車床主(zhǔ)軸與進(jìn)給(gěi)軸耦合熱誤差建模及補償研究
2015-11-23 來源:數控機床市場網 作者:西安交通大學機械製造係統孫誌超陶(táo)濤(tāo)黃曉勇
孫誌超,陶濤(tāo),黃曉勇,梅雪鬆(sōng),王新孟,楊軍,趙(zhào)亮(liàng)
(西安交通大學機械製造係統工程國家(jiā)重點實驗室,710049,西安)
摘要:針對車床實際加工中主軸與進給軸的熱誤差(chà)相互耦合共同影響工件精度的問題(tí),建立了(le)綜合熱誤差模型,並進行了有效補償。以海德曼 HTC500/500 精密車床為研究對象,對車床主軸(zhóu)與進給軸熱誤差(chà)的耦(ǒu)合關係進(jìn)行了解耦。利用模糊聚(jù)類理論實現(xiàn)了車床(chuáng)測溫點的優化分組,建(jiàn)立了(le)主軸與進給軸的耦合熱誤差多元線性回歸模型,並在精密(mì)車床上得到實(shí)際應用。結果表(biǎo)明:車床耦(ǒu)合熱誤(wù)差模型符合實際工(gōng)況,模(mó)糊聚類有效降低了溫度變量之間的多重共線性,提高了模型的預測精度;主軸x/z方向熱誤差模型預測(cè)精度達(dá)88.4%、90.7%, x/z軸熱誤差模(mó)型預測精(jīng)度達82.9%、71.3%;補償後車床 x/z 方(fāng)向精度分別提高了60.3%和 56.6%,證(zhèng)明耦合熱誤差模型的準確性。
關鍵詞:熱誤差解耦;熱誤差建模(mó);模糊聚類分析;誤差補償
機床熱誤差嚴重製約著精(jīng)密和超精密加工行業(yè)的發展,熱誤差占據了機(jī)床總誤差的 70%,對機床的加工精度影響最大(dà)。目前,消除熱(rè)誤差主要有兩種方法(fǎ):熱誤差預防法和熱誤差(chà)補償法。近年來,對機(jī)床熱誤差方(fāng)向(xiàng)的研究越來越多,相關方麵的理論也越來越多,產生了很(hěn)多有價值的科(kē)研成果。Donmez 認為變化的溫(wēn)度是機(jī)床產生熱變形,是機床的(de)主要(yào)誤差源,機床越精密受(shòu)其影(yǐng)響越大;Mou 認為機床的熱特性是(shì)由(yóu)於熱源位置、機床材料及(jí)強度、機床結構(gòu)等多(duō)種因素共同作用相互耦合作用的結果;Min 等人提出了(le)基於傅裏葉熱力學方程為基礎的熱態模型,分析不同(tóng)邊界條件下絲杠溫度場的分布特性,對研究機床進給軸(zhóu)熱誤差特性打下一定的基礎(chǔ)。