高速微銑(xǐ)削鋁合金銑削力與表麵粗糙度(dù)研究
2015-12-29 來源:長春理工大學 機電工程學院 作(zuò)者:張欣欣,於化東,許金凱,楊舒
摘要: 隨著航空(kōng)航天技術的發展,微(wēi)小零部件變得越(yuè)來越重要,對(duì)製備具(jù)有表麵質(zhì)量好、尺寸(cùn)精度高、加工誤差(chà)小的微機械結構提出了(le)新的挑戰。通過高速微銑削技(jì)術在 7075 航空係列鋁(lǚ)合金表麵銑削微細直(zhí)槽結構,以主軸轉速、進給速度(dù)與(yǔ)軸向切深為研究因素(sù),采用多因素(sù)正交試驗與極差、方(fāng)差(chà)分析法分別對銑削力和表(biǎo)麵粗糙(cāo)度進行研究。結果表明:銑(xǐ)削參數對銑削(xuē)力的影(yǐng)響按從大到小依(yī)次為進給速度、軸向切深、主軸轉速;增大(dà)主軸轉速,減小進給速度和軸向切深可獲得較小(xiǎo)的(de)銑削力(lì)與較高的加工精(jīng)度;主軸轉速對表麵粗(cū)糙度 Ra 影響最大,進給速度次之(zhī),軸向切深對其(qí)影響最小;當主軸轉速為 48000r/min,進給速度為(wéi) 30mm/min,軸向切深為 20μm 時,高速微銑削鋁合金微細直(zhí)槽(cáo)表(biǎo)麵質量最優。
關鍵詞: 高速微銑(xǐ)削(xuē);正交試驗;銑削力;表麵粗糙度
0 引言
隨著航空航天、生物、醫學、建築、以及汽車製造業的(de)發展,對(duì)微小機械的功能、結(jié)構複雜性、可(kě)靠性的要求越來(lái)越高,從而對加工具有一(yī)定尺寸精(jīng)度和表麵質(zhì)量要求的精密三維微小零部件的需求(qiú)也越來越廣(guǎng)泛。高速微銑削(xuē)技術以其加工(gōng)精度高、工藝簡(jiǎn)單、材料約束少、加工效率高,可實現複雜形(xíng)狀三維(wéi)微小結(jié)構的加工等優點在國內外得到了大量應用。
近年來,鋁合(hé)金(jīn)材料由於其塑性好、強度高、重(chóng)量輕以及具(jù)有優良的導電性、導熱性(xìng)和抗腐蝕性等(děng)特性被廣泛地應用(yòng)於航空航天製造領域中。為減少(shǎo)飛機的重量和提高其使用性能, 在飛機結構設計中大量采(cǎi)用(yòng)鋁合金製備梁(liáng)、肋、桁條、隔框、整體框架和起落架等結構,但是,這類結構件的(de)剛度較低,對於低剛度的複雜構(gòu)件,加(jiā)工時由(yóu)於切削力、切(qiē)削熱以及主軸(zhóu)跳動等原因(yīn)很容易發生變形,嚴重(chóng)的影響了(le)工件的加工質量和表麵精度(dù)。因此要提高低剛度構件的加工質量與精度,就要減小工件在加工過程(chéng)中的(de)變(biàn)形。經過大量分析得出切削力是引起加工變形的一個主要原因,因此減小切削力就可以有效減小低剛度構件(jiàn)的加工變形。李豔聰等采用直徑為 16mm 的銑刀對不鏽鋼、鋁合金的平麵加工精(jīng)度進(jìn)行了研究(jiū),得出(chū)了切削力(lì)與切(qiē)削參數的關係。但(dàn)是,對於微米(mǐ)級結構件銑削力的研究卻很少。本文采用直徑為 0.2mm 的微(wēi)徑銑刀在鋁合金表麵加工微細直槽(cáo)結構,采用正交試驗研究銑削參數對銑削力與表麵粗糙度的(de)影響規律並進行參數優化,最終得到最優銑削參(cān)數使加工表麵質量最優。該研究為獲得表麵質量好、尺寸精度高的微小零部件的高速銑削加(jiā)工提(tí)供了依據。
