PCD 刀具(jù)車削鋁合金表麵粗(cū)糙度的研究
2016-10-27 來源:陽江(jiāng)職業技術(shù)學(xué)院 深圳信息職業技(jì)術學院 作者:喬龍陽 劉白
摘 要:影(yǐng)響PCD 刀具車(chē)削鋁合金表麵(miàn)粗糙度的主要因素是切(qiē)削速度、進給量、背(bèi)吃(chī)刀量。以黃金分割(gē)法設計(jì)了(le)實驗方案,優選了三因素的水平範圍,用等距法設(shè)置了水平值。實驗結果表(biǎo)明,對(duì)工件車削表麵粗糙(cāo)度影(yǐng)響最大的因素是進給量,次之是切削深度,切削速(sù)度的影響最小。通過正交實驗法驗證了上述實驗數據並篩(shāi)選了含優(yōu)區間,獲得了本(běn)工藝的最佳切削參數。
關鍵詞:PCD 刀具;車削;鋁合金;黃金分割法;表麵(miàn)粗(cū)糙度
0. 引言
為滿足使(shǐ)用性能、外形美觀等要求,5052 鋁合金產品的表麵粗糙度需達(dá)到Ra0.4 以上的技術要求。但是,傳統加工普遍采用硬質合金刀具低速車削加工(gōng),切屑容易與刀具發生(shēng)“膠(jiāo)焊”或粘連,形成積屑瘤,加工質量差、生(shēng)產效率非常低[1-2] 。
PCD 刀具材料硬度高、導熱性(xìng)好、摩擦係數小,使得切屑變(biàn)形和切削力降低、刀具磨損緩慢、切(qiē)削過程更為穩定(dìng),有利於降低表麵粗糙度[3-5] ,高速(sù)車削[6] 時零件表麵可達到鏡麵效果,是目前車削鋁合金理想的刀具材料。不足之(zhī)處是針對5052 鋁合金(jīn)的研究,大多是麵向其生產工藝(yì)[7] 、焊接組織和性能[8-9] 等方麵的研究,而(ér)針對其車削加工性能的實驗(yàn)研究很少,因此開展PCD 刀具車削鋁合金表麵粗糙度的研究,對於(yú)提高這類材料產品質量和生產效率有著現實的意(yì)義。
鋁合金車削性(xìng)能相關的實驗研究,大多采用正交實(shí)驗(yàn)或單因素實驗等方法,這些方(fāng)法存在實驗次數多、實驗精(jīng)度不高的缺(quē)點。現以黃(huáng)金分割法優選影響5052 鋁合金表(biǎo)麵粗糙度的切(qiē)削參數因素水平(píng)範圍,以等距法確定因素水平(píng)值,以(yǐ)正交實驗篩選驗證(zhèng),得出影(yǐng)響表麵粗糙度的主要因素(sù),確定臨界(jiè)區域,以黃金分割法為單因素考察方法,確定PCD 刀具(jù)車削5052 鋁合金表麵粗糙度的最佳工藝條(tiáo)件(jiàn)。
1. 黃金分割(gē)法實驗原理
黃金分割法是通過逐步縮小搜索區間,來求得一元函數極值點近似值的一種方法,又稱為0.618 法。黃金分割法實(shí)驗點選取,如圖1 所示,實驗範圍[a,b] ,將第一個實(shí)驗點x1安排在實驗範圍(wéi)內的0.618 處(距左端點(diǎn)a),即(jí)x1 =a+(b-a)×0.618,得(dé)到(dào)實驗結果f(x1 );再在x1的對稱(chēng)點x2 ,即x2 = a+(b -a) ×0. 382,得到實驗結果f(x2 ),且f(x) 值(zhí)越大,效果越(yuè)好(hǎo)。若f(x1 ) >f(x2 ),即f(x1 )比f(x2 )好,則根據“留好去壞”的原則,去掉實驗範圍[a,x2 ] 部分,在[x2 ,b] 內繼續實驗。以後每次取一個試點,比較2 個結(jié)果,去(qù)壞留好,進一步縮小範圍,進一(yī)步做實驗。
