3D掃描可大幅提(tí)高葉盤銑削過程的精度和效率(lǜ)
2021-6-16 來源:雷尼紹 作者:-
Technopark Aviation Technology公司位(wèi)於俄羅斯烏法,是一家教育、科研和工程服務(wù)提供商。它與俄羅斯(sī)規模最大的燃氣渦輪發動機提供商合作密切,後者設計和製造高性能燃氣渦輪發動機,服務於固(gù)定翼和旋轉翼飛機行(háng)業以及天然氣和石(shí)油生產領(lǐng)域。
Technopark的(de)一位客戶希望提高葉盤銑削過程的精度和效率(lǜ)。燃氣渦輪發動機的(de)葉(yè)盤具(jù)有複雜的高曲率表麵,因此製造過程非常(cháng)具有挑戰性。
為了攻克這項(xiàng)難題,Technopark采用了搭載(zǎi)SPRINT™技術的雷尼紹OSP60機內3D掃描測頭和Productivity+™掃描(miáo)軟件包。
背景
在(zài)由(yóu)壓縮機、燃燒器和渦輪組成的精密機械組件中,葉盤在(zài)減少阻(zǔ)力、優化發動機內(nèi)的氣流及其產生的推力方麵發(fā)揮(huī)著重要作用。
葉盤在20世(shì)紀八十年代中期(qī)推出,是一個由轉子輪盤和多個彎曲葉片組成(chéng)的單(dān)一組件(jiàn)。由於葉盤不需要將每個葉片連接到裸露的輪盤上,因此有效改進了渦輪設(shè)計,大大(dà)減少了(le)零件數量,並(bìng)提高了(le)可靠性和發(fā)動機效率。
葉盤由非常堅硬的高價值金(jīn)屬(通常是鈦或鎳基合金)製(zhì)成。迄今為止,銑(xǐ)削是葉盤製造過程中最(zuì)重要的加工(gōng)工(gōng)藝,而且由於葉盤(pán)具有高曲率表麵,因此(cǐ)需要使用多軸數控機床和先進的軟件(jiàn)進行加工。
葉盤銑削通常(cháng)先通過粗銑和半精銑(xǐ)加工製成近終成形工件,然後再通過精銑製成最終的高(gāo)精度(dù)葉片和轉子(zǐ)表麵(miàn)。
挑戰
葉盤具有高度複雜性和嚴苛的製造精度要求(qiú),這意味著其各式葉盤的精銑過程是一個勞動密集型且成本日益增(zēng)加的工藝。
盡(jìn)管使用觸發式測頭可進行機內(nèi)葉盤測量,但在銑(xǐ)削(xuē)後需要將每個工件從數控機床上(shàng)取下進行離線測量和檢測,然後再重(chóng)新裝回機床上進行後續加工。這個過程需(xū)要重複多次,而且(qiě)容易受到(dào)人(rén)為誤差的影響。
據該公司推斷,機外檢測和(hé)銑削過程約占葉盤生產總人力成本的30%至60%。此外,葉片尺寸偏差(在前緣和後緣加(jiā)工(gōng)之後)的統(tǒng)計分析結果證明存在誤差。
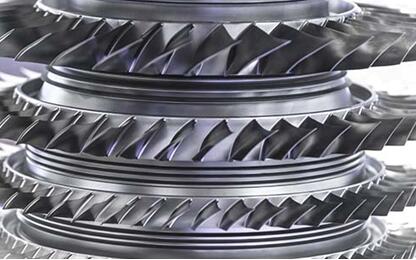
結果顯示,葉片橫截(jié)麵的偏差為:殘留餘量波動±0.064 mm,實際輪(lún)廓偏差0.082 mm。縱截麵的偏差與(yǔ)橫截麵相似:殘留餘量波動±0.082 mm,實際輪廓偏差0.111 mm。
導致邊緣加工過程(chéng)中產生偏差的主要原因可(kě)歸結(jié)為:加工過程中機床的五(wǔ)軸運動誤差(chà);葉片在切削過程中由於其剛性低而發生彈性變形;以及刀具在金屬切削(xuē)過程中發(fā)生彈性變形。”
“這個(gè)過程需要大量的人工幹預,但(dàn)是由於人為誤差不可避免,會導致廢品率(lǜ)增加。我們迫切需(xū)要開發一種全新的解(jiě)決方案,以提高葉盤銑削速度和精度。”
開發用於葉盤銑削的CNC加工過程包括以下要求:
• 使用參數化(huà)控製程序進行(háng)半(bàn)精銑加工
• 機內工件檢測
• 根據檢測結果修正參數化控製程序
• 使用修正後的參數化控製程序對工件進行精銑
解決方案