1 試驗研究
1.1 試驗條(tiáo)件
該銑削(xuē)試驗采用課題組自行研製的(de)小型高速微銑削機床,主軸最高轉速可(kě)達(dá) 100000r/min,主軸回轉精度為 1μm,工作(zuò)台位置精度為 ± 0.5μm/100mm,重複定位精度為 ± 0. 2μm;采用 Kistler 三向動態壓(yā)電測力儀、5070A 電荷放大器和計算機數據采集係統(tǒng)測量與(yǔ)記錄銑削力;利用(yòng) MarSurf LD120 輪廓與(yǔ)粗糙度測量儀測量微細直(zhí)槽底麵(miàn)的粗糙度;刀具選用雙刃整體硬質合金塗層微徑立銑刀(dāo),刀柄和刀刃直徑分別為 4mm 和0.2mm,刃長為 0.5mm,螺旋角為 45°,刀尖圓(yuán)弧半徑為 10μm,塗層材(cái)料為 TiAlN;工件(jiàn)材料為 7075 航空係列鋁合金;銑削(xuē)加工過程中采用油霧潤滑與冷卻。圖
1 為銑削力(lì)測試係統原理圖(tú)。
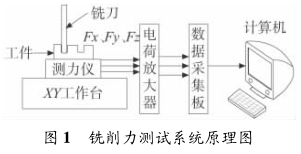
1.2 試驗方法
在 5052 鋁合金表麵加工微細(xì)直槽結構如圖 2 所示,采用全(quán)徑向銑削方(fāng)式,即直槽寬度與銑刀直徑相等。選取主軸轉速 n、進給速度 vf、軸向切(qiē)削(xuē)深度 ap三個參(cān)數作為研究因素,采用(yòng)三因素四水平正交試驗表L16(43)研究銑削參數對銑削力和表麵粗(cū)糙(cāo)度的影響規律,通過極(jí)差與方差分析法得到銑削力和(hé)表麵粗糙度較小的因素水平組合。正交試驗各因素的水平值根據試驗經驗選取,如表(biǎo) 1 所示。
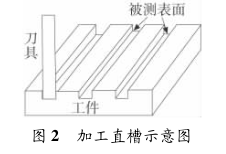
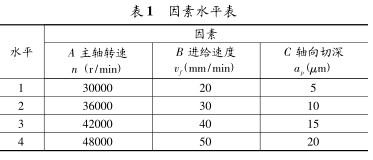
2 試驗結果與分(fèn)析
正交試驗方案與極差分析結果如表 2 所(suǒ)示,方差(chà)分析結果如表 3 所示,每組參數重複進行三次,對本試驗中測得的銑削(xuē)力數據進行噪音去除處理,其中 Fx、Fy、Fz 為銑削力在 X、Y、Z 三個方向的分力,Ra為直槽底部的表麵粗糙度。根據表 2 中所測的各銑(xǐ)削分力值可以看出,高速微銑削鋁合(hé)金微細直槽時所產生的銑削力都很小,Fx 最大為 0.063N,Fy 最大為 0.099N,Fz最大為 0,076N。
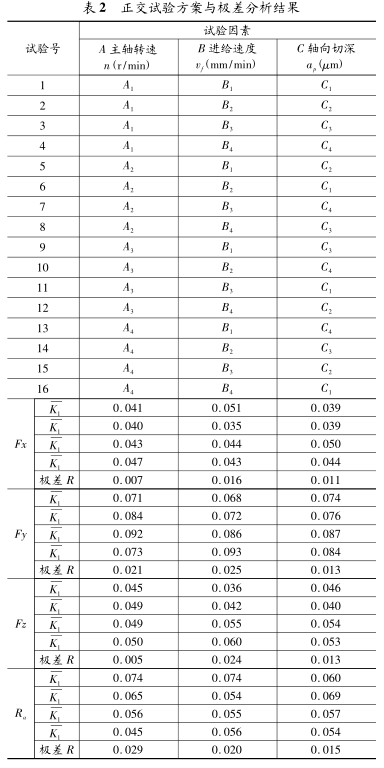
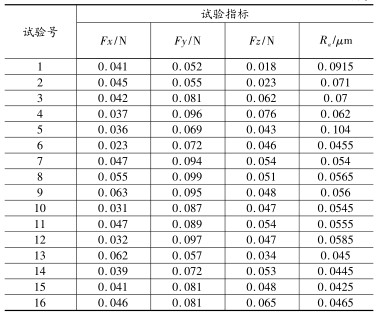
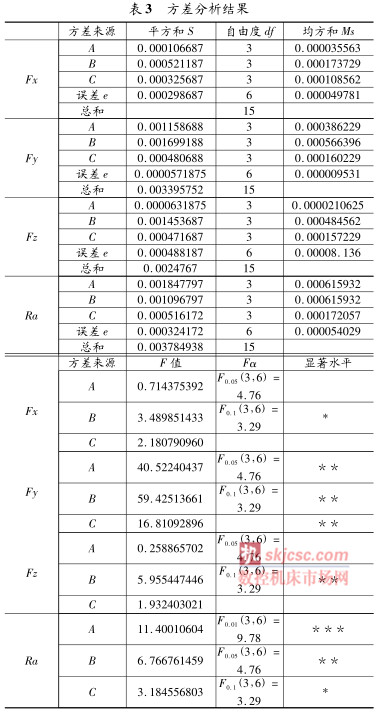
2.1 銑削力分析
圖3 為采用 MATLAB 軟件由極差(chà)分析結果(表 2)生成的銑(xǐ)削(xuē)參數與(yǔ)各銑(xǐ)削分力的關係曲線圖。從圖(tú)中可以看出,銑(xǐ)削分力 Fy 最大、Fz 次之、Fx 最小。由方差分析結果(表3)可知,銑削參數對銑削分力的影響存(cún)在明顯差異,各參數對主切(qiē)削力 Fy 影響(xiǎng)最大,軸(zhóu)向力 Fz次之,徑向力 Fx 影響(xiǎng)最小。銑削(xuē)時(shí),由於切削變形與摩擦,銑刀每一參與切(qiē)削的(de)刀齒上(shàng)都受到銑削力。