超精密車床主軸回轉誤差測試係統的研究
2016-12-14 來源(yuán):哈爾濱工業大學 作者:王世良
第 3 章
徑向運動誤差分離(lí)及實驗研究
本章以三點(diǎn)法誤差分離算法為基(jī)礎,提出徑(jìng)向誤差測量實(shí)驗除噪、濾(lǜ)波、同步運動誤差的提取和三點法誤差分(fèn)離算法的(de)頻域連續性處理方法,減少測量信(xìn)號(hào)在時域頻域中的變換計算。利用之前搭建的回轉(zhuǎn)誤差測試係統對超精密車床(chuáng)主(zhǔ)軸回轉誤差進行實際測(cè)量實驗和數據分析(xī)。本(běn)章還從超精密車床(chuáng)固定方向刀具加工工件表麵成形角度,分析(xī)一階諧波去(qù)除依據。
3.1 徑向運動誤差分析
3.1.1 最(zuì)小(xiǎo)二乘(chéng)偏心對徑(jìng)向運動誤差的不可分離性
本節將分析傳感器測量值在頻域中的解析構成,並分析最(zuì)小二(èr)乘圓心對徑(jìng)向回轉誤差的不可分離性。下麵首先討論回轉是理想軸,測試件表麵輪廓不是理想圓的情況傳感(gǎn)器的測量值。圖 3-1 中曲線為測試工件某一截麵的實際輪廓,O 為截麵的最小二乘圓心,由於安裝偏心使得測試工件最小二乘圓心 O 與回轉軸心 O?有偏差 e。
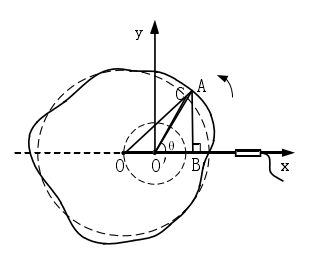
圖(tú) 3-1 實際表麵輪廓傳感器測(cè)量
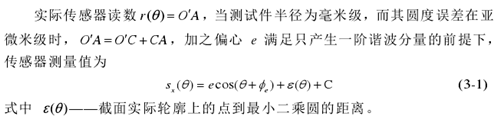
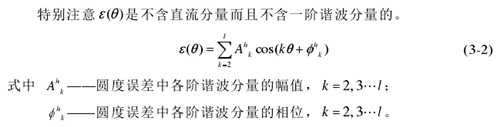
由式(3-2)可知,非理想截麵(miàn)時,建立在回轉軸心(xīn)處的測量坐標係(之後還會介(jiè)紹坐標係不建在回轉軸心處)中,x 軸(zhóu)方向的傳(chuán)感器讀數為最小二乘圓心在 x 軸方向上的運動(dòng)軌跡。如果截麵平麵內布(bù)置兩(liǎng)個(gè)傳感器,則可以測出最小二乘圓心在平麵內的運動軌跡。
安裝偏心,通常指的是人為安裝測試件到回轉軸(zhóu)時產(chǎn)生的偏心。但是即便不安裝測試工件,直接對主軸某一截麵進行測量,實際情況下此截麵(miàn)的最小二乘圓(yuán)心和(hé)其回轉軸心也基本不會重合。故定義此(cǐ)處最小二乘圓心與瞬時回轉(zhuǎn)中心的偏差為最小二(èr)乘偏心。這個最小二乘偏心與之前討論的安裝偏心並無本質區別,隻是最小(xiǎo)二乘偏心比(bǐ)安裝偏心小很多(duō)罷(bà)了,所以將(jiāng)安裝偏心歸到最小二乘偏心概念中。最小(xiǎo)二乘偏心滿足一定條件時,隻產生一階諧波分量,並(bìng)引入到傳感器測量值中。

式(3-4)給出傳感器測量值在頻域中的(de)解(jiě)析構成,等式右側第一項為最小二乘偏心運動,第二項(xiàng)為回轉(zhuǎn)軸的一階諧波運動,第(dì)三項為回轉軸的二階及以上諧波運動,前三項的值指的都是最小二乘圓心運動在傳感(gǎn)器軸線方向上的分量。第四項為(wéi)被(bèi)測截麵實際輪廓上的點(diǎn)到最小二乘圓的距(jù)離(注意(yì)此項不含直流分量和一階諧波分量),實際(jì)上也是截麵轉動(dòng)時在傳感器軸線方向上的輪廓上的點到最小二乘圓的距離,組後一項為直流分量。除去直流分量所(suǒ)有項之(zhī)和為最小二乘圓心的運動與(yǔ)圓度誤差的疊加。
下麵(miàn)將從傳感器測(cè)量值在頻域中的解析構成(chéng)結合三點法誤差分離算法分析(xī)最小二(èr)乘偏心對徑向運動誤差的不可分離性:
