一、概述
臥(wò)式銑鏜加工中心(xīn)體現了國產數控機床快速(sù)發展(zhǎn),標誌著我國數控機床在技術上的新突(tū)破。產品有小規格300mm工作台到大規格2500mm工作台,有單工作(zuò)台到雙交換工作(zuò);有普(pǔ)通型到精密、高速型加中心(xīn)等等。此次把臥式銑鏜加(jiā)工中心作為論述的重點,是由(yóu)於這類產品在我國生產製造已經有幾十年的曆史,其製造技術比較成熟,一般生產機(jī)床工作台規格都(dōu)在2000mm以下(xià)。上個世紀八十(shí)年代開始,由最初國內(nèi)幾家企業(yè)到(dào)如今製造該產品的企業達(dá)幾十家,產品技(jì)術水平(píng)也有了質的飛躍。但在幾十餘年的發(fā)展曆程(chéng)中,該產品雖然在技術性能、精度、主軸轉速及坐標移動速度等方麵不斷突破(pò),而在產品規格上最大也隻是2000mm工作台。大規格(gé)、重大形(xíng)式臥(wò)式銑鏜(táng)加工中心近幾年才開發出來。如今,2500mm或(huò)以上規格工作台、帶(dài)交換工作台站的重大型(xíng)臥式加工中心,開創(chuàng)了(le)該類產品曆史先河,為我(wǒ)國航空(kōng)、航天、軍(jun1)工、電力、船舶、工程機械和(hé)其它機械製造業行業提供了大型關鍵設備。
二、臥式銑鏜加工中心總(zǒng)體布局(jú)的結構特點與技術分析
本分析隻對傳統上刨台(tái)式及(jí)十字滑台式臥式加工中心進分析,不包括落地式及五軸加工中心。
臥式(shì)加工中心產品的總體布局有立柱固定(dìng)式和移動式結(jié)構;主軸箱有(yǒu)正掛箱和側掛箱;主軸形式(shì)有固定式(shì)和移動式,移動式主軸有鏜杆式、滑枕式、平旋盤式等多(duō)種結構。
1. 立柱固定式結構
采用立柱(zhù)固定式結構的機床,其機床布局(jú)不外乎有這麽幾種形式:
1)立柱固定在床身上,工作台沿X向、Z向作十(shí)字運動(dòng),主軸箱沿Y向上下運動(dòng)。主軸箱可以是正掛箱、側掛箱兩(liǎng)種形式。此類機床適用於中型複雜零件的鏜、銑等多工序加工(gōng)。
2)固定式(shì)框架立柱(zhù)結構(gòu),主軸箱(xiāng)沿(yán)X、Y向作十字運動,工作(zuò)台沿Y向運動。此類機(jī)床適用於中小型零件的鏜、銑(xǐ)等多種工序加工。
3)立柱固定(dìng)在床身上,主軸箱側(cè)掛在立柱(zhù)上,主軸箱(xiāng)沿Y、Z向作運動,工作台沿X向運動。此類(lèi)機床適用於中型零件鏜(táng)、銑等多工序加工。
2. 立柱移動式結構
立柱移動式機床特點是整體床身大多呈T字型布局,它包括這麽幾種結構形式:
1)床身呈T字布局刨台式結構,立柱在縱床身上沿Z向(xiàng)運動,工作台在(zài)橫床身上沿(yán)X向運動。主軸箱在立柱上有正掛(guà)箱、側掛箱兩種形式,沿(yán)Y向運動。這類機床適用於中、大型零件,特別是長(zhǎng)度較大零(líng)件的(de)鏜、銑等多工序加工。
2)床身呈倒T字形布局結構,立柱在橫床身上作X向運動,工作(zuò)台(tái)在(zài)縱床身上作Z向運動。主軸箱在立(lì)柱上(shàng)有正掛箱、側掛(guà)箱兩種形式,沿Y向運動。這(zhè)類機床適用(yòng)於中、大型零件的鏜、銑等多工序加工。
3)床身呈倒十字形布局結構,立柱沿X、Z向十字運動,主軸箱在立柱上作Y向運動,工作台固定在前床身上。這種機床可適用於中、小(xiǎo)型複雜零件的鏜、銑等多工序加工。
