基於剛(gāng)度(dù)分析的機器人銑削加工刀具角度優(yōu)化(huà)
2022-9-5 來源:商丘職業技術學院 徐州工程學院機電工程(chéng) 作者:黃蓓 陳鳳(fèng)騰
摘要:為提高多軸機(jī)器人銑削的加工精度,提出一種新型的刀具方向角優化方(fāng)法。 該(gāi)方法綜合考慮(lǜ)了串(chuàn)聯機構的固有特性及其(qí)與機器人剛度的關係,從而在生成精加工刀具方向角時選擇最佳的機器人姿(zī)勢。 由於在不改變刀具軌跡的情況下,通(tōng)過優化選擇刀具的方向角來減少加(jiā)工誤(wù)差,該優化方法無需修改原始刀具軌跡以便補(bǔ)償預(yù)測偏差。 在(zài)多軸銑削機器人係統上的(de)實驗結果驗證了該方法的有效性。 研究結果表明,該方法能夠加工出(chū)具有(yǒu)精細表麵的三維形狀,並減少(shǎo)了由於刀具向機器人剛度(dù)最低方向位移所引起的偏(piān)差。 相比基於體積剛度性能指標的刀具方向角優化方法,RMS誤差減少了0.05mm。
關鍵詞:機器人銑削;多軸銑(xǐ)削;刀具方向角;剛度
0 、引(yǐn)言
近年來,工業機器人在機械加工(gōng)中的應用引起了廣泛(fàn)的關注(zhù)。 盡管此類機器人主要用於焊接和(hé)搬運,但(dàn)大量研究試(shì)圖(tú)將其應(yīng)用擴展到倒角、去毛刺、拋光甚至醫療手術等任(rèn)務。 最近,主要由剛性數(shù)控機(jī)床處理的任務(例如機器人銑削(xuē)) 已成為學術研究和工業研究的熱點。
串聯工業機器人機構(gòu)的特殊性質使它們能夠在相(xiàng)對較小的空間內以較低的成(chéng)本加工各種(zhǒng)大小的複雜形狀。 盡(jìn)管有這些優點,但在加工任務中使用工業機人仍有一些困難,例如定位精度低和剛度低。 盡管這些問題可通過改善其物理結構來解(jiě)決,例如采用(yòng)更好的編碼器和連(lián)杆,但機器人剛度的姿態依賴性仍然是一個未解決的問題。最近,與機器人加工相關的研究試圖通過(guò)在線和離線補(bǔ)償方法來減少刀具變形,從而提高(gāo)機器人的加工精度。
在線補償技術通常(cháng)需(xū)要昂貴(guì)且複(fù)雜的實時傳(chuán)感係統。 此外,當機器人(rén)處於低(dī)剛度的姿勢時(shí),該技術可能涉及機器人和工件的突然相對運動,這不可避免地會影響表麵光潔度。 離線補償技術依賴於刀具模型、刀具⁃工件接觸模型、切削力(lì)預測算法以及所用機器人剛度模型的準確性。 此外,曲勝等的研究(jiū)表明,由於需要完全修改原始刀具軌跡以補償預測偏差(chà),因此計(jì)算變得(dé)更加複雜(zá)。
雖然這些離(lí)線補償研究在無需複雜、昂貴在線係統的條件(jiàn)下提高了加(jiā)工精度,但是由(yóu)於沒有考慮主動(dòng)剛度的影響,即,機器人剛度隨機器人姿態的變化,因此它們僅能部分補(bǔ)償(cháng)加(jiā)工(gōng)誤差。因此(cǐ),在本研究中,提出了一種新的離(lí)線優化刀具方向(xiàng)角的方法。 利(lì)用(yòng)機器人剛度相對於刀具方向角的變化,生成具有最大剛度姿態的簡單" 之" 字形(xíng)刀具軌(guǐ)跡,從而減少刀具的(de)潛在偏差。 由於在不改變刀具軌(guǐ)跡的情況下,通過優化選擇刀具的方(fāng)向角來減少加工誤差,因此該方法比傳統優化方法具有更小的複雜度(dù)。
