提高汽車模具零件加工(gōng)精度與效率的方法
2017-11-27 來源: 四川宜賓普(pǔ)什模具有限公司 作者:堯軍
摘要:通過(guò)對加工工藝(yì)流程和裝配工藝流程的分析,找出影響汽車模具零件製作精度的因(yīn)素,通過(guò)改善(shàn)模具零件的裝(zhuāng)夾方式、加工順序、加工條件和優(yōu)化裝配淬火流程,在保證(zhèng)單件(jiàn)加工尺寸精(jīng)度的同時強調過程檢驗,以達到提高模具零件製作精度的目的。
關鍵詞:等高墊鐵;淬火流程;過程檢驗;模具零件
l 、引言
隨著汽車工業的飛速發展(zhǎn),對於汽車模具零件的加工精度要求越(yuè)來越高,周期要求越來越短。為(wéi)滿足模具零件加工的要求,越來越多的企業采(cǎi)用購買高精(jīng)機(jī)床進(jìn)行模具零件加工(gōng),但是從實際加工生產來看,加工的模具零件精度仍(réng)不(bú)能得到很好的保證(zhèng),因此如何優化模具零件的(de)加工(gōng)工藝流程顯得尤為重要。
2、合理的加工工藝
模具(jù)零件加工受機床(chuáng)、切削力(lì)、溫度的影(yǐng)響,導致模具零件的加工質量及尺寸精度也受到影響,因此需要通過優化加工流程來提高零件的(de)加工精度。
2.1零件裝夾優化
模具零件裝(zhuāng)夾的一般流程為:采用墊鐵安裝模具零件,保證墊鐵等高(同時平磨),將(jiāng)墊鐵分布到零件的四周,如圖1、圖2所示(shì),然後按操作流程進行模具零件的裝夾。

圖(tú)1模具零件尺寸<2m
加工時通常隻關注墊(diàn)鐵是否等(děng)高,而(ér)忽略(luè)當墊鐵擺到機床工作台上時是否等高,由於機床工作台(tái)長(zhǎng)期使用,有可能導(dǎo)致墊鐵放到點後而高度不一致,導致模具零件裝(zhuāng)夾(jiá)不平(píng)。每次(cì)零件裝夾前應確認墊鐵擺到機床工作(zuò)台上(shàng)後是否等高。
模具零件加工後由於切削應力和熱變形,將會導致模(mó)具零件加工完後有變形,零件底麵與墊鐵接觸麵越多,越能反映加工後零件的平麵真實(shí)情況。試驗表明,4塊墊鐵和(hé)6塊(kuài)墊鐵導致的模具零(líng)件精度差在O.05 mm左右,模具零件越(yuè)大精度差越明顯(xiǎn)。
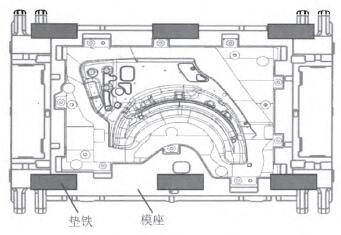
圖2模具零件尺(chǐ)寸>2 m
對於薄板類模具零件(如落料模模座)加工前其自身就會產生變形,即使(shǐ)對零件進行多次加工仍可能無法保證(zhèng)底(dǐ)麵平整,裝好後始終會有一(yī)個角與接觸(chù)麵有間隙(xì),對於這種情況,再用機床加工來解決變形隻(zhī)會增加製造成本。由於模具零件最終是在機床上進(jìn)行作業,上機(jī)床後工作狀態為直接(jiē)將模(mó)具裝夾到工作台上,隻要保證模具的裝夾狀態與機床的裝夾狀(zhuàng)態一致,就能保證其加工精度。為此對於此類模具零(líng)件無法加工平整的,加工時(shí)保證其(qí)平(píng)麵度在0.3 mm以(yǐ)內,對於模具零件的裝夾,條件允許的(de)情況下直(zhí)接放在工作台上更能保證其加工精度。
