精密離心機主軸回轉誤差測量仿真(zhēn)技術研(yán)究
2017-1-10 來源:中國工程物理研究院總(zǒng)體工程研究所(suǒ) 作(zuò)者:張 榮,牛寶良(liáng),淩明祥,王 玨,周繼(jì)昆
摘要:精密離心機主軸回轉誤差(chà)直(zhí)接影響精密離心機動態(tài)半徑的(de)測量、離心加速度(dù)輸出精度以及精(jīng)密離心機主軸運行安全性,必須(xū)精確測量主軸回轉誤差參數(shù);介紹一種應用3 個電(diàn)容測微儀(yí)測試並分離主軸回轉誤差與圓度誤差的方法,利用MATLAB 對三隻電容測微儀安裝角度誤差、主軸(zhóu)全周采(cǎi)樣點數、測試係統本底噪聲對主軸回轉誤差測試結果影響進行仿(fǎng)真分析,得出采樣點數N、測微儀安裝角度誤差(chà)δα、δβ 以及測試係統本底(dǐ)噪聲對(duì)回轉誤差分離的影響,基於仿真結果確定了1 0 -6 量級精密離心機主軸回轉誤差測(cè)量(liàng)的幾個工程參數。該方法已應用於(yú)某高精度精密(mì)離心(xīn)機主軸回轉誤差精密測試中,實(shí)測表明,轉速在300 rpm 內精密離(lí)心機純回轉誤差測量結果為0.2 5 μm,滿足1 0 -6 量級高精度精(jīng)密(mì)離心機的研製指標需(xū)求。
關鍵詞:精(jīng)密離心機;回轉誤差;圓度誤差;三點法;電容(róng)測(cè)微儀
0.引言
精密離心機空氣主軸(zhóu)徑向回(huí)轉誤差是(shì)影響(xiǎng)高精度精密離心機性能的重要因素,主要表現在(zài):1 ) 在(zài)利用外基準測量精密離(lí)心機動態(tài)半徑時,主軸徑向回轉誤差將混入動態半徑測量值中(zhōng),回轉誤差量級較大時,其對(duì)動態半徑的影響不可忽略,必須對動態半(bàn)徑進行補償(cháng),否則經離心加速度補償模(mó)型(xíng)[1 ]輸出的加(jiā)速度信號精度無法得到(dào)保證;2 ) 主軸徑向回轉誤差直接關係到主軸運行安全(quán),對於空氣靜浮主(zhǔ)軸,氣膜厚度通常僅幾(jǐ)微米,為保證離心機在各G 值下(xià)安全運行,必須對主軸的(de)回轉運動誤(wù)差進行監視,設定(dìng)主軸回轉運動誤差限,當主軸回轉運動誤差接近超限值時,離心機必須停機。