在三點法誤差分離過程中,因權函數 G(1) ?0 ,抑製一階諧波(bō),使傳感器(qì)中(zhōng)的一階諧(xié)波量沒有分開。分離出的圓度誤差不含一階諧(xié)波分量,即(3-2)式。傳感器測量值中的一階(jiē)諧波分量全部歸(guī)到主軸回轉誤差運動中,從(3-4)式可知歸到主軸回轉運動誤差中的一階諧波分量就包含最小二乘圓心的偏心(xīn)運動,這個偏心運動量影響了主軸(zhóu)回轉誤差的分離(lí)精(jīng)度。
從式(3-4)中去掉(diào)圓度誤差項和直流分量項即為三點法得到的回轉運動誤差(chà),其中第一項與第二(èr)項是最小二乘偏心運動量和回轉誤差一階諧波分量。因為(wéi)二者都(dōu)是一階諧波,其和(hé)亦(yì)為一階諧波。顯然一二(èr)項的合成是唯一的,而若已知合成項,其分解不(bú)唯一,所以最小二乘偏心運動與回轉軸的一(yī)階諧波運動是不可分的(de)。
如(rú)果在測量試驗中人(rén)為安裝測試件進行測量,則最小二乘(chéng)偏心量相(xiàng)對於回轉誤差(chà)會很大,嚴重影響回轉誤差(chà)的分離結果,即便是直接對回轉軸截麵直接測(cè)量,回轉誤差中依然包含了最小二(èr)乘偏心(xīn)量,隻不過相對於安裝偏心量小些罷了。
鑒於最小二乘偏心對徑向運動(dòng)誤差的不可分離性,由兩種處理方式得到回轉軸回(huí)轉誤差:一是保留一階諧波分量,缺點是回轉誤差中包含了最小二乘圓心的(de)偏心運動量;二(èr)是(shì)去掉一階諧(xié)波分量,缺點是回(huí)轉誤差中損失了回轉軸的一階諧波分量。如果用安裝測試件進行測量時,要(yào)去掉一階諧波分量,因為此時最小二乘偏心運(yùn)動量相對於回轉誤差太大,如保留一階諧(xié)波分量,分(fèn)離出(chū)的回轉(zhuǎn)誤差將嚴重(chóng)失(shī)真。
下麵討論(lùn)一階(jiē)諧波分量如何處理的問題:
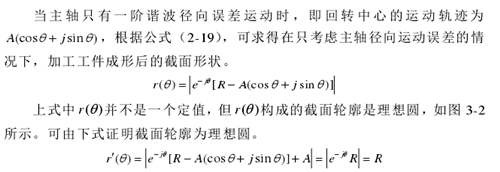
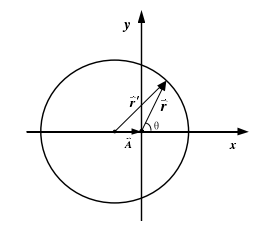
圖(tú) 3-2 主軸(zhóu)具有(yǒu)一階諧波(bō)誤(wù)差運動固定方向刀具加工工(gōng)件成形
至(zhì)此可得出結論:超精密車床主軸徑(jìng)向一階諧波誤差運動不影響固(gù)定方向刀具加工工(gōng)件截麵形狀(zhuàng)輪廓,所以從加工工件的角度來講超精密車床主軸徑向運動誤差中的一階諧波分量(liàng)可不予以考慮(lǜ)。綜(zōng)合上述信息,利用三點法誤差分離測量主軸的(de)徑向(xiàng)回轉誤差可以不計(jì)一階諧波分量(liàng)的影響,故在在誤差分離之前可以將信號中的一階諧波分量直接去掉。
3.1.2 同步誤差和異步誤差的頻域(yù)提取
在分析同步和異步運動誤差之前先來看一下一(yī)種常用的誤(wù)差分(fèn)離方法——集合平均。集合平均(jun1)是對同一誤差信號進行 N 次(cì)采樣,然後對這 N 次采樣的數據按點位求平均值。
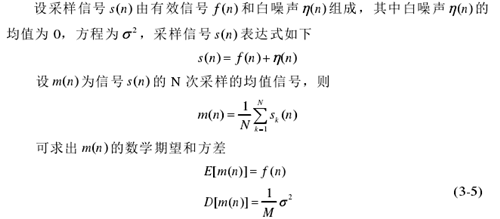
可見對信號做集(jí)合平均(jun1)處理有(yǒu)抑製隨機噪音的作用。
所謂的(de)同(tóng)步誤差就是回轉軸的(de)多轉采樣數據的均值,異步誤差是從每轉采(cǎi)樣(yàng)數據(jù)中減掉同步誤差[45],如圖 3-3。主軸的回轉(zhuǎn)誤差運動實際上不是周期性的,對於超精密車(chē)床,其主軸的回轉精度很高,每轉的回轉誤(wù)差運(yùn)動(dòng)基本保持一致(zhì)。由此計算(suàn)出的同步誤差(chà)可以視(shì)作主(zhǔ)軸的回轉運動誤差。