目前,國(guó)內外臥式加工中心機床布(bù)局大多采用T字形結構,這種結構的機床技術比較成熟。從上述結構布局(jú)分析可(kě)以看出,一般中、小型機床采用倒T字型(xíng)結構。這種結(jié)構機床可配備多個(gè)工作台實現快速交換。運動部件也可高速移動,並能高速切削加工,提高工作效率。而T字(zì)形刨(páo)台式結(jié)構適(shì)用於大、重型機床,可(kě)配備雙(shuāng)工作台交換加工,機床工作的同時可(kě)以(yǐ)在待加工區進行工件的裝夾,提高機床加工效率。這種結構布局可作(zuò)為柔性單(dān)元,搭配自動線構成柔性製造係(xì)統。
3. 主軸箱正掛箱結構分析
主軸箱為正掛箱即(jí)是主軸箱體(tǐ)在龍門框架式熱對稱立柱中央(yāng)沿立柱導軌上下移動。由於是正掛箱結構,主軸處於箱體的對稱中(zhōng)心部位,機床運轉所產生箱體溫升變形對主軸軸線位(wèi)移影響較小。因此,主軸箱為正掛箱的機床更容易保證零件加工(gōng)精度。而主軸箱體裝在龍門框架立柱(zhù)內部(bù),其裝配工藝複雜,必須有特殊工藝、工裝(zhuāng)才保證主軸箱與龍門式立(lì)柱的裝配。這種結構的機床提高了工藝製造成本。
4. 主軸箱側掛箱結構分(fèn)析
側掛箱則是主軸箱側掛於立柱外側沿立柱導(dǎo)軌上下移動。立柱一般都是(shì)采(cǎi)用封閉式(shì)矩形箱(xiāng)型結構,其抗彎、抗(kàng)扭(niǔ)、抗(kàng)變形能力較強。由於主(zhǔ)軸箱掛於立柱側麵,機床運轉所產生(shēng)箱體溫升(shēng)或(huò)受其他熱覆射使箱體變形而使主(zhǔ)軸軸線產生偏移,影響工(gōng)件(jiàn)的加工精度(dù)。這種結構機床可承受較大的切(qiē)削力,且裝配較正掛箱相對容易簡(jiǎn)單。
加工中心是一種高精度機械加工設備,以提高零件(jiàn)加工精度為前題(tí)。因此,國內(nèi)外企(qǐ)業的臥式(shì)加工(gōng)中心大多數采用(yòng)正掛箱結構。
5. 主軸部件(jiàn)分析
1) 固定式(shì)主軸結構:
● 機械主軸:當今一般都采用結構緊湊集成主軸組結構(gòu),通過獨立伺服(fú)電機驅動(dòng),經齒輪有級傳動帶動主軸旋轉。由於采用齒輪降速傳動,主軸變速範圍大,可實現大扭矩、重切削加工要求。另外還有采用齒型帶同步傳動結(jié)構,可實現主軸無(wú)級調速。無論采(cǎi)用哪種傳動的主軸結構,主軸軸徑頭部位(wèi)置與箱體間存在有間隙。一般在(zài)箱體或(huò)主(zhǔ)軸法蘭藍盤設計成迷宮式結構,並以氣幕加以保護,避免切削液和粉(fěn)塵等滲入,以(yǐ)保證主(zhǔ)軸的精(jīng)度(dù)和使用壽(shòu)命。
● 電(diàn)主軸:這種主軸通常(cháng)采用內藏式(shì)電機主軸單元結(jié)構,以零(líng)傳(chuán)動的方式實現主軸高速旋轉。主軸(zhóu)內部裝有編(biān)碼器,通過伺服裝置對主(zhǔ)軸運轉(zhuǎn)進行控製,可完成主軸準停、急停等功能。由於是電機直接驅動無傳動鏈,可使主軸達幾萬轉或(huò)更高轉速,並可減少機床(chuáng)的噪聲、發熱、振(zhèn)動和功率損失。一般適用於切削力(lì)小、薄壁(bì)、複雜曲麵、精密零件的加(jiā)工。
2)移動(dòng)式主軸結構:
移(yí)動式(shì)主軸結構一般用在中、大型機床上。它克服了固(gù)定式主軸接(jiē)長刀杆加工易使刀杆變形而帶來的弊端,通常用以較深孔的鏜削或平麵銑削加工。鏜杆或滑枕(zhěn)伸出時會產生(shēng)撓度誤差(chà),而影響工件加工質量,因此,對於采用移動式主軸的機床這是一(yī)個比(bǐ)較關鍵項目。國內外企(qǐ)業對此不斷進行深入研究,采用新材料,改(gǎi)進(jìn)設計、工藝,采用主(zhǔ)軸(zhóu)集成技術等方法提高移動部件的剛(gāng)性,利用控製及補償技術修正移動誤差來保證加工精度。
● 鏜杆式移動主軸:這種主軸結構可以由獨立伺服電機驅動滾珠(zhū)絲杠拖動鏜軸移動,鏜軸移動位置由位置控製(zhì)器監控。它作為機床一個坐標軸可(kě)自行或參與(yǔ)機床坐標聯動加工。通常定義該軸為W軸。另外還(hái)有由液壓係統作為(wéi)動力,液壓(yā)油缸為執行元件拖動鏜軸移動。這種結構鏜軸的移動過程沒有位置監控,不能成為(wéi)機(jī)床的坐標軸。
● 滑枕式移動(dòng)主軸:這種主軸結構可以進行滑枕大行程對工件加工,比鏜(táng)杆移動式結構達到更深的孔或麵的加工。這是由於在滑枕移(yí)出的基礎上主軸在滑枕內繼續移(yí)出,總行(háng)程一般可達1000mm以上。由於(yú)滑枕截麵(miàn)是矩形結構(gòu),滑(huá)枕行程移動的間隙類似於機床矩形(xíng)導(dǎo)軌其間隙可調,保證了滑枕運動中的高剛性和可重複性。因此,它的導向性能(néng)和移動精度優於純鏜杆移動式主軸結構。
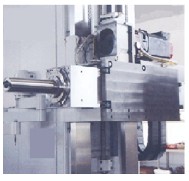
● 平旋盤式主軸:平(píng)旋盤可分為固定式和可拆式兩種。固定式平旋(xuán)盤是安裝在機床上不(bú)可拆卸的,而可拆式平旋盤拆卸與否可根據加工的(de)需(xū)要來確定。平旋盤(pán)旋轉(zhuǎn)運動是(shì)由主電機經齒輪傳動完成主切削運動;平旋盤滑塊(kuài)的徑向進給(gěi)移動是由伺服電機驅動,經(jīng)齒輪行星機(jī)構傳遞完成。平旋盤還可以帶有兩(liǎng)個滑塊同向或反向沿徑向移動,實現進給加(jiā)工(gōng)。這種平旋盤結構(gòu)與普通機床上的平旋盤不同,平旋(xuán)盤滑塊的進(jìn)給是(shì)由伺服電機控製完成,稱為U軸。平旋盤徑向滑塊上帶有刀(dāo)具自(zì)動夾緊裝置,可實現刀具的自動交換,故(gù)稱其為數控平旋盤。可實現複雜零件回轉麵及溝槽的車鏜加(jiā)工。
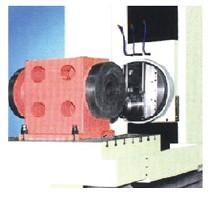
三、高精(jīng)度、高(gāo)速度、重大(dà)型是臥式銑鏜加工中心技術發展的重點方向(xiàng)
目前國內生產製造臥式(shì)加工中心企業有幾十家,產品規(guī)格從工作台300mm到2500mm等各種規格二十多台。在這些企業中我們發(fā)現很(hěn)多新麵孔。據了解,他(tā)們有的是近兩年才轉入機床行業並自行開發、製造臥式加(jiā)工中心,其機床製造(zào)技術不是很成熟,機床指標與性能還處(chù)於一般水平(píng)。有的卻(què)是高起點,利用(yòng)國外先進技術生(shēng)產(chǎn)製造中、大型臥(wò)式加工(gōng)中心及其(qí)他類型高端數控產品。
一般工作台(tái)規格在630mm以(yǐ)下的中小規格機床,機械主軸最高轉速大多在8000r/min以下;各直線坐標最大(dà)位移速(sù)度在60m/min以下(xià);定(dìng)位精度在0.01mm左(zuǒ)右。而中大型規格的臥(wò)式加工中心機床指標低於上述(shù)指標。 通過資料顯示,有些企業機床性能、參(cān)數可作為選項,根據(jù)用戶需要,采用不同配製。例如:有些中、小規格的加工中心,采用了電動主軸(zhóu),使機床主軸(zhóu)轉速可(kě)達上(shàng)萬轉/分鍾甚(shèn)至幾萬轉/分鍾。滿足了汽車工業中的模(mó)具(jù)製造、以及動力設備製造業中難加工材料如:鈦合金、鉻、鎳(niè)、鐵等合金的加工。
