某型精密數控機床床身的優化設計及性能分析
2021-6-29 來源: 沈機集團昆明機床股(gǔ)份有限公司 作者:張偉華,賽雲祥(xiáng),李佳,黃(huáng)漢輝
摘要: 以某精密數控機床床身(shēn)為研究對象,利用有限(xiàn)元技術分析其靜動態特性,鎖定結構薄弱環節,以此為基礎,通過靈敏度法分析床身壁(bì)厚、筋板高度及厚度結構尺寸對床身動態特性的影響,並研究了床身內部筋板布局形式(shì)變化對床身動態特(tè)性的影響,最終給出該型機床整體床身的優選方(fāng)案。
關鍵詞: 精密數控機床(chuáng); 床身; 優化設計; 有限元分析; 靜動態性能分析(xī); 靈敏度
近年來,隨著航空、航(háng)天、汽車等行業的發(fā)展(zhǎn),對機床的回轉速度、進給速(sù)度、加工效率、加(jiā)工精度、性能穩定性、可靠性等方麵都提出較(jiào)高(gāo)的要求。精密數控機床廣泛應用於汽(qì)車、航空、航天、船舶、交通、能源、軍工等行業中大型(xíng)箱體類、盤類等精密零部件的(de)機械加工。為了使產品能夠適應市場需(xū)要,提高市場競爭力,公(gōng)司開展某(mǒu)精密(mì)數控機床(chuáng)係列產品(pǐn)的(de)關鍵技術研究及其(qí)工(gōng)程應用,圍繞某係列精密數控(kòng)機床(chuáng)的靜動態性能、精度、熱特性、穩定性及可靠性等方麵開展研究。
1、 概述
某精密數控機床作為(wéi)高(gāo)速切削機床,必須具有較高的進給速度和加(jiā)速度,並在高速下仍有(yǒu)高的定位精度。在產品的設計中,其中的大件結構設計( 包括床身、主軸、立柱、工作(zuò)台、橫(héng)梁(liáng)等尺寸和質量較大的零件或部件) ,雖然件數不多,但質量卻占機床(chuáng)總(zǒng)質量的 80% ~ 85%。它們不僅是機床的運動支承件,而且是機床外觀的主要體現。機床的其它零部件,或(huò)者固定在大件上,或者工作時在大件的導軌上運動,因此(cǐ),大件結構的材料與製造工藝費用在設計中必須加以考慮。對機床進行優化設計的目的就是要使(shǐ)之在滿足結構性能的基礎上,具有合理的結構布局和最輕的(de)質量,文中僅以床身進行說明。此外,機床結構的動態性能的優劣直接影響機床(chuáng)的工作性能和產品(pǐn)質量,決定著機床的加工精度。所以研究機床動力學特性對加工性能和加工(gōng)精度的影響規律找到解決工程應用中出現的(de)機(jī)床振動、精度不穩定等問題,提升(shēng)機床的整體性能,為(wéi)高性能機床的產業化鋪平道路。某精(jīng)密(mì)數控機床,如圖 1 所示。其床身設計是其(qí)重難點之一,因為(wéi)它承載機床絕大部分的部件(jiàn)和載荷,其剛度、固有頻率等直接影響整機的加工性能和效率,因(yīn)此對床身進行優化設計及性能分(fèn)析(xī)具有重要意義。
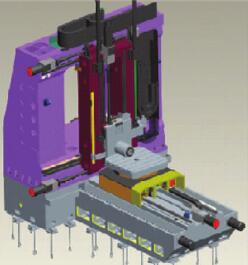
圖 1 精密數控機床整(zhěng)體布局
