PCKF1825 可逆雙反擊錘式破碎機回轉部的優化設計
2020-4-3 來源:北(běi)方(fāng)重工富勒( 沈陽) 礦業有限公司 作者:趙冬博(bó) 李樂
摘(zhāi)要:針對 PCKF1825 可逆雙反擊錘式破碎機在實際投入使用後發現(xiàn)的諸多問題,進行了深入的研究和分析,運用 Solidworks 軟件對回轉部建立三維模型,優(yōu)化關鍵部件並對主軸進行仿真模(mó)擬校核,最終達到了(le)降低設備維護成本、延長部件(jiàn)使用壽命(mìng)、強化設(shè)備整體性能的(de)目的。
關鍵詞:可逆雙反(fǎn)擊錘式破碎機 回轉部(bù) 錘頭 錘盤 Solidworks 主軸
PCKF1825 可逆雙反擊錘式破碎機是一種新(xīn)型的破碎設備,回轉部是其關鍵部件,盡管該設備與傳(chuán)統 PC 型錘(chuí)式(shì)破碎(suì)機相(xiàng)比有諸多優勢,但在實際使用中也存(cún)在錘頭、錘柄組件更換率(lǜ)高,錘盤磨損嚴重(chóng)等(děng)問題,這給設備的使用效率和經濟效益帶來直接(jiē)影響。為解決上述問題(tí),運用 Solidworks 軟件對設備回轉部進行了優化設計和主軸校核。優化後的設備(bèi)在(zài)投入使用(yòng)後,提高了整體性能,滿足了設計(jì)和工作要求。
1、 PCKF1825 可逆雙反擊(jī)錘式破碎機
PCKF1825 可逆(nì)雙反擊錘式破碎機( 以(yǐ)下(xià)簡稱:PCKF1825 錘破) 破碎原理是物料通過錘頭組件的高速旋轉將其打擊,在經曆兩次破碎後進入主破碎腔,高速衝(chōng)向(xiàng)左右兩側的鋸齒形齒板,通過被錘頭和齒板的反(fǎn)複破碎,最後從(cóng)出料口排出,完成破(pò)碎。設(shè)備(bèi)主要由破碎機主體、電動機、液力偶合(hé)器及液壓站等組成。破碎機主體主要由中箱體、側箱體(tǐ)、底座部及回轉部組(zǔ)成。
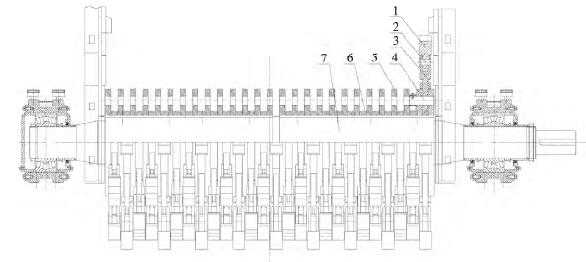
圖 1 原回轉部結構(gòu)示意
1—錘頭; 2—錘頭銷軸; 3—錘柄; 4—錘柄銷軸; 5—錘盤; 6—隔套; 7—主軸
回轉部( 見圖 1) 是整台設備的核心部分,主要由主軸、錘盤(pán)、錘頭組件及軸承座等組成(chéng)。其回轉部采用大轉子多錘頭,電機為高速度。同樣的電機功(gōng)率,當(dāng)轉子直(zhí)徑加大時(shí),其線速度加快,從而可加大打擊力度,提高破碎能力,節省能源。主軸的兩端支撐在軸承座(zuò)上,軸承選用(yòng)專用軸承,可自動調心,能承受(shòu)較大的動載荷和震動。軸上固定有許多錘盤(pán),在錘盤(pán)之間(jiān)通過錘柄銷(xiāo)軸連接(jiē)錘頭組(zǔ)件(jiàn),錘頭組件由錘頭、錘柄、錘頭(tóu)軸、錘柄軸(zhóu)等組合而成。錘頭采用了特(tè)種耐磨合金材料製成(chéng),安裝好(hǎo)的錘柄、錘頭可正反兩(liǎng)麵使用。回轉部是可(kě)逆的,當一側錘頭(tóu)與反擊板磨(mó)損過大時,可使轉子反向旋轉,利用(yòng)錘頭與反擊板的另一麵工作,盡可能的延長使用壽命。
