高速(sù)、高精度數控銑(xǐ)床(chuáng)電主軸結構優化及其(qí)性能研究
2016-8-25 來源:機械工程(chéng)學院 作者:陳麗婷
高速(sù)、高精度(dù)電主軸(zhóu)靜態性能的分析及其結構優化設計(jì)
3.1、高速、高精度電主軸的靜態性(xìng)能理論(lùn)分析
在靜載(zǎi)荷下主軸抵抗變形的能力就是高速電主軸的靜態(tài)性能。高速電主軸靜(jìng)態性就(jiù)是指主軸的靜剛度。彎曲靜剛度與軸向靜剛度是主軸的靜剛度的兩種表現形(xíng)式。對主軸單元而言,彎曲剛度與負荷能力及抗震性密(mì)切相關。彎曲剛度可(kě)W代表靜剛度。電主軸的彎曲(qǔ)剛度K表示當主(zhǔ)軸前端產生單位徑向(xiàng)位移8時,在位移方向所需施加的力Fy6]。
電主軸單元(yuán)靜剛度的計算公式(shì)如下:

K一主軸係統靜剛度,單位N知(zhī)m:
Ff—主軸係統前端的(de)徑向力,單位N;
5—徑向力作用下主(zhǔ)軸(zhóu)前端位移,單位^ml。
芯軸剛度與軸承剛度能夠綜合反映電(diàn)主軸係(xì)統的剛度。電主軸係統剛度大小會受到主軸形狀、尺寸及各組成部件的加王製造精度的影(yǐng)響(xiǎng),同時軸承組預緊力、級聯方式等也(yě)會(huì)影響電主軸剛度。
電主軸係統的剛(gāng)度與機床的加工性能息(xī)息相關,一旦剛度達不到要求,就會使得主軸(zhóu)變形量過大,降低機床的加(jiā)工性能,導致精度要求達不到,同時可能導致軸承不能正常運轉,軸承磨損(sǔn)加劇嚴重時甚至會導致軸承失效。在對高速機(jī)床的(de)靜剛度測量研究中發現,機床變形的一(yī)半1以上部分發生在機床主軸部件處,因此,為提高機床的加工可靠性,就必須加強對主軸靜剛度的研究。接下來我們運(yùn)用有限元分析軟件ANSYSWorkbench分析對電(diàn)主(zhǔ)軸的進行靜態特性。
3.2、高速、高精度主軸係統靜態特(tè)性的有(yǒu)限元分析
3.2.1高速、高精度主軸係統靜力分析的模型簡化及建模
a)構(gòu)建主(zhǔ)軸係統幾何(hé)模型(xíng)
電主軸單元主要由旋轉件和支撐(chēng)件和固定件H部分構成。旋轉件主要是指芯軸、轉子、軸承組(zǔ)內(nèi)圈、滾(gǔn)動體等;支承件是指軸承組外圈W及滾動(dòng)體與軸承內圈的點支撐;固(gù)定件就是指(zhǐ)固定不動的殼體、定(dìng)子冷卻套等。在對電主軸單元的靜態分析時,隻有旋轉(zhuǎn)件和(hé)支撐件起作用,可W忽略固定件的作用。僅(jǐn)對旋(xuán)轉(zhuǎn)件與支承件進行分(fèn)析,其結果能夠代表主軸係統的整體靜力學性能。在進行分析之前I我們首先要對電主軸係統做如下簡化:
1)將電主軸的芯軸和轉子作為一(yī)個整體進斤處理,並且假設(shè)其具有相同的(de)材料屬性;
2)用彈性支撐(chēng)來代表軸承徑向剛度(dù),彈性約束值(zhí)用軸承徑向剛度值(zhí)來表示;
3)不考慮軸承(chéng)組(zǔ)軸向剛度。最終得(dé)到電主軸係統的簡化模型如(rú)圖3.1所示。
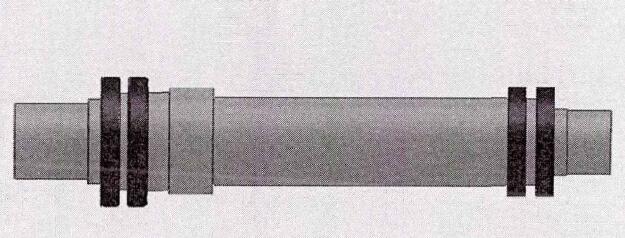