此外,由於計算(suàn)是基於剛度性能指標,即更容易操(cāo)作的標(biāo)量測量,因此也減少了計算誤(wù)差,並通過加工實驗對該方法進行(háng)了驗證。
1 、機器人加(jiā)工係統
本研究采用的機器人加工係統包括一(yī)個 6 軸垂直關節式機械手(Motoman SV3X)、一個(gè)提(tí)供工件傾斜和旋轉運動的 2 軸工作台、一個末端執行器及(jí)其外圍部件。 末端執行器包括一個超精(jīng)密的主軸部件(EM25N⁃5000⁃J4),用來支撐刀具。 所用 8 軸機器人銑(xǐ)削(xuē)係統如圖 1 所示。
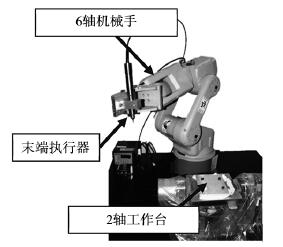
圖18 軸(zhóu)機器(qì)人(rén)銑削係統
為了確(què)保所提機器人係統的靈(líng)活性和定位精(jīng)度(dù),采取了兩項主要措施。 首先,對刀架進行了設計,以便可以使(shǐ)用懸掛和(hé)指向兩種配置。 但是,在這項工作中,由於其相對較高的靈活性,因(yīn)此僅測試了懸掛配(pèi)置。其次,按照機械手製造商推薦的程序對機器人進行在(zài)線和(hé)離線校準(zhǔn),以盡可能減少定位誤(wù)差。 校準結果表明(míng),與校準前的0.369mm相比,可以將定位誤差降低到 0.203mm。
由於機械手的運動即使在沒有切削力的情況下也會受到這種定位誤差的(de)影響,因此所提係統的加工精(jīng)度最好也是(shì)相(xiàng)同的量(liàng)級,或者(zhě)略次(cì)於(yú)它。
2 、機器人剛度分析
2.1機(jī)器人剛度(dù)識別
通常(cháng),在整體機器人剛度的建模中僅考慮關節的剛度。 然而,為(wéi)了更精確地表示機(jī)器人剛度,需(xū)要考慮機器人的姿勢和(hé)作用在(zài)機器人上的外力,式(1) 則描述了這種關係:
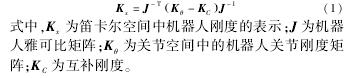
2.2剛度性能指(zhǐ)標
體積剛度性能指標最早由 Lehmann C 等提(tí)出。該指標利用(yòng)機械(xiè)手的柔度矩(jǔ)陣,避(bì)免了與計算雅可比逆有關的數值誤差。 最初,該指標用於鑽井應用中的姿勢優化,在其研究中的實驗測試證明,該(gāi)指標在增加機器人整體剛度和改善鑽孔質量方麵是有效的。本文提出了(le)一種新的指標(biāo):單(dān)向剛度性能(néng)指標,其設計目的是減少在機器人銑(xǐ)削應用中觀察到的非期望滑動運動。 該設計沒有優化機器人的整體剛度,而是專注於機器人在垂直於刀具行進軸線方向上容易發生的變形。 單向剛度性能指標(biāo)的數學公式是基於 Leh⁃mann C 等描述的柔度子(zǐ)矩(jǔ)陣。 將整體剛度計(jì)算(suàn)替換為垂(chuí)直於刀具行進軸(zhóu)線方向(xiàng)(單向)剛度計算,因此更有(yǒu)利於提升常規的“之”字型銑削加工精(jīng)度。
其中,力(lì)的方向和位移是(shì)本研究的主要問題。 如(rú)果施加到機器