2 、優化設計的必要性
盡管(guǎn) PCKF1825 錘破與傳統 PC 型錘式破碎機相比有諸多(duō)優勢,例如采用由特種耐磨合金(jīn)材料製造的鋸形齒板和(hé)錘頭,金(jīn)屬(shǔ)利用率高; 可逆的回部,具(jù)備高轉速、大破碎比、能耗低的性能,可以正反轉(zhuǎn)進行工作,提(tí)高了錘頭和齒板的利用率,延長了其使用壽命; 左、右箱體下部的偏心調(diào)節器使破碎腔內左右箱體同步變化,克服了分點調節因錯位而引起的同側箱體間(jiān)隙不均,保證出料(liào)細度均勻,提高(gāo)出料細度百分率等特點; 但在設備(bèi)實際投入使用後,尤其是在破碎鐵礦石的過程中,出(chū)現了以下問題:
( 1) 錘頭(tóu)組件磨損很(hěn)快。錘頭組件( 見圖 2) 是錘式破碎機最為關鍵的零部件之一,PCKF1825 錘破原設計所采用的是組合式的錘頭,由錘頭(tóu)、錘柄和銷軸等零件(jiàn)組成,其中(zhōng)錘柄是焊接件,是連接錘盤和錘頭的重要部件。盡管錘頭的材質是耐磨(mó)合金,在破(pò)碎物料過程中,尤其是破碎鐵礦(kuàng)石時,即便礦(kuàng)石硬度為中等硬度(dù),錘頭組件的(de)磨損率(lǜ)依然(rán)很高。按設備每天(tiān)平均工作 16 h 計算,大概 4 ~ 5 d 就要將 1台份( 共計 104 個) 錘頭組件全部更換 1 次(cì),更換至少需(xū)要 1 ~ 2 d。在更換的同時還需要對錘頭組件進行配裝,個(gè)別錘頭組(zǔ)件還需(xū)要打磨修整。
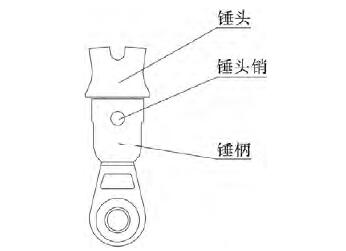
圖 2 原錘頭組件結構示意(yì)
錘頭組件磨(mó)損率過(guò)高的主要原因是錘柄,因為錘柄是焊接件,耐磨性不高,而其(qí)本身又是連(lián)接錘盤和錘頭的(de)主要部件,所以在破碎物料的過程中,錘柄(bǐng)的磨損在所難免,而且錘柄的過度磨損直接(jiē)影(yǐng)響(xiǎng)錘頭對破(pò)碎物料(liào)的(de)使用效率及性能,同時(shí)也無法給錘頭良好的支撐。尤其是當錘柄磨損率達到某一程度時,將無(wú)法固定和支撐錘頭,在轉子極大的慣性力(lì)作用下,錘頭很可能(néng)受到離心力的作用,脫離錘(chuí)柄,隨慣性飛(fēi)出(chū),在破碎機腔內不規則運動,對設備生產安全和使用壽命產生嚴(yán)重影響。此外,錘頭(tóu)的磨損使(shǐ)其有效的打擊麵積變小,在運轉中不能對物料進(jìn)行(háng)充分的打擊破碎和對錘盤及主軸進行有效的保護。