為了實際應用,通常假定各刀齒上的(de)銑削(xuē)力的合力 F 作用於某個(gè)刀齒上(shàng),並(bìng)將它分解為三個相互垂直的分力:主切削力 Fc 、徑向力 Fp、軸向力 Fo[銑削分力 Fx、Fy、Fz可近似等同於三個相互垂直的分力,即 Fx 對(duì)應(yīng)於徑向(xiàng)力 Fp、Fy 對應於主切削力 Fc、Fz 應於軸向力 Fo。主切削(xuē)力 Fc(Fy)是主運動切削速度方向的分力,是最大的一個分力,它消耗了切削總功率的 95% 左(zuǒ)右(yòu),是設計與使用刀具的主要依據,並用於驗算機床、夾具等主要零部件的強度(dù)和剛(gāng)度以及機床電(diàn)動機功率。軸向力 Fo(Fz)是軸向切深(shēn)方向的分力,消耗了總功率的 5% 左右,是驗算(suàn)機床進給係統主(zhǔ)要零部件強度和(hé)剛性的依據。徑向力 Fp(Fx)是進給方向的分力,它不消耗功率,但在機床、工件、夾具與刀具所組成的工藝係統剛性(xìng)不足時,是造成振動的(de)主要因(yīn)素。所以,各銑削分力按(àn)大小順序排列(liè)依次為 Fy >Fz >Fx。
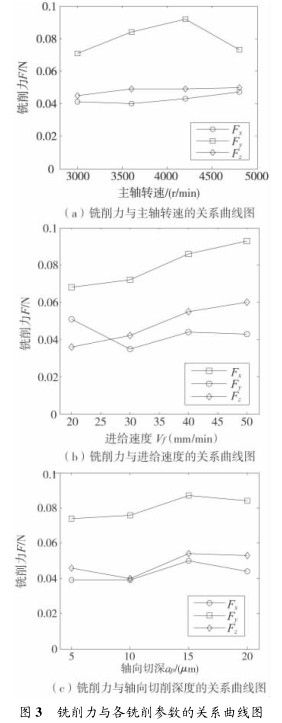
從圖(tú) 3a 中還可以看出,Y 方向的銑削力隨著主軸轉速的增大呈開口向下的拋物線分布,隨著主軸轉速的增大而增大(dà),在 n =42000r/min 時,銑削力達(dá)到最大值 0.092N,當 n > 42000r/min 時,Fy 隨(suí)著主軸轉速的繼續增(zēng)大而減小;主軸轉速對銑削分力 Fx、Fz 的影響波動不大,整體呈緩慢上升趨勢,即隨著主軸(zhóu)轉速的增大而緩(huǎn)慢增大;由圖 3b 可知,銑削分力 Fy 與 Fz 的變化趨勢相似,都隨著進給速度的增大而增(zēng)大,而銑削分力 Fx 呈二次(cì)曲線分布,即隨著進給速度的(de)增大,先減小後增大,最後又(yòu)減小(xiǎo);由圖 3c 可以看出,銑削分力Fx、Fy、Fz 的(de)變化趨勢相似,都呈拋物線分(fèn)布,在 ap=15μm 時,銑削力同時達(dá)到最大值,但當 ap< 10μm 時銑削分(fèn)力 Fx、Fy 隨著軸向切深的增大而增大,而(ér) Fz 正好相反(fǎn),隨著軸向切深的(de)增大而減小, 當 ap> 10μm時, 三者的變化趨勢相同。
由極差和方差分析結果(表 2 與表(biǎo) 3)及圖 3 可知,進給速度對銑削力的影響最大,軸向切(qiē)深次(cì)之,主軸轉(zhuǎn)速最小(xiǎo);並且提高主軸轉速,減小進給速度和軸向切深既可以獲得較小的銑削(xuē)力(lì)又可以得到較高(gāo)的加工精度。
2.2 表麵粗糙(cāo)度分析
由表 2 與表 3 可以得出銑削參數與(yǔ)表麵粗糙度 Ra的變化趨勢,如圖4 所示。從圖中可以得(dé)出銑(xǐ)削參數對(duì)表麵粗糙(cāo)度(dù) Ra的影(yǐng)響規律:隨著(zhe)主軸轉速的(de)增大表麵粗糙度減小,分(fèn)析其(qí)原因,其它加工參數不變時,高主軸轉速下的切(qiē)屑與刀具前刀麵發生(shēng)局部融化,形成一(yī)層保護膜(mó),大大的減小了刀具前(qián)刀麵的磨損和變形,同時也減小了切屑的變形時間(jiān),切屑快速的被(bèi)切離工件並帶走了70% ~80%的切削熱,有效的減小(xiǎo)了切削力;隨著進給速度的增大表(biǎo)麵粗糙度先(xiān)減小後增大(dà),這說(shuō)明並不(bú)是采用越(yuè)小的進給量得到的表麵質量越好,分析其原因可能是刀具與工件之間(jiān)的摩擦力和(hé)擠壓力造成的,在vf=30mm/min 