相關理(lǐ)論的增多也伴隨著(zhe)機床熱誤差建模(mó)方法的增多,Yang等人利用神經網(wǎng)絡技術建立(lì)了主軸(zhóu)熱誤差與溫(wēn)度之(zhī)間的關係模型;楊軍等人利用模糊聚類優化溫度測點,並結(jié)合最小(xiǎo)二乘支持向量機和神經網絡技術,構建了精密坐標鏜床主軸的熱誤差模型,取得了良好的預測效果;Wu 等人利(lì)用有限元仿真技術,建立了絲杠預緊力和(hé)進給(gěi)速度與絲杠溫度場(chǎng)和熱變形的關係模型,並通過試驗驗證模型的有效性;Lin 等人利用最小二乘支持向量機理論建立了主(zhǔ)軸熱誤差與溫度變化的相關關係;郭前建等人結合聚(jù)類分(fèn)析理論建立了滾齒機熱誤差的多元線性回歸模型,提(tí)高了熱誤差模型的(de)預測精度。Chao 等人(rén)利用 BP 神經網絡模型和基於反(fǎn)饋線性自(zì)回歸滑動平均的小波元神經網(wǎng)絡模型建立了數控機床進給係統在不同工況(kuàng)下溫度場分布和熱變形的數學模型;謝春等人利用 BP 神經網(wǎng)絡算法建立了五軸車銑複(fù)合加工中心(xīn)進給軸的綜合熱誤差(chà)模型,並做(zuò)了(le)相關實驗驗證;Abdulshahed 等人提(tí)出了一種改進的自適應模糊推理係統(ANFIS),建立機床主軸的(de)熱誤差預測模型,提高了預測精度;苗恩(ēn)銘等人建立了數控加工中心主(zhǔ)軸的支持向(xiàng)量回歸機模型,並在不同的環境溫(wēn)度下驗證模型的準確性,均取得了良好的預測效果。
當前文獻主(zhǔ)要針對機床的主軸(zhóu)和進給軸單個係統分別(bié)進(jìn)行建模(mó)及(jí)補償,而實際加工中主軸與(yǔ)進給軸的熱誤差是並行存在,共同影響(xiǎng)工件的加(jiā)工精度。單個係統(tǒng)獨立補償與實際不符,而將兩者的(de)熱誤差結合在一起的研究非常少。本文針(zhēn)對機床主軸與進給軸熱(rè)誤差(chà)的耦合問題,進行了解耦分(fèn)析,建立了(le)耦合熱誤差(chà)模型;並以海德曼HTC550/500 車床為研究(jiū)對象,進行了(le)補償應(yīng)用,驗證了耦合熱誤差模型的有效性及魯棒性。
1 Siemens 係統熱誤差(chà)補償方(fāng)法
1.1 Siemens 熱誤差補償方式(shì)
為了適應市場需求,西門(mén)子為用戶提供(gòng)了熱誤差(chà)補償的接口,供用(yòng)戶自定義熱誤差補償的形式及模型參數。西門子認為(wéi)金屬受(shòu)熱膨脹(zhàng)與溫度之間是線性關係,主軸的熱誤(wù)差模型隻與溫度有關,與坐標位置無關;進給軸的熱誤差模型則與溫度和坐標位置(zhì)都相關。西門子開放的熱誤差(chà)補償(cháng)方(fāng)式如圖 1 所示。

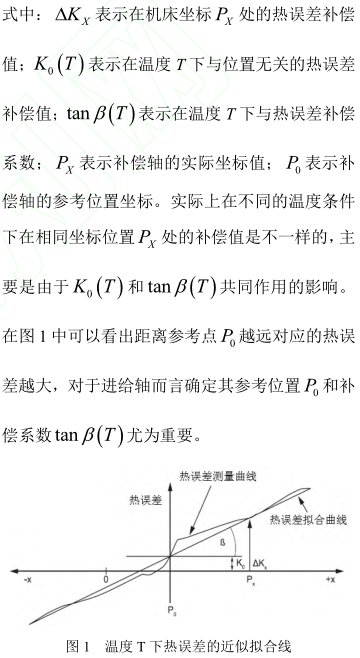
1.2 主軸與進給軸熱誤差解耦