提取(qǔ)同步誤差的作用是從(cóng)主軸的回轉運動采集信號中提取周期性回轉(zhuǎn)運動(dòng)感誤差,作為誤差分離的基礎信號。另(lìng)外,同步誤差的提取同於對(duì)信號做了集合平均,所以對信號(hào)中的隨機噪聲也有一定的抑(yì)製作用。
同步運動誤差是多轉數據(jù)對應點位的均值,所以要求每轉(zhuǎn)的采集信號是嚴格的等角度采樣,否則均化後的結果將失真(zhēn)。
以上討論了從時域角(jiǎo)度提取主軸的同步運動誤差,並可(kě)知提取同步運動誤差不但提取了主軸的周期(qī)性(xìng)的高回轉精度運動誤差,還具有集合平均的效果,降低低階噪聲的影響。下麵討論從頻域中提取同步和異步運動誤差:
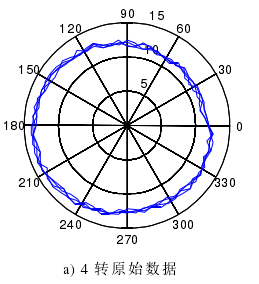
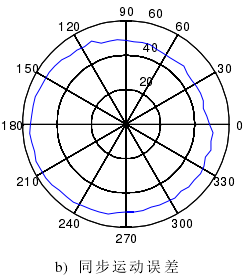
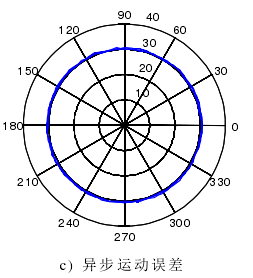
圖(tú) 3-3 Maltab 仿真傳感器(qì)的 4 轉數據及同步、異步運動誤差時域圖
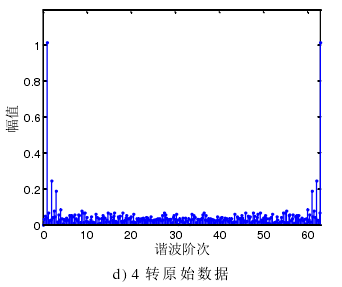
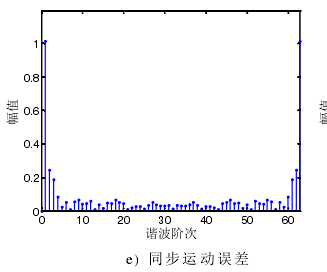
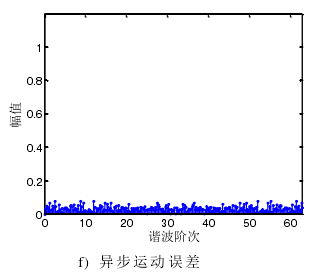
圖(tú) 3-4 Maltab 仿真傳感器的 4 轉數據及同步異步運動誤差頻域圖
對一個傳感器的 4 轉數據(jù)(每轉 64 個點)進行傅裏葉變換,整數倍(bèi)諧波階次對應的是同步運動誤差的諧(xié)波(bō)成分,如圖 3-4 e)所示;小數倍諧波階次對應(yīng)的(de)是異步(bù)運動誤差的諧波成分,如圖 3-4 f)所(suǒ)示。已知這個結論,從(cóng)頻域中提取整數倍諧(xié)波分量成分,即是主軸的同步運動誤差(chà)。
3.1.3 徑向運動(dòng)誤差數據的頻域連續性(xìng)處理
本節將(jiāng)綜合除噪、濾波、提取同步運動誤差和三點法誤差分離在頻域中進行連續處理,即從傳感器原始(shǐ)電壓時域信號(hào)開始,上述步驟全部(bù)在頻域(yù)中處理,不在時(shí)域中提取同步運動誤差,減(jiǎn)少信(xìn)號在時域頻域中的轉化計算。圖 3-5 是頻(pín)域連續性處理與一般方法對比圖,從圖中可以看出(chū),頻域連續性處理減少了時域信號和頻域信號(hào)之間的轉(zhuǎn)換次數,即可以減少額外的計算量。頻域連續性處理的關鍵即是 3.1.2 節中講述的從頻域中提取主軸(zhóu)的同步運動誤差,在這個(gè)環節中可以減少時域頻域的轉換計算。
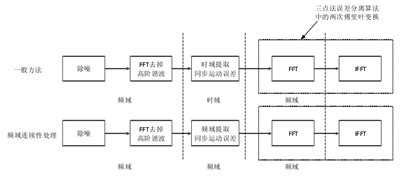
圖 3-5 頻域連續性處理與一般方法對比圖
以下將詳細展開(kāi)頻域連續性處理的各個(gè)環節,首先討論濾波。在(zài)采集(jí)模擬信號之前,通常要對此信號進行抗混疊濾波。所謂的抗混疊濾波(bō)[47],即是設置濾波器的截止頻率(lǜ)為有用信(xìn)號的最高頻率,將高於截止頻率的成分從信號中去除。抗混疊濾波的(de)作(zuò)用是在采樣之前將高頻無(wú)用(yòng)頻率成分去掉(diào),防止在(zài)之後(hòu)的采樣(yàng)過程(chéng)中將(jiāng)高頻幹擾信號采樣(yàng)成低頻(pín)成分,出現頻率混疊現象,造成采集信(xìn)號的失真(zhēn)。
