加工方法及工裝(zhuāng)設計
- 傳統鑽削與螺旋銑孔加工工藝的區別