提高機床進給速度、縮短零(líng)件加工時間,是提高生產效率的重要保證。因此在高(gāo)速(sù)進給技術方麵,已(yǐ)采用直線電機驅動或采用大導程滾珠絲杠為驅動,進給加速度達1.5G~ 2G,快(kuài)速進給速度達120 mm/min。此類產品(pǐn)在於機體的小型化,通過采用相應的技術手段是不(bú)難達到的,這類產品更易於形成柔性線體係。
在機床行業追求高精度、高速度的同時,我國航空(kōng)、航天、軍(jun1)工、能源裝備和重型機械工程等重點發(fā)展領域正在快速發(fā)展,對金切機床技術水平、性能指(zhǐ)標要求越來越高。這些行業的(de)突出特點是零件基體龐大、結構複雜、品種繁多,精度要求高,通常為(wéi)小批量生產,無法采用大規模流水生產(chǎn)方式來提高效率和降低成本。特別是大型箱體零件惟有重、大型臥式加工中心水(shuǐ)平(píng)軸切線削加工比較適合。如寧波(bō)海天精工機械有限公司生產(chǎn)的HTM-160HA、上海三一精機有(yǒu)限(xiàn)公司生產的HMSD250P及意大利PAMA(上海公司)生產的TB3000臥式加中心等。其工作台規格(gé)分別達2000mm、2500mm和1600mm,並采用雙交換工作站結構。這類機床可(kě)承載(zǎi)大型(xíng)零件,一般最大可承載零件重達二十多噸。該類機床均采用鏜杆式移動主軸結(jié)構,鏜軸直徑為φ130mm至φ160mm。采用大功率和高扭矩設計,可進(jìn)行強力、高速切削加工(gōng)。目前帶雙交換工作站結構最大規格(gé)工作台已達到3000mm×2500mm,鏜軸直(zhí)徑為φ160mm。而固定工作(zuò)台結構機床,工作台最大可達4500mm×3000mm如台灣達佛羅企業有(yǒu)限公(gōng)司生產(chǎn)的HBM-7T型產品(pǐn)。
四、結束語
目前(qián),中小規格臥式加工中心產品涉足廠家較多,產品的整體製造技術比較成熟,產品的技術性能與技術指標已接(jiē)近國外發達國家產品水(shuǐ)平。這類產品市(shì)場容量大(dà)、但競爭(zhēng)也較為激烈,已麵臨著產能過剩的危機。而國內重大型(xíng)臥式加工中心製造技術還處於發展階(jiē)段,國內(nèi)能夠掌握其核心(xīn)技術生產、製造的企業不多,重大型產品競爭遠不如中小規格產品競爭(zhēng)激烈,致使企業缺少產品了創新意思,產品的技術挖潛升級步伐較慢,導致重大型產品技術發展落後於(yú)中小規格產品。若要(yào)實(shí)現(xiàn)核(hé)心技術突破,企(qǐ)業應積極跟蹤市場和(hé)國外產(chǎn)品技術發展趨勢,踏實做(zuò)好核心技術的攻關研究工作(zuò),如大(dà)型移(yí)動部件(jiàn)的剛性研究以及拖動技術的研究(jiū),熱變形補償技術的研究等(děng)等,使之提高(gāo)機床的精度(dù)和穩定性,真正實現從提供機床產品到機床商品的轉變,為(wéi)我國重點發展(zhǎn)領域及新興產業(yè)提供先進適用的機床裝備。
如(rú)果您有機(jī)床行業、企業相關新聞稿件發表,或進(jìn)行資訊合作,歡迎聯係本網編輯部, 郵箱:skjcsc@vip.sina.com