抗混疊濾波是在模擬信號進行數字化采集之前(qián)由硬件實現(xiàn)的,另一(yī)種方法是通過軟件濾波的方式實現數據(jù)采(cǎi)集的抗混疊作用。具體(tǐ)操作是直接進(jìn)行(háng)模擬信號(hào)的數據采集,但是要求采樣(yàng)頻率應為高於高頻幹擾成分頻率的至少兩倍以上。采集得到的數據再進行數字(zì)濾波,將高於有用信號的(de)最高頻(pín)率的成分去掉(diào)。如果采樣頻率僅僅設置為(wéi)高於有用信號的(de)最高頻率的兩倍以上,那麽高頻幹擾成分會在采樣過程中錯誤的采樣為低頻成(chéng)分,在以後的處理(lǐ)中,再也(yě)無法用數(shù)字濾波器濾除了。圖 3-6 為防止頻(pín)率混疊的兩種方(fāng)法:
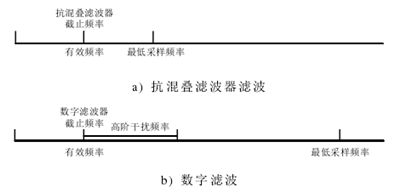
圖 3-6 抗混疊濾(lǜ)波和數字濾波比較(jiào)

表 3-1 抗混疊濾波和數字濾波區別

由圖 3-6 和表(biǎo) 3-1 可見,采用數字濾波的優點是采集係統中不(bú)用加入抗混疊濾波器硬件,缺點是(shì)由於采樣頻率較(jiào)高,增(zēng)加了 A/D 轉化的成本(běn)以及後期的數據處理運算量。
對采樣後的數據,要將信號中的高階成分去掉(diào)。根據 ISO 標準,工件的(de)圓度誤差多為低頻信號,當被測件的圓度(dù)誤差的諧波階次大於 22~45 階後,通常就歸於(yú)零件的表麵質量如波紋度、表麵粗糙度等,如圖 3-7。從超精密車床加工的角度來講,其加工的(de)零件的輪廓誤差的主要來源(yuán)是主(zhǔ)軸的回轉運動誤差。工(gōng)件的表麵形狀誤差(chà)的(de)主(zhǔ)要來源於主軸的低階回轉運動誤差,工件的表麵質量如波紋度、表麵粗糙度誤差主要來源於(yú)主軸的高階回轉運動誤差。本論文對主軸回轉運動誤(wù)差的測量目的(de)主要是為後期提高加工工件(jiàn)表(biǎo)麵形狀誤差做準備,所以分離主軸回轉運(yùn)動誤差與分離圓度(dù)形狀(zhuàng)保(bǎo)留同樣的諧波階次即可。論文中將保留誤差信號(hào)的低 50 階信號,將高於 50 階的信號全部除掉。
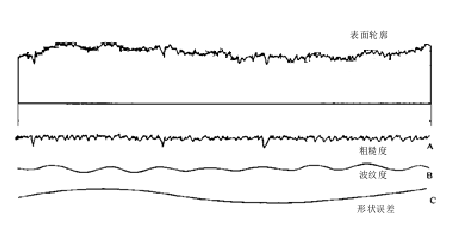
圖 3-7 工件表麵輪廓成(chéng)分組成
具體除掉(diào)采集信號高階信號的(de)做法是(shì):首先對采集信號做傅裏葉變換,將(jiāng)相應的高階項及對稱項置零,然後在做反傅裏葉變換得到濾掉高階成(chéng)分的信號(hào)。這種數字濾波方式可以將信號中(zhōng)給定的高階成分全部濾掉,帶(dài)通內的諧波(bō)成分全部保留而且沒(méi)有任何衰減(jiǎn)。
綜合以上分析,圖(tú) 3-8 給出徑向運動誤差(chà)頻域連續性處理的詳細數據處理(lǐ)過程。
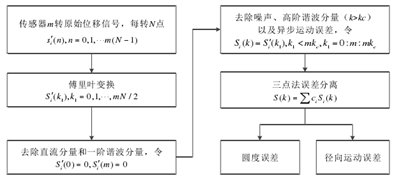
圖 3-8 徑向回轉誤差頻域連續性數據處理流程
3.1.4 主軸回轉精度的評價(jià)
最小二乘圓法對評價圓度誤差最常用的方法,對(duì)於主軸徑向誤差運(yùn)動的評價可以參照(zhào)圓度誤差評價,采用最小二(èr)乘圓評價。利用最小二乘法,找(zhǎo)出(chū)實際輪廓的(de)理想圓,使得輪廓上(shàng)各等分點沿徑向到圓(yuán)周距離的(de)平方和最小,這個理想圓即為最小二乘圓(yuán),其圓心為最小二乘圓心,如圖 3-9 所示。