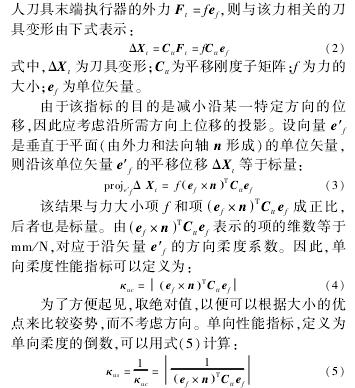
3、刀具方向(xiàng)角優化
刀具方(fāng)向角優(yōu)化過程(chéng)針對的是粗加工後的精(jīng)加工階段。 首(shǒu)先將所有刀具位置的集合表(biǎo)示為一個高度陣列。 設置垂直(zhí)分辨(biàn)率和水平分辨率分別等(děng)於切削深度(dù)和步進量。 通過相對於所需形狀偏移(yí)高度陣列來防止工件過度切削。 創建(jiàn)刀具位置的(de)偏移高度陣列後,通過圍繞(rào)刀具旋轉機械手來選擇每個刀具位置的機器人姿態。 機械(xiè)手繞刀軸(zhóu)旋(xuán)轉如圖 2 所示。
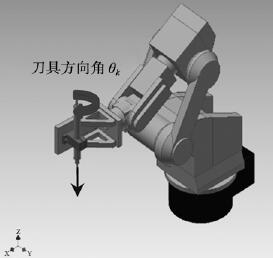
圖 2 機械手繞刀軸旋轉
從一(yī)個相(xiàng)對於 X 軸的初始角位置(zhì)(θ0) 開始,機械手的角位置增加一(yī)個常數值(θk)。 在當前刀具位置為加工選擇第一個不以碰撞結束的姿態。 這個過程在整個高度陣列中從上到下以之字形重複進行。 為了(le)簡單起見,該刀具在陣列所有點上保持垂直於水平麵。精加工(gōng)的目的是減少表麵輪廓的缺陷,並生成盡可能類似於所需形狀的最終結果。 這通(tōng)常(cháng)是通過在更適度的加工條件下加工工件來實現的,即在較低的材料去除速率下(xià),從而將刀具偏差抑製到允許的水平。除此策略外,本文使用(yòng)剛度性能指標值優化機器人姿態。 高度陣列數據(jù)結構用於生成刀具軌跡。 此外,加工切削中的刀具軌跡不是從頂部平麵到底部逐層生成(chéng)的" 之" 字形刀具軌(guǐ)跡,而是(shì)采用常規的" 之" 字形輪廓,其高度隨(suí)刀具沿X 軸的位(wèi)置而變化。 通過(guò)上述方法生成的精加工刀具位置集如圖 3 所示。
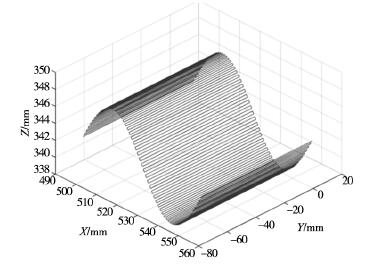
圖 3 精加工刀具位置集
一(yī)旦生成刀具位置集,就(jiù)對該集的每個點進(jìn)行機(jī)器人姿態優化。 為簡單起見,刀具應保持垂直於水平麵。 然(rán)後(hòu),機械手以上述的方式沿刀具旋轉,不同之處在於它現在考慮了機器人剛度,該剛度是針對所有刀具位置上所有可能的姿勢(shì)計算得出的。 該計算將生成一張硬度指標圖,顯示其與刀具方向(xiàng)角(jiǎo)的關係。 通過將剛度性能指標設置為零,可以將導致(zhì)機械手碰撞(zhuàng)的姿(zī)態從有效姿勢集中移除。 剛(gāng)度性能(néng)指(zhǐ)標與刀(dāo)具方向角(jiǎo) α 之間的關係如圖4 所示。
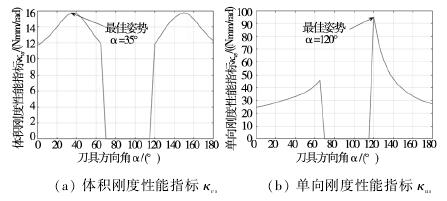
圖 4 剛度(dù)性能指標與方向角
4、 實驗(yàn)結果與分析
4.1 實驗裝置
由於(yú)關節(jiē)剛度通常是未知的,因此采用 Dumas C等提出的識別(bié)方法對(duì)機械手(SV3X)的關節剛度進行識別。 用於關節剛度識別的實驗裝置如圖 5 所示(shì)。
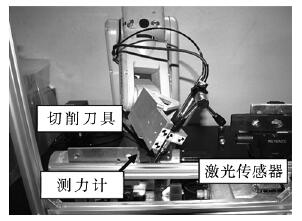
圖 5 用於關(guān)節剛度識別的實驗裝置