圖3.1電主軸靜(jìng)態(tài)分析(xī)簡化幾何模型(xíng)
b)建立電主軸有限元模型電主軸係統靜態分析的有限(xiàn)元建模,具體步驟如下:
1)簡化(huà)幾何模型在DesignModeler中的建立(lì)
首先,建(jiàn)模可W選擇DesignModeler的自體建模(mó)屬性進行(háng)實體建模,也可W選擇將電(diàn)主軸單元已經在SolidWorks中建立好的H維模型進(jìn)行導入達(dá)到建(jiàn)模的目的。此處,由於我們事先己經(jīng)完成了H維模型在SolidWorks中(zhōng)的建(jiàn)立,隻需將文件格式存儲為電主軸.agd即可直接將(jiāng)電主(zhǔ)軸模型(xíng)導入。簡化幾何(hé)模(mó)型(xíng)如圖3.2所示。
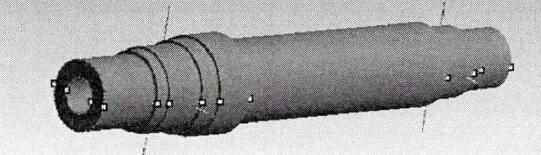
圖3.2導入的(de)幾何模型
2)添加材料屬性
主軸係統選用(yòng)40CrNi,此材料的參(cān)數為:彈性模量E=210N/mm2,泊鬆比^1=03。在軟件中選擇模型的幾何體形(xíng)式為"目〇郵",然後巧(qiǎo)開EngineeringDate窗日進行材料屬性的添加,完成後返回Simula化n窗口。
3)劃分幾何模型的網格
雙擊model進入電主軸靜態性能仿真(zhēn)分析,首先完成模型(xíng)網格劃分的操作。首先在"Mesh<Method"中利用(yòng)過濾體rigid功能鍵選擇主軸係統整體模型,設定網格類型為優先選擇空間六麵體;然後設(shè)定模型網格大小,通過在"Mesh<化ing"設定5mm為網格的劃(huá)分尺寸。此後,通過單擊(jī)"Mesh<GenerateMesh"即(jí)可完成網格的劃分。模型共有115776個單元和169503個節點。對有(yǒu)限(xiàn)元模型進斤網格劃分後如圖3.3所示(shì)。
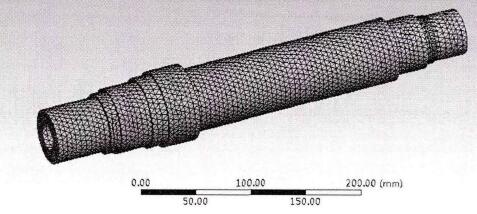
圖3.3電主軸的有限元模型
3.2.2高(gāo)速、高精度電主軸靜態載(zǎi)荷的計算
銳削加(jiā)工時的(de)銳(ruì)削力是電主軸主要靜(jìng)態外載荷。因為不(bú)同工況下鑰削力的差(chà)異(yì)很大,結合VMC係列現有機床加工條件,確(què)定銳床工況進行設定:立式(shì)鑰床在統削加工(gōng)時,假定(dìng)采用端麵粗齒硬質合金端麵統刀,工件材料定為鑄鐵,並且采用對稱銳削,根據VMC係列現有端麵統刀(dāo)的銳削參數選擇維克特63A04R-SCMORC10-22,具體刀具參數如表3.1。下麵對錠削力進行計算:
表3.1維克特63A04R-SCMORC10-22刀具參數(shù)
1)已知條件
由第二(èr)章初步確定的高速錠削電(diàn)主軸的基(jī)本尺寸,設定電主軸的(de)工況:作i定采用端麵粗(cū)齒(chǐ)硬質合金端(duān)麵就刀(dāo),工件材料定為鑄鐵,並旦采用對稱統(tǒng)削。維克特63A04R-SCMORC10-22,具體刀具參數,統刀直徑d0=63mm,鑰刀齒(chǐ)數Z=4,每齒進給量3/=化22mm/Z,毎次銳削深(shēn)度即背吃刀(dāo)量(liàng)=2mm,洗削寬度=40mm。