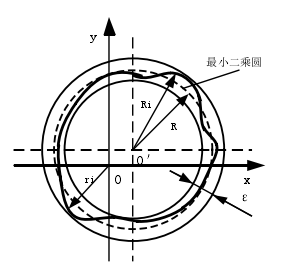
圖 3-9 最小二乘(chéng)法確定理想圓圓心
最小二乘圓的圓(yuán)心 O'?坐標 (a,b),半徑為 R,則
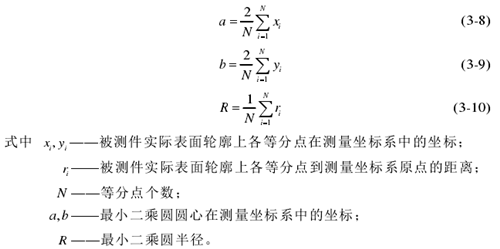
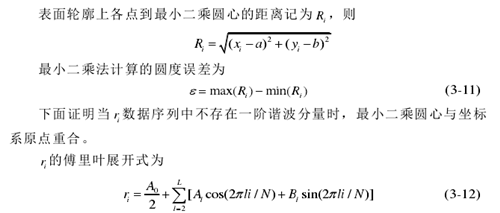
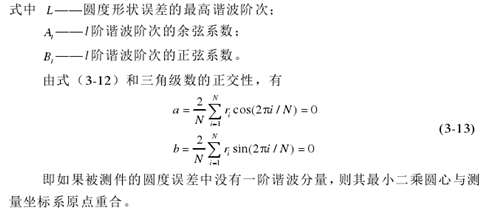
3.2 徑向運動誤(wù)差測量實驗及(jí)分析
3.2.1 傳感器安裝角位(wèi)置的(de)確定
在滿足 G(k)≠0(k=0,2,3,4…N)的條件(jiàn)下,即除三點法原理性一階諧波抑(yì)製以(yǐ)外,保證(zhèng)其(qí)他諧波成分不被抑製,p1、p2有(yǒu)很多組,文獻[50]給出確定三點法傳(chuán)感器最佳角位置(zhì)的(de)方法(fǎ)。圓度誤差各階諧波分量的誤差傳遞係數Q(k) 的計算方法如(rú)下:

式(shì)中ɑ (k),β(k)——分別為權函數G(k)的實部和虛部。
Q(k) 包含由傳感器自身精度(如傳感器的非線性,靈敏度係數誤差及隨機噪聲等)和傳感器安裝誤差(安裝間隔偏差,傳感器測量軸線偏斜等)對分離出的圓度誤(wù)差的第 k 階諧波分量引入的誤差係數。
為增大圓度誤差分離精度,應該減小圓(yuán)度誤差的各階諧波分量的傳遞誤(wù)差,其中(zhōng)一種方法是使 Q(k)的最大值(zhí)最小。本課題據此設定傳感器安裝位置(zhì)N=128,p0=0,p1=17,p2=32,其權函數如圖(tú) 3-10 所示。
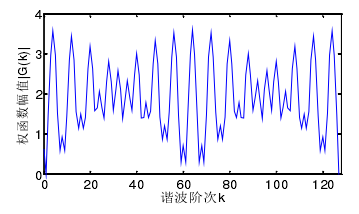
圖 3-10 N=128,p0=0, p1=17,p2=32 時的權函數圖
3.2.2 測試工件(jiàn)選取及安裝偏差消除
通常在主軸(zhóu)回轉(zhuǎn)運動誤差測量試驗中會采用標準球或標準棒作為被測試件,如圖 3-11,通過對被測試件的運動的測量來主軸的回轉運動誤差。標準球和標準棒各有各的優缺點,標準球的優點是可以用位(wèi)移傳感器通過掃(sǎo)描的方式精確的找到球赤道位置,可用於調整傳感器位置使所有傳感器共赤(chì)道(dào)平麵安裝;標準棒可以提供更多的測量截麵,而且相(xiàng)同精度的標準棒相對於(yú)標準球的價格會低一些。
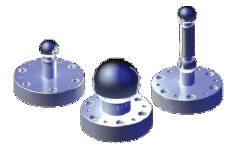
圖 3-11 標(biāo)準(zhǔn)球
雖(suī)然高質量標準球或標準棒的截麵圓度誤差可以控製在 25 nm 以下,但(dàn)是對於(yú)超精密車床,十幾納米或是幾十納米的圓度誤差相對於(yú)主軸回轉運動誤差來說還是不可以忽略,依(yī)然要在數據處(chù)理中將圓度誤差分離出去。
另外,人工裝夾被測試件(jiàn)到超精密(mì)車床時一定會帶來安裝偏心及安裝傾角的(de)問題。安裝偏心一方麵導致測量信號混入較大(dà)的一階諧波分量,通常會比其他階次諧波分量大出幾個量級;另一方麵較大的安(ān)裝偏(piān)心會使測量到的位移分布在一個較大的範圍(wéi),傳感器非線性誤差帶來的影響會增大。雖然傳感器的非線性誤差影響非常之小,但是對於精密測量來(lái)說(shuō),我們(men)要考慮到每一個細節問題。標(biāo)準測試件的安裝傾角偏差也是(shì)一個很大的影響因素,很小的安裝傾角也會導致被測試件末端截麵產生較(jiào)大的(de)偏心運動。