的時後,表麵(miàn)粗糙度達到最小值 0.054μm;從圖中(zhōng)還可知軸向切深與進給速度的變化趨勢正好相反,隨著軸向切削深度的(de)增加,表麵粗糙度先增(zēng)大後(hòu)減小,在 ap=20μm 時,表麵粗糙度最小(xiǎo),這可能是由於最小切削厚度 12- 15 效應引起的,當每齒(chǐ)進給量小於刀尖(jiān)圓弧半徑時(shí)無切屑(xiè)產生,工件發生彈性變形並產生犁耕現(xiàn)象,使(shǐ)表麵粗糙度增(zēng)大。
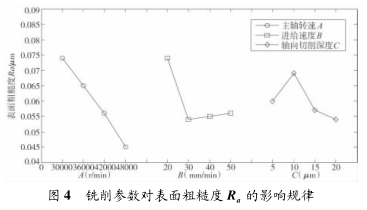
根據極(jí)差與方差分析法可知,銑削參數(shù)對表麵粗糙(cāo)度(dù)的影響程度按從大到小(xiǎo)依次排列為主軸轉速、進給速度、軸向切削深度。根(gēn)據極差分析法可以求出最優組(zǔ)合為 A4B2C4,即 n = 48000r/min,vf= 30mm/min,ap=20μm 時,表麵粗糙度最小,加工表麵質量最好。
3 結論
通(tōng)過多因素正交試驗分析直徑(jìng)為 0.2mm 的微徑銑刀銑削鋁合金時的切削力與表麵粗糙度,可以得出以下結論:
(1)對銑削力影響最大的試驗因素是進給速度,其次(cì)是軸向切深,主軸轉速對銑削力影響最小。
(2)提高主軸轉速,減小進給速度和軸向(xiàng)切(qiē)深可以獲得較小的銑削力(lì)和較高的加工精度。
(3)各銑削參數對銑削(xuē)分力的影響存在明顯差異,各(gè)參數對主切削力 Fy 影響最大,軸向力 Fz 次之,徑向力 Fx 影響最小,且各銑削(xuē)分力按大小排列依次為:Fy > Fz > Fx。
(4)銑削參數對表麵粗糙度的影響(xiǎng)程度從大到小依次為主軸轉速(sù)、進(jìn)給速度、軸向切深。
(5) 當主軸轉(zhuǎn)速為 48000r/min,進(jìn)給速度(dù)為30mm/min,軸向切深為 20μm 時,高速微銑削鋁合金微細(xì)直槽表麵加工質量最優。
投稿箱:
如果您有機床行(háng)業、企業(yè)相關新(xīn)聞(wén)稿件(jiàn)發表,或(huò)進(jìn)行資訊合作,歡迎聯係本(běn)網編輯部, 郵箱:skjcsc@vip.sina.com
如果您有機床行(háng)業、企業(yè)相關新(xīn)聞(wén)稿件(jiàn)發表,或(huò)進(jìn)行資訊合作,歡迎聯係本(běn)網編輯部, 郵箱:skjcsc@vip.sina.com
更多相關信息
業界視點
| 更多
行業數據
| 更多
- 2024年11月(yuè) 金(jīn)屬切削機床產量數據
- 2024年11月 分地(dì)區金屬切削機床(chuáng)產量數據
- 2024年11月 軸承出口情況
- 2024年11月 基本型乘用車(轎車)產量數據
- 2024年11月 新能源汽車產量(liàng)數據
- 2024年11月 新能源汽車銷量情(qíng)況
- 2024年10月 新能源汽車產量數據
- 2024年10月 軸承出口情況
- 2024年10月 分地區金屬切削機床產量數據
- 2024年10月 金屬切削機床產量(liàng)數據
- 2024年9月 新能源汽(qì)車銷量情況
- 2024年8月 新能(néng)源汽車產量數據
- 2028年8月 基本型乘用(yòng)車(轎車)產量數(shù)據