2、床身結(jié)構(gòu)方案(àn)模型優化及性能(néng)分析的目的
確定床身載荷及約束條件後,建立床身的有限元模(mó)型,建立合(hé)理(lǐ)的結構單元、網格大小。通過載荷添加及邊界條件約束後,進行求解計算,通過拓撲優(yōu)化,獲取結構載(zǎi)荷傳遞(dì)路徑,確定(dìng)結構的概(gài)念造型,通過拓撲結(jié)構圓整,獲取(qǔ)床身的結構三維模型,對模型進行(háng)性能分析。通過對結構特征進(jìn)行參數建模(mó),並在(zài)有限元分析軟件中進行分析和(hé)優化,確定(dìng)結構特(tè)征的靈敏度,確定結構特征的較優結構尺寸,最終獲得床身靜動態性能較優的結構模型(xíng)。其優(yōu)化的數學模型為:
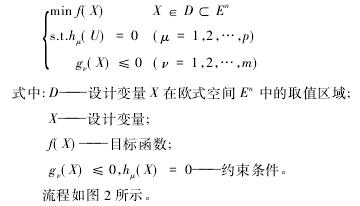
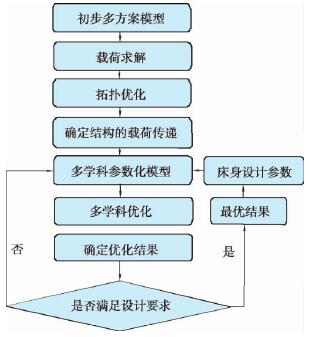
圖 2 結構方案優(yōu)化確定
床身性能分析及優化工作的主要內容和目的: ( 1) 確定載(zǎi)荷傳遞路線及主要結構特征。( 2) 考察床身在靜態載荷條件下的變形特性,對其靜剛(gāng)度進行校核和驗證。( 3) 考察主(zhǔ)要結(jié)構件固有的動態特(tè)性,分析其動態薄弱環節,為整機動態分析設計提供依據。( 4) 對不同的設計方案進行分析、比較和優選,進行床身的(de)輕量化設計。
3、床身結構方案的(de)優化及(jí)性能分析
3. 1 床(chuáng)身結構拓撲優化
以減小的材料質量為狀態變量,對床身的原始模型進行形狀拓撲(pū)優化計算(suàn),為後期的詳(xiáng)細設計提供(gòng)依據,目的(de)是確保其承載能力的基(jī)礎上減輕床身質量,降低製造成本首先,根據工藝需求分析,確定床身結構尺寸參數和初步結構方案,並對結構方案進行拓(tuò)撲優化,確定床身結構的載荷傳遞路(lù)徑。如圖 3 所示,根據設(shè)計任務書要求,床身結構確定為 T 字形(xíng)整體式床身(shēn)。建立床身三維結構骨架模型,對床身進行有限元劃分,並對(duì)床身地腳螺(luó)栓支撐進行約束,如圖 4所示,導軌上承受 20 000 N 工作台的載荷,30 000 N最大加工工件載(zǎi)荷,再加(jiā)上立柱滑板主軸箱載荷,其前處理如圖(tú) 5所示,床身材料彈性模量為 1. 5× 10(11次方)Pa,泊鬆比為 0. 25,密度為 7400 kg /m(3次方) 。
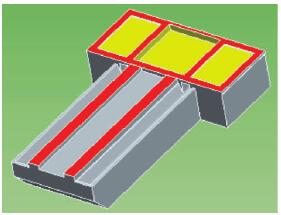
圖 3 床身(shēn)結構初步方案圖
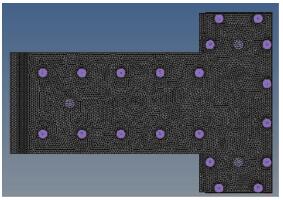
圖 4 床身地腳螺栓
以機床質量和體積因素為設計變量,以床身變(biàn)形最小、1 階固頻最大為約束條件,以質量降低(dī)為設計目標,對床(chuáng)身進行(háng)拓撲優(yōu)化,其優(yōu)化結(jié)果如圖 6 所示。通過對結構進行(háng)拓(tuò)撲優化,確定載荷的傳遞路徑及(jí)床身結構的主要支撐著力點。