綜合以上分析,即便是采購高質(zhì)量的標準球或是(shì)標準棒,對於超精密車床主軸回轉運動誤差不可忽略,那麽我們可以放寬對標(biāo)準測試(shì)件圓度誤差的精度級別的限製。對於本試(shì)驗來講,最合理的方法既是利(lì)用機床本身加工圓柱體工件作為被測試件,在不拆卸狀態下接著進行主軸回轉運(yùn)動誤差的(de)測(cè)量試驗(yàn)。這種做法(fǎ)合理的原因有:
(1)雖然目前實驗室超精密車床還無法加(jiā)工出圓度誤(wù)差在 25 nm 以(yǐ)下(xià)的柱體或是球體,但是其加工的工件的圓度誤(wù)差和主軸的回轉運動(dòng)誤差(chà)處(chù)在同一個數(shù)量(liàng)級(加工工件的圓度誤差的最主要來源是機床主(zhǔ)軸的回轉運(yùn)動誤差),不會影響(xiǎng)誤差精度(dù);
(2)消除人(rén)工裝夾標準測試件帶來(lái)的安裝(zhuāng)偏心和安裝(zhuāng)傾角誤(wù)差,可以更(gèng)精確地分離主軸回轉運動誤差(chà)。
(3)加工圓(yuán)柱體工件要(yào)比球形工件更為簡單,而且精度要更高,可以節約購買(mǎi)標(biāo)準球或是標準棒的試(shì)驗成本。
3.2.3 位移傳感器初始間隙的安裝要求
位移傳感器的安裝初始間隙對(duì)測量試驗也有一定的影響,下麵對此進行討論:
capa NCDT6300 傳感器線(xiàn)性度(dù)≤0.2%FSO,即在滿量程 50 μm 的情(qíng)況下傳感器的精度不會超過 100 nm。通常超精密車床主軸誤差運動(dòng)在幾納米到幾百納(nà)米之間,而且傳感器在小量程測量(liàng)時的線性度要好於滿量程線性度,所以如果傳感器在 500 nm 的測量範圍內,其測量(liàng)精度(dù)可以控製到 1 nm 以下。
傳感器滿(mǎn)量程線(xiàn)性度不超過 0.2%,但是在量程內不同範圍內的非線(xiàn)性誤差是不(bú)一(yī)樣的。為了保(bǎo)證更嚴格的測量數據,在進行實際測量試驗時,多個(gè)位移傳感器測頭到被測(cè)試(shì)件的初始安裝間隙盡量保持在相同的數(shù)據範圍內,盡量減(jiǎn)少(shǎo)傳感器非(fēi)線性誤差帶來的影響。
3.2.4 徑向誤差測量試驗方案
超(chāo)精(jīng)密車床(chuáng)徑向回轉誤差運動包含(hán)徑向 x,y 兩個自由度方向上(shàng)的運動,從算法角度上來說,利用三(sān)點(diǎn)法(fǎ)誤差分離技術,可以從數據中將主軸的徑向兩個(gè)自由度的誤差運動提(tí)取出來(lái)。徑向(xiàng)誤差測量裝置係統(tǒng)圖如圖 3-12 所示,實際實驗裝置如圖(tú) 3-13 所示。
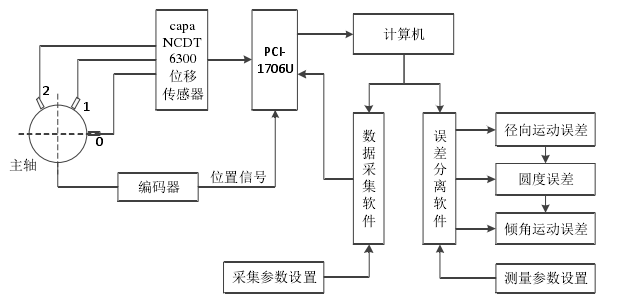
圖 3-12 測量裝置係統圖
在進行數據采集的過程中,通常為等時間采(cǎi)樣。但是為了消除主軸轉動時的速度波動對采(cǎi)樣(yàng)角位置的影響,采取(qǔ)等(děng)角度采樣,即每隔一個(gè)相同的角度進行一次數據(jù)采集。保證等角采樣(yàng)的方法是利用旋轉編碼器,利用編碼器發出的脈(mò)衝信號觸發采樣。編碼器保證等角度(dù)采樣一是三點法誤差分離算法的要(yào)求,二是在求同步誤差時,非等角度采樣均化後將使同步運動誤差失真。
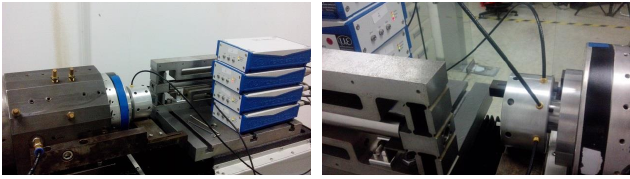
圖 3-13 三點法實際測量試驗傳感器(qì)布(bù)置
3.2.5 徑向運動誤差分離實驗數據處(chù)理