2)切削力計算
根據主軸係統結構進行受力初步分析,用於(yú)指導電主軸結(jié)構(gòu)的靜力學分(fèn)析巧優化設(shè)計。在滿足主軸靜力分析的前提下(xià),簡化後的係統受力(lì)如圖3.4和圖3.5所示。

圖3.4主軸係統(tǒng)徑向簡化受(shòu)為圖
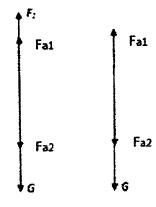
a)切削工作b)空轉
圖3.5軸向受力分析
切(qiē)削受力點到主軸係統前支承點之間的垂直距離為115mm,CD代表刀具切削受力點到主軸係統中屯(tún)、線之間的距離為31.5mm。根據理論力學中力(lì)矩平衡(héng)得如下方程;
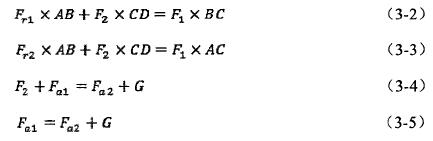
其中,frl——後軸承徑向支撐(chēng)力,i;2——前軸承徑向支撐力,——後軸承軸向力,F。^前軸承軸向支撐為,&——切削力徑向分力,&——切削力軸向分力。
由上述公式可知,若想求得主軸係統軸承組徑向、軸向支(zhī)撐為,需先求出切削力徑向分力(lì)和切削(xuē)力軸向分力。對於端麵鏡削加工,單個刀片的受為情況如圖3.6。單位切削為(wéi)是指單位(wèi)切削麵積上的(de)主切削力,鑄鐵材料(liào)的單位切削力是1200N/rnm2。所W己知單位切削力的條(tiáo)件下主(zhǔ)切削力的求(qiú)解公(gōng)式為口7]:

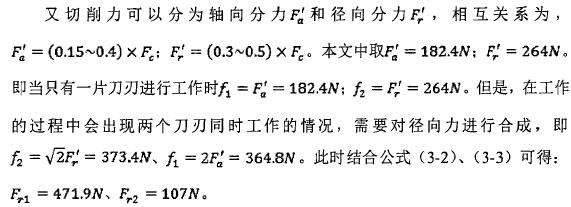
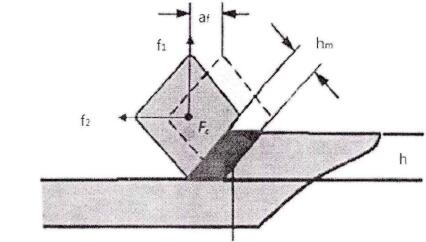
圖3.6單個刀(dāo)片的受力情況
由於建模時,未將刀(dāo)具考慮在內,需將力換算到主軸(zhóu)懸伸段的端部(bù)。顯然由於主軸在徑向方向上受力(lì)平衡。在主軸係統懸仲段端部Fr=與1-與2=364.9。
3.2.3髙速、高精(jīng)度電主軸靜力分析的加載、約束及求解
本論文在對電主軸係統進行靜力學分析時,主要分析其鏡(jìng)削力載荷,由上章節計算得到的(de)主(zhǔ)軸在設定工況下在主軸前端節點上所受最大徑向載荷為
Ff=364.9W。
在實際工(gōng)程中,軸承係統會(huì)發生(shēng)非彈性形變,形變會影響(xiǎng)機床的加工質量(liàng)和(hé)主軸係統的靜(jìng)態特性。前麵在進行模型簡化時己經指出,本文用ANSYSWorkbench中的彈性約束來模擬將軸承(chéng)的彈性支承,用軸承徑向剛度來表示約束剛度值。
下麵具體描(miáo)述如何在ANSYSWorkbench的(de)Sta化Structure功能模塊中對(duì)模型進行加載、約(yuē)束與(yǔ)求解,步驟如下:
a)施加載荷W及約束(shù)
1)施加約束
首(shǒu)先添加圓柱麵約束於電主軸前後軸承軸段麵(miàn)處,選擇Si5)ports>CylindricalSupport,選擇過濾電主(zhǔ)軸模型安裝軸承組圓柱麵,而後對圓柱麵進行約束,設置兩圓柱麵徑向和軸向自由,切向有約束。對主(zhǔ)軸前軸承組處(chù)添加固定約束,選擇Siq)ports>FixedSi5)port,選擇安(ān)裝前軸承組的主軸圓(yuán)柱麵的後端麵。最後對簡化的軸承組(zǔ)添加彈性約(yuē)束(shù),選擇Si5)ports>ElasticSiq)port,過濾選擇(zé)電主軸芯軸用於(yú)配合前、後軸承安裝處的圓柱麵。給定前圓柱麵的徑向剛度值為324(N/|un),後圓(yuán)柱麵的徑向剛度值為(wéi)297卿Aim)。