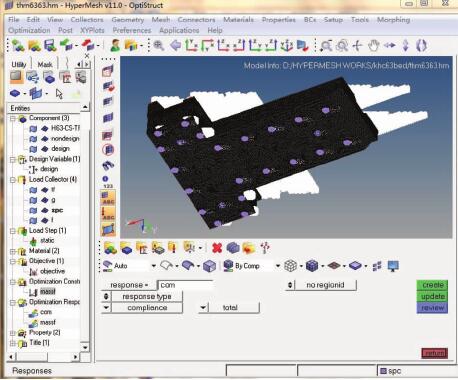
圖 5 拓撲優化前處理
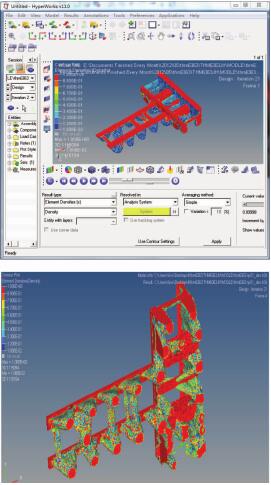
圖 6 整體(tǐ)式床身(shēn)的拓撲優化(huà)結果
3. 2 床身的(de)建模(mó)分析及(jí)優(yōu)化
對拓撲優化後(hòu)的結構進行結(jié)構圓整(zhěng),確定床身結構筋板主要布置形(xíng)式,並通過參數化建模軟件,建(jiàn)立床身結(jié)構三維(wéi)參數化模型。如圖(tú) 7 所示。

圖 7 整體床身結構的參數化模型
建立床身結(jié)構(gòu)的有限元模型,對床身(shēn)結構進行靜、動態分析,主要是: ( 1) 考(kǎo)察結構在(zài)靜態載荷條件(jiàn)下的變形(xíng)特性,對(duì)其靜剛度進行校核和驗證。( 2) 考察結構(gòu)固有的動態(tài)特性,分析其動態薄(báo)弱環節,為整(zhěng)機動(dòng)態(tài)分析設計提供依據。
3. 2. 1 不加工件,隻考慮工作台重力和床身自重
通過對床身的靜(jìng)力學分析,床身的整體變形(xíng)如(rú)圖 8 所示。分析(xī)結果顯示: 床身最大變形(xíng)約(yuē)為 8. 2 μm,導軌上的變形(xíng)為2~5. 6 μm,其中最大變形(xíng)為 5. 6 μm 出(chū)現在 Z 軸方向2. 15 m處( 床(chuáng)身後麵為零點) 。
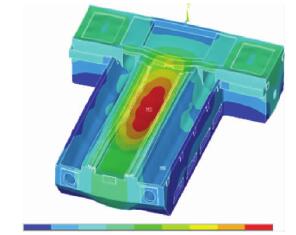
圖 8 不加工件(jiàn),床身靜載變形圖
3. 2. 2 考慮(lǜ)實際工況載荷
以一種典型工(gōng)況為例: 工件和滑塊總質量為 5 t,作(zuò)用在上導軌上; X 向的切削力為 6 600 N; 立柱自重為 10 t,並考慮床身自重(chóng)。變形情況如圖 9 所示。結果顯示,此時最大變形約為16 μm;主要考慮導軌上的變形,其變形為 5 ~ 12. 4 μm; 其中最大變形12. 4 μm 仍出現在 Z 軸方向 2. 15 m 處( 床身後麵為零點) 。
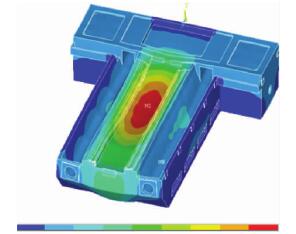
圖 9 考慮實際工況下床身靜載變形圖
3. 3 模態分析
在床身底麵(miàn)施加位移約束,計算所(suǒ)得(dé)前 5 階模態(tài)頻率與振(zhèn)型如(rú)表 1 所示。
表 1 床(chuáng)身前 5 階模態頻率與振型
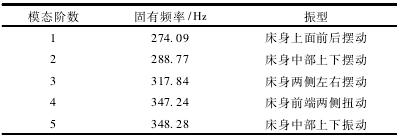
圖 10 給出了床身的前 3 階模態振型圖。其中第 1 階振(zhèn)型為床身上表麵的前後擺動; 第 2 階振型為床身中部(bù)的上下擺動(dòng);第 3 階振型為床身兩側(cè)的扭動。
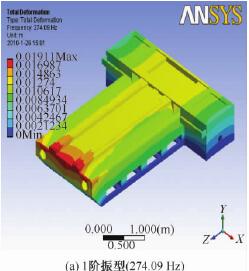