因此,為滿足高精(jīng)度精(jīng)密離心機研製技術指標,對其主軸的回轉運動參數必須進行精確測量。針對某1 0 -6 量級精密離(lí)心機研製,精密離心機主軸回轉(zhuǎn)誤差的精度指標為≤0.5 μm,為完成該參數的高精度測試,筆者提出采用電容測微儀和三點法進行測試,並(bìng)設計精密測試係統完成了1 0 -6 量級精密離心機主軸回(huí)轉誤差的測試,實測主軸純回轉誤差為0.2 5 μm。
1精密離心機主軸回轉誤差測試方法研究
目前,對於1 0 -5 及(jí)以下量級精密(mì)離心機研製, 由於量級(jí)低,主軸回轉誤差的量(liàng)值大小對精密(mì)離心機輸出加速度精度影響不明顯,而(ér)主軸運行安全性監測是主要(yào)的(de),常采用在主軸截麵上安裝(zhuāng)兩隻[2 3 ]正交的電容傳感器測量主軸轉動一周測微儀輸出最大值與最小值,這種測量無法測試出純主軸回轉誤差運動(dòng)極值。對於1 0 -6 及以上量級的精(jīng)密(mì)離心機研(yán)製(zhì),必須考慮主軸安全性以及主軸運動誤(wù)差對動態半徑的貢獻,采用雙測微儀法測試無法滿足測試要求,必須(xū)采用新的測試手段。
1.1主軸回轉誤差測試的難點
主軸(zhóu)回轉誤差測試難點在於通(tōng)常主軸圓度(dù)誤差和回轉誤差同時混雜於測試結果中, 並且圓度誤差往(wǎng)往比回轉(zhuǎn)誤差大得(dé)多,測試純回轉誤(wù)差較難,解決方法有兩種:一種是(shì)借助於安裝在主軸上的標(biāo)準球, 采用電容(róng)非接觸式或電感接觸式(shì)測試標(biāo)準球的徑向跳動量, 此時忽略標(biāo)準球圓度誤差, 采(cǎi)用正交雙測微儀合成李薩如[4 ]圖獲(huò)得主軸回轉誤差, 但該法僅(jǐn)適用便於安裝標準球的場(chǎng)合(hé), 同時標準球的安裝還存在偏心(xīn)誤差,必須在測量結果中進行一次諧波分(fèn)離去偏(piān)心誤差; 對不便安裝標準球的測試, 如(rú)本項目中的精密離心機主軸, 采用在主軸外沿安(ān)裝測微儀測試, 測試結果(guǒ)包括了主軸回轉差和圓度誤差兩(liǎng)類信號(hào),必須通過測試方法從(cóng)結果(guǒ)中分離出圓度誤差信號,得到真(zhēn)實的回轉誤差信號, 故信號分離算(suàn)法(fǎ)是關鍵。目前基本的圓度誤(wù)差分(fèn)離方法有反向法[5 ]、多點法[6 ]、多(duō)步(bù)法[7 ]等, 多點法分兩(liǎng)點法、三點法、四點法等。