2)施加載荷
漆麵己經計算得到了主軸的境像銳削力F,=364.9N,本論文模擬分析時將此力(lì)W集中力的形式對主軸前端進行加載施(shī)。具體操作時,選擇Loads>Force,然(rán)後選擇前軸端邊的錠削力作用點,將載荷類型設置(zhì)為Compoiients,Z軸負方向,大小為(wéi)364.9W。電主軸(zhóu)模型添加載荷W及約束後如圖3.7所示(shì)。
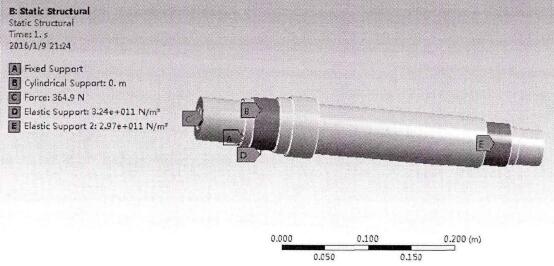
圖3.7添加載荷^^^及約束後(hòu)的電主軸模型
b)指定求解參數並完成求解
靜(jìng)力變形是電主軸靜態分析的主要體現形式,所研究主軸的變形情況是靜力分析必(bì)須要做的工作。經過上述加載後,選擇Deforma化n>Toal>Slove,得到電主軸的靜力(lì)變形。結果如圖(tú)3.8所(suǒ)示。
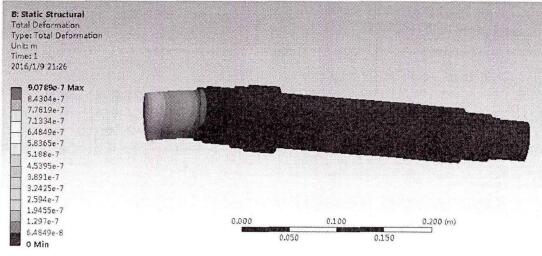
圖3.8高速電主軸的靜態變形圖
從圖3.8可W得出(chū),電主軸在典型切削條(tiáo)件下(xià),最大形變出現在主軸係統前端。最大變(biàn)形量(liàng)表示(shì)為6=9.0巧Xl(r7mWo.giym,其他區域所受影響都相對較小,變(biàn)形量可1^忽略。由電主軸靜剛度的計算(suàn)公式(3-1)可(kě)得:

本(běn)論文設計目標要(yào)求電主軸靜剛度不低於235W佔m,實際上電主軸的靜剛度為400扣/^?11,顯然電主軸的靜剛度符合設(shè)計要求。
3.3、基於ANSYSWorkbench的電主(zhǔ)軸結(jié)構優化設計
3.3.1結構優化(huà)的具體內容(róng)和優化設計
在(zài)對高速電(diàn)主軸結構設計完成W後,我(wǒ)們可W巧步認定電主軸(zhóu)的總體結(jié)構、電機選擇、軸承的配置W及係統(tǒng)的靜剛度等部分已經基本達到設評目標(biāo)要求。接下來主要對主軸結構參數(shù)進斤優化(huà)。
作為高速機床的核屯、部件,電主軸的性能直接決定其(qí)加工精度和(hé)生產效(xiào)率。電主軸(zhóu)的靜剛度對其性能有(yǒu)很大影響,它的數值大小主要受電主軸(zhóu)徑向尺寸、電機、滾動軸承W及預加載荷(hé)的大小的影響。在進行模擬實驗時,主軸前端懸伸量
(a)和前後支撐跨(kuà)距(L)能(néng)夠(gòu)直觀的反映電主軸的靜剛度大(dà)小。
研究發(fā)現,在對電主軸進行結構設計時,主軸前端懸伸量越小主(zhǔ)軸剛度值越大。而主軸支撐跨距(jù)對電主軸靜剛度之間的關係屬於非線性,很難通過^計算方法跨距的合(hé)理值。主軸剛度在兩者之間的綜合作用下變得更加難W確近年(nián)來,隨著(zhe)有限元(yuán)法的快速發展,主軸前端懸伸量(liàng)和前後支撐跨距等參數(shù)已經(jīng)可W用ANSYSWorkbench進行優化。而且其(qí)優(yōu)化結果與實際實驗結果誤差不大,能夠做到(dào)對電主軸結(jié)構參數的(de)優化。