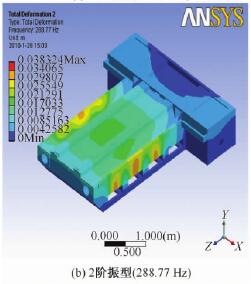
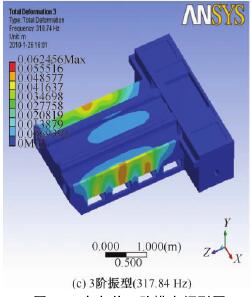
圖(tú) 10 床身前 3 階模(mó)態(tài)振型圖
由以上分析可(kě)以看出床身固有頻率(lǜ)比較高,考慮到主(zhǔ)激(jī)勵源頻率大約在 50 Hz 左右( 工作(zuò)轉(zhuǎn)速(sù)在 3 000 r/min) ,故床身滿足整機總體動態特性要求(qiú)。4 床身導軌及內部筋板的優化。
4. 1 前部床身導軌(guǐ)優化
其中: P1為前部床(chuáng)身兩根導軌的間距,P2為最大總變形,P3為導軌上表麵最大變(biàn)形。DP1點為寬度增加 60 mm 後,Dp2為寬度增加(jiā) 107 mm 後結果。原模型為 650 mm,增加 107 mm 後,其最大變形為(wéi) 8. 9 μm,變形減少 1. 1 μm。如表 2 所示。
表 2 導軌優(yōu)化後變形 mm
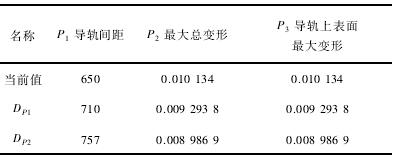
4. 2 前部床身筋(jīn)板厚度、高度參數(shù)優化
對筋板布置進行參數優化,通過改變筋板參數數值,進行計算分析,獲取筋板參數對床身變形的靈敏度圖,從而取得較優的筋板結構參數(shù),其優化形狀及(jí)參(cān)數如圖 11 ~ 圖 14所(suǒ)示。
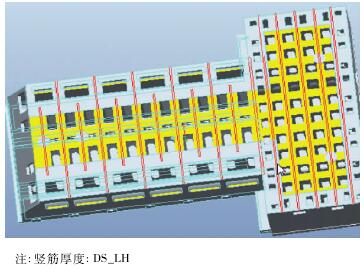
圖 11 床身豎筋
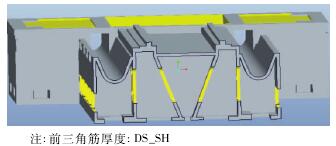
圖 12 床身三(sān)角筋
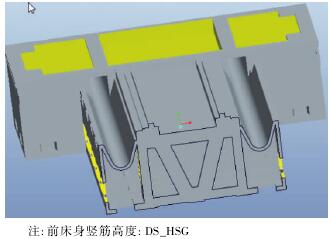
圖 13 床身豎筋高度
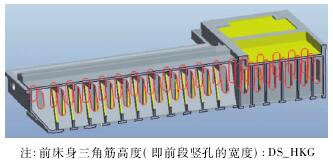
圖 14 床身三角筋高度
( 1) 采(cǎi)用表 2 中第 3 組結果 C 時,導軌最大總(zǒng)變形減(jiǎn)小0. 6 μm,總質量減小 200 kg。此(cǐ)時 4 個參數分別為(wéi): 筋板厚度:DS_LH 為 12.51 mm ( 減(jiǎn)小 8 mm) 、DS _SH 為 34.85 mm ( 增加4 mm) 、高度 DS_HSG 為 107. 7 mm( 增加 17 mm) ; DS_HKG 為80 mm( 減小 20 mm) 。如表(biǎo) 3 所示。
表 3 筋板參數優(yōu)化結果
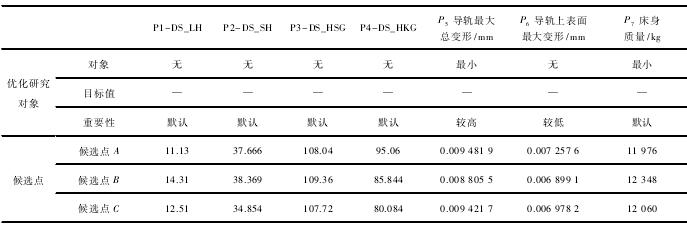
( 2) 各參數的靈敏度。
文中以床身的壁厚、筋板高度及筋板厚(hòu)度作(zuò)為一組設計(jì)變量(liàng),利用靈敏度法分(fèn)析各結構參數變化對床身動態性能的影響。結果如圖 15 所示。
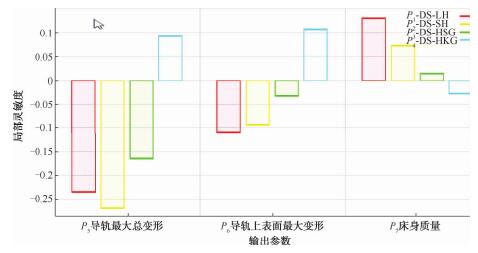
圖 15 床身各參(cān)數靈(líng)敏度
