變速箱齒座加(jiā)工(gōng)工藝優化
2019-6-20 來源:東風(十堰(yàn))發動機部件有(yǒu)限公司 作者:房遠奇
摘要(yào): 針對變速箱齒座加工(gōng)中(zhōng)存在的缺陷(xiàn),通過(guò)改善內孔加工方法、攻克質量風險點及優化加工參數等(děng)改進措施,達(dá)到了優化工藝、解決問題的目的。
我公司(sī)目前加工的零件以鑄鐵件為主(zhǔ)。若根據現有的加工條件來完成相對高精度的鋼件加(jiā)工,無法在有效的成本控製(zhì)範圍內來完成相應的生產。依照現有的刀具、夾具對鑄鋼材質的齒座(zuò)進行(háng)加工驗(yàn)證後(hòu),無論(lùn)是加工節拍、加工質量,還是工藝(yì)流(liú)程的繁複程度,都不能(néng)滿足低成本的要求。
通過對內(nèi)孔孔徑進行改善,對質量風險點進行攻關,對加工參數進行優化等一係(xì)列措(cuò)施,達到了工藝流程的優化,降低了生產成本,提高(gāo)了產品質(zhì)量。
1. 產品結構和技術要求
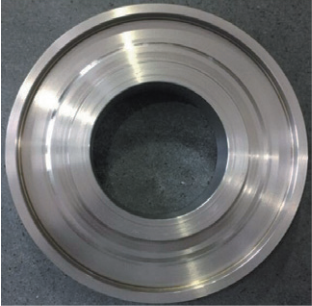
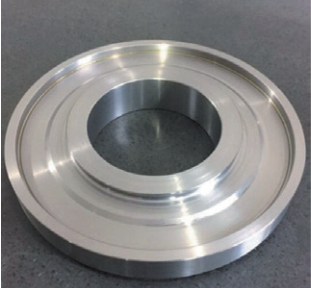
圖 1 產品結構
變速箱齒座零件為盤類結(jié)構(見圖1),材料為鑄鋼(DFS5218SH2),硬度為150~190HBW。產品技術要求如圖2所示。
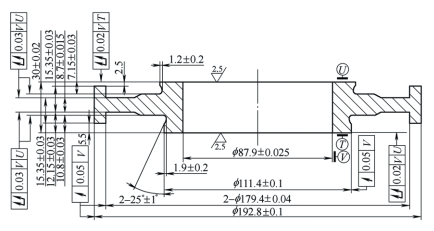
圖 2 產品技術要求
2. 加工工藝
考慮到零件尺寸鏈(liàn)關係比較複雜,以及尺寸精(jīng)度大部分都在0.05mm以內,在試加(jiā)工階段采用的是粗、精工(gōng)序分開加工完成,具體流程如表1所示。
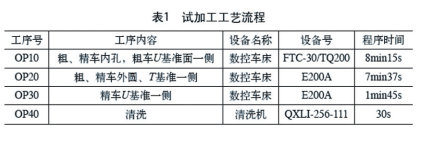
3. 孔徑(jìng)加(jiā)工變形問題
零(líng)件中心孔在OP10序中完成,定(dìng)位方式是基準T麵定(dìng)位和夾緊外圓夾緊(見圖3)。中心孔孔徑為φ(87.9±0.025)mm,孔徑深度32.7mm。在實際(jì)加工過程中發現孔徑存在圖1產品結構喇叭(bā)口的問題。進刀口直徑與出(chū)刀口(kǒu)直徑相差0.01~0.04mm,尺寸不穩(wěn)定。
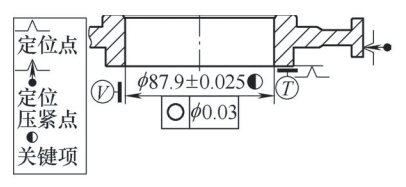
圖 3 OP10 定位方式
經分析,主要(yào)可能存在如下問題:①夾緊變形。卡爪夾(jiá)緊壓力導致(zhì)孔徑存在應力(lì)消除後的變化,或者外圓夾緊位置偏低導致零(líng)件抬起。②刀具讓刀。刀柄直徑過(guò)小導致零件在切削時讓刀。③餘量過大。精車餘量偏大導(dǎo)致加工時讓刀。④應力未消除。鋼(gāng)件零件自身材質偏軟,加工後,零件因(yīn)為應力(lì)消失而部分還原。針(zhēn)對這些問題,采取了如下改(gǎi)善措施:
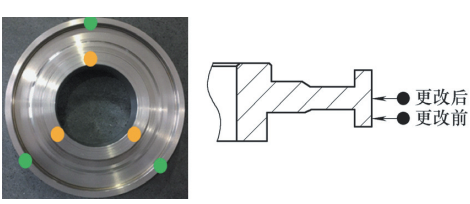
圖 4 定位(wèi)點、壓緊(jǐn)點更改位置
(1)更改定位點和(hé)夾緊點(見圖4)。首先,更改T基準麵上(shàng)的定位點,增加支撐點之間的距離,從而(ér)增加(jiā)支撐的穩(wěn)定性;其次,更改卡爪(zhǎo)夾緊點的位置,將卡爪從外圓的靠邊(biān)位(wèi)置更改到中間位置(zhì),以便(biàn)使零件的受力(lì)是(shì)在零件主體上;最後,對卡爪壓力作出適當調整。
(2)將目前使用的φ25mm刀(dāo)杆更換成φ30mm刀杆,並將刀片換成鋼(gāng)件專用刀片(piàn)(刀片的後(hòu)角更大),更有利於切屑的切斷和排出。
(3)變(biàn)更(gèng)餘量試驗中,發現鑄(zhù)鋼件(jiàn)不同於鑄鐵件的加工,不是精車餘量越小越好。鋼件精車餘量越小,零件表麵外觀質量反而(ér)越差,存在無規則的花紋。雖然尺寸沒有什麽影響,但是外觀(guān)很差。多(duō)次驗證後發現(xiàn),將精車餘量控製在0.15~0.25mm為最(zuì)佳。最後(hòu)以滿足質量為前提,將精(jīng)車(chē)餘量確定為0.2mm,從而放棄在精車餘(yú)量上的再次變動。
(4)在上述三點(diǎn)改善措施均完成之後,進行連續性(xìng)的小批量驗證。先采(cǎi)集加工後的數據(jù),然後將零件進行時效處理,之後(hòu)再複測采(cǎi)集數據。依照前後兩次采集的數據進行對比分(fèn)析,發現以(yǐ)下兩點:①喇叭口(kǒu)現象依然存在。②進出口尺寸相對穩定,有一定的規(guī)律性,而不再是雜亂無(wú)章。
進出口直徑相差均值為0.015mm。根據以(yǐ)上分(fèn)析和試驗,在加工穩定的情況下,從程序上進行修改,使出口直(zhí)徑比進口直徑大0.015mm。後續試驗證明,該方法不僅滿(mǎn)足了孔徑的要求,而(ér)且還通過了CPK大於1.33的驗(yàn)證(見圖(tú)5)。
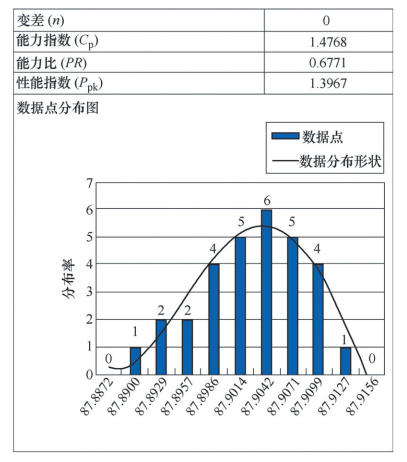
圖 5 數據(jù)點分布及過程能力值(zhí)
4. 清根問題
根據圖樣要求,零件有4處需(xū)要清根,而(ér)且相關尺寸控製也比較嚴格。
四處清根部分,最大加工餘量1.9mm,最小加工餘量(liàng)0.5mm。根據圖樣要求以及機床刀位的控製,A、B兩處隻能(néng)選用主偏角>90°、副偏角>25°的車刀,C、D兩處隻(zhī)能(néng)選用主偏角>112°、副偏角>0°的車刀。