機(jī)床(chuáng)的熱誤差最終反映在刀具與工件相對位置的偏離,從而導致機床的加工精度降低,廢品率升高造成生產成本的提高。熱誤差補償的目的就在於消除或者(zhě)減小(xiǎo)由於金屬熱膨脹而導致的(de)機床刀具與工件之間的(de)位置偏(piān)離,從而提高機(jī)床的加工精度。刀具與工件之間位置的偏離本質上是(shì)由於主軸與進給軸熱誤(wù)差相互耦合共同作用的結果,因(yīn)此尋找主軸與進給軸之間的耦合關(guān)係對於熱誤差模型的建(jiàn)立至關重要。為了能夠得到準確的熱誤差數學模型, 就需要對兩者之間進行解耦,分別得到各自(zì)的數學模型,再將模型根據耦合關係耦合(hé)在一起,便得到了機床總體的(de)熱誤差數學(xué)模型。
進給軸在進給狀態下絲杠螺母副由於(yú)摩(mó)擦產生熱量,絲(sī)杠(gàng)溫度升高,伴隨著熱伸長。此車床是半閉(bì)環係(xì)統,絲杠的伸長導致進給軸熱誤(wù)差(chà)的產生。主軸在高(gāo)速狀態下旋轉時,前端軸承與後端軸承由於摩擦產生一定的熱量,熱量傳遞到主軸,主軸受熱就會產生熱變形,導致熱誤差的產生。主(zhǔ)軸熱伸長 l的方向 z 軸相同,而(ér)主軸熱升高 h則會在 x 軸方向產生分量 x。隻有分別分析主軸和進給軸(zhóu)的熱誤差,分別建(jiàn)立相應的數學(xué)模型,才能準(zhǔn)確全(quán)麵的反映車床在 x、z 方向產生的熱誤差。主軸與進給(gěi)軸(zhóu)的熱誤差耦合示意(yì)圖如圖 2 所示(shì)。
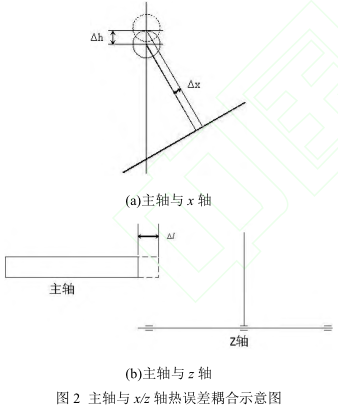
車床主軸隻有旋轉一個運動狀態,不存在坐標位置的變換,故主軸的熱誤差隻(zhī)與自身溫度變化相關,熱誤(wù)差模型與位置無關。環境溫度的改變,以及主軸由於旋轉造(zào)成(chéng)自身溫(wēn)度(dù)的提高,不僅會影響主軸的熱伸長,同樣會造成主軸在垂直方向的變化。主(zhǔ)軸在垂直方向位置的變化主要是由於主軸箱體受熱(rè)膨脹導致主軸整體升高,受環境溫度影響較大,主軸在 x 方(fāng)向的熱誤差(chà)多元線性回歸(guī)模型可以表示為
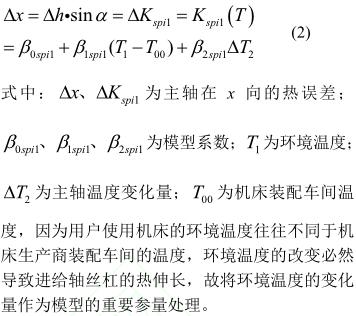
x 軸的熱誤差主要是由 x 軸絲杠的熱伸長引起的,絲杠的固定方式為一端固定一端遊動,靠近電機端為固定端,遠離電機端為遊動端,當 x軸絲杠受熱時會向遊動端伸長,固定端位置不會發生變化,可以作為熱誤差為零的參考點。x 軸熱(rè)誤差與位置和溫度相關,選定參考點(diǎn),x 軸的熱誤差多元線性回歸模型可以表(biǎo)示(shì)為
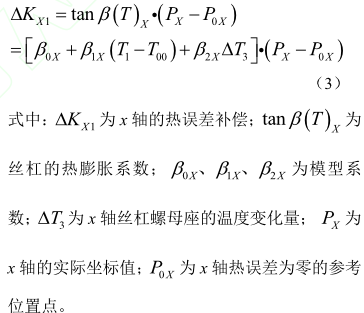
以上將機(jī)床(chuáng) x 方向的熱誤(wù)差(chà)分(fèn)別解耦到(dào)主軸和 x 軸各自的熱(rè)誤差,並分別建立了各自的熱誤差模型。解耦是將複雜問題(tí)簡單化,解耦之後還需要解耦後的結果重新進行(háng)耦合。x 軸為傾(qīng)斜式安裝,如圖 2a 所示,機床 x 方向熱誤差的耦合模型為