利用(yòng)ANSYSWorkbench的優化設計模塊DesignXplorer對初步完成結構設計的電主軸進行優化,W電主軸前端(duān)懸伸量(a)和前後支撐跨距(L)為設計變量來提高電主軸靜(jìng)剛度,進而完成電主軸係統(tǒng)的結構優化設計8]。
3.3.2ANSYSWorkbench優化設(shè)計的(de)基本概念(niàn)
從己經有的方案中,選出最滿(mǎn)意(yì)的(de)設計方案,就是優化(huà)設計。在實際工程設計中,往往(wǎng)會遇到想要實(shí)現某一特定功能或需要多個參數達到綜合性能最佳(jiā),此時(shí)通常數學學科的最優設計理論為指導,通過計算機軟件(如ANSYSWorkbench)來實現。解決最優解的問題(tí)時,首先根據設計目標(biāo),建(jiàn)立目標函數,然後給出函數變(biàn)量的取值範圍,最後求解,得(dé)到最優方(fāng)案8]。
3.3.3高速、高精度電主軸結構優(yōu)化設計的具體步驟
通過分析可知,影響電主軸(zhóu)靜剛度的最主要參數就是主軸前(qián)端懸伸量(a)與前後支撐跨距(L)。下麵W主軸前端懸伸量(a)和前後支撐跨距(L)為設計變量,W提高電主軸靜剛度為設計目標,完成電主軸的結構(gòu)優化。同(tóng)時還要考慮減小主軸質量,一方麵節約鋼材,另一方(fāng)麵也可W降低主軸慣性矩(jǔ)。也就是說,電主軸靜剛度最大的問題也就是(shì)使主軸前(qián)端位移最小的問題。
ANSYSWorkbench的優化(huà)設計放在靜力學有限元仿真後麵進行研究,與靜力學(xué)分析不同,既然是(shì)優化分析,那麽優化後的主軸前端懸伸量(a)和前後支(zhī)撐跨距(L)值必(bì)然(rán)與優化前有所不同,因此優化設計時主軸前端懸伸(shēn)量(liàng)(a)和前後支撐跨距(L)必須設置為變量,即(jí)需要參數化構建有限元模型,因此須將進行結構優化設計的電主軸(zhóu)前端(duān)懸伸量(a)和前後(hòu)支撐跨距(L)設置為變量(a的初(chū)值是原設計(jì)值,為50mm;L受建模的限製將軸承(chéng)安裝軸段的長度都計(jì)算在內為(wéi)305mm),這樣才能(néng)用DesignXplorer功能模塊進行仿真和優化設計。電主軸結構優化設計的模型與電(diàn)主軸靜態分析的實體模型相同,因(yīn)此在電主軸的(de)靜(jìng)力學分析基礎上,設置目標函數,即在geometry模型選擇主軸前端(duān)變形量(a)和前後支撐跨距(L)使之成為輸入設計變量,如圖3-9。此處(chù)需要說明,前後軸承支撐跨(kuà)距選擇軸承安裝軸段兩端麵之間(jiān)的距離代替。然(rán)後(hòu)在結構(gòu)靜力學(xué)分析求(qiú)解模型的結果求解欄中勾(gōu)選totaldeformation中的最大結果作為輸出變量,即主軸的最大型變量為輸出結果,如圖3.9。
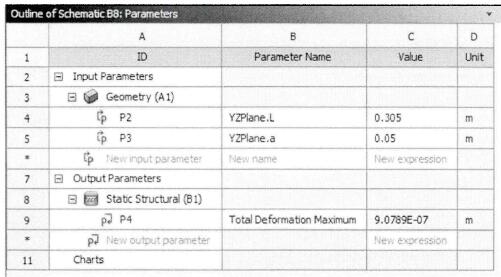