Technopark被指定負責開發和部署所(suǒ)需的製程控(kòng)製(zhì)技術。Technopark的副博士、創新部負責人Semen Starovoytov說:“我們已經與雷尼紹合作多年,我們在各式機床上配備雷尼紹觸發式(shì)測頭來達到完美的測量精度。”
“對於此項目來說,很顯然(rán)需要基於掃描測頭開發軟件,因此我們決定向雷尼紹尋求合(hé)作。雷(léi)尼(ní)紹用於機床的SPRINT 3D掃描測量技術滿足了我們的所有(yǒu)技術要求。”
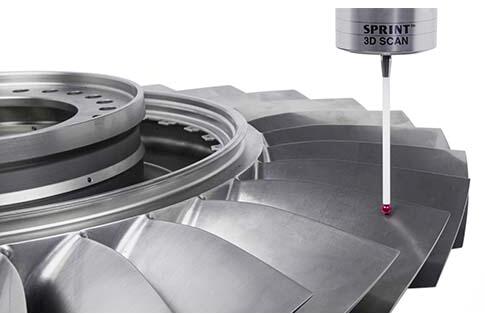
結果
引入Productivity+軟件和OSP60測頭之後,葉盤製造過程的加工精(jīng)度、速度和人力成本發生了顯著改變。
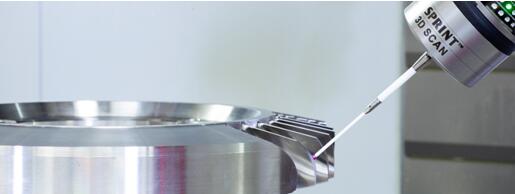
通過在機床上對葉盤進行高速3D掃(sǎo)描和測量,大幅節省了生產時間,從而顯著提高了數(shù)控機床的生產效率。
在葉盤銑削精度方麵,加工後的葉盤(pán)橫截麵和縱截麵偏差均有顯著改進:從原來的0.082 mm和0.111 mm提高到(dào)現在的1 µm和28 µm。
在機床人員配備方麵(miàn),Starovoytov說:“製程控製模式的執行能夠基於OSP60測頭提供的3D葉片掃(sǎo)描數據,自動調整CNC控製程序。這(zhè)意味著工程師不再需要始終監控機床運轉。”
他(tā)總結說:“將SPRINT 3D掃描技術與Productivity+ CNC軟件結合在一起,即使葉盤(pán)形狀發生極細微的偏差也能夠實時識別出來,而(ér)使用觸發式係(xì)統卻無法檢測到這些偏差。”
“這項投資帶來的回報遠遠(yuǎn)超出了我們的預期。葉盤的精銑精(jīng)度提高了三倍以上,而且相關的人力成本降低了一半。”
SPRINT™技術
OSP60機內3D掃描測頭搭(dā)載雷尼紹獨(dú)特的SPRINT技術(shù)。
測尖(測球)可沿葉盤表麵進行精確測量(liàng)移動(dòng),測頭能夠精確記錄高分辨率測針偏折(shé)數據,獲取超靈敏測尖(jiān)在X、Y和Z軸上的亞微(wēi)米級運動數據。
OSP60測頭采用高速、抗噪的光學傳輸連接,每秒可將1000個XYZ測尖中心數據點傳輸到OMM-S接收器。然後,使用高級算法處理測頭偏(piān)折數據與機床位置編碼器數(shù)據,以生成精確的葉盤表麵數據,最後再利用這些數據精確計算特征位置、大小和形狀。
Productivity+™技術
使用Productivity+ CNC plug-in軟件可實現高達15,000 mm/min的掃描速度,機內測量速度有時甚至可以(yǐ)比(bǐ)傳(chuán)統觸發式係(xì)統快5倍。在(zài)機床上掃描葉盤,則(zé)無需在加工過(guò)程(chéng)中取下工(gōng)件。
該軟件可在屏幕上實時顯示高(gāo)精度測量結果,並利用這些(xiē)數據自動調整機床(chuáng)設置,以便進行後續的精銑過程(chéng)。還可將測量報告導出到文件中進行分析或用於執行質(zhì)保。
使用現有的(de)機外圖形編程工具可(kě)基於實體模型幾何特征快速、輕鬆地生成(chéng)葉盤檢測(cè)程序,同時可通過Productivity+交互式前端平台簡單(dān)易(yì)懂的圖形(xíng)屏幕來編輯和模擬測頭檢測程序,用戶無需直接應對(duì)複雜的NC代碼(mǎ)。
詳情請訪問www.renishaw.com.cn/ umpo
詳情請訪問(wèn)www.renishaw.com.cn/mtp
投稿箱:
如果您有機床行業、企業相(xiàng)關新聞稿件發(fā)表,或進行資訊合作,歡迎聯係本網編輯部, 郵箱:skjcsc@vip.sina.com
如果您有機床行業、企業相(xiàng)關新聞稿件發(fā)表,或進行資訊合作,歡迎聯係本網編輯部, 郵箱:skjcsc@vip.sina.com
更多本(běn)專題新聞
專題點擊前十
| 更多(duō)