三點法誤(wù)差分離是通過布置垂直於軸線的同一個截麵(miàn)上的三(sān)個位移傳感器進行測(cè)量的(de),在算法上要(yào)進(jìn)過兩次傅裏葉變換,得到將主軸的圓度誤差和主軸兩個自由度上的徑向運動誤(wù)差(chà)分(fèn)離開來。下麵將介紹三點法頻(pín)域誤差分離試驗的具體分離過程。
我們在(zài)最終計算時(shí)采用的每轉采集 128 點進行誤差(chà)分離,為保證有效地去除采(cǎi)集信號中的高頻成分,減小頻率混疊帶來(lái)的影(yǐng)響,在原始電壓(yā)采集過程中將提高采樣頻率,每轉采樣點為 768 點。圖 3-14 是三個傳感器采集主軸在(zài)轉速為 1000 r/min,采樣頻率設置為 1280 Hz,轉動 20 轉的原始電壓數(shù)據。
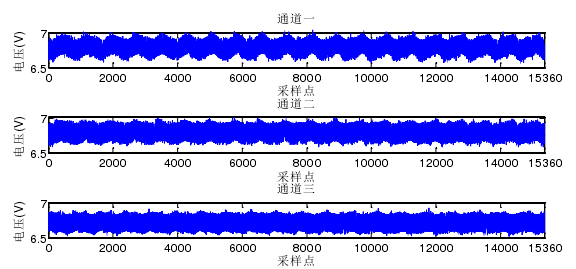
圖 3-14 三個傳感器采集的 20 轉原始電壓讀(dú)數
從(cóng)上圖可以看出,各傳感器的原(yuán)始電壓信號噪音成分還是很高的。先將傳感器電壓信號根據公式(shì)(2-20)轉化為位移信號,這是一個簡單的線性變換。然後對 20 轉的數據進行(háng)傅裏葉變換,對直(zhí)流分(fèn)量、一階諧波分量(liàng)和高於50 階諧波分量傅裏葉變換(huàn)項置零去掉上述成分。圖 3-15 為 0 號傳感(gǎn)器 20 轉采樣信號去掉直流分量、一階諧波分(fèn)量和 50 階以(yǐ)上諧波分量後的頻譜圖。
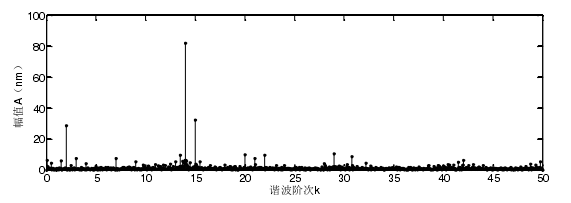
圖 3-15 傳感器 0 濾掉直流分(fèn)量、一(yī)階和 50 階以上諧波分量後的諧波圖(tú)
根據 3.1.2 節(jiē)講述的從頻域中提取整(zhěng)數倍諧波階次分(fèn)量,即可得到超精密車床主軸回轉誤差運動中的徑向同步運動誤差,其(qí)諧波成分如圖 3-16 所示(shì)。
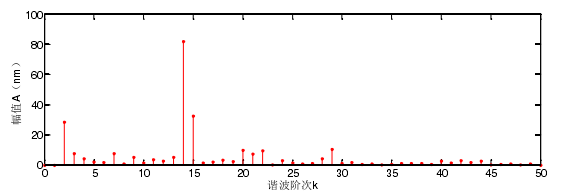
圖 3-16 主軸在傳感器 0 軸線方向上的同步運動誤差諧波圖
圖 3-17 為圖 3-15 和圖 3-16 中信號的時域極坐標圖,此(cǐ)處給出其(qí)時域圖(tú)形,為的是直觀地顯示主(zhǔ)軸的在傳感器 0 方向上的(de)運動誤差。
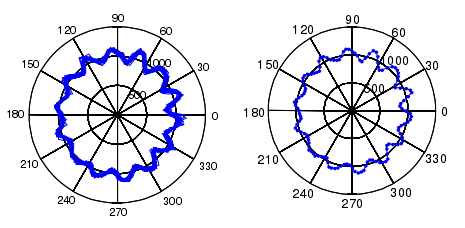
圖 3-17 傳(chuán)感(gǎn)器 0 的 20 轉數據及同步運動誤差
以上是在頻域中去掉直流分量、一階諧波分量、50 階以上(shàng)諧波分量以及(jí)在頻域中提取同步(bù)運動(dòng)誤差的過程。其中提取同步運(yùn)動誤差的過程中(zhōng)不僅提取了主軸回轉誤差運動中的周期性運動,而且還對信號起集合平均作用,進(jìn)一步抑製低頻噪聲。
圖 3-18 給出三個位移同步運動誤差信號的諧波圖,此信號中包(bāo)含被測試件的圓度誤差和主軸徑向運動(dòng)誤差(chà),是三(sān)點法誤差分離的基礎數據。
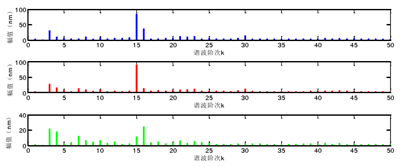
圖 3-18 三個(gè)傳感器的同步運動誤(wù)差諧波圖
基於三(sān)個傳感(gǎn)的同步運動誤差利用三點法頻域誤差分離技術進行圓度誤差和主軸徑向回轉誤差的分離,分離結果如圖 3-19 所示。
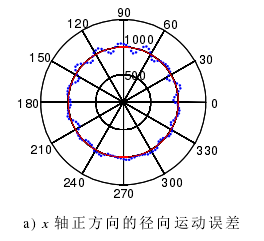
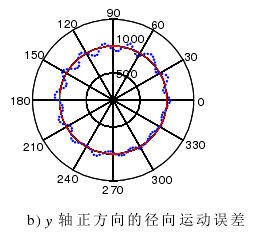