( 3) 最終床身優化結構。
①床身導軌變形較大,達到 10 μm。為減小變形,對床身筋板厚度、筋板(bǎn)高度進行優(yōu)化,優化後變形為 8 μm,變形減(jiǎn)少 20%。
②前部床身整體結構較差,僅對筋板厚度、高度(dù)進行優化變形減小有限。由於前部床身中間沒(méi)有支撐( 僅靠(kào)前部兩(liǎng)點) ,且導軌靠近(jìn)前部床身中間(jiān),故變形較大。通過不斷優化,導軌間距離增加 125 mm 後,變形減(jiǎn)小 1. 2 μm,變形減少 12%。其(qí)最終結果如圖 16 所示(shì)。
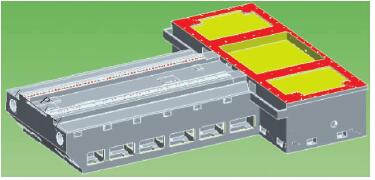
圖 16 整體式床(chuáng)身的最終三維結構
經過(guò)多次分析計算和相應的結構優化(huà),床身結構(gòu)的各項性能指標(biāo)均達到了設計(jì)目標值(zhí),取得了較好效果(guǒ)。
5、結(jié)論
通過有限元模型(xíng)確定結構方(fāng)案(àn),再對結構方案進 行拓優化,靜、動態(tài)模態分析; 找出床身結構的薄弱(ruò)點,並不斷(duàn)優化導軌及(jí)內部筋(jīn)板的結構,達到最終的最(zuì)優結(jié)構。采(cǎi)用該方法,可獲得床身在(zài)不同載荷工況下承受的載荷大小,從而為精確計算不同工況(kuàng)下導軌變形提供準確載荷模型。可以快速獲取結構件在不同工作位(wèi)置及受力工況下靜動態性能,並(bìng)通過結構參數化設(shè)計可(kě)以獲取不同方案下(xià)結構的綜合性能(néng),從而能夠快速確定較佳的結構方案(àn)。推廣(guǎng)並運用在機床其他大件的優化設上,取得了良好的效果。
投稿箱:
如果您有(yǒu)機床行業、企業相關新聞稿件發表,或進行資訊合作(zuò),歡迎聯係本網編輯部, 郵箱:skjcsc@vip.sina.com
如果您有(yǒu)機床行業、企業相關新聞稿件發表,或進行資訊合作(zuò),歡迎聯係本網編輯部, 郵箱:skjcsc@vip.sina.com
更多(duō)相關信息
業(yè)界視點
| 更多(duō)
行業數據
| 更多
- 2024年(nián)11月 金屬切削機床產量數據
- 2024年11月 分地區金(jīn)屬切削機床產量數據(jù)
- 2024年11月 軸(zhóu)承出(chū)口情況
- 2024年11月 基本型(xíng)乘用車(轎車)產量數據
- 2024年11月 新能(néng)源汽車產量數據
- 2024年11月 新能源汽車銷量情況
- 2024年(nián)10月 新能源汽車產量數據
- 2024年10月 軸承出口情(qíng)況
- 2024年10月 分地區金屬切削機床產量數據
- 2024年10月 金屬切削機床產量數(shù)據
- 2024年9月(yuè) 新能源汽車(chē)銷量情況
- 2024年8月 新能源(yuán)汽車產量數據
- 2028年8月 基本型乘用車(轎車)產量數據
博文選萃
| 更多