考慮到旋轉位移明顯小於(yú)平移位移,因此隻考慮力和平移位移。 用數字測力計(FGP⁃5,Nidec⁃Shimpo)將力施加在切(qiē)削刀具上, 並(bìng)借助激光位移傳感器(LT9030M,Keyence)測量在所(suǒ)有三個軸上測量刀具位移。 由(yóu)於激光位移(yí)傳感器和數(shù)字測力(lì)計的精度均優於激光跟蹤器和(hé)彈簧秤,因此這(zhè)種方法得到的結(jié)果更準確。
此外,由於轉動位移和扭矩可以忽略不計,從式(1)中可推(tuī)導出,在(zài)計算中不需要第 6 個(gè)關節的連(lián)接剛度(dù)。 結果表明,用上(shàng)述方法計算(suàn)的機械手各關節剛度(dù)分別為[90.925, -2.869, -3.641,1.745,1.743] ×105Nmm /RAD。加工實(shí)驗中工件的所需形狀如圖 6所示。
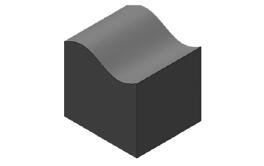
圖 6 工(gōng)件的所需(xū)形狀
由於曲麵上每個點的位置都可以用正弦函數計算。 因此,通過比(bǐ)較實(shí)際切(qiē)削高度的值和用該函數計算的(de)值,可以很容易(yì)地計(jì)算加工誤差。
4.2加工(gōng)結果對比
為了評估所提(tí)出的刀(dāo)具定向角優化方法的精(jīng)度,進行(háng)了一係列加工實驗。 工件材料選擇了主要由丙烯腈⁃丁二烯⁃苯乙(yǐ)烯(ABS)塑料(liào)組成(chéng)的(de)合成樹脂。 因為具有良(liáng)好的(de)可加工性和快(kuài)速成型優勢,該材料在機(jī)器人(rén)銑削中的得到廣泛應用。 采用了半徑為 1mm 的球頭立銑刀(SEC⁃PLBEM2S1)。 工件的材料是相同的合成樹脂,加工條件如表 1 所示。
表 1 加(jiā)工條件
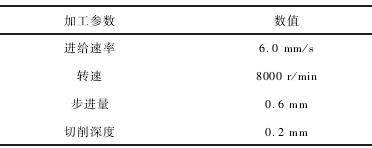
具體進(jìn)行了三種不同類型的加工實驗:①刀具方位角未優化;②以體積剛度性能指標優(yōu)化刀具方位角;③以單向剛度性能指標優化刀具方(fāng)位角(jiǎo)。 選擇刀具(jù)方向角(jiǎo)的過(guò)程與第(dì) 3 節中描述的過(guò)程相同。 但是,在非優化切削中,除了需要避免碰撞的(de)情況外,刀具方向角均保持(chí)恒定(α=0 )。 3個試(shì)驗的加工結果(guǒ)如圖 7 所示(shì)。
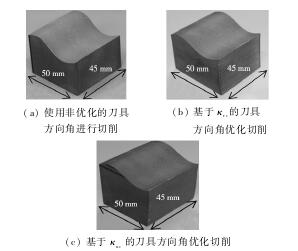
圖 7 3 個試驗(yàn)的加工(gōng)結果
加工後工件的表麵輪(lún)廓也用 3D 掃描機( RolandMXD4)進行測量,一共進行了10次測量。 圖8顯示了所測輪廓與所需形狀的(de)比較(jiào)。
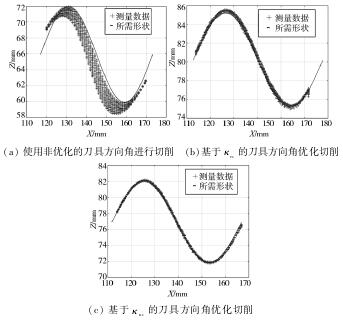
圖 8 所(suǒ)測輪廓與所需形(xíng)狀的比較
在非優化切削的情況下,雖然圖 7a 所示的表麵輪(lún)廓形狀表明加工後的表(biǎo)麵是光滑,但圖 8a 卻表明該表麵實際上與所需形(xíng)狀有較大差異。 這表明係統本身不足以實現更高的精度。相反,圖 8b 和圖 8c 表(biǎo)明表(biǎo)麵輪廓中也存在這樣的扭曲,但比刀具方向角未優化的情況要小得多(duō)。