( 2) 錘盤磨損嚴重。對於磨損的問題不止於錘頭組件,錘盤的磨損也同樣存在,尤其是錘盤的外圓,PCKF1825 錘破破碎腔(qiāng)有(yǒu)效長度為 2 458 mm,在該跨度中均勻分布 27 個錘盤,錘盤(pán)直徑為 800 mm,單個錘(chuí)盤的厚度為 40 mm,兩個錘(chuí)盤(pán)之間圓周方向均布 4 個(gè)錘頭組件,整個回轉部的錘頭交叉(chā)排(pái)列。雖然設備運行時回轉部是高速運轉的,物料在破碎腔內受到錘頭的打擊破碎,但也有部分物料在(zài)受到打擊產生(shēng)反彈(dàn)之後會(huì)不規則(zé)的打擊到錘盤外圓,錘盤外徑與左、右箱體最小距離至少有 500 mm,給物料足夠的勢(shì)能(néng)和打擊空間,再加上物料被(bèi)打擊到齒板之後所產生的(de)反彈力,這對於普通(tōng)碳鋼材質的錘盤是極大的衝擊,尤其對(duì)錘盤外圓更是造成嚴重(chóng)的磨損。原設計(jì)並未充分考慮上述幾點,也未針對錘盤外圓(yuán)進行有效的耐磨保護,進而造成錘盤外圓磨損嚴重。原錘盤(pán)結構示意見圖 3。
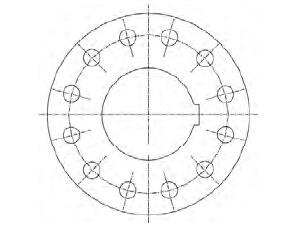
圖(tú) 3 原錘盤結(jié)構示意
3、 改進方式及優化設計
通過對上述問題的分析、研究與總結,決定對PCKF1825 錘破回轉部進行針對性的優化設(shè)計。在保證左、右箱體所組成的破碎腔(qiāng)空(kōng)間尺寸(cùn)不變的(de)情況下進行改進優化。
3. 1 錘頭的改進和優化設計
將原來的組合式錘(chuí)頭改為(wéi)一體式錘頭,取(qǔ)消不耐磨的焊接錘柄(bǐng)。同時,加大錘頭的外(wài)廓尺寸(cùn),增加破碎的有效麵積,提高錘頭整體的耐磨性,通過對鑄造工藝(yì)的(de)研究,在鑄造時加入磁性元素,使新型錘頭表麵呈弱磁性,這樣在(zài)破碎鐵礦石時,物料粉末就可被吸附在錘頭上,對錘頭進行有效的保護。通過(guò)理論設(shè)計和設(shè)備實際運行情況分析,新錘頭( 見圖(tú) 4) 采用整體鑄造結構,錘頭厚(hòu)度由(yóu) 90 mm增加到 110 mm,整體長度(dù)變短至 390 mm。將錘頭設計變短的原因主要是: 降低錘頭受到離心力和慣性力(lì)矩的影響,提(tí)高錘(chuí)頭的運轉安全性; 降低更換錘頭的時間和經濟成本。通過(guò)計算和 SolidWorks 模擬分(fèn)析,對錘頭的質量和打擊平衡中心進行了重新計算,同時保留原錘柄位(wèi)置(zhì)的限位塊設計,錘頭重量由39 kg 降至 29 kg。
改進後的錘頭外廓尺寸更大,破碎物料的有效麵積更(gèng)大,取消錘(chuí)柄、銷軸等零件,也避免了錘(chuí)柄的不耐磨(mó)和銷軸因受到循環應力而產生鬆(sōng)動或斷裂[1]。使錘頭的耐磨性、安全性、使用壽命都有所(suǒ)提高,同時對(duì)錘盤也起到了更好(hǎo)的保護作用。
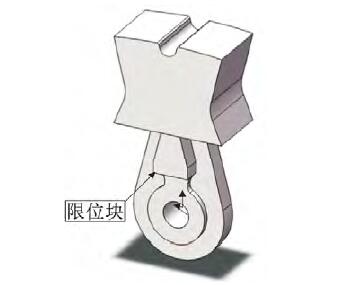
圖 4 改進後錘頭(tóu)結構示意
3. 2 錘盤的改(gǎi)進和優化(huà)設計