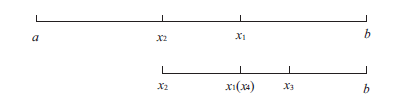
圖1 黃金分割法實驗點提取示意圖
在生產(chǎn)實踐和科學實驗中,應用黃金分割法(fǎ)單因(yīn)素實驗可以有效減少實驗次數,去掉“劣”點部分(fèn),保留“優”點部分,快速逼近真實值,並得到更為精準的(de)實驗數據。
2. 實驗條件
實驗材料:5052 鋁合金,規格為(wéi)Φ60 mm×55 mm 的鋁合金管,壁厚4 mm,采用專用向心結構夾具裝夾定(dìng)位。
刀具材料:三菱公(gōng)司PCD
材(cái)質MD220。
實驗機床:XKNC-50G 精密(mì)數控車床(chuáng),主軸最大轉速6 000 r/ min。
實驗儀器:JB-3C 粗(cū)糙度測試儀,分辨率0.001 μm,Ra 值測量範圍0.001-10 μm。
車(chē)削環境:濕式車削,采用煤油(yóu)作為切削液。
評價方法:取輪廓算術偏差Ra作為評價參數,測量時取樣長度為1 mm,評定長度為5 mm。
3. 實驗方法
為了獲得較好的實驗(yàn)效果,對影響表麵粗糙度較大的切削參數三因素切削速度、進給量和背吃(chī)刀量,開展黃金分(fèn)割法(fǎ)優選(xuǎn)實驗,逐步縮小實驗範圍,直(zhí)至取得最佳的(de)實驗數據。
3.1 黃金(jīn)分割法優選實驗
1) 利(lì)用黃金分割法確(què)定進給量的水平範圍
依據王洪祥等[10] 金剛石車削表麵微觀形貌形成機理的(de)研究,認為表麵粗糙度值與進給量和(hé)刀尖圓(yuán)弧半徑存在如下關係(xì):

依據此經驗公式,選取進給量實驗範圍[0.02,0.20]、背吃刀量0.3 mm、切削速度600 m/ min。按黃金分割法實驗點的提取步驟,在[0.02,0.20]的0.618 處取值,選取第1 實驗點為:
P1 =0.02+0.618(0.20-0.02)= 0.131 2
第2 實驗點為:
P2 =0.02+0.382(0.20-0.02)= 0.088 7
實驗測得P2的表麵粗糙(cāo)度值Ra1.375 μm 優於P1 的表麵粗糙度值Ra1.841 μm,則舍(shě)棄不包括P1 點的以外部(bù)分,在留下(xià)部分再找出P2的對稱點P3。
第3 實驗(yàn)點為:
P3 =0.02+0.382(0.131 2-0.02)= 0.062 5
實驗測得P3的表麵粗糙度值Ra0.843 μm 好於P2 的表麵粗糙度(dù)值Ra1.275 μm,則舍棄(qì)不包括P2 點的以外部分(fèn),在留下的部分中找到P3的對稱點(diǎn)。
第4 實驗點為:
P4 =0.02+0.382(0.088 7-0.02)= 0.046 2