實際上,通過比較(jiào)加工誤差的均方根(Root Mean Square,RMS)值可以(yǐ)看出,刀具方向角優(yōu)化時加工精度最好,均在機器人定位誤差的範圍內。 此外,當(dāng)使用單向剛度性能指標優化刀具方向(xiàng)角時尤(yóu)其如此,因為體積剛度(dù)性(xìng)能指標的(de) RMS 誤差為 0.22 mm,而單向剛度性能指標的 RMS 誤差為0.17mm,減少了0.05mm,即進一步提高了加工精度,驗證了其有效性(xìng)。
5、結論
本文提(tí)出了一種用於精密機器人加(jiā)工的新型刀具定(dìng)向角(jiǎo)優(yōu)化方法。 該方法利用機器人剛度隨刀具方向角變化的特(tè)點,生成機器人姿態優化(huà)後的刀具軌跡。通過加(jiā)工實驗得如下(xià)結論:
(1)與刀(dāo)具(jù)方(fāng)向角不優化時相比,方(fāng)向角優化方法能成功地生成更光滑(huá)、更精確的曲(qǔ)麵輪廓;
(2)采用(yòng)單向剛度性(xìng)能指標比采用(yòng)體積剛度性能指標更有(yǒu)效,兩種情況下的加工誤差分別為0.22mm和0.17mm,均在機器人定位誤差的範圍內,表明在加工合成樹脂等軟材料,該方法可以最大限度地(dì)提高銑(xǐ)削機器人的加工精度(dù)
。
投稿箱:
如果您有機床行業、企業相關新聞(wén)稿件發表,或進行資訊合作,歡迎聯(lián)係本網編輯部, 郵箱:skjcsc@vip.sina.com
如果您有機床行業、企業相關新聞(wén)稿件發表,或進行資訊合作,歡迎聯(lián)係本網編輯部, 郵箱:skjcsc@vip.sina.com
更多相關信息(xī)
業界視點
| 更多
行業數據
| 更多
- 2024年11月 金屬切削機床產量數據
- 2024年11月 分地區金屬切削機床產量數據
- 2024年11月 軸承出口情況
- 2024年11月 基本型乘用車(chē)(轎車)產量數據
- 2024年11月 新(xīn)能源汽車產量(liàng)數據
- 2024年11月 新能源汽車銷(xiāo)量情況
- 2024年10月 新(xīn)能源汽車產量數據
- 2024年10月 軸承出口情況
- 2024年10月 分地區金屬切削機床產量(liàng)數據
- 2024年(nián)10月 金屬切削機床產量數據
- 2024年9月(yuè) 新能源汽車銷量情況
- 2024年8月 新能源汽車產量數據
- 2028年8月 基本型乘用車(轎車)產量數據
博文選萃
| 更多
- 機械加工過程圖示
- 判斷(duàn)一台(tái)加(jiā)工中心精度的幾種辦(bàn)法
- 中走絲線切割機床的發展趨(qū)勢
- 國產數(shù)控係統和數(shù)控機床何去何從?
- 中國的技術工人都去哪裏了?
- 機(jī)械老板做了十(shí)多年,為何還是小作坊?
- 機械行業最新自殺性營銷,害人害己!不倒(dǎo)閉才
- 製造業大逃亡
- 智能時代,少談點智造,多談點製造
- 現實麵前,國人沉(chén)默(mò)。製造業的騰飛,要從機床
- 一(yī)文(wén)搞懂數控車床(chuáng)加工刀具補償功能
- 車(chē)床鑽孔攻(gōng)螺紋加工方法(fǎ)及工(gōng)裝(zhuāng)設計
- 傳統鑽削與螺旋銑孔加工工藝的區別