圖3.9設計變量
點擊進入ANSYSWorkbench的優化模(mó)塊ANSYSDesignXplorer的ResponseSurface模塊(kuài)中,在滿足電主軸結構設計要求的前提下,設置主軸前端變形量(liàng)(a)和前後支撐跨距(jù)(L)變量(liàng)的變化範(fàn)圍如(rú)圖3.10(a)、(b)所示。然(rán)後(hòu)對(duì)DOE功能模塊中對10個設計點(diǎn)進行預覽和更新操作,結果(guǒ)如圖3.11。
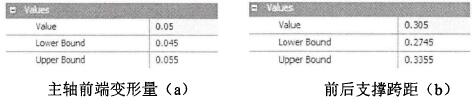
圖3.10變量的變化範圍(wéi)
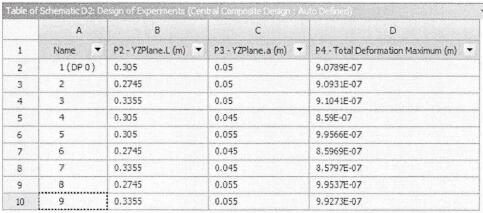
圖3.11對10個設計點更新的(de)結果
然後單擊生成優化結果(guǒ),得到結構優化後的方案(àn)。單擊"Min/MaxSearch*"得到設計變量使得目標函數取到最大/最小值時的(de)值,如(rú)圖3.12所示。

圖3.12目標函數的最值
由(yóu)圖3-12的(de)優化(huà)結(jié)果可知,當主軸前端懸伸量3=45mm和前後支撐跨距L=274.8mm時,主軸前端變(biàn)形量達到最小值(zhí),此時主軸整體(tǐ)尺寸變小,直徑不變,質量(liàng)也相對(duì)較小。綜合各方麵的因素,最終取各優化參數如表3.2所示。
表3.2主軸最優化參數
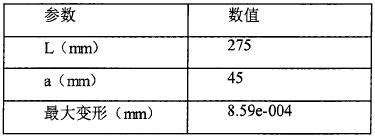
從(cóng)上表可W看出,結構優化(huà)後的電主軸前端懸伸量(a)減小了5mm,前後支撐(chēng)跨距(L)減少31mm,主軸前端變形量最小,大小為H=0.000859mm=0.859^m,此時,電(diàn)主軸的靜剛(gāng)度值最大,大小增大到42日N/imi,比原值(400NAmi)提高了6%。優(yōu)化後電主軸係統質量也有(yǒu)明顯的減(jiǎn)小。優化後的電主(zhǔ)軸係(xì)統結構圖(tú)如圖(tú)3-13所示:
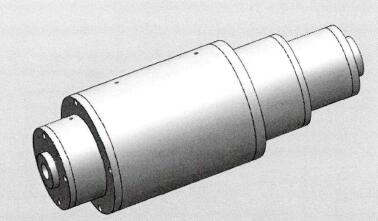
圖3-13優化後的電主軸係(xì)統結構圖
3.4、本章(zhāng)小結
本章首先對電主軸結構進行靜態分析,得到靜剛度值400N/^im,初步驗證了電主軸結構設(shè)計的合理性(xìng)。然後應用ANSYSWorkbench的優化模塊(kuài)ANSYSDesignXplorer對電主(zhǔ)軸靜剛度的重(chóng)要影響因(yīn)素;電主軸前端懸伸量(a)和(hé)前(qián)後支撐跨距(L)進行優化(huà)設計,結果使電(diàn)主軸的靜剛度提高6%,同時主(zhǔ)軸質量比優化前有所減小。優化結果對電主軸靜動態性能的提升意(yì)義重大。
投稿箱:
如果您(nín)有機床行業、企業相關新聞(wén)稿件發表,或進(jìn)行資訊合作,歡迎聯係本網編輯部, 郵箱:skjcsc@vip.sina.com
如果您(nín)有機床行業、企業相關新聞(wén)稿件發表,或進(jìn)行資訊合作,歡迎聯係本網編輯部, 郵箱:skjcsc@vip.sina.com
更多本專題新聞
專題點擊前十
| 更多