實驗測得的P4的表麵粗糙度值Ra0.495 μm 好於P3的表麵粗糙度值Ra0.843 μm,則(zé)舍棄(qì)不包括P3 的以外部分,在留下的部分(fèn)中找到P4的對稱點。
P5 =0.02+0.382(0.062 5-0.02)= 0.036 2
實驗測(cè)得的P5的表麵粗(cū)糙度值Ra0.371 μm 好於P4的表麵粗糙度值Ra0.495 μm,則舍棄不包(bāo)括P4 的以外部分。
進給量對表麵(miàn)粗糙度的影響,如圖2 所示。隨著進給(gěi)量的增大,工(gōng)件表麵粗糙度值顯著(zhe)增大(dà)。實驗點所在實驗範圍包括含優點,則實驗結束(shù),優(yōu)選(xuǎn)實驗範圍為[0.02,0.046] 。
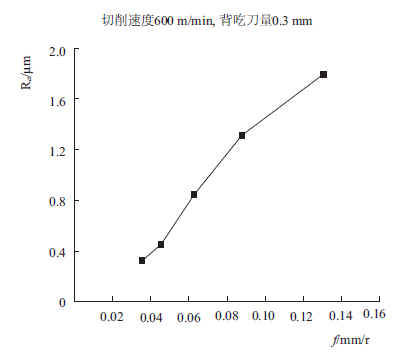
圖2 進給量對表麵粗糙度的影響
2) 利用黃金分(fèn)割法確(què)定切削速度(dù)的水(shuǐ)平範圍
選取切削速度實驗範圍[500,1 000]、背吃刀量0.3 mm、進給量0.1 mm/ r。按黃金分割法實(shí)驗點的(de)提取步驟,在(zài)[500,1000]的(de)0.618 處取值(zhí),選取第1 實(shí)驗(yàn)點為:
P1 =500+0.618(1 000-500)= 809
第2 實驗點為(wéi):
P2 =500+0.382(1 000-500)= 691
實驗測得P1的表麵粗糙(cāo)度值Ra1.241 μm 優於P2 的(de)表麵粗糙度值Ra1.375 μm,則舍(shě)棄不包括P2 點的以外部分,在留下部分再找出P1的對(duì)稱點P3。
第3 實驗點(diǎn)為:
P3 =691+0.618(1 000-691)= 882
實驗測(cè)得P3的表麵粗糙度值Ra1.233 μm 好於P1 的表麵(miàn)粗糙(cāo)度值Ra1.241 μm,則舍棄不包括P1 點的以外部分。
切削速度(dù)對表麵粗糙度的影響,如圖3 所示。隨著切削速度的增大,工件表麵粗糙度值逐漸減小,在切削速度達到800 m/ min 以(yǐ)上(shàng)值後,對表麵粗糙度的(de)影(yǐng)響降低,表麵粗糙度值趨於穩定。因此,實驗結束,優選範圍為[809,1 000] 。
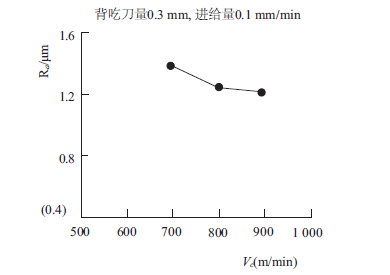
圖3 切削速度對表麵粗(cū)糙度的影響
3) 利用黃金分割法(fǎ)確定背(bèi)吃(chī)刀量的水平範圍
選取背吃刀量實驗範圍[0.05,1.0]、進給(gěi)量0.1 mm/ r、切削速度600 m/ min。按黃金(jīn)分割法實驗點的提取步(bù)驟,在[0.05,1.0]的0.618 處取值,選取第1 實驗點為:
P1 =0.05+0.618(1.0-0.05)= 0.637 1
第2 實驗點為:
P2 =0.05+0.382(1.0-0.05)= 0.412 9
實驗測得P2的(de)表麵粗糙度(dù)值Ra1.415 μm 優於P1 的表麵粗(cū)糙度(dù)值Ra1.554 μm,則(zé)舍棄不包括P1 點的以外部(bù)分,在(zài)留下(xià)部分再找出P2的對稱點P3。
第3 實(shí)驗點為:
P3 =0.05+0.382(0.637 1-0.05)= 0.274 3
實驗測得P3的表麵粗糙度值Ra1.293 μm 好於P2 的表麵粗糙(cāo)度值Ra1.415 μm,則舍棄不包括P2 點的(de)以外(wài)部分,在(zài)留下的部分中找到P3的對稱點(diǎn)。
第4 實驗點為:
P4 =0.05+0.382(0.412 9-0.05)= 0.188 6
實驗測得的P4的表麵粗糙度值Ra1.271 μm 好(hǎo)於P3的(de)表麵粗糙度值Ra1.293 μm,則舍棄不包(bāo)括P3 的(de)以外部分,在留下(xià)的部分中找到P4的對稱點。
P5 =0.05+0.382(0.274 3-0.05)= 0.135 7
實驗測(cè)得的P4的表(biǎo)麵粗糙度值(zhí)Ra1.271 μm 好於P5的表麵(miàn)粗糙度值Ra1.280 μm,則舍棄不包(bāo)括P5 的以外部分(fèn)。
背吃刀量對表麵粗糙度的影響,如圖(tú)4 所示。隨著切削深度的增大,工件表麵粗糙度值逐漸增大,增大趨勢不明顯;但(dàn)在(zài)切削深度(dù)小於0.1 mm 時,測得(dé)工(gōng)件表麵(miàn)粗糙度又趨於反(fǎn)方向細微增大。實驗結(jié)束(shù), 優選範圍為[0.135 7,0.274 3] 。
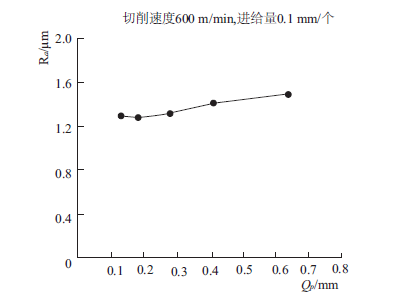
圖4 背(bèi)吃刀量(liàng)對表麵粗糙度(dù)的影響
3.2 等距法確定因素水平值
依據(jù)等距(jù)法,切削速度範圍[809,1 000] ,因素水平(píng)值為809、905、1 000;進給量範圍[0.02,0.046] ,因素水平(píng)值為0.02、0.033、0.046;背吃刀量範圍[0.13,0.27] ,因素水平值為0.13、0.20、0.27。
3.3 正交實驗
采用三(sān)因素三水平L9(33)組(zǔ)合切削參數,3 個因素分別(bié)是:切削速度νc 、進給量f 和背吃刀量ap ,以工件(jiàn)表麵粗糙度作為質(zhì)量特征,評價切削參數的優劣。正交實驗的因素水平表見表1。
表1 正交實驗因素水平表
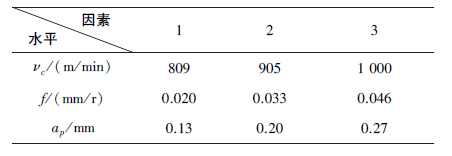
t 正交實驗方案與結果(guǒ)見表2。
表2 正(zhèng)交實驗方案及結果
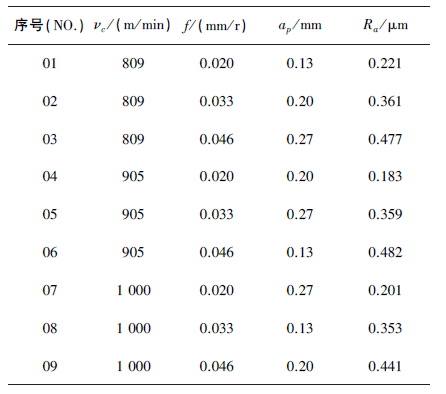
由實驗數據分析,對工件表麵(miàn)粗糙度影響(xiǎng)最大的因素是進給量(liàng),次之是切削深度,切削速度的(de)影響最小。如圖5 所(suǒ)示,切(qiē)削參數對表麵粗(cū)糙度的影響(xiǎng)驗證,隨著切(qiē)削速度的增大,工件表麵粗糙度值逐(zhú)漸減小;隨著切削深度的增大,工件表麵粗糙(cāo)度值逐漸(jiàn)增大;隨著進給量的增大,工件表麵粗糙(cāo)度值顯著增大。工件表麵二次元成像微觀機理顯示,隨進給量的增大,走(zǒu)刀(dāo)間距變大,工件表麵上紋路清晰,是造成工(gōng)件表(biǎo)麵粗糙(cāo)度值變大的主要因素。