表1 [8 ]是幾類誤差分離方(fāng)法精度統計, 通常各方法應用在不同的測試場合,但(dàn)對於回轉誤差的總體分離精度均可控製在1 0 %以內,這為本項目中空氣主軸的回轉(zhuǎn)誤差的測試奠定了基礎。從技術實現難易程度、成本等綜合考慮選擇(zé)在項目中應用三點(diǎn)法測試(shì)主軸回轉誤差。
表1 回轉誤差與圓度誤差分離方法及(jí)誤差表

1.2 三點法主軸(zhóu)回轉(zhuǎn)誤差分離測試原理
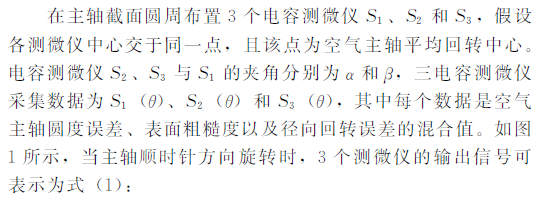
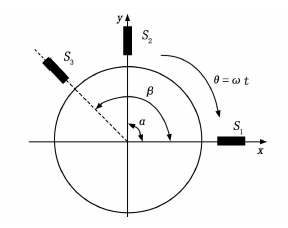
圖1 三點法主軸回轉誤差分離測試示意圖
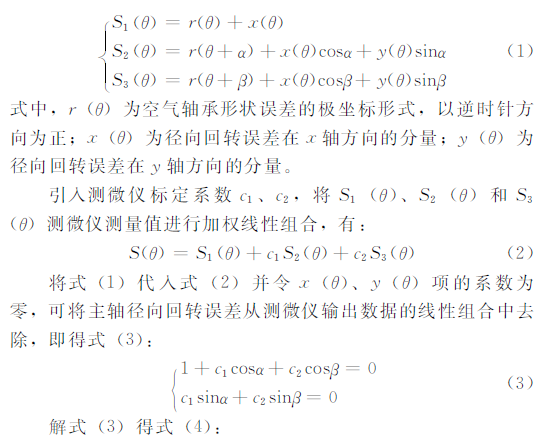
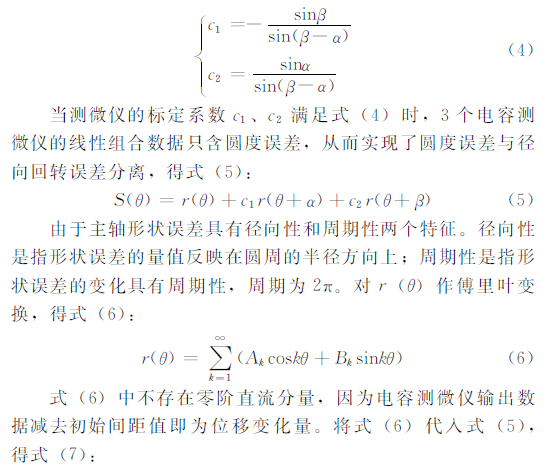
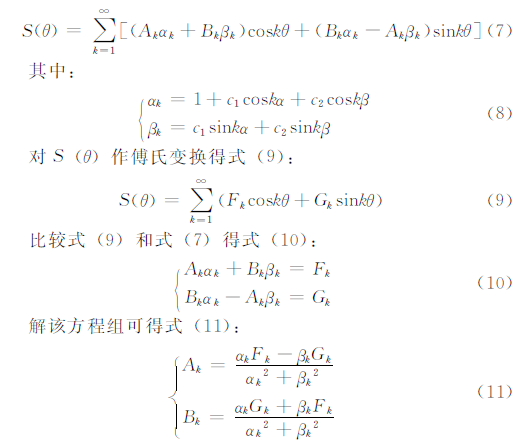
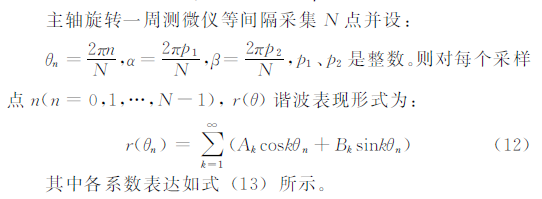
由式(1 3)可知,采樣點數N 、測微儀安裝角度誤差以及諧波分析階次均會給分離精度帶來影響,故須根據諧波分析階次與分離精度要求確定(dìng)三測微儀安裝角度; 根據ISO 標準,當被測零件(jiàn)圓度誤差(chà)的諧波次數大於22 ~45 階後,可將(jiāng)其歸結為零件表麵(miàn)粗糙度和(hé)波度[9 ],本項目參考ISO 標準, 設定主軸圓度誤差諧波上限為45 階,45 階以上的諧波成分將作為表麵粗糙度與波紋度處理。圓度誤差分離完成後,則回轉誤(wù)差也即得到分離。
2.主軸回轉誤差(chà)分離(lí)測試影響因素的仿真分析
精密離(lí)心機主軸回轉誤差測試實(shí)際設計(jì)時,需確定(dìng)主軸全周采樣點數N 、三測微儀安裝角度誤差以及測試係統本底噪聲對回轉誤差分離結果的影響程(chéng)度, 為(wéi)此在MATLAB 下
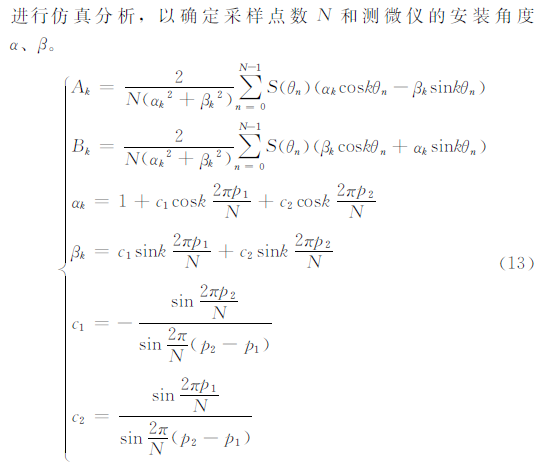
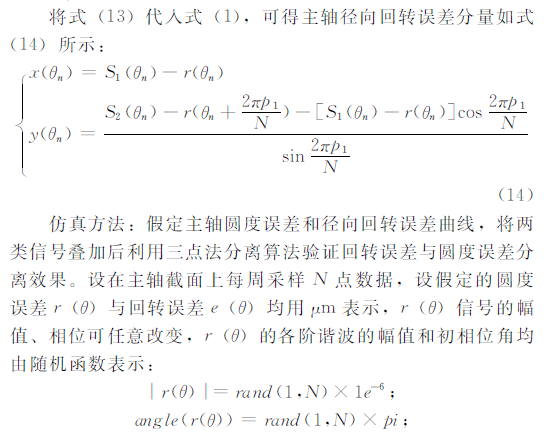