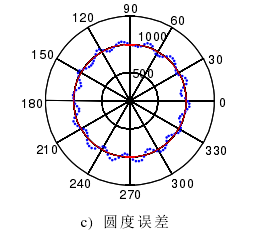
圖 3-19 誤差分離(lí)後的徑向運(yùn)動誤差和圓度(dù)誤差
3.2.6 主軸轉速對(duì)徑向運動誤差的影響
前幾節分析的是主軸在 n=1000 r/min 的(de)轉速下進行的徑向誤差測量(liàng)試驗,主軸在不同的轉速條件下,其徑向運動誤差是不同的。本節的內容主要(yào)研究主軸的不同轉速下進行測量試驗,分析其徑向運動誤差和轉速的(de)關係。表 3-2是主軸在不同轉速下,根據 3.1.4 節講述的最小二(èr)乘圓方法評價的圓(yuán)度誤差和主軸徑向運動誤差。圖 3-20 給出徑向運動誤差在不用轉速下的曲線圖。
表 3-2 轉速對主(zhǔ)軸徑向運動誤差的影響(xiǎng)
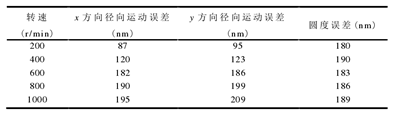

圖 3-20 主軸在不同轉速條件下的(de)徑向運動誤差(chà)
從上(shàng)表(biǎo)和圖中(zhōng)可以看出主軸在不同的轉速下,從測量數據中分離出的圓度誤差基本保(bǎo)持一致,但 x 和 y 方向的主軸(zhóu)徑向運動(dòng)誤差隨著轉速的降(jiàng)低而減小。當轉速降到 600 r/min 時,其徑向回轉運動誤差迅速降低;當轉速(sù)在200 r/min 以(yǐ)下時主軸的徑向運動誤差在(zài) 100 nm 以內。
圖 3-21 中(zhōng)給出主軸轉速在 1000 r/min,600 r/min 和 200 r/min 時,誤差分離的具體(tǐ)數據極(jí)坐標圖形。從圖中可以直觀地看出,不同轉速下分離的圓度誤差圖形基(jī)本一致,而隨著主軸轉速的下降其
x 軸方向的徑(jìng)向運動誤差不斷的減小。需要注意的是不同轉(zhuǎn)速下分離出的圖像在相位上有些差別。
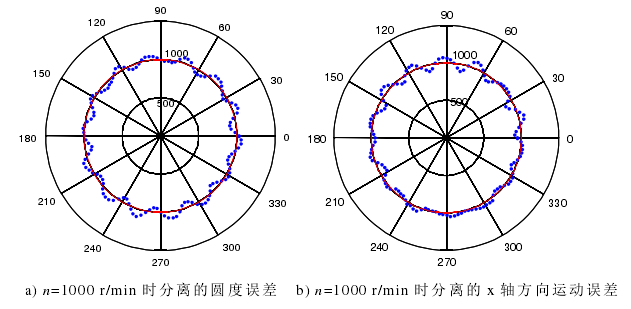
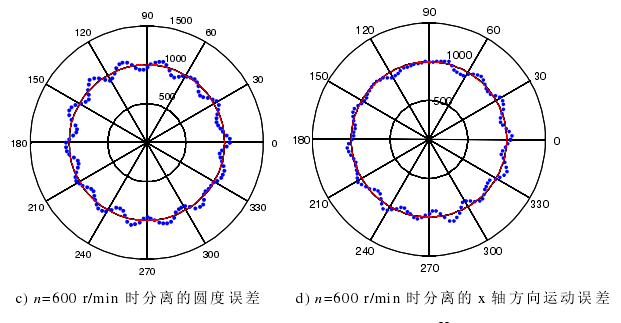
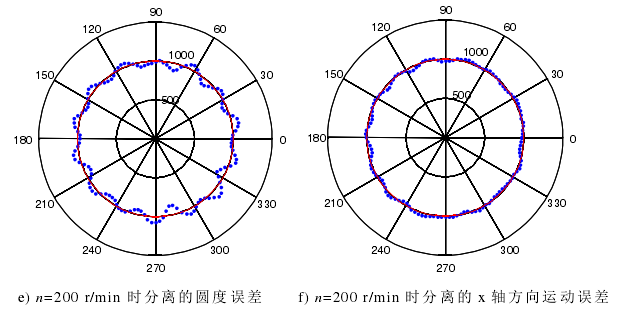
圖 3-21 主軸(zhóu)在不同轉速下分離出的圓度誤差和 x 軸方向的徑向運動誤差(chà)
3.3 本章小結
本章以三點法誤差分離(lí)算法為基(jī)礎,借助(zhù)從頻域中提取同(tóng)步運動誤差原理,將(jiāng)實際測量實(shí)驗中的除噪、濾波和同步運動誤差的提取整(zhěng)合全部在頻域中處理。而且(qiě)頻域連續處理可以一(yī)直延伸到三(sān)點法誤差分離算法中,即將三點法中的(de)部分計算統一整合到(dào)頻域處理。通過統一多個步驟在頻域(yù)中的(de)連續處理,減少了測量信號在時域頻域中的變換計算。從超精密車(chē)床固定方向刀具加工工件表麵成形角度,利用之前建立的運動學模型分析了一階諧波分量對工件表麵成形(xíng)無影響,為測量實驗中去掉一階諧波(bō)分量提供理論(lùn)依據。針(zhēn)對超精密車床進行徑向運動誤差測量實驗,並分析主(zhǔ)軸不同轉速下的回轉誤差(chà)精度。
投稿(gǎo)箱:
如(rú)果您有機床行業、企(qǐ)業相關新聞稿件發表,或進行資訊合作,歡迎(yíng)聯係本網編輯部, 郵箱:skjcsc@vip.sina.com
如(rú)果您有機床行業、企(qǐ)業相關新聞稿件發表,或進行資訊合作,歡迎(yíng)聯係本網編輯部, 郵箱:skjcsc@vip.sina.com
更多本專題新聞(wén)
專題點擊前十(shí)
| 更多