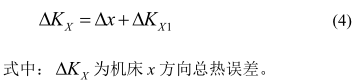
同理,主軸的熱伸長與 z 軸方向相同,熱誤差多元線性(xìng)回(huí)歸模型可以表示為
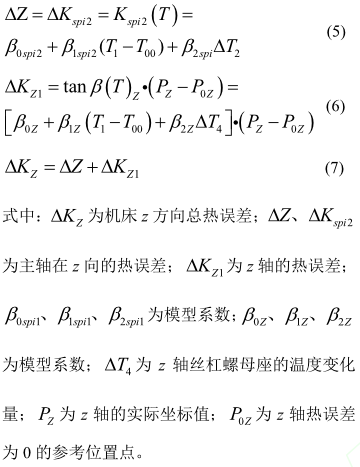
2 熱特性實驗及結果分析(xī)
2.1 實驗設計及測量原理
以浙(zhè)江海德曼機床有限責(zé)任公司生產的HTC550/500 車床為研究對象,分(fèn)析車床 x、z 方向熱誤差與溫度(dù)變量(liàng)的關(guān)係。車床 x 和 z 方(fāng)向(xiàng)的(de)最大有效行程分別為 180 mm 和 520 mm,最(zuì)高進給速度分別(bié)為 30 m/min 和 36 m/min。
測試設(shè)備如下: RENISHAW 激光幹(gàn)涉儀用於測量進給(gěi)軸熱誤(wù)差值;溫度位移同步采集係統獲得溫(wēn)度(dù)值及主軸熱誤(wù)差值;選用高精度溫度傳(chuán)感器 PT100、高精度(dù)電渦流位移傳感器。溫度傳感器 PT100 記為:T1…T17,T1~T8安裝(zhuāng)在主軸箱前端、後端和中部,T9z 軸(zhóu)電機,T10z 軸前軸承,T11z 軸後軸承,T12z 軸螺母座,T13x 軸電機,T14x 軸前軸(zhóu)承,T15x 軸後軸(zhóu)承,T16x 軸螺母座,T17 環境溫度;位移傳感(gǎn)器記為:S1,…,S5。試驗現場和主軸測量原理如圖 3、圖 4 所示。 以機床主軸、x/z 軸的(de)熱誤差為研究對象,主軸的熱誤差測量采用五點法測量,如圖(tú) 4 所示(shì)。主軸的熱伸長有 S5測量獲得,x 方向的熱(rè)誤差由S1和 S3測量獲得(dé),y 方向的(de)熱誤差由 S2和 S4測量獲得。由於(yú)轉速不同,主軸的熱變形略(luè)有(yǒu)不同,實驗中設計了(le) 1 000、1 500、2 000 r/min 3 種(zhǒng)不同的轉速。 z 軸熱誤差由激光幹涉儀進行(háng)測量,測(cè)量範圍為[-495,0],各測量點間距為 45 mm,共 12個測點。z 軸坐標 0 處作為激光幹涉儀測量原(yuán)點。x 軸的(de)熱誤差測(cè)量範圍為[-165,0],各測點間(jiān)距為15 mm,共 12 個測點,0 處作為激光幹涉(shè)儀測(cè)量原點。試驗初始時,在冷態下測量進給軸各(gè)測點誤差,作(zuò)為進給(gěi)係統的幾何誤差,進(jìn)給係統連續往複運動 30 min 後測量各(gè)測點的誤差值(zhí),此誤差值減去幾何誤差作為此刻進(jìn)給係統的熱誤差。