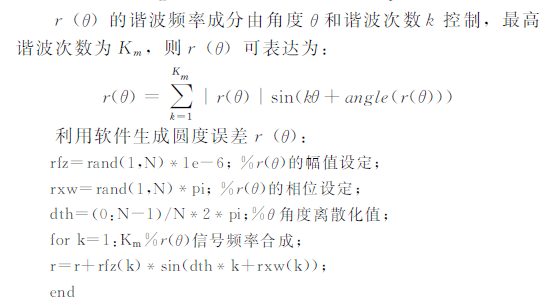
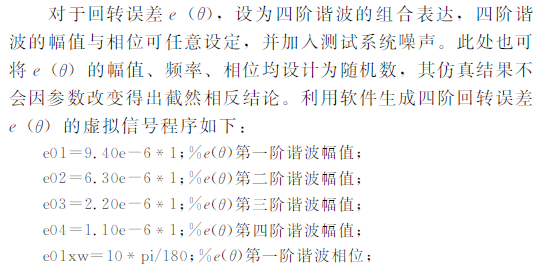
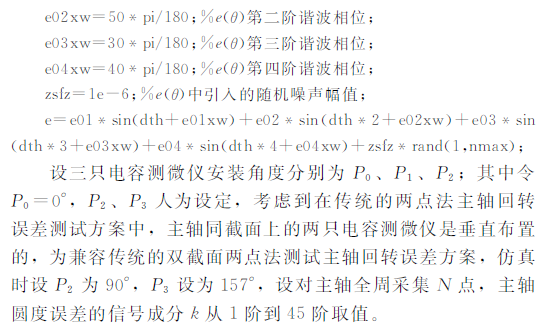
2.1采樣點數N 對(duì)回轉誤(wù)差測試影響仿真
分別設定(dìng)N =1 28,N =5 1 2 進行仿真,回轉誤差與圓度誤差的分離結果如圖2 ~圖(tú)5 所示。
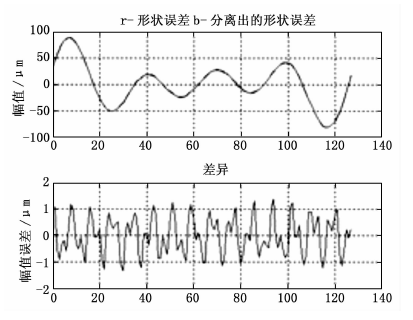
圖2 N =1 2 8 時圓度誤差設定與分離結果
從仿真結果看(kàn),N 值越大,回轉誤差與圓度誤差(chà)的分離精度越高,適當選(xuǎn)擇N 值可使圓度誤差分離信號的誤差達1 0 -1 3 量級。本項目(mù)中N 取1 600 點。
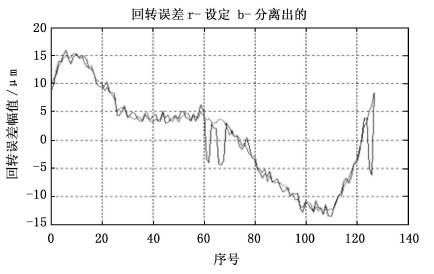
圖3 N =1 2 8 時回轉誤差設定與(yǔ)分離結果
2.2 測微儀安裝角度對回轉誤差測試影響仿真
設三隻測微儀(yí)理論安裝角度分別為0°,α=90°,β=1 5 7°。工程設計時因測(cè)微儀裝配誤差使各(gè)安裝角度存在誤差,以第一(yī)隻測微儀安裝位置為(wéi)參考,第二隻與第三隻測微(wēi)儀相對於第一隻(zhī)測微(wēi)儀的安裝夾角(jiǎo)存(cún)在偏差δα、δβ, 仿真δα、δβ 對回(huí)轉誤差分離結果的影響。考慮到(dào)離心機最高轉速為300 rpm 的工程實際,設測微(wēi)儀(yí)安裝偏差角δα、δβ 控製在±1°範圍內(nèi),在輸入信號和采樣點數N =1 024 不變時,開展如表2 仿真(zhēn)分析(xī),給出代表性的仿真(zhēn)結果如圖6 ~圖9 所示。
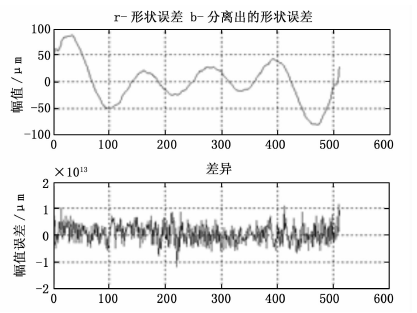
圖4 N =5 1 2 時圓度誤差設定與(yǔ)分離(lí)結果
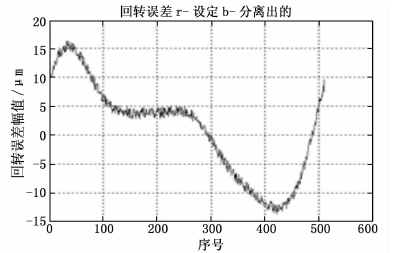
圖5 N =5 1 2 時回轉誤差設定與(yǔ)分離結果(guǒ)
表(biǎo)2 仿真測試測微儀安裝角(jiǎo)度偏差(chà)δα、δβ 表 c°
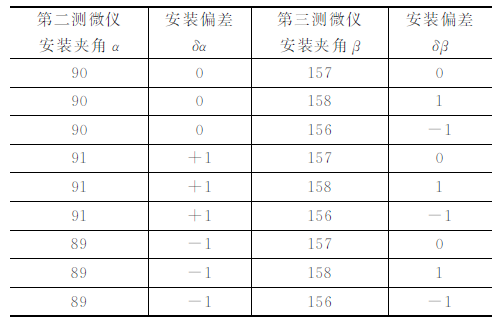
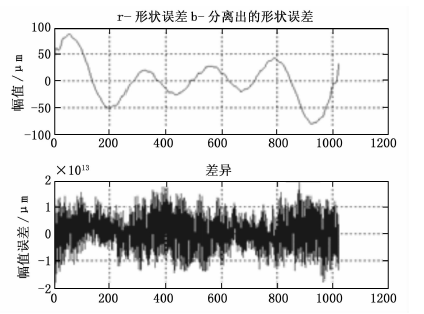