墊鐵安裝(zhuāng)好後就需要對模具零件進行校(xiào)平找正,為了能夠快速校(xiào)平找正,可利用模具零(líng)件(jiàn)底平麵的(de)十字鍵(jiàn)槽進行定(dìng)位,製作定位鍵,定位鍵(jiàn)的上端與模具零件(jiàn)的鍵槽(cáo)配合,下端與機床工作台(tái)上(shàng)的鍵槽或者T型槽配合,如圖3、圖4所示。
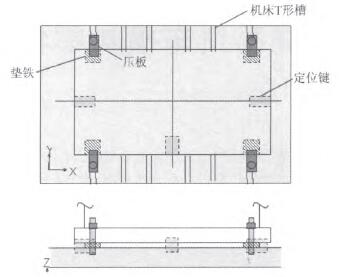
圖3 模具零件定(dìng)位安裝樣圖
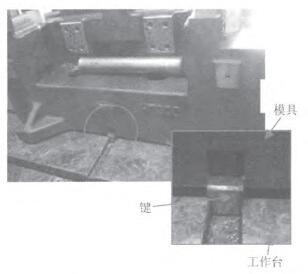
圖4模具零件定位安裝
相對傳統的手(shǒu)工校平方式,用定位(wèi)鍵自動校平可提高約50%的裝夾效率。同時(shí)模具(jù)零件(jiàn)緊固從以往靠壓板與零件及工作台之(zhī)間的摩擦來限製(zhì)模具零件的水平自由度,改為直接剛性限(xiàn)製其水平自由度,這樣能獲得更好的安裝效果。
2.2製作工序的合理安排
對於零件加工,最重要的是基準(即瓜,,、z基準),基準的準確與否直接影響模具零件的(de)最終(zhōng)加工精度。Z基準即(jí)模具零件的底麵,考慮如何裝夾(jiá)來應對模具零(líng)件(jiàn)的變形,首先要考慮盡(jìn)量減小或者消除零件自身的變形。一般模具零件底麵的製作流程為:①底麵粗加工;②底麵壓夾槽、鍵(jiàn)槽(cáo)等(děng)粗精加工;③底麵精加工,然後進(jìn)行正麵的(de)一次加工,組(zǔ)裝後的二次加工。這樣(yàng)的製作流程消除了模具(jù)零件底麵(miàn)由於大餘量(liàng)切削產生的加工變形,但是加工應力和熱應力不能得到充分釋放,也就是後期模具零件還會有變形,同樣會使得(dé)後(hòu)期進(jìn)行二(èr)次加工時Z基準平麵不平,經驗證,其變形量(liàng)約O.2 mrrd2 m。一(yī)般模具零件一次加工完成後進入鉗工組裝鑲件,然後再(zài)進行加工需要2~3天(tiān),在這過程中模具零件(jiàn)也在(zài)進(jìn)行自然時效,而模具零件的二次加工量很少,對模座加工產(chǎn)生的應(yīng)力很小(xiǎo)。因此隻要在二次加工時先將底麵重新精光加工一次,就能(néng)很好消除底麵變形(xíng)產生的影響,保證模具零件z基準精度。
Z基準重新精光(guāng)後,原來的從】,基準也會有相應的變化。在(zài)一次加工時(shí),基準孔做小一號(同樣按H7製作),二次(cì)加工時將其精加工到位,這樣能(néng)保證其精確。同(tóng)時將精度要求高的導向麵、導向孔(kǒng)也安排在二次加工時精加工,以保證導向精(jīng)度。
2.3 加工機床的合理使用
零件加工時常會將粗加工機床和精加工機床分開,可以更好地(dì)保護機床。由於各種因素的影(yǐng)響,精/JnY-.機床(chuáng)的精度一般≤0.01 mm/1 m,重複精度一般≤0.006 mm/1 m,但是對於不同(tóng)的機(jī)床,有些機(jī)床精度可能是(shì)0.01 mm/1 m,有(yǒu)些是一O.01 mm/1m,這樣同樣用於精加工(gōng)的不同機床,其誤差就(jiù)在(zài)0.02 mm/1 m。模具零件的精度要求:型麵+--0.05mm,導向孔±0.01 mm,導向麵±0.05 mm,也就是不同機床不能滿足導向(xiàng)孔的精度要求。因此對於(yú)模具(jù)零件的二次精加工,采(cǎi)用(yòng)上、下模同一台機床加工更能保證其配合精度。