依據 VDI/ISO 標準,每次重複測量 3 個循環,每個測點測量 2 s,進給係統暫停 4 s,為防止反向間隙對端點出熱誤差產生影響,取反向越(yuè)程 5 mm。由於進(jìn)給速度不同,進(jìn)給係統的熱變形略有不同(tóng),實驗設計了(le) 500 mm/min、1 000 mm/min、1 500 mm/min。
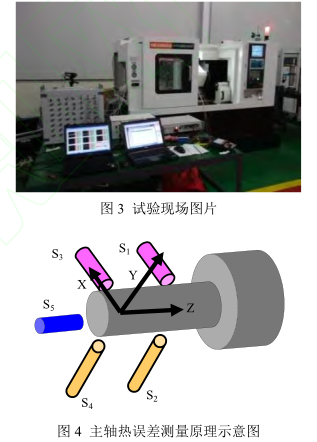
2.2 結果分析(xī)
2.2.1 溫度場時域分(fèn)析
當主(zhǔ)軸旋轉進給軸不動時,主軸箱的溫度變化如(rú)圖 5a 所示。主軸箱前端最高溫度(dù)達 36℃,最大溫差大約 13℃;主(zhǔ)軸箱後端最(zuì)高溫度達 34℃,最大溫度差 12℃;主軸箱中部最(zuì)高溫度達 33℃,最大(dà)溫差 11℃。由主軸(zhóu)的結構可知主軸前端有一個圓柱滾子(zǐ)軸(zhóu)承和兩個角接觸球軸承,後端一個圓(yuán)柱滾子軸承,主軸箱內部有空隙。主軸(zhóu)箱前端生熱較(jiào)多,後端生熱較少,所以主軸箱的溫度場分(fèn)布如圖 5a 所(suǒ)示,前端溫度高於後端,中部溫度最低。
當 z 軸進給主軸不動時,z 軸絲杠螺母座與電機端軸承(chéng)的(de)溫度變化如圖 5b 所示。由於絲杠為轉動體,無法用 PT100 直接測量絲杠的溫度,因此改為測量絲(sī)杠(gàng)螺母座和電機端軸承座的溫度來間接反映絲杠的溫(wēn)度(dù)變化(huà),這是由於絲杠溫度的變化是由軸(zhóu)承及絲杠與螺母之間(jiān)相對轉動產生摩擦而發熱,引(yǐn)起溫度的變化(huà)。因此,由螺母座和電機端軸承的溫度來間接反(fǎn)映絲杠的溫度變(biàn)化是合理的。同理,當 x 軸進給時機床其他部分靜止,x軸絲杠螺母座與電機端軸承的溫度變化(huà)如圖 5b所(suǒ)示(shì)。
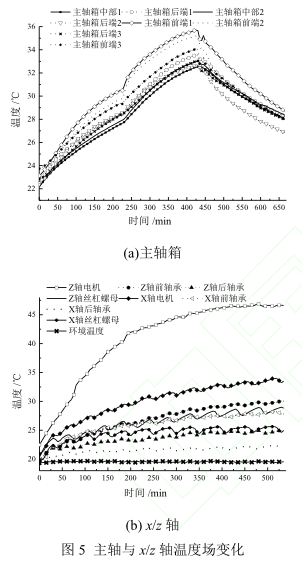
2.2.2 主軸熱變形分析(xī)
主軸的內部結構如(rú)圖 6a 所示,由圖可看出皮帶輪帶動(dòng)整個主軸係統的運轉,主軸為中空軸,有循(xún)環空氣進行(háng)冷(lěng)卻,主軸(zhóu)前端有三個軸承後端一個軸承,主軸的中部與主軸箱之間有空氣間隔。主軸旋轉時軸承的內外圈與(yǔ)滾子之間相對運動產生摩(mó)擦而發熱,熱量通過熱(rè)傳導分別傳遞到主軸、主軸箱體下部及主軸箱的其他部分(fèn)。主軸溫度的升高是導致主軸熱伸長的主要原(yuán)因,而主軸的熱伸長(zhǎng)導致機床 z 方向產生熱誤差 Z;主軸(zhóu)箱體下部的溫升是(shì)導致主軸整體升高 h的主要原因,而主軸的(de)整體升高導致機床 x 方向產生熱誤差x。 x由 S1、S3測量得到,取其平均值(zhí)作為 x熱誤(wù)差值。