在回轉(zhuǎn)部整體外徑保持不變的基礎上,由於錘頭整體(tǐ)變短,所以錘盤外徑相應增加,由 800 mm增加到 1 125 mm,進一步(bù)減小了物料在破碎腔內對錘盤的打擊空間,使物料在(zài)更合理的破碎腔空間內被高(gāo)效破碎。改(gǎi)進後的左、右兩端的(de)錘盤( 見圖5) 厚度由 40 mm 變為 45 mm,中間錘盤( 見圖(tú) 6) 厚度由 40 mm 變為 33 mm,圖 5、圖 6 中錘盤圓周黑(hēi)色邊緣部分是在錘盤外圓堆焊耐(nài)磨層[2],堆焊厚度約為 5 mm,目的是為了(le)保護錘盤,提(tí)高耐磨性。
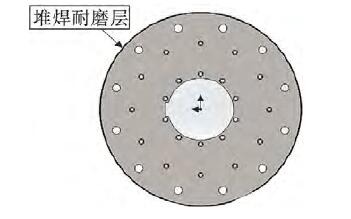
圖 5 端部錘盤結構(gòu)示意
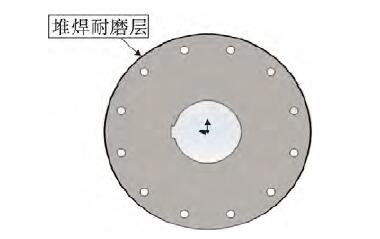
圖 6 中間(jiān)錘盤結構示意
3. 3 回轉部整體改進和優化設計
在對回轉部兩個主要零件改進(jìn)後,再(zài)將錘盤、錘頭進行重新布置,由於錘頭的外廓尺寸加大,錘盤的厚度也有所變化,所(suǒ)以在(zài)保證主軸整體裝配長(zhǎng)度(dù)不變的情況下,將錘盤間距由 53 mm 變為 61 mm,錘盤總數由原來的 27 件/台變為 26 件/台,錘頭數量由原(yuán)來的 104 件/台變為(wéi) 100 件/台。其次,由於錘盤外徑的增大,在裝(zhuāng)配過程中,為保證各錘盤之間的間(jiān)距(jù)及垂(chuí)直度,在每兩個錘盤之間增加 1 個支撐隔套。支(zhī)撐隔套的固定方式是將隔套一端(duān)采用斷續焊的(de)方式與錘盤焊成一體裝配在主軸(zhóu)上[3]。改進(jìn)後的回轉(zhuǎn)部結構示意見圖 7。
3. 4 利用 Solidworks 校核主軸
在對回轉部優化設計後,雖然整體結構形式變化不大,但主要零部(bù)件(jiàn)的尺寸、重量、數量等參數均有所(suǒ)改變,這(zhè)些參數的改變對主軸的強度產生了一定的影響,使主軸承受的總(zǒng)載荷有所增加。原回轉部主(zhǔ)軸(zhóu)上承載的部件總重為 8 143 kg,改進後總重增 加(jiā)至9 583 kg ,總 載荷增加 了約18 個百 分 點 。
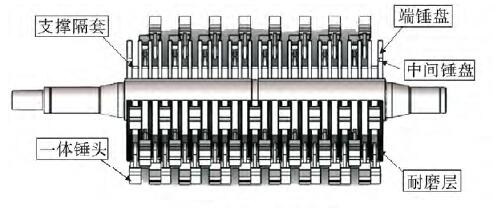
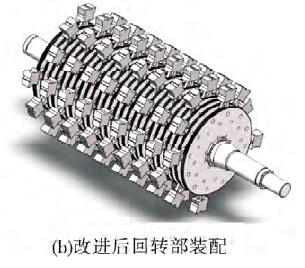
圖 7 改進後(hòu)的回轉部結(jié)構示意
運用 Solidworks 對主軸進行模擬分析,在固定主軸兩端軸承座位置的圓柱麵後,對主軸的主要承載表麵均布施加 一 個 100 kN 的 外部 載荷,然 後通 過Solidworks 對主軸進行強度運算得出結果。運算主要考察主軸的應力、位移及應變情況,看其是否仍滿足設計(jì)要求。運算結果見圖 8。由運(yùn)算結果可知,主軸的最大應力為4. 56 MPa,最大位移量為 0.011 mm,最大應變為1.3 × 10- 5。由於主軸材質為 45 號鋼,調質後的抗拉強度為 590 MPa,根據軸的材質和抗拉強度,查詢機(jī)械設計手冊[4]得其許用應力為 95 MPa。主軸的(de)最大應力遠小於其許用應力,最大位移和最大應變對主軸及回轉部的(de)整體影(yǐng)響也極小,基本可忽略不計,故主軸仍滿足設計和工作(zuò)要求(qiú)。