3、運用合理的裝配流程(chéng)
裝配流程的優劣直(zhí)接影響模具零件的(de)製作質(zhì)量和生產成本,因此在模具零件製作環節起著(zhe)關(guān)鍵性的作用。模具零件(jiàn)的裝配包(bāo)括下模與凸(tū)模的組裝、上模與鑲件的組裝、上模與壓料器的組裝、斜楔與模座的組裝等,這裏主要(yào)是淬(cuì)火(huǒ)工序和組裝基準對模具零件(jiàn)精度的影響(xiǎng)。
3.1淬火工序的合理安排(pái)
隨著模具(jù)零件製作技術的不斷進步(bù),淬火工序也在進行不斷優化,以鑲件淬火為例,以往的淬火流程如表1所(suǒ)示。
上述流程的優點:能夠很好地保證鑲件(jiàn)之間拚接,精加工時餘量均勻。缺點(diǎn):組(zǔ)裝粗加(jiā)工會增加(jiā)加工難度,整體型麵粗加工容易出現加工盲區(qū),球刀粗加工時加工(gōng)量大,對機床損傷嚴重,同時也增加了模(mó)具零件在機(jī)床的占機時間(jiān),加工周期長。優化後的(de)淬火流程如表2所示。
優化後的加工流程優點:機床的加工時間得到(dào)有效降低(隻有8 h),對加工效率提高具有很大的作用,節約了(le)加工成本,後期鉗工裝配時間也大大縮短,進一步縮短模具零件生產周期。缺點:由(yóu)於采用單件(jiàn)加工隻有單件基準,也就是會出現基準誤差,再加上鉗工的研配,會出現組裝(zhuāng)後鑲件之間型麵輪廓結合不(bú)好的情況,嚴重時沒有加工餘量,增
加了返修次數(shù)。要解決這一問題,首先要(yào)保證鑲件的一次加工質量(liàng),同時加工工藝充(chōng)分考慮鑲件淬(cuì)火前的加工餘量。
表1淬火(huǒ)流程
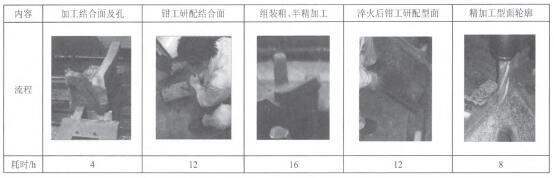
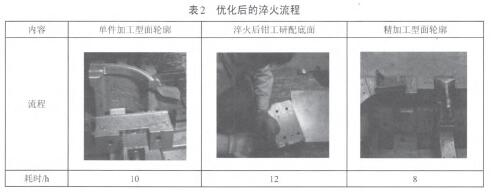
綜上所述,采用優化後的淬火流程能夠很好(hǎo)地在保證零件加(jiā)工(gōng)質(zhì)量的前提下提高生(shēng)產效率(lǜ),這是目前廣泛采用(yòng)的(de)加工(gōng)方式。也並非所有的鑲件都適合先淬火後加工,圖5所示的鑲件內圓角R1 mm,由於CNC加(jiā)工(gōng)很難(nán)達(dá)到R1 mm的加工(一般到R2mm),導致加工完成後內圓角尺加工不(bú)到位,隻能留給鉗工修配,如果先淬火,勢必會增加鉗工的(de)修配難度(dù),還會由於工(gōng)具限製(zhì)無(wú)法(fǎ)實現修配,此類鑲件適宜鉗工研(yán)配好後進行淬火。
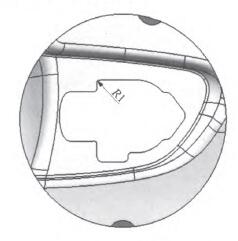
圖5車門板鎖(suǒ)口位置
3.2組裝工(gōng)序的合理選擇(zé)
各零件組裝加(jiā)工有利於保證整體模具的製作精度,但影(yǐng)響模具的製作周期,如何保證零件加工精度需從工藝流程上對其進行優化。