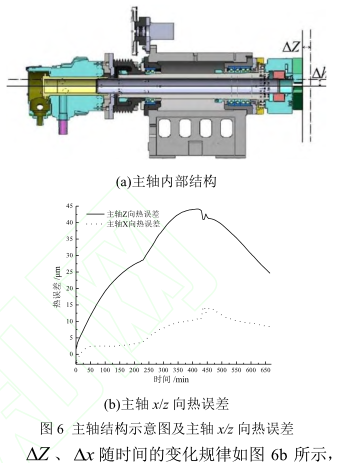
其變(biàn)化規(guī)律與圖5a主軸箱溫度變化規律基本(běn)保持一致。這就說明主軸的熱變形與主軸箱溫度之間存在(zài)者密切的關係:隨著主軸箱溫度的升高,主軸的熱變(biàn)形隨之(zhī)增大,當溫度最高時(shí)主軸的熱(rè)形達到最大值;主軸停止旋轉後(hòu)主(zhǔ)軸箱溫度逐漸下降,主軸的(de)熱變(biàn)形也隨之減小。S1/S3的采(cǎi)集值偏(piān)差較大,這說明主軸在徑向產生(shēng)了偏擺,本(běn)文忽略了主軸在 x/y 方向的擺角(jiǎo)問題。
2.2.3 進給軸位置相關熱誤差分析
進(jìn)給軸 x、y 具有同樣(yàng)的結構形式,兩端分別為固定端和遊動端。當進給係統(tǒng)運動時,電機、軸承、絲(sī)杠螺(luó)母(mǔ)副生熱,導致進(jìn)給軸絲杠受熱膨脹,固定端位置(zhì)不變,遊動端向自由方向伸長,進給軸在本實(shí)驗中的熱變形如圖 7 所示。

在冷態下第(dì)一次測量誤差作為機床(chuáng)的幾何誤差(chà),即第一次冷態測量時各測點的熱誤差為 0,圖 7 說明各次測量的時間間隔,由圖可以看出,進給軸的熱誤差與位置相關,兩者之間近似成(chéng)線性(xìng)關係,且熱誤差隨坐標(biāo)位置的增大而增大。進給軸的固定端熱誤(wù)差變化相對較小(xiǎo),而遊動端熱誤差變化相對較大,說明車床進給軸位置坐標距離電機越遠,定位精度越低,熱(rè)誤(wù)差越大,這種變化規律符合絲杠的結構形(xíng)式。電機端為絲杠的固定端,遠離電機端(duān)為(wéi)絲杠的遊(yóu)動端(duān)。
3 熱誤差建(jiàn)模及補償實(shí)現
3.1 溫度測點優化
3.1.1 模糊聚類分組(zǔ)
利用模糊聚類分析方法對溫度變量進行分
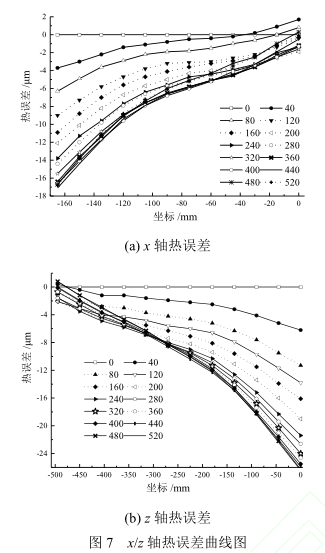
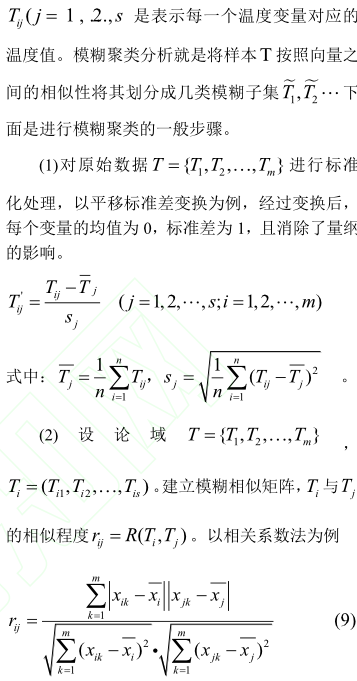
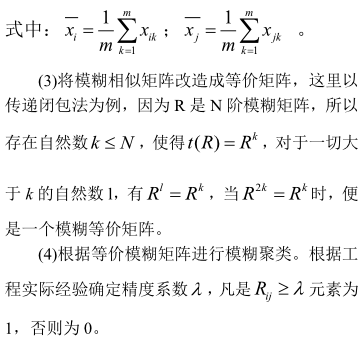
3.1.2 基於相關分析的溫度測點篩選
依據上述模(mó)糊聚類分組結果,應用統計(jì)學相關性理論進行測點優化,求取Ti與熱誤(wù)差 E 的相關係數為
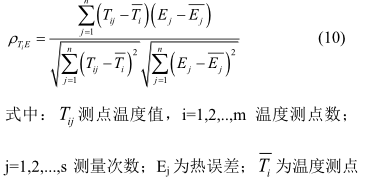
的平均值;iE 為熱誤差的平均值。相關係數(shù)如(rú)表1 所示,選擇每個聚類分(fèn)組中相關(guān)係數大的溫度作為典型變(biàn)量。故選擇 T12,和 T17為典型溫度變量。