在(zài)實際加工中,隻有C、D兩處刀具能夠走軌跡一次(cì)加工(gōng)成(chéng)形(xíng)。而A、B兩處主偏角過大,理論上一次切削量不能(néng)太大,否則會存在崩刃的(de)風險。實際加工驗證存(cún)在崩刃、纏屑、“噎刀(dāo)”和外觀不良等諸多問題,隻能采取分量多次(cì)加工(見圖6)。後續加工驗證,雖(suī)然軌跡走刀加工出了輪廓,但在軌跡接(jiē)口的位置仍然存在一個(gè)目測可視的台階(見圖6左側黑點處(chù)),無法步判定台階與切屑排(pái)除不及時有關。經過(guò)多次試驗驗證和改良, 將等(děng)量切削的餘量改為由大變小地進行切削, 使刀具在切削軌跡(jì)將近完成時, 切屑量減少而使切屑崩斷。 最終完美地解決了問題。
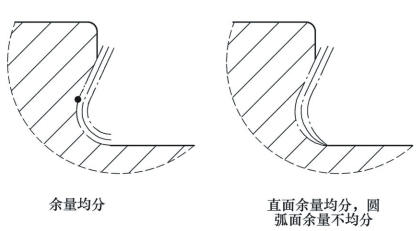
圖 6 走刀軌跡變更對比
5. 加工參數優化(huà)
在樣(yàng)件試製階段, 雖然已經參考(kǎo)現有的刀具和刀具加工參數經驗, 也(yě)采用了一部分鋼(gāng)件專用刀具, 但是在實際生產中, 仍然存在切屑纏繞嚴重(見圖 7b) 、 換刀頻次偏低以及零(líng)件表麵外(wài)觀差(chà)(見圖(tú) 7a) 等(děng)諸多(duō)問題(tí)。 而且加工時間(見表 1)始終無法再次提升。
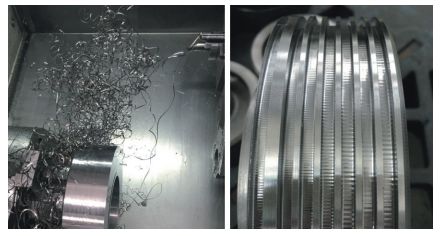
圖7 b 圖(tú)7a
在無法滿足廠家指定成本和產能輸出的(de)情況下, 對刀具進行了更換(huàn), 對加工參數進行了修改(gǎi)。加工參數和(hé)程序優化後, 零件表麵和斷屑得到了(le)很(hěn)好的改善。 同時換刀(dāo)周期也有明(míng)顯的改善。對參數進行更改(見表 2) 後, 纏繞切屑變成了 3~5mm 的卷狀切屑且自然斷裂, 零件表麵不規則光亮帶(dài)也消失了。
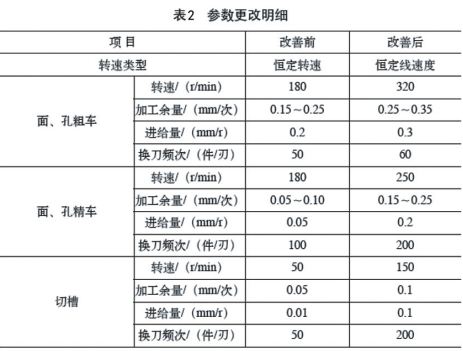
6. 工藝流程優化
通過以上改進措施, 提高了產品質量, 且產品質量穩定, 加工效率得到了提升, 最(zuì)終根據改圖 6 走刀軌跡變更對比善(shàn)後(hòu)的實際情況, 對工藝流程(chéng)重新進行了布置和規劃, 避免了部分零(líng)件多次定位造(zào)成的磕碰(pèng)以及工序不必要的加長。 具體的工序變更情況如表 3所示。
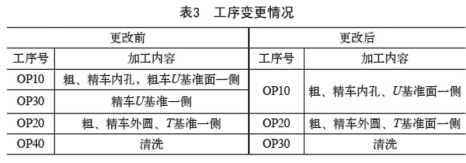
7. 工藝優化效果
在完成孔徑變(biàn)形、 清根纏屑外觀不良、 刀具及參數提速不明顯、 工藝優化等幾個問題的整改和改善之後, 對齒座的質量、 工藝節拍和成本等有了一定的控製和優化, 減少了該零件(jiàn)的製造成(chéng)本, 從而以更優(yōu)的質量和市場價格來麵對市場的需求和(hé)變化(huà)。