一般在凸模基準側(cè)的壓料器和斜(xié)楔、整形壓料器都需要組裝加(jiā)工,這樣能更好地保證基準精度。而對於其他壓料器和斜楔采用單件加工,能縮短加工(gōng)周期。單件加工會產生基準累積誤差,導致(zhì)模具零件精度下降。壓料(liào)器、斜楔與模座一般(bān)都是采用導板或導柱導向進行組合,以保證其組合精度。壓料器、斜楔其導向一般都(dōu)是(shì)在背麵加工,而型麵在(zài)
正麵(miàn)加工(gōng),因此就存在背麵和正麵的相對誤差,而且導向尺(chǐ)寸(cùn)公差的不一樣,會產生直線誤差,這樣就使得加工完成後組裝到模座裏麵型麵不吻合(hé)。對於不組裝的壓料器、斜楔,在做正麵加工時需以背麵導向尺寸類來確定基準,首先保證導向類(lèi)尺寸公差一致,然後將其轉換到正麵,保證相對基準。
4、進行有效的過(guò)程檢驗
檢驗可以第一時間發現製作(zuò)過(guò)程中加工零件的質量問題,但是一般檢驗都是(shì)在模具零件加工完成(chéng)下機後或者是(shì)鉗工裝配完成後進行,這樣雖然發現了問題,但是沒能在第一時間解決加工尺寸問題,會(huì)造成(chéng)模具零件的(de)返工返修。因此在模具零件(jiàn)製(zhì)作過程中引入(rù)過程檢驗,在加工過程中,對零件關鍵(jiàn)尺寸進行實時(shí)檢查確(què)認,對沒有加工到位或者裝配不合理的及時予以修正,保證其加工下(xià)機前零件合格,如圖6所(suǒ)示。
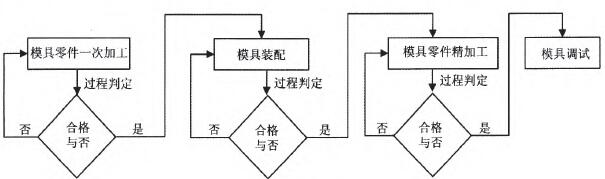
圖6過程檢驗流程圖
通過在加工製作的(de)同時確認加(jiā)工零件尺寸精度,避免了(le)重複上機床翻修,可大大降低返修時間(裝夾、轉運、二次加工找正等工時消(xiāo)耗)。
5、結(jié)束語(yǔ)
影響模具零件加(jiā)工(gōng)精度的因素有很多,如操作技能等。隨著(zhe)自動化加工的不斷深入,模具零件的製作采用機床(chuáng)全程序加工,同時(shí)將裝配工序細分,保證每一部位零件的裝配質量;並且重視模(mó)具零件存(cún)放時的擺放狀態,減小模具零(líng)件變形對其(qí)精度的影響,更有利(lì)於模具精度的提高。
投(tóu)稿箱(xiāng):
如果您有機床行業、企業相關新(xīn)聞稿件發表,或進行資訊合作,歡迎聯係本網編輯部, 郵(yóu)箱:skjcsc@vip.sina.com
如果您有機床行業、企業相關新(xīn)聞稿件發表,或進行資訊合作,歡迎聯係本網編輯部, 郵(yóu)箱:skjcsc@vip.sina.com
更多相關信息
業界視(shì)點
| 更多
行業數據
| 更多
- 2024年11月 金屬切削機床(chuáng)產量(liàng)數據
- 2024年11月 分地區金屬切削機床產量數據
- 2024年11月 軸承出口情況
- 2024年11月 基本型乘用車(轎車)產量數據
- 2024年(nián)11月(yuè) 新能源汽車產量數據
- 2024年11月 新能源汽車銷量(liàng)情況
- 2024年10月 新能源汽車產量數據
- 2024年10月 軸承出口情況
- 2024年10月 分地區金屬切削機床產量數據
- 2024年(nián)10月 金屬切削(xuē)機(jī)床產量數據
- 2024年9月 新能源汽車銷量情況
- 2024年8月 新能源汽車產量數據
- 2028年8月(yuè) 基本型乘用車(轎車)產量數據