以上介紹是以其中一項熱誤差為(wéi)例,實際中熱誤差包括主軸熱伸長、主軸熱升(shēng)高(gāo)、x 進給軸熱(rè)誤差及 y 軸進給軸熱誤差,在進行模(mó)糊聚類時(shí)需要針(zhēn)對不同(tóng)的熱誤差項分別進(jìn)行聚類分組,得到與各個誤差項最(zuì)相關的(de)典型溫度變量(liàng)。
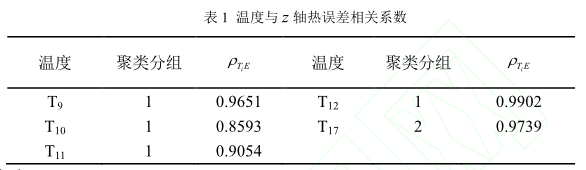
3.2 熱誤差模型
溫度變量(liàng)優化之後可以進行熱誤差數學模型的建立(lì),主要有 BP 神經網絡法、支持向(xiàng)量機法、多元線性回歸等,本文以多元(yuán)線性回(huí)歸模型為例。基於多元線性回歸模型(xíng)及實驗數據,可得到熱誤差的數學補償模型。分別建立機床主軸 x 向熱誤差與 z 向熱誤差、x 進給軸及 y 進給(gěi)軸的熱誤差補償模型(xíng),即
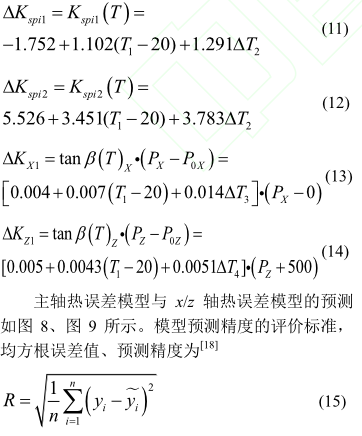
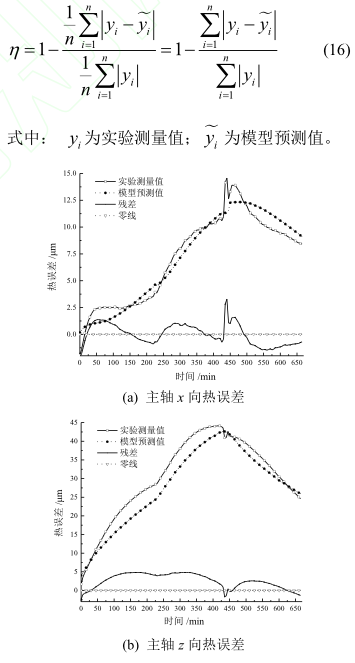
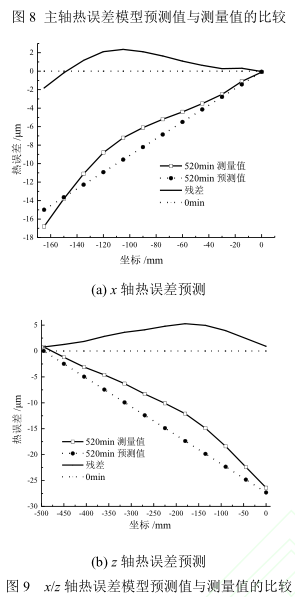
主軸x/z方向的熱誤差模型預測值的R和分別為 0.9μm、3.2μm 和 88.4%、90.7%;x/z 軸熱誤差模型預測值的 R 和 分別為 1.4μm、3.4μm 和82.9%、71.3%。證明熱誤差模型具有很高的準確性,在工程實際中還需進一步驗證。預測模型之(zhī)所以沒有達到百分之百(bǎi),任何一種模型都存在自身的模型誤差。此外,機床的(de)誤差包括伺服誤差、插補誤(wù)差、跟隨誤差、幾何誤差、安裝誤差等(děng),建模(mó)過程中這些係統誤差未予考慮,都(dōu)會導致預測模(mó)型精度的降低,因此預測模(mó)型都存在一定的誤差。
3.3 機床熱誤差補償工程應用
熱誤差補(bǔ)償係統的總體結構設計主要有溫度采集係統和 PLC 補償係統兩部分組成。溫度采(cǎi)集係統用於獲取熱敏感點的(de)溫度值,並對采集的溫度信號進行濾波、放大及 A/D 轉(zhuǎn)換。獲取溫度之後在PLC內部根據前麵的數學模型分別計(jì)算出每個軸的補償參數tanoK。PLC 將補償參數通過Siemens828D 數控(kòng)係(xì)統內部特有的 PLC 與 NC 數據通(tōng)信接口數據塊 DB1200 寫入 NC 係統內部,NC 係統會根據熱(rè)誤差補償參數(shù)對機(jī)床各軸的插補指令做相應調整,從而提高了機床各軸的定(dìng)位精度。