圖6 α=90°,β=1 5 8°圓度誤差設定與(yǔ)分離結果
仿真表明,在實際安裝夾角α、β 偏離理想安(ān)裝夾角± 1°時,安裝夾(jiá)角的偏差(chà)δα、δβ 對主軸圓度誤差與徑向回轉誤差
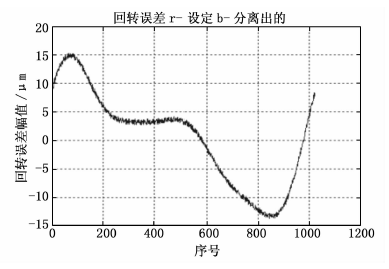
圖7 α=90°,β=1 5 8°回轉(zhuǎn)誤(wù)差設定(dìng)與分離結果
分離有一定影響(xiǎng),但影響較小,圓度誤差分離誤差量級通常在1 0 -1 3 以上,可忽略。其中,僅在α=90°、β=1 5 6°時圓度誤(wù)差(chà)的分離誤差達到了0.03 μm 左右, 這是由於安裝夾角引起的分離過程諧波抑製,多(duō)次仿真發現,這種諧波(bō)抑(yì)製(zhì)現象引起的分離誤差最大均(jun1)控製在0.05 μm 以下, 這對於本項(xiàng)目的主軸徑向回轉誤差分離影響較(jiào)小可忽(hū)略。因此,在實際測微儀安裝
時可適(shì)度降低安裝精度,允許一定安裝角度偏差,並可根據角偏差的不確定度評估出主軸圓度誤差和徑向回(huí)轉誤差的分離不確定度。
投稿箱:
如果您有機床行(háng)業、企業相關新聞稿件發表,或進行資訊合作,歡迎聯係本網編輯部, 郵箱:skjcsc@vip.sina.com
如果您有機床行(háng)業、企業相關新聞稿件發表,或進行資訊合作,歡迎聯係本網編輯部, 郵箱:skjcsc@vip.sina.com
更多相關信息
業界視點
| 更多
行業數據(jù)
| 更多
- 2024年11月 金屬切削機床產量數據
- 2024年(nián)11月 分地區金屬切削機床產量數據
- 2024年(nián)11月 軸承出口情況
- 2024年11月 基本型乘用車(轎車)產量數(shù)據
- 2024年11月 新能源汽車產量數據
- 2024年11月 新能源汽車銷量(liàng)情況
- 2024年10月 新能源汽車產量數據
- 2024年10月 軸承(chéng)出口情況
- 2024年10月 分地區金屬切削機(jī)床產量數據
- 2024年10月 金屬切削機床產量數據(jù)
- 2024年9月 新能源汽車銷(xiāo)量情況
- 2024年8月 新能源汽車產(chǎn)量數據
- 2028年(nián)8月 基本型乘用車(轎車)產量數據
博文選萃
| 更多