4、 結 論
( 1) 通過對 PCKF1825 可逆雙反擊(jī)錘式破碎機回轉(zhuǎn)部的性(xìng)能(néng)研究(jiū),結合設備在實際運行(háng)中回轉部錘頭、錘盤等部件出現的問題(tí),運用 Solidworks 三維軟件建立模型,對回轉(zhuǎn)部、錘頭、錘盤進行結構分析和優化設計,對改進後主軸重新校核,確認仍滿足設計和工作要求。
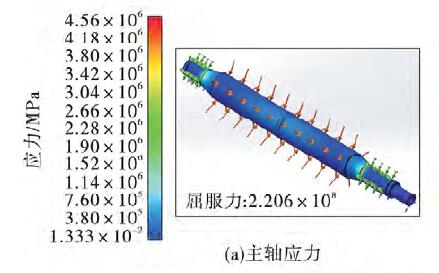
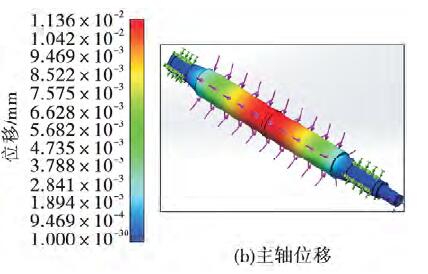
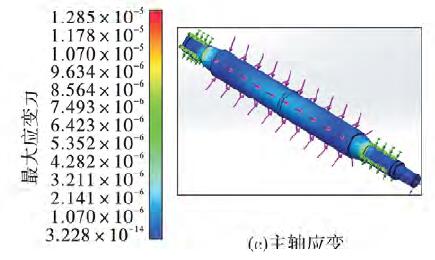
圖 8 主軸強度校核(hé)
( 2) 采用一體化高(gāo)強度(dù)錘頭、錘盤堆焊耐磨層等設計方案使部件的耐磨性和抗衝(chōng)擊性均有(yǒu)很大(dà)改(gǎi)善,提高了 PCKF1825 可逆(nì)雙反擊錘式破碎機(jī)的技術性能。
( 3) 據現場實際(jì)應用(yòng)情況反饋,改進(jìn)後(hòu)錘頭平均使用壽命由 5 d 增至近 20 d,錘盤磨損情(qíng)況有了(le)根(gēn)本性改善,更換錘頭的次數和更(gèng)換時(shí)長也明顯降低,設備運行時間和使用效率明顯提(tí)高,降低(dī)了維護(hù)成本和(hé)更換部(bù)件所產生的費用,提高(gāo)了經(jīng)濟效益。
投稿箱:
如果您有機床(chuáng)行業、企業相關新聞稿(gǎo)件發表,或進行資訊合作,歡迎聯係本網編輯部, 郵箱:skjcsc@vip.sina.com
如果您有機床(chuáng)行業、企業相關新聞稿(gǎo)件發表,或進行資訊合作,歡迎聯係本網編輯部, 郵箱:skjcsc@vip.sina.com
更多相關信息
業界視點
| 更多
行(háng)業數據
| 更多
- 2024年(nián)11月 金屬切削機床產(chǎn)量數(shù)據(jù)
- 2024年11月 分地區金屬切削機床產量數據
- 2024年11月 軸承出口情況
- 2024年11月 基本型乘用車(轎車)產量數據
- 2024年11月 新(xīn)能源汽車產量數據
- 2024年11月 新能源汽車銷量情況
- 2024年10月 新能源汽車產量數據
- 2024年10月(yuè) 軸承出口情況
- 2024年10月 分地區(qū)金屬切削機床產量數據
- 2024年10月(yuè) 金屬切削(xuē)機床產量數據
- 2024年9月 新能源汽(qì)車銷量情況
- 2024年8月 新能源汽車產量數據
- 2028年8月 基本型乘用(yòng)車(轎車)產量數據
博文選萃
| 更(gèng)多