冷態下測量結束後(hòu)根據實(shí)驗測量原理(lǐ)開始運轉機床,直至機床達到熱平(píng)衡狀態。機床在熱平衡狀態下補償(cháng)前和補償後的(de)熱誤差如(rú)圖 11 所示。實驗過程中主軸與進給軸(zhóu)同時運轉,使得機床主軸與進給軸的(de)熱誤差耦合在一起,從而驗證(zhèng)熱誤差耦合模型的準確性。補償前 x/z 軸的定位精度為18.6μm、24.3μm;補償後 x/z 軸的定位精度為7.4μm、10.5μm,補償後 x/z 軸的定位精度提高了60.3%、56.6%,充分驗證了熱誤差耦合模型的準確(què)性。
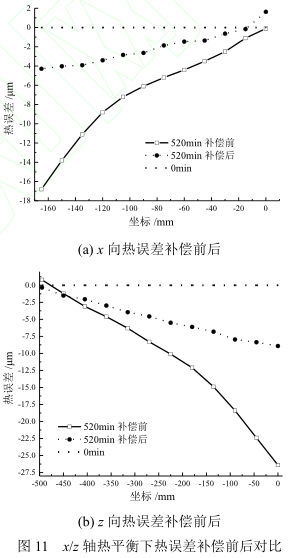
4 結 論
本文深入研究了機床熱誤(wù)差補償理論及西(xī)門子 828D 數控係統熱誤差補償機製,開發了基(jī)於828D 的熱誤差(chà)補償係(xì)統, 運(yùn)用多元線性回歸與模糊聚類相結合的方法建立(lì)機床(chuáng)各軸的(de)熱誤差(chà)數學模型,並分析了(le)主軸與進給軸之間熱(rè)誤差(chà)耦合與解耦過程(chéng),建立了主(zhǔ)軸與進(jìn)給軸之間的耦合(hé)模型,利用模糊聚類方法對(duì)溫度測點進行優化,選取熱敏感(gǎn)點典(diǎn)型溫(wēn)度變量,降低了溫度變量之間多重共線性的問題,提高了熱誤差模型的預測精度。最後,將建好的主軸與進(jìn)給(gěi)軸耦合模型嵌入 PLC中,在浙江海德曼機床廠生產的 HTC550/500 係列車床上得到實際應(yīng)用,並且進行批量生產,機床在不同溫度下(xià)的(de)定位精度得到明顯的提高,也(yě)為後期機床熱誤差的研究工作提供了重要依據。
投稿箱:
如果您有機床(chuáng)行業、企業相關新(xīn)聞稿件發表,或進行資訊合作,歡迎聯(lián)係本網編輯部, 郵箱:skjcsc@vip.sina.com
如果您有機床(chuáng)行業、企業相關新(xīn)聞稿件發表,或進行資訊合作,歡迎聯(lián)係本網編輯部, 郵箱:skjcsc@vip.sina.com
更多相(xiàng)關信息
業界視點
| 更多
行業數據(jù)
| 更多
- 2024年11月 金屬切削機床產量數據(jù)
- 2024年(nián)11月 分地區金屬切削機床產量數據
- 2024年11月 軸承出口情(qíng)況
- 2024年(nián)11月 基本型乘用車(轎車)產(chǎn)量數據
- 2024年11月 新能源汽車產量(liàng)數據(jù)
- 2024年11月 新能源汽車銷量情況
- 2024年10月 新能源汽(qì)車產量數據
- 2024年10月(yuè) 軸承出口情況
- 2024年10月 分地區金屬切削機床產(chǎn)量(liàng)數據
- 2024年10月 金屬切削機床產(chǎn)量數據
- 2024年9月 新能源汽車銷量情況
- 2024年8月 新能(néng)源汽車產量數(shù)據
- 2028年8月 基本型乘用車(轎車)產量數據