圖5 切削參數對表麵(miàn)粗糙度的影響
正交實驗驗證:在穩定的高速車削環境(jìng)下,切削速度與切(qiē)削深(shēn)度對表麵粗糙度值影響較小,進給量是造成工件表麵粗糙度值變大的主要因素。提取(qǔ)進給量的含優區間為[0.033,0.046]。
3.4 黃金分(fèn)割法單(dān)因(yīn)素(sù)實驗(yàn)
選取進給量實驗範圍[0. 033,0. 046]、背吃刀量0.2 mm、切削(xuē)速度900 m/ min。按黃金分割法(fǎ)實驗點的提取步驟(zhòu),在[0.033,0.046]的0.618 處取值(zhí),選取(qǔ)第1 實驗(yàn)點為:
P1 =0.033+0.618(0.046-0.033)= 0.041
第2 實驗點為:
P2 =0.033+0.382(0.046-0.033)= 0.038
實驗P1 的表麵粗糙度值Ra0.391 μm,P2 的表麵(miàn)粗糙度(dù)值Ra0.387 μm,則P1 測得的是最(zuì)優實驗(yàn)值。實驗結束,進給量取值為(wéi)0.041 mm/ r。
4. 結語
在穩定的高速車削環境下,切削速度與切削深度對表麵粗糙度值影響較(jiào)小,進給量(liàng)是影響工(gōng)件表麵粗糙(cāo)度值變化(huà)的(de)主要因素。PCD 刀具車削5052 鋁合金表麵粗糙度達到Ra0. 4 技術要求的(de)最(zuì)佳工藝參數(shù)是: 進給量0.041 mm/ r、背吃刀量0.2 mm、切削(xuē)速度900 m/ min。黃金(jīn)分割法應(yīng)用於鋁合(hé)金車削表麵質量的實驗(yàn)研究,拓寬了實驗方法,有效地減少了(le)實驗次數,提高了實驗精度。所獲得的實(shí)驗數據為這類材料高精度、高效率車削加工提供了可(kě)靠的理(lǐ)論依據。
投稿(gǎo)箱:
如果您(nín)有機床行業、企業相關新聞稿件發表,或進行資訊合作,歡(huān)迎聯係本網編輯部, 郵箱:skjcsc@vip.sina.com
如果您(nín)有機床行業、企業相關新聞稿件發表,或進行資訊合作,歡(huān)迎聯係本網編輯部, 郵箱:skjcsc@vip.sina.com
更多相關信(xìn)息
業(yè)界視點
| 更多
行業數據
| 更多
- 2024年11月 金屬切削機床產(chǎn)量數據
- 2024年11月 分(fèn)地區(qū)金屬切削(xuē)機床產量數據
- 2024年11月 軸承出口情況
- 2024年11月 基(jī)本型乘用車(轎車)產量(liàng)數據
- 2024年11月 新能源汽車產量數據
- 2024年11月 新能源汽車銷量情況
- 2024年10月 新能源汽車產量數據(jù)
- 2024年10月 軸承出口情況
- 2024年(nián)10月 分地(dì)區金屬切削機床產量數據
- 2024年10月 金屬(shǔ)切削機床產量數據
- 2024年9月 新能源汽車銷量情況
- 2024年8月 新能(néng)源汽車產量(liàng)數據
- 2028年8月(yuè) 基本型乘(chéng)用車(轎車)產量數據