8. 結語
從開始調試到中期各種問(wèn)題點的解決, 到後(hòu)期的工藝(yì)流程優化, 一環扣一環。 初期(qī)問題的及時(shí)發現, 中期問題的及時改善, 後期(qī)工藝的及時優化、 固(gù)化, 都為齒座加工質量的成功改善提(tí)供了(le)動力。
工藝的優化都是在市場需求情況下一步步地發現、 改善、 提升、 優化、 再發(fā)現……, 處於不斷循環之中。 隻有不停地改善提(tí)升, 才能更好(hǎo)地適應市場的需求和衝擊, 才能在未來的市場中站穩腳(jiǎo)跟。
投稿箱:
如(rú)果您有機床行業、企業相關新聞稿件(jiàn)發表,或進行資(zī)訊合作,歡迎聯係本網編輯部, 郵箱:skjcsc@vip.sina.com
如(rú)果您有機床行業、企業相關新聞稿件(jiàn)發表,或進行資(zī)訊合作,歡迎聯係本網編輯部, 郵箱:skjcsc@vip.sina.com
更多相關信息
業界視點
| 更多
行業數據(jù)
| 更(gèng)多
- 2024年11月 金屬切削機床產量數據
- 2024年11月 分地區金屬切削機(jī)床產量數據
- 2024年11月 軸承出口情況
- 2024年11月 基本型乘用車(轎車)產量數據
- 2024年11月 新(xīn)能源汽(qì)車產量數據
- 2024年(nián)11月(yuè) 新能源汽車銷量情況
- 2024年10月 新能源汽車產量數(shù)據
- 2024年10月 軸承出口(kǒu)情況
- 2024年10月 分地區金屬切削機床(chuáng)產量數據
- 2024年10月 金屬切削機床產量數據
- 2024年9月 新能源汽車銷量情況
- 2024年8月 新能源汽車產量數據
- 2028年(nián)8月 基本型乘用車(chē)(轎車)產量數據
博文(wén)選萃
| 更多
- 機械(xiè)加工過程(chéng)圖示
- 判斷一台(tái)加工中心精度的幾種辦法
- 中走絲線切割機床的發(fā)展(zhǎn)趨(qū)勢
- 國產數控係統和(hé)數控機床何去何從?
- 中國的技術工(gōng)人都去哪裏了?
- 機(jī)械(xiè)老板(bǎn)做了十多年,為何還是小作坊?
- 機械行業最新自殺性營(yíng)銷,害人(rén)害己!不倒閉才
- 製造業大逃亡
- 智能(néng)時代,少談點智造,多談點製造
- 現實麵前,國人沉默。製造業的騰(téng)飛,要從機床(chuáng)
- 一文搞懂數控車床加工刀具補償功(gōng)能
- 車(chē)床鑽孔攻螺紋加工方法及工裝設計(jì)
- 傳統鑽削與螺旋(